- Insgesamt zählen zum Strukturentwicklungslabor zehn Testingenieure und 27 Werkstattmitarbeiter – hier ist ein Teil davon: (stehend, v.l.n.r.): Miroslaw Zieba, Daniel Mumme, Andreas Liebmann, Kai Kircher, Stefan Laick, Bernd Schad, Siegfried Schindler, Rainer Wenz, Stefan Schuch, Oliver heck, Francisco Steines Vieira; vorne, sitzend: Peter Taeny, Otto Hemmelmann
The testers consider the “normal” life
of a vehicle to be ten years of use or
160,000 kilometers
traveled
Time is relative. It is hard to imagine a better place to experience just how variable time can be than Opel’s Structural Development Laboratory at the International Development Center (ITEZ) in Rüsselsheim, Germany. We take a closer look at the door operation test rig where an Opel prototype is enthroned. Its doors keep opening and closing over and over, operated by mechanical arms working with a precisely defined force and speed, extremely fast but exactly synchronized – as though they were the subject of a time-lapse video.
In principle, the ordeal imposed on the doors is intended to be precisely that. This test subjects the closing mechanisms of the Opel chassis to the stresses they will be exposed to “outside” during the lifecycle of a normal vehicle. And so the doors open and close, seven days a week for four weeks…
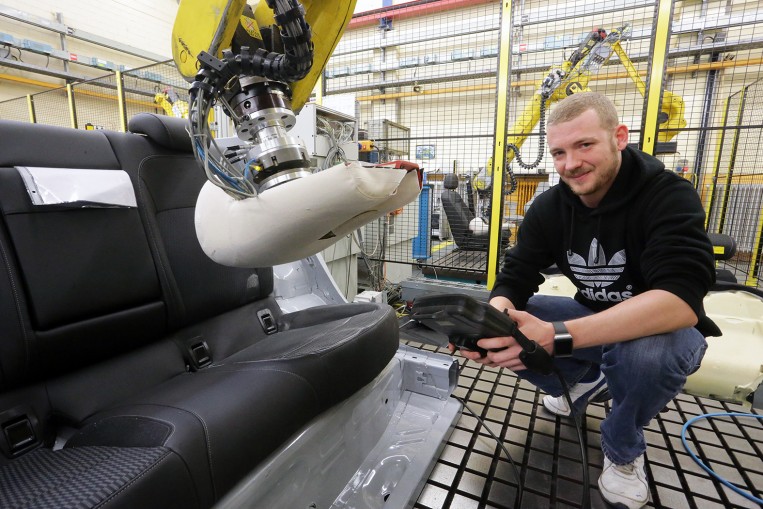
Everything in place? Tobias Friedrich checks the test rig before the test series begins.
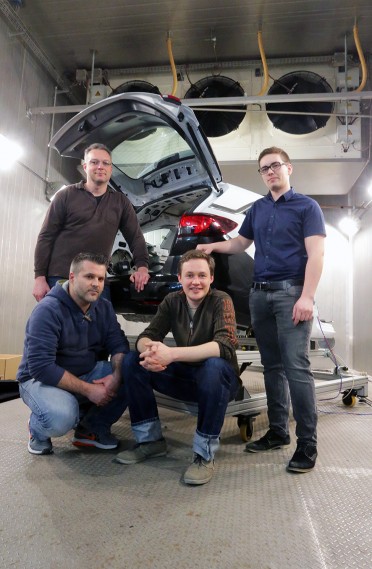
They only slam doors for testing: Bernd Schad, Oliver Heck, Siegfried Schindler and Francisco Steinnes-Vieira (l. to r.).
TEN YEARS OF USE OR 160,000 KILOMETERS
In fact, this test rig simulates as much as 1.6 times the average automobile life expectancy. “For the hatch and the hood, we even go as high as a factor of 1.83,” boasts test engineer Siegfried Schindler, who administers the series of tests together with technician Oliver Heck. This ensures that Opel drivers can be confident the doors on their vehicle will close just as well on its final day as on its first.
The testers consider the “normal” life of a vehicle to be ten years of use or 160,000 kilometers traveled. Documenting and evaluating the tests and reporting the results and insights to the respective departments “is very exciting,” says Francisco Steinnes-Vieira. At 24, he is the youngest test engineer in the team of Otto Hemmelmann, Lead Engineer for Test Methods. Steinnes-Vieira has already completed professional practical training in P10, written his bachelor thesis here, and is now a permanent member of the test team since successfully completing his studies.
CHANGEABLE WORKING CLIMATE:
FROM MINUS 40 TO PLUS 80
Currently, Steinnes-Vieira is administering a series of tests in the climate chamber of the “Slam” test section. Once again the doors keep opening and closing, but under continuously changing outside conditions: The facility can simulate cold temperatures of minus 30 degrees Celsius, as well as a sweltering 80 degrees or 95 percent relative humidity. “Here you can see the reasons behind the development work we do every day,” enthuses Steinnes-Vieira about his job. It really does make time fly…
What the climate chamber in the “Slam” test section does to a single door can also be done to a complete vehicle in P10. Not only does the heat and cold test rig support temperature fluctuation tests from minus 40 to plus 80 degrees at different, defined relative humidity levels, but also tests with the engine running in road use that can be simulated with the integrated “four-poster system”. With this, even the quality of the road surface can be varied.
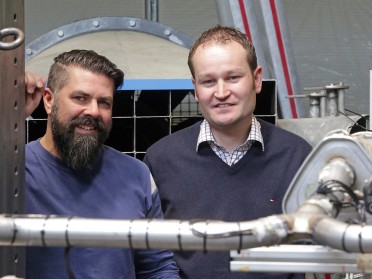
Blowing off steam? Just an ordinary day in the exhaust system test rig, where Stefan Schuch and Alexander Schmidt are making sure everything goes according to plan.
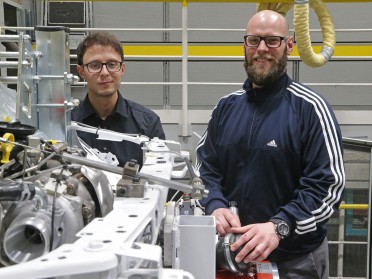
Shaking all over: Kai Kircher and Peter Taeny use the “Shaker” to verify that the engine mounts keep the Opel promise in the long term.
“We can also simulate passengers getting into and out of the vehicle, and we can vary the passenger parameters from the average 1.80 meters to an overweight person with a giant torso“
– Tobias Friedrich –
COORDINATION BETWEEN TEST DRIVERS AND LABORATORY TESTERS
Complete vehicles are also put through their paces in the 26-channel whole vehicle test rig. Here, the focus is on the long-term durability of the chassis and frame. The short but intense life of the prototype in this chamber is correspondingly “moving.” “Stress tests with this objective are also conducted on the special tracks at the Opel Test Center Rodgau-Dudenhofen,” test engineer Kai Kircher tells us. “But the test drivers need three to four months to replicate the entire life of a vehicle. With our test rigs running around the clock, we only require a third of that time.” Of course, the laboratory testers and test drivers do not view each other as competitors, quite to the contrary: “We regularly compare our results, leading us to important insights that help us create even more realistic conditions in our facilities.”
SHAKING OR BOXING? MATERIAL IS STRESSED IN MANY DIFFERENT WAYS
Meanwhile, the “shaker table” leaves things thoroughly shaken, not stirred – not a Martini, obviously, but rather a new Opel engine. Here the testers are focusing on the long-term load capacity of the engine and transmission mounts. Fellow workers in the Powertrain department check the quality of the unit in their own tests.
In another test rig, a robotic arm equipped with an oversize boxing glove beats up seat upholstery and foam materials to test the fatigue strength of an Opel seat. “We can also simulate passengers getting into and out of the vehicle, and we can vary the passenger parameters from the average 1.80 meters to an overweight person with a giant torso,” explains Tobias Friedrich, who recently finished his training as a technician.
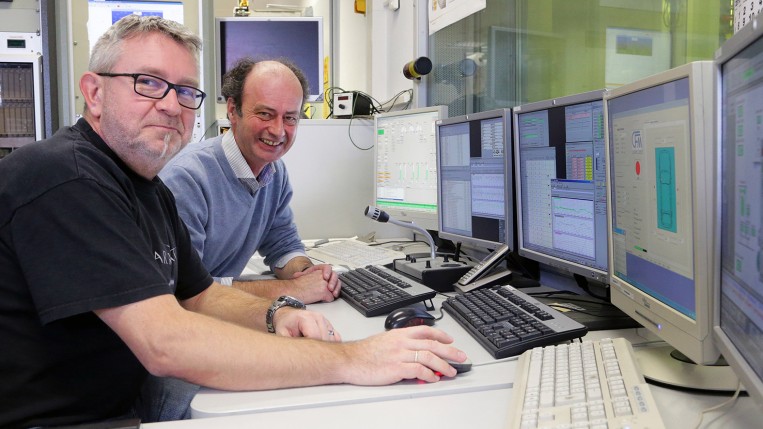
Rainer Wenz (links) und Otto Hemmelmann
“By now, our test series accompany the entire vehicle development process“
– Otto Hemmelmann –
TIME NEVER STOPS
The test facilities in P10 have been in operation since 2001. Time has never stopped since, because testing has to keep pace with the continuous and ongoing development of Opel vehicle technology. “For instance, nobody would have thought 20 years ago that we would ever have to test the electronic control of a hatch,” Otto Hemmelmann tells us.
As the number of internal customers keeps growing, the tasks become ever more varied and challenging. “By now, our test series accompany the entire vehicle development process,” explains the laboratory manager. In practice, this means that even as the first basic designs of a new Opel are created in the CAD (computer-aided design) program, the simulation specialists already have access to the data collected in the Structural Development Laboratory. Individual components have to be tested time and again during the product development process, with increasing complexity. In addition, validation tests for the complete vehicle have to be conducted shortly before the start of series production.
Careful advance planning is called for along with sophisticated time management. Simulating the entire life of a vehicle in four weeks may seem like a very short time, but having the test rig tied up for such an extended period can be a long time when other orders are waiting. Time is relative after all – especially in the Structural Development Laboratory.
February 2016