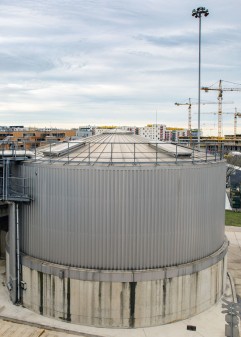
Der Abwasser-Sammel-Tank.
Wasser ist nicht gleich Wasser. Vor allem
nicht bei Opel Wien.
Wieder verwenden ist eine gute Sache. Auch beim Abwasser. So der Grundgedanke hinter einem Projekt, das Christian Völk/Plant Engineering mit dem Institut research TUb der Technischen Universität Wien umsetzte.
Was dabei klar wird: Wasser ist nicht gleich Wasser. Vor allem nicht bei Opel Wien. Denn da gibt es nicht nur Wasser aus der Städtischen Wasserleitung – das im Werk Aspern überwiegend als Trinkwasser und für die Sanitäranlagen genützt wird, sondern auch noch Brunnen. Insgesamt acht an der Zahl. Einer davon ist sogar 91 Meter tief. Aus diesem Brunnen schöpft das Werk Aspern seinen Wasserbedarf für die Produktionsprozesse. Aus den anderen Brunnen wird Löschwasser für die Feuerwehr, Wasser zum Gießen von Rasen, Sträuchern und Bäumen u.s.f. gewonnen.
Das Wasser, das in der Produktion eingesetzt wird, wird hauptsächlich für Kühlmittelanlagen, Waschmaschinen und Kühltürme benötigt. Damit alle diese Abläufe wirklich „wie geschmiert“ ablaufen, kommen Kühlschmierstoffe und Waschmittel der neuesten Generation zum Einsatz.
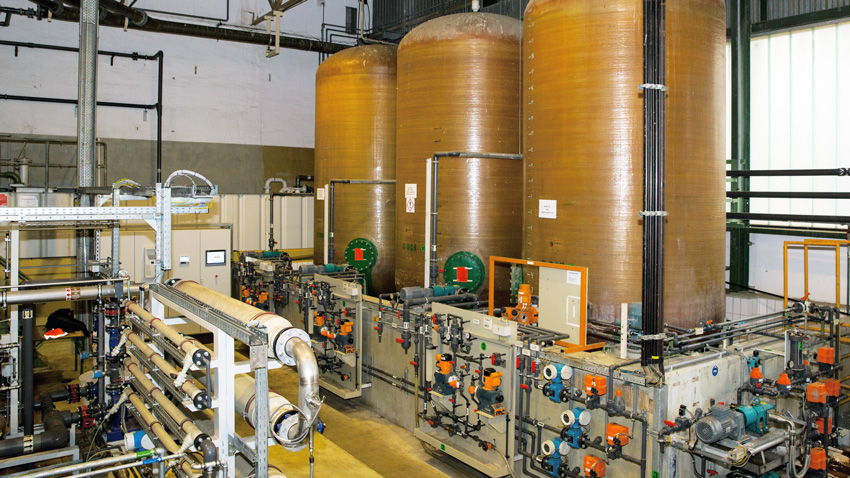
Öltrennanlage innen: Zu sehen sind die Behälter mit den Spaltchemikalien mit den zugehörigen Dosierpumpen sowie – im Vordergrund – die Mischelemente der Messstrecke und der Hauptstrecke.
Öl-Suppe
Nach der Verwendung in der Produktion wird das Öl-Wasser-Gemisch in einem 1.500 Kubikmeter Flüssigkeit fassenden Tank gesammelt. Danach – so lief es bisher – wurde das Abwasser, sobald mehr als 500 m3 davon im Sammeltank angesammelt waren, in einen der beiden Spaltbehälter gepumpt. Dort wurde mithilfe chemischer Zusatzstoffe das Öl vom Wasser getrennt und der Säuberungsgrad vermessen. Das Öl wurde in die Altölbehälter gepumpt, und das Wasser in die Öltrennanlage weitergeleitet. In der Nachspaltung wurden nochmals verschiedene Chemikalien zugesetzt, um auch noch das letzte vorhandene Öl abscheiden zu können. Das so behandelte Abwasser gelangte weiter in die Flotation. Dort schwamm das restliche Öl auf, wurde mit einem Räumer abgeschöpft und dann ebenfalls in die Altölbehälter gepumpt.
Nach all diesen Reinigungsvorgängen wurde das gereinigte Abwasser in den städtischen Kanal abgeleitet – natürlich unter Einhaltung der behördlichen Grenzwerte, die ständig kontrolliert wurden. Und das Altöl wurde von der Firma Saubermacher der thermischen Wiederverwertung zugeführt.
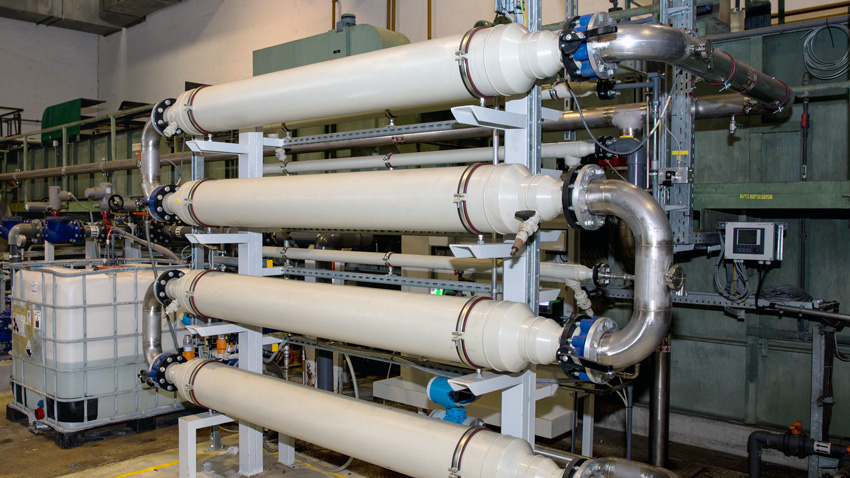
Mischeinheit im Hauptstrom.
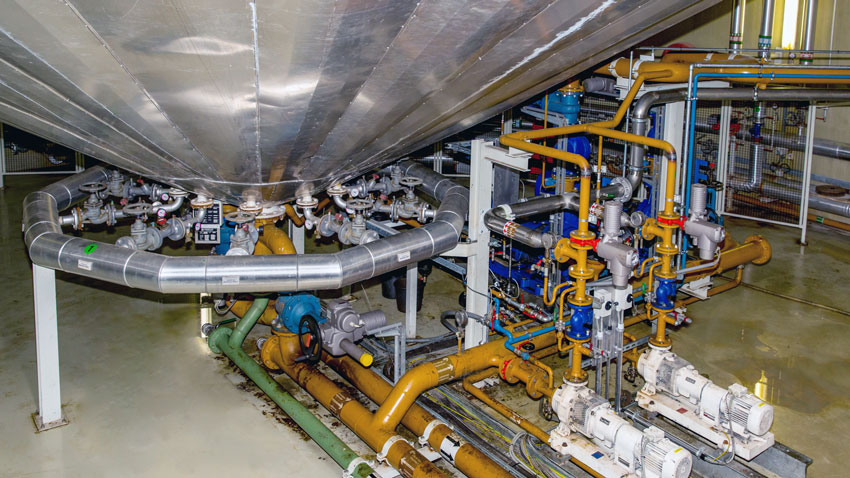
Im Keller unter dem Sammelbehälter: im Vordergrund die weißen Pumpen für die automatische Spaltung.
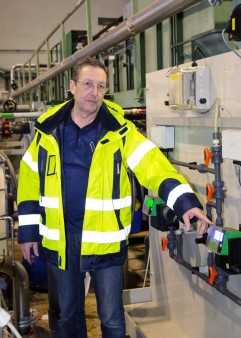
„Das ist die Dosierpumpe der Messstrecke“, zeigt Christian Völk.
Jetzt geht’s im Kreis
Jetzt läuft das System andersrum. Denn im Projekt mit dem research TUb-Institut wurde ein neuer Kreislauf geschaffen – das Abwasser wird nun zu 70 Prozent in der Produktion wieder verwendet.
Als erste Voraussetzung dafür wurde der Ablauf des Öl-Wasser-Spaltungsprozesses verändert. Dieser erfolgt nicht mehr tankweise, sondern kontinuierlich – mit ständigem Hinzufügen von Spaltmitteln. Was wiederum laufende Messungen in zwei neu geschaffenen Messstrecken erfordert. „Die richtigen Sensoren dafür zu finden, war ein Problem“, wirft Christian Völk ein. „Wie überhaupt das Messen eine besondere Herausforderung ist: Die Zusammensetzung des Abwassers ändert sich ja stündlich, je nachdem ob eine Pumpstation in den Sammelbehälter zurückpumpt oder ob es regnet und Abwasser von den beschichteten Flächen im Freien draußen zufließt.“
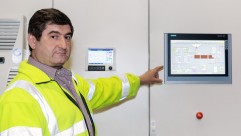
Erich Resnizcek vor dem Schaltschrank der Spaltanlage.
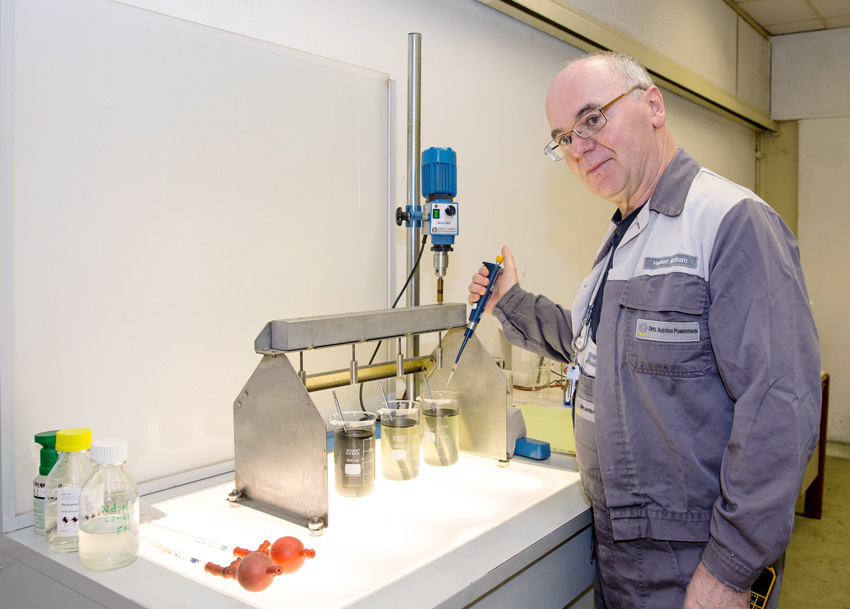
Herbert Neckam bei einem Spaltversuch im Labor.
Misch-Wasser
Nach dem Durchlaufen der Öltrennanlage wurden noch weitere neue Schritte eingeführt: Erstens wird das Klarwasser – das ist das Abwasser, das die Öltrennanlage bereits durchlaufen hat und von dem das Öl abgeschöpft wurde – zur Ultrafiltration gepumpt. Hier erfolgt eine erste Nachreinigung. Danach gelangt das Wasser in einem zweiten Schritt zur Umkehrosmose, so dass daraus vollentsalztes Wasser entsteht. Dabei wird das Wasser mit einem Druck von etwa 15 bar durch Spezialfilter gedrückt. „Wir bekommen dadurch weicheres Wasser, das Brunnenwasser ist ja eher hartes Wasser“, erklärt Völk. „Die passenden Filter dafür zu finden, war eine spezielle Aufgabe.“
Und das ist der umweltfreundliche Clou: Das durch Ultrafiltration und Umkehrosmose weichere Wasser wird nun neuerlich dem Produktionsprozess zugeführt. Damit benötigt das Werk Aspern weniger Brunnenwasser. Und leitet weniger Abwasser in die städtische Kanalisation ab.