Beim Zusammenstellen des Materialwagens für das Cockpit eines ADAM weiß der Eisenacher Kollege Ronald Liebmann, dass er trotz der großen Teilevielfalt immer genau das richtige Teil nimmt. Michael Müller und Willi Entenmann in der Lauterer Motorenmontage sind sich absolut sicher, dass sie immer die passende Schraube anziehen beziehungsweise die Lagerschale an der richtigen Position einlegen. Denn sowohl im thüringischen als auch im pfälzischen Werk sind smarte Helfer im Einsatz, die eine Fehlervermeidung in Echtzeit bewerkstelligen. Intelligente Schraubwerkzeuge, Datenbrille, Tracker am Handrücken oder Smartwatch – die intelligenten Assistenten sind Teil einer neuen Ära industrieller Fertigung: der so genannten „Smart Factory“.
Die Testszenarien haben das
Versuchslabor verlassen.
Die Weichen hin zur Werker-Assistenz der nächsten Generation werden im Internationalen Technischen Entwicklungszentrum (ITEZ) in Rüsselsheim im Bereich „Advanced Manufacturing Technologies“ (AMT) unter Leitung von Dr. Petra Krammer Hand in Hand mit den Kollegen aus den Bereichen Supply Chain und Manufacturing IT gestellt. „Bis zur Smart Factory, in der Maschinen, Menschen, Werkzeuge und Ressourcen miteinander nahtlos vernetzt sind und kommunizieren, ist es noch ein weiter Weg. Wir versuchen aber smarte Technologien, wie die Werker-Assistenzsysteme jetzt schon in unsere Werke zu bringen, um den Betrieb in Echtzeit optimieren zu können“, erläutert Krammer.
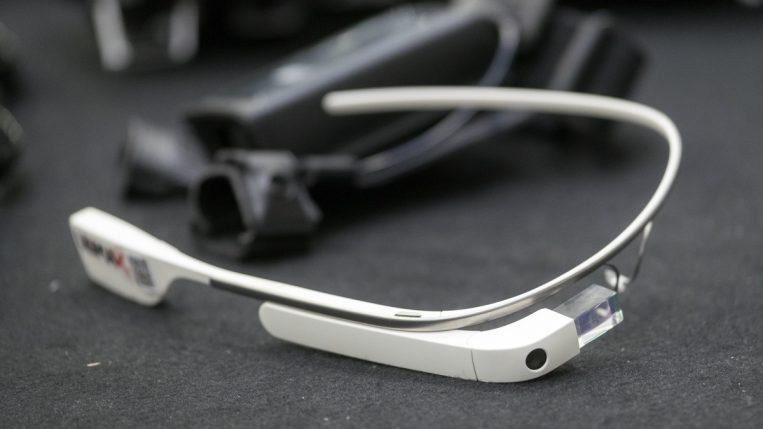
Smarter Assistent Die Datenbrille stellt Kommissionierern in Eisenach Informationen zur Verfügung, welches Teil als nächstes entnommen werden muss.
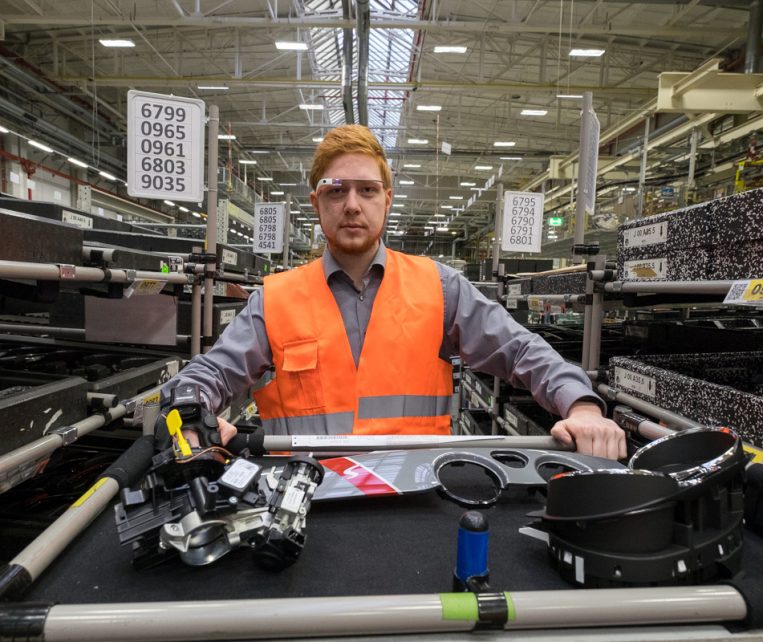
Vielfalt Allein beim Cockpit eines ADAM stehen 450 Einzelteile zur Auswahl.
In einem AMT-Versuchslabor hat Dr. Benjamin Kuhrke mit seinem Team die für die industrielle Fertigung weitestgehend neuen, aus dem eignen Alltag aber hinlänglich bekannten Technologien ins Visier genommen. „Wenn wir uns ein Fitnessarmband ans Handgelenk schnallen, das Daten per Bluetooth an das Smartphone überträgt oder wir uns Echtzeitdaten zur aktuellen Verkehrs- oder Wetterlage auf das Display holen, dann nutzen wir wie selbstverständlich diese smarten Helferlein, die aus unserem privaten Umfeld nicht mehr weg zu denken sind“, erläutert Kuhrke. Sein Team arbeitet bereichsübergreifend mit anderen ITEZ-Bereichen daran, deren Anwendungsmöglichkeiten in diversen Bereichen in den Werken auszuloten. Einige der erprobten Anwendungen haben inzwischen das Versuchslabor verlassen.
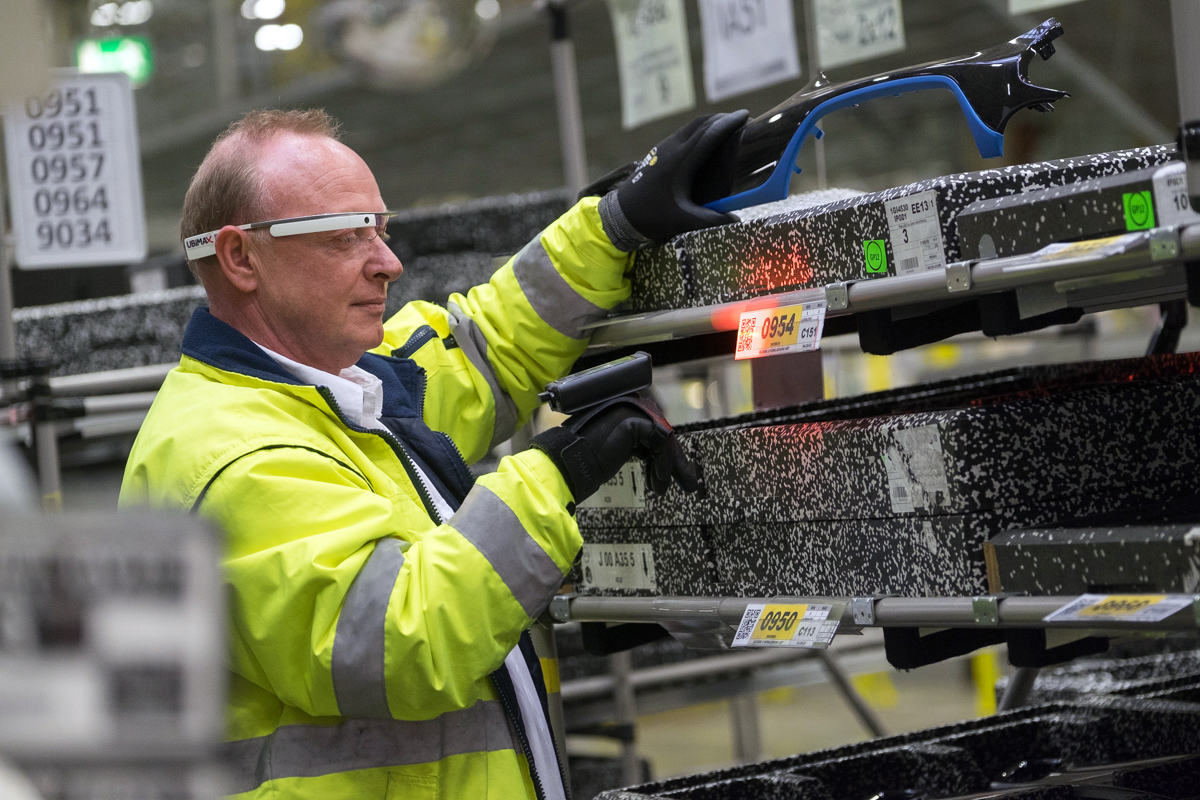
Fehlervermeidung in Echtzeit Die Teilenummer stimmt mit der Vorgabe überein – den entsprechenden Hinweis erhält der Kollege auf das Display der Datenbrille.
Beispiel 1: Kommissionieren in Eisenach
SPS-Station Cockpit, Opel-Werk Eisenach. Hier werden die jeweils 450 Cockpit-Teile für den ADAM und den Corsa kommissioniert, also zusammengestellt für den Einbau an der Linie. Die Spätschicht hat begonnen. Ronald Liebmann, seit 20 Jahren im Werk, fährt mit dem Materialwagen innerhalb der Station an dutzenden Materialkisten vorbei. Er bleibt stehen, entnimmt ein Teil, legt es auf das Rack und geht weiter. Der 57-Jährige trägt auf dem Handrücken einen Scanner, auf der Nase eine Datenbrille. Seit Mitte Januar werden an der Set-Part-System-Station für das Cockpit intelligente Helfer wie Scanner am Handrücken, Tablet, Smart-Watch und Datenbrillen eingesetzt. Mit dem Handscanner liest der Kollege den Auftrags-Code ein, Name und Codierung des zu pickenden Teils erscheinen vor seinem rechten Auge im Display der Datenbrille; die als nächstes zu entnehmende Nummer erscheint auf dem Display in Gelb. Ein grüner Haken signalisiert: Auftrag abgeschlossen. Ronald Liebmann hat sich als technisches Visualisierungsmittel für die Datenbrille entschieden, „weil das Arbeiten mit ihr eine schöne Sache ist und weil man die Hände frei hat“. Alternativ stehen eine Smartwatch oder ein Tablet zur Auswahl.
Zusammen mit einem Eisenacher Team unter Leitung von Frank Schäfer, Assistant Manager Supply Chain, und Thomas Döring vom Core-Team Supply Chain hat das Rüsselsheimer AMT-Team die technischen Neuerungen mit Unterstützung des Bereichs Manufacturing IT eingeführt. Aktuell werden von den 2.300 Teilen etwa 30 Prozent mit Hilfe von verschiedenen Qualitätssicherungssystemen sequenziert. Tendenz steigend.
„Der größte Vorteil der Assistenz-Systeme: Es entstehen so gut wie keine Fehler mehr, was Nacharbeiten reduziert und die Mitarbeiter bei der Arbeit entlastet.“
– Dr. Benjamin Kuhrke –
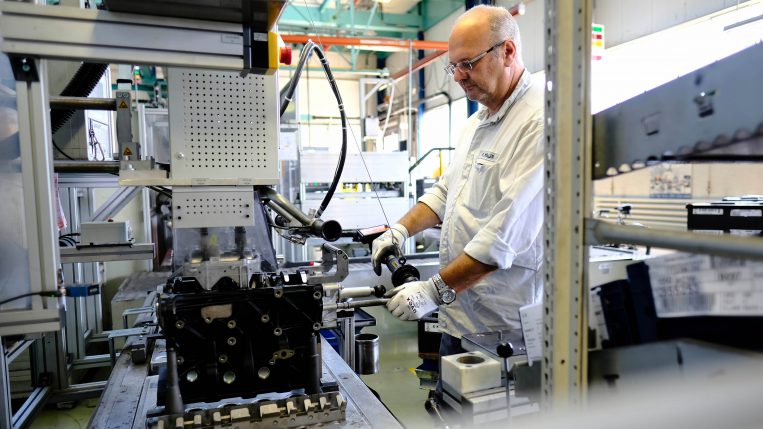
Ölpumpenmontage Michael Müller arbeitet mit Werkzeug, das ihm assistiert.
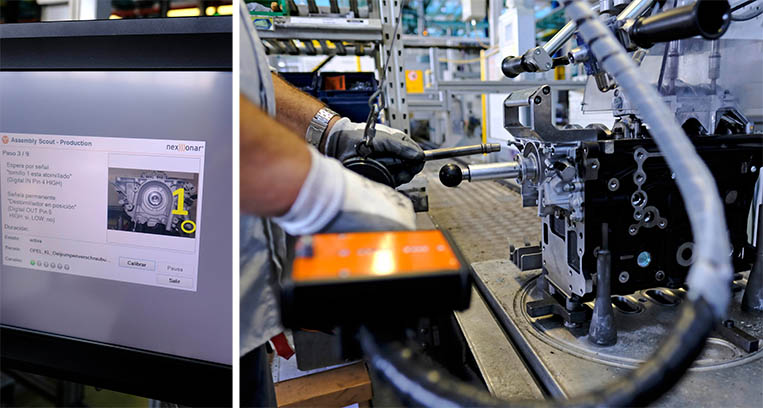
So funktioniert’s Der Monitor zeigt an, welche Schraube als nächstes angezogen werden muss (links), und der Tracker am Schrauber sorgt dafür, dass gar keine andere angezogen werden kann (rechts).
„Wenn ich eine falsche Schraube anziehen möchte, blockiert es solange, bis ich an der richtigen angesetzt habe.“
– Michael Müller –
Beispiel 2: Intelligentes Werkzeug in Lautern
Michael Müller arbeitet seit zwölf Jahren in der Motorenmontage im Opel-Werk Kaiserslautern, aktuell als Teamleader. Längst ist ihm der Umgang mit seinen Werkzeugen in Fleisch und Blut übergangen. Doch ein Schraubwerkzeug wie das, mit dem er derzeit an der Ölpumpe arbeitet, hat er noch nie in der Hand gehabt. Es lässt sich nicht nur einwandfrei handhaben, es scheint sogar mitzudenken: „Wenn ich eine falsche Schraube anziehen möchte, blockiert es solange, bis ich an der richtigen angesetzt habe.“
Fehlervermeidung in Echtzeit also. Technisch ermöglicht wird dies mithilfe eines „Infrarot-Trackers“, der an dem Schrauber angebracht ist. Eine Infrarot-Kamera erfasst alle Bewegungen des Werkzeugs und kontrolliert deren korrekten Ablauf. Michael Müller verfolgt alles unmittelbar von seinem Arbeitsplatz über einen Monitor: Hier wird der nächste Bearbeitungsschritt visualisiert und der zuletzt ausgeführte bewertet. Somit ist nicht nur völlige Fehlervermeidung, sondern auch optimale Transparenz gewährleistet.
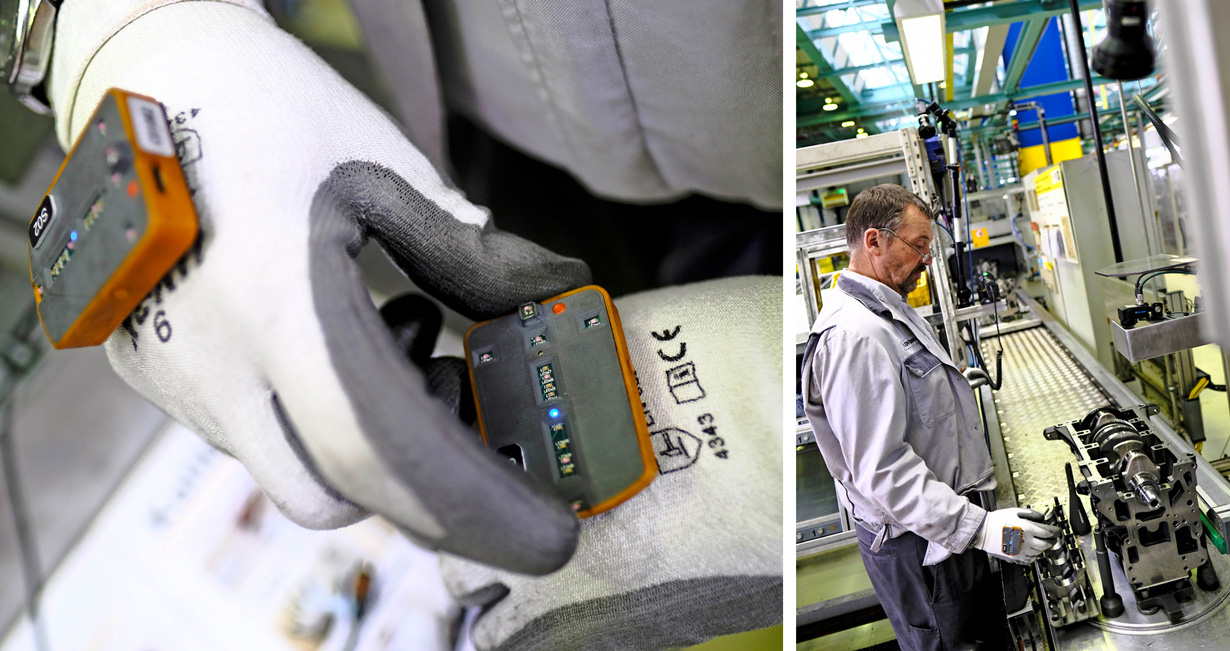
Beispiel 3: Zylinderkopfmontage in Lautern Willi Entenmann trägt einen Motion Tracker auf dem Handrücken. Dieser überwacht den Einsatz der richtigen Lagerschale in Echtzeit. Das faszinierende dabei: Das System arbeitet so genau, dass Fügestellen, die nur wenige Zentimeter auseinanderliegen, sicher erkannt werden. Es ist der erste Versuch, bei dem der Tracker auf dem Handrücken eines Mitarbeiters installiert ist. Seine Finger dienen dabei quasi als Sensoren.
Weitere Ideen sind in Arbeit.
Besonders für das Infrarotsystem hat man noch nicht alle möglichen Anwendungsfälle ausgeschöpft. Bei der Sequenzierung von Seitenscheiben in Eisenach werden derzeit auch Datenbrillen in Kombination mit Handrückenscannern getestet. Das Infrarotsystem wird hier den Scanner ablösen, um die Entnahme der Seitenscheiben aus den Boxen und das Ablegen im Sequenzwagen automatisch, und damit ohne „Zeitverschwendung“, zu überwachen. Zum Einsatz kommen in diesem Fall Tracker, die man per Klett am Schweißband befestigen kann.
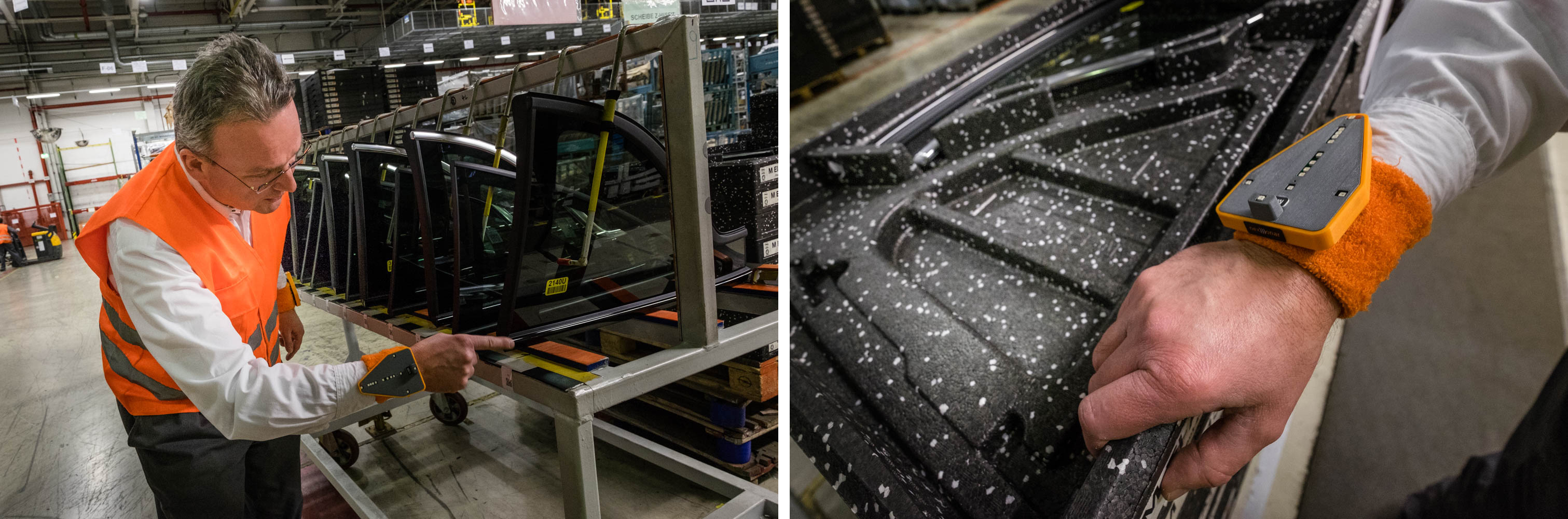
In Vorbereitung Neben den aktuellen Pilotprojekten arbeitet das AMT-Team an weiteren Ideen im Bereich der smarten Werker-Assistenz. Frank Schäfer demonstriert in Eisenach einen Tracker, der direkt am Schweißband befestigt werden kann. Mit ihm soll künftig die Entnahme von Seitenscheiben überwacht werden.
Weitere Anwendungsbeispiele aus der Industrie 4.0-Welt sind Tablet basierte Lösungen: Reale Objekte werden mit den Daten virtueller Objekte überlagert. So lassen sich Ist- und Sollzustand zu Qualitätszwecken vergleichen – das Stichwort lautet Augmented Reality, also die erweiterte Realität. Wieder zurück auf der Nase, also als Datenbrille, können damit auch neue Mitarbeiter bei der Einarbeitung oder Instandhalter bei der Reparatur von Maschinen unterstützt werden. Es werden schon bald weitere Ideen das AMT-Versuchslabor verlassen.
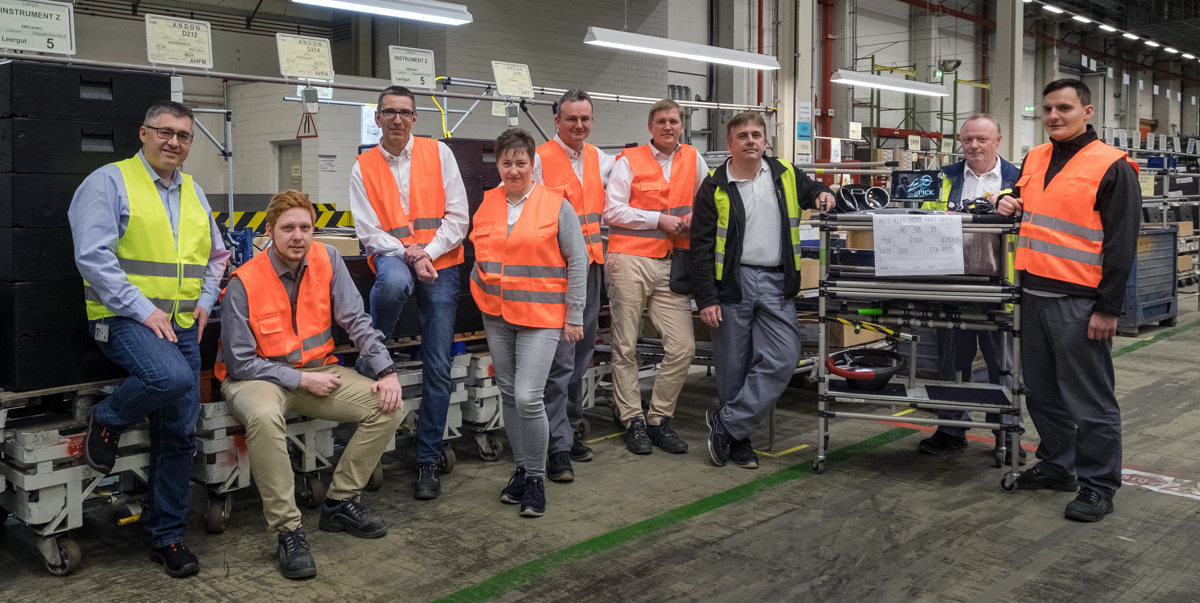
Das Team, das die smarte Werker-Assistenz nach Eisenach gebracht hat (von links) Frank Bartnik (Manufacturing IT), Sebastian Wörlein (KIS Student bei AMT), Frank Walper (Manufacturing IT), Annett Kästner (Werk Eisenach), Frank Schäfer (Werk Eisenach), Dr. Benjamin Kuhrke (AMT), Thomas Döring (Werk Eisenach), Thomas Bradsch (Werk Eisenach) und Enrico Theeg (Werk Eisenach).
Stand Februar 2017