Despite his young age of just 24, Hans-Sebastian Wilhelm at the Kaiserslautern production facility has a lot of experience. The trained industrial mechanic has already worked in front wheel mount construction and maintenance, among other areas. He volunteered to work in the new seat production operation in production hall K20. “What attracted me was the fact that you really get to see the entire product being created, from the raw sheet metal right through to the finished seat,” he says.
The production division welds and assembles three basic seat variations: two, four and six-way seats. It is also necessary to differentiate between left and right seats. What’s more, there are also power versions. These seats feature an electric engine that can make particular movements. In total, 13 different types are produced in the first stage of expansion in Kaiserslautern. Further eight types are added for a follow-up model.
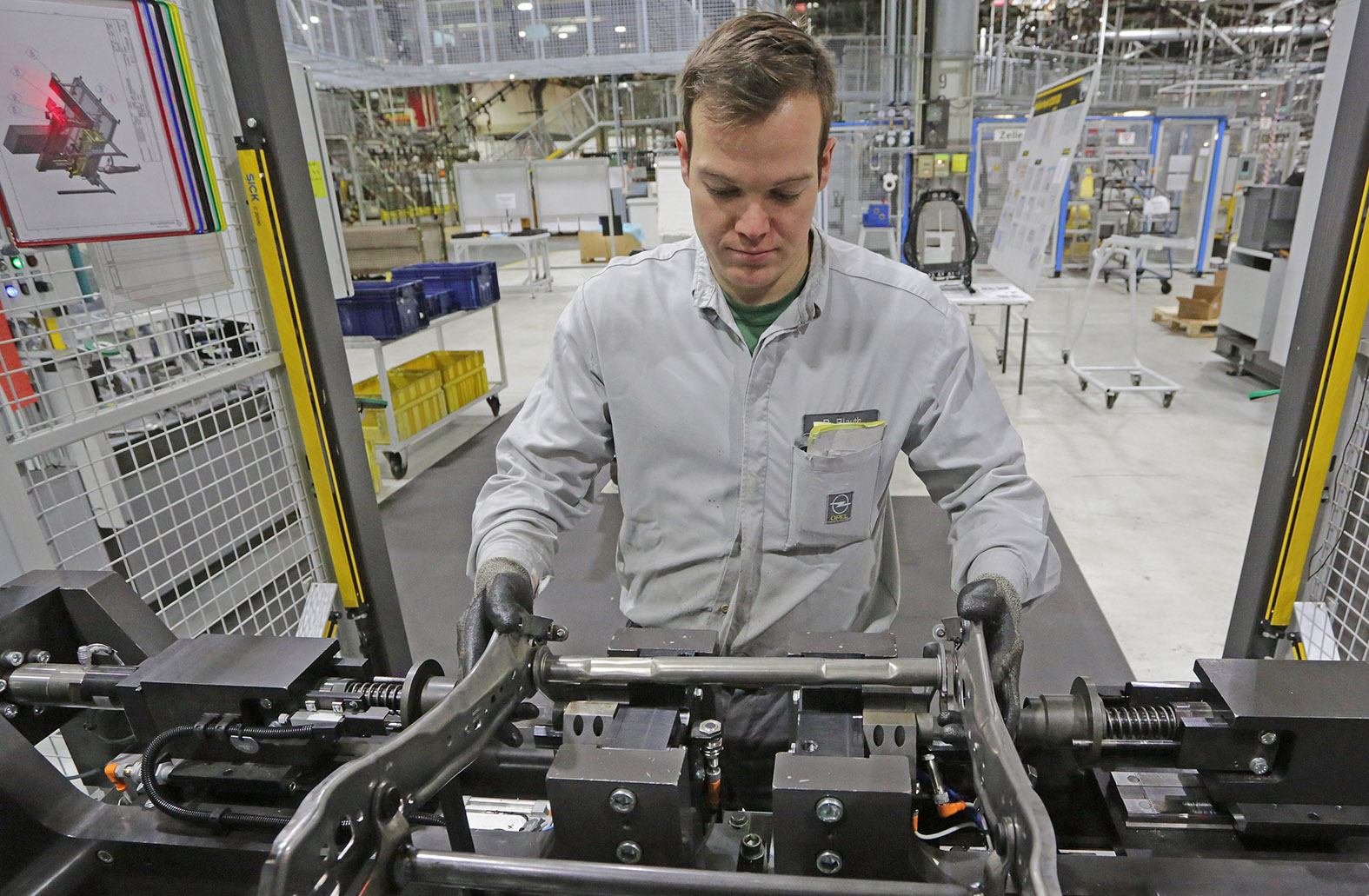
Seat manufacturing: Patrick Blauth at his individual workstation.
“After 40 years of experience manufacturing seating components, it’s the first time in Kaiserslautern that seat backs and seat covers will be not only be welded, but also fully assembled,” explains Michael Schmitt, Area Manager Chassis and Seat Components. In order to master the challenge at the highest productive and qualitative level, the Kaiserslautern team is breaking new ground in many respects, both in terms of technology and processes as well as in terms of the qualification of personnel.
TECHNICAL PRODUCTION SPECIALISTS: PILOT CONCEPT
Young technical specialists form the nucleus of the division. Working alongside Hans-Sebastian Wilhelm are Patrick Blauth , Carsten Schweitzer, Julian Adrian, Felix Heinen, Florian Koning, and Carsten Müller.
They are workers, maintenance employees, and team leaders all rolled into one. “We’re pursuing a new concept that the management and works council agreed on, and it’s a pilot concept in seat production,” explains Area Manager Michael Schmitt.
For this reason, there are all kinds of new policies in seat production. For example, each seat is labeled upon completion. The bar code contains precise information about who manufactured the component, when it was constructed, and under which conditions it was manufactured.
STEPPING AWAY FROM THE ASSEMBLY LINE – AN INNOVATION?
The division is set to have a total of around 24 technical production specialists like Patrick Blauth. “At least two of them will be deployed in every team in the final stage,” explains Schmitt. “If there is a problem on a system, the technical production specialist simply switches workstations with the worker and takes care of it.”
The core maintenance team from production hall K20 is also part of the project. It will provide the technical production specialists with support during the start-up phase and step in to handle any large-scale maintenance and repair work during series manufacturing. For the most part though, the teams of technical production specialists will complete maintenance work themselves.
The individual workstations where Hans-Sebastian Wilhelm and Patrick Blauth now assemble seats are the most obvious innovation in the new division. Is this step away from the line really an innovation? Or is it more of a step back to the early stages of industrial production before Henry Ford invented the assembly line?
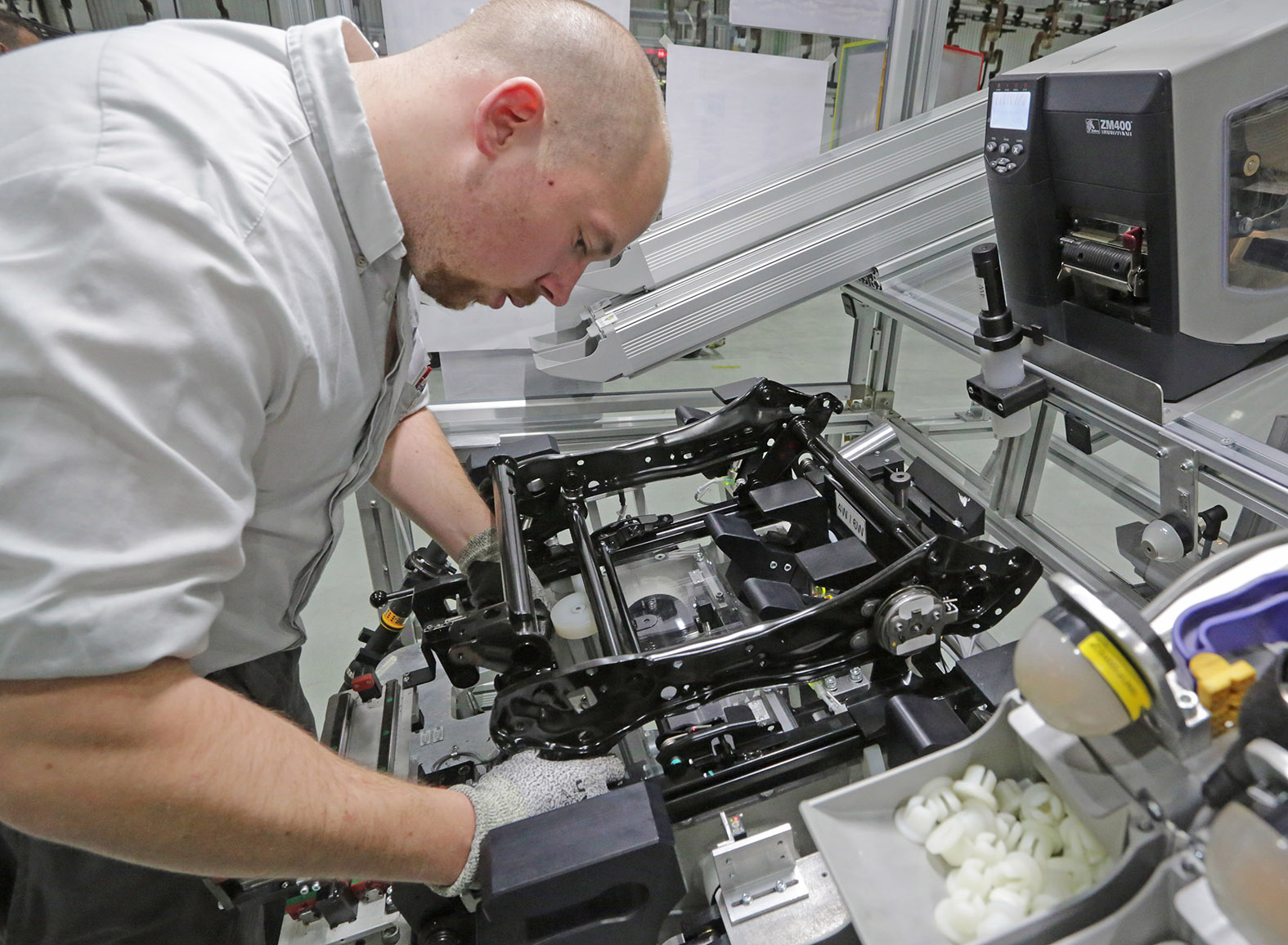
Everything has to fit perfectly: Hans-Sebastian Wilhelm takes a close look.
INDIVIDUAL WORKSTATIONS: MANY ADVANTAGES OVER AN ASSEMBLY LINE
“Only if you look at the face of it,” says Area Manager Schmitt with a smile. “In terms of technology, we are absolutely groundbreaking in terms of a modern seat structure production, even when it comes to documentation and error prevention systems.” For the purposes of this project, individual workstations offer several advantages over production on a line. First of all, they are particularly cost effective. “A line has to be completely installed at the start of production. With individual workstations, I can install them gradually when the start-up curve grows.”
There are two stations in operation in the current validation phase, and there will be six in the final stage. When you have a line, it always has to be staffed with a fixed number of workers in order to ensure they can work efficiently. “Individual workstations allow you to respond more flexibly to increasing or decreasing levels of demand. If I have to operate additional shifts on the weekend, I can take my time and work out beforehand whether I really need to man every station,” says Schmitt.
Another advantage of the individual workstation principle is when it comes to training new employees, explains Schmitt: “A line is only as fast as the slowest produce link in the chain. This is not the case for individual workstations. But of course, new semi-skilled employees initially need a little more time.”
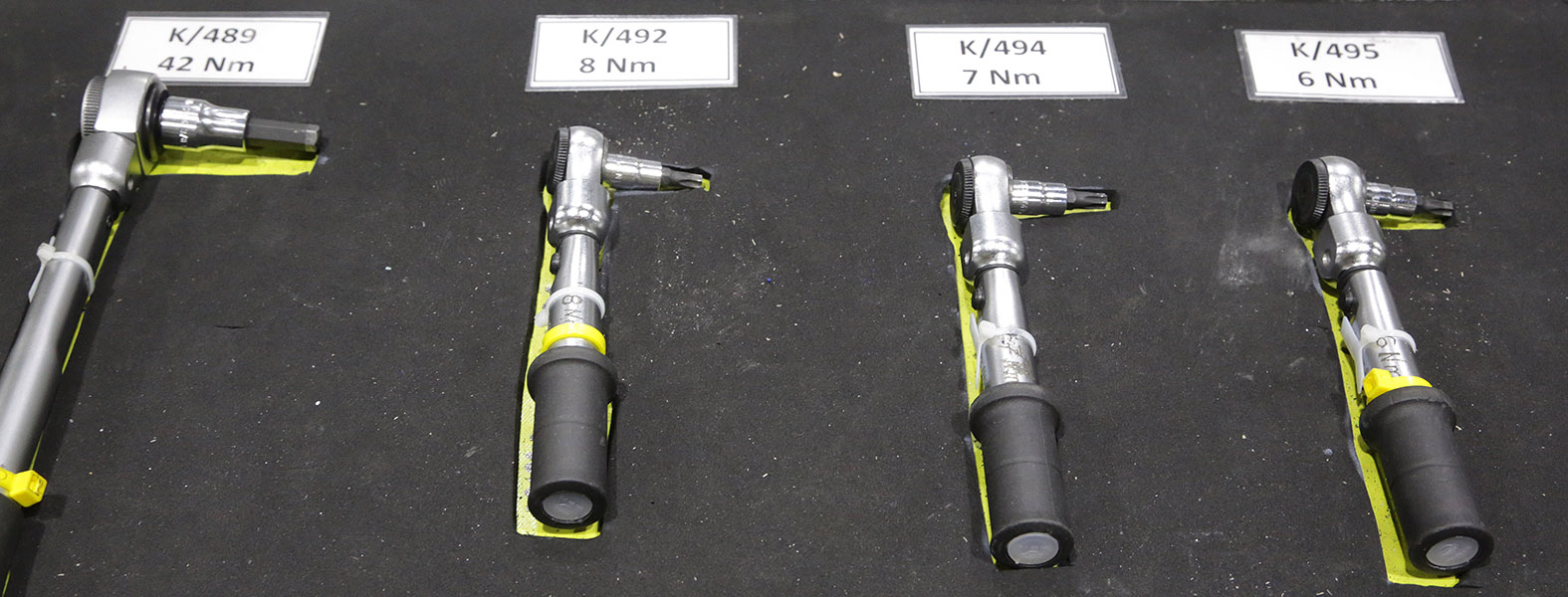
Millimeter precision is the order of the day: The test equipment helps to ensure it.
A MIX OF MOTIVATION AND RESPONSIBILITY
The new division offers another advantage: It is the special way the employees identify with the product. Assembling the entire seat and then being able to hold the finished product, minus the upholstery, motivates employees in a special way, as Hans-Sebastian Wilhelm confirms. Yet it also comes with enormous responsibility. This is because each seat is labeled upon completion. The bar code on the label contains accurate information about who has the component when and with which values such as torque, angle or processes it was produced..
The division also scores with various technical innovations. Let’s take a look at an example: The individual components for height adjustment were assembled in the new Tube End Forming (TEF) system. It installs without welding or gluing. Rather, it deforms, compresses, and presses steel. This is a highly efficient and accurate process. “Height adjustment on the TEF tubing cannot under any circumstances deform in the event of a crash,” explains Area Manager Schmitt. “We quality check the TEF tubing with the force of 400 Newton meters, or in other words, with the power of a diesel engine made in Kaiserslautern.”
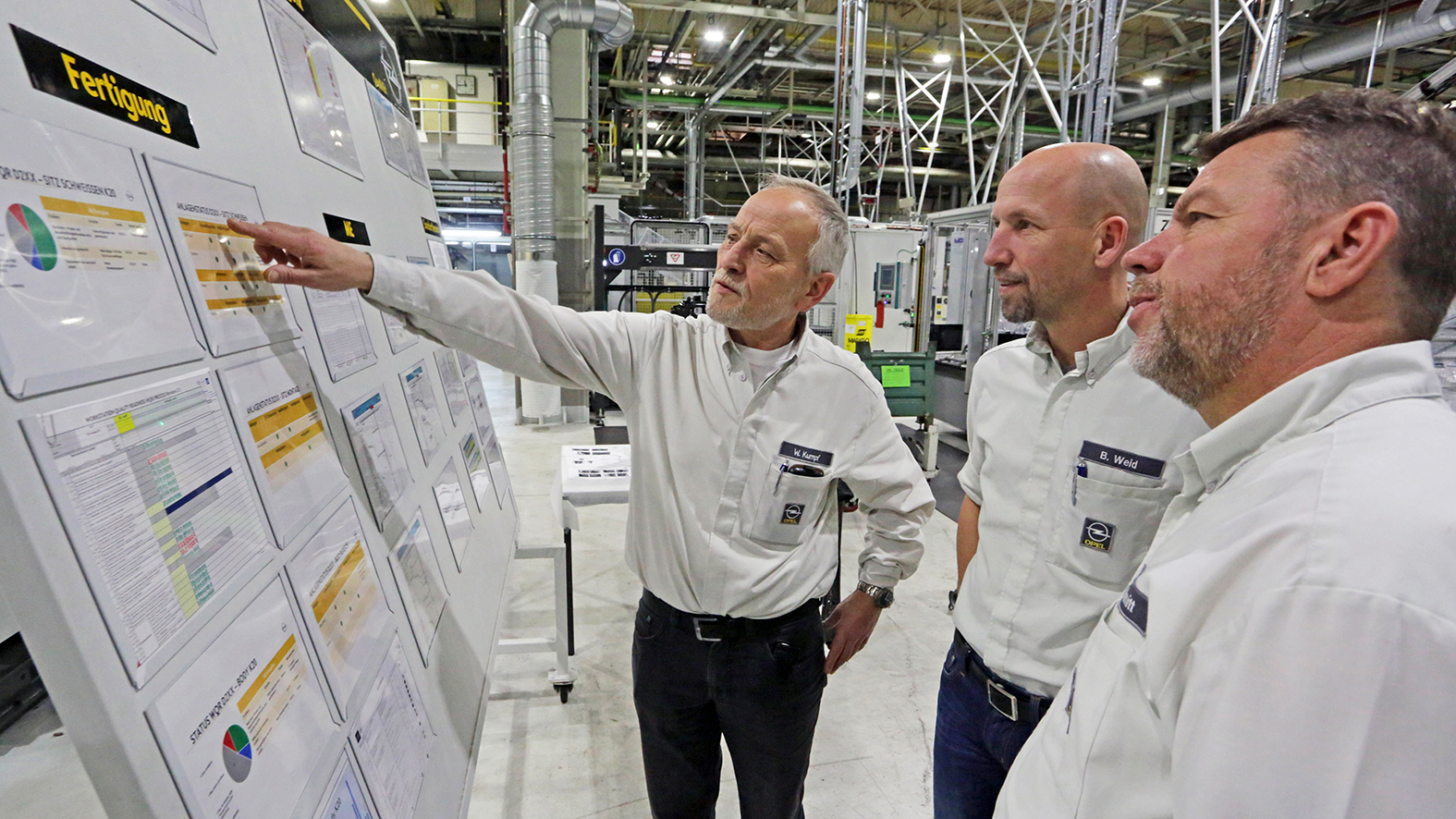
Discussing the situation: Area Manager Michael Schmitt (right) with his colleagues Werner Kumpf (left) and Bernd Weid.
ERRORS ARE ELIMINATED
This 100-percent final seat inspection is new in Kaiserslautern. It sees all traverse forces precisely measured. There is also an ease of movement check for unlocking. At the end of the day, it is these details that lead customers to consider a product to be of high quality.
Nothing is left to chance when it comes to the transport rack for customers in Gliwice and Ellesmere Port. A green light tells the employee which container to place the respective seat variation into. If he makes a mistake, a red light immediately flashes. This pick to light system was skillfully implemented by Michael Klaffke and his team, which is responsible for the Ongoing Improvement Process (OIP) in the welding area of K20, as well as the trainees currently being trained in maintenance in production hall K20. The stylish cube on the ceiling of the production hall characterizes the division visually. It is designed to ensure that the new Kaiserslautern seat production operation is technically, organizationally, and visually future-oriented for the production site.
By the way, the seats will be used first in the new Astra generation.
40 YEARS AGO
Did you know? Seat production has a longer history in Kaiserslautern than engine manufacturing. In 2013, the Opel plant in Kaiserslautern celebrated its 40th anniversary since launching production.
Over 38 million seating components have been built in Kaiserslautern since then. In order to remind employees and visitors of this fact, Michael Schmitt, Area Manager Chassis and Seat Production, has set up a small museum of sorts in his division. It showcases the different generations of seats side by side for visitors to marvel at.
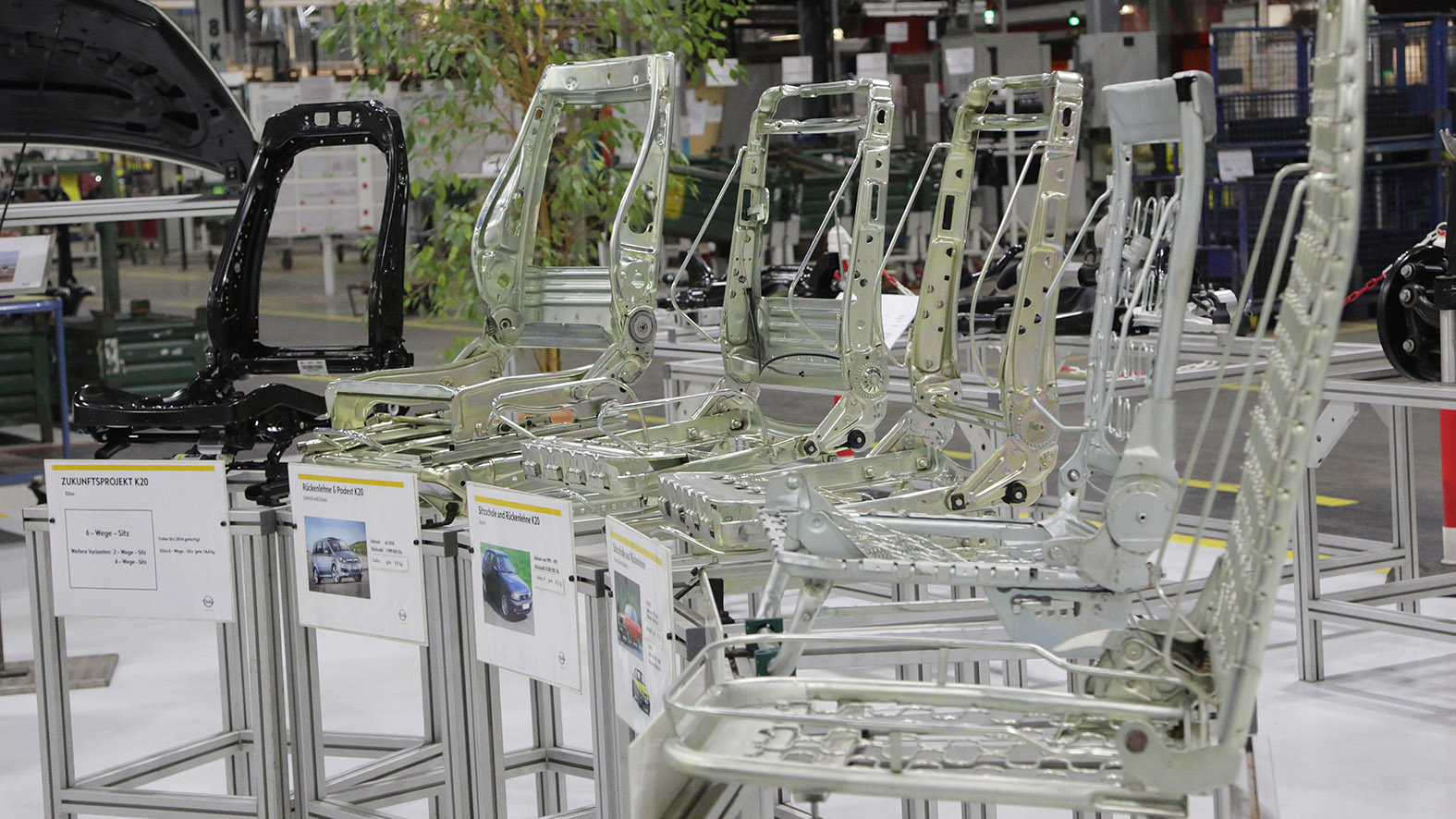
A short history of the seat: A small exhibition opens up an opportunity to review 40 years of seating production in Kaiserslautern.
The seats were used in Opel GT, Ascona, Manta, Kadett, and Astra models. “Above all else, this documents the speed at which the Opel seats developed constructively,” says Michael Schmitt.
Three-millimeter thick sheet metal still was used on the first models, explains Schmitt. “We now rely on high-strength steel that’s just 0.6 millimeters thick.” To process that, it takes a team with a lot of experience – “which we have in Kaiserslautern, as the exhibition documents impressively.”