Trotz seiner erst 24 Jahre ist Hans-Sebastian Wilhelm am Produktionsort Kaiserslautern viel herumgekommen. Der gelernte Industriemechaniker hat unter anderem bereits im Vorderradträgerbau und in der Instandhaltung gearbeitet. In die neue Sitzfertigung in der Produktionshalle K20 hat er sich freiwillig gemeldet. „Es hat mich gereizt, dass man hier quasi das komplette Produkt entstehen sieht, vom rohen Blechteil bis zum fertigen Sitz“, sagt er.
In dem Fertigungsbereich werden drei Grundvarianten von Sitzen geschweißt und montiert: Zwei-, Vier- und Sechs-Wege-Sitze, zudem muss zwischen linken und rechten Sitzen unterschieden werden. Darüber hinaus gibt es „Power“-Varianten, also Sitze, an denen Elektromotoren bestimmte Bewegungen ausführen. In Summe werden in Kaiserslautern 13 unterschiedliche Varianten in der ersten Ausbaustufe gefertigt. Für ein Folgemodell kommen noch weitere acht Typen hinzu.
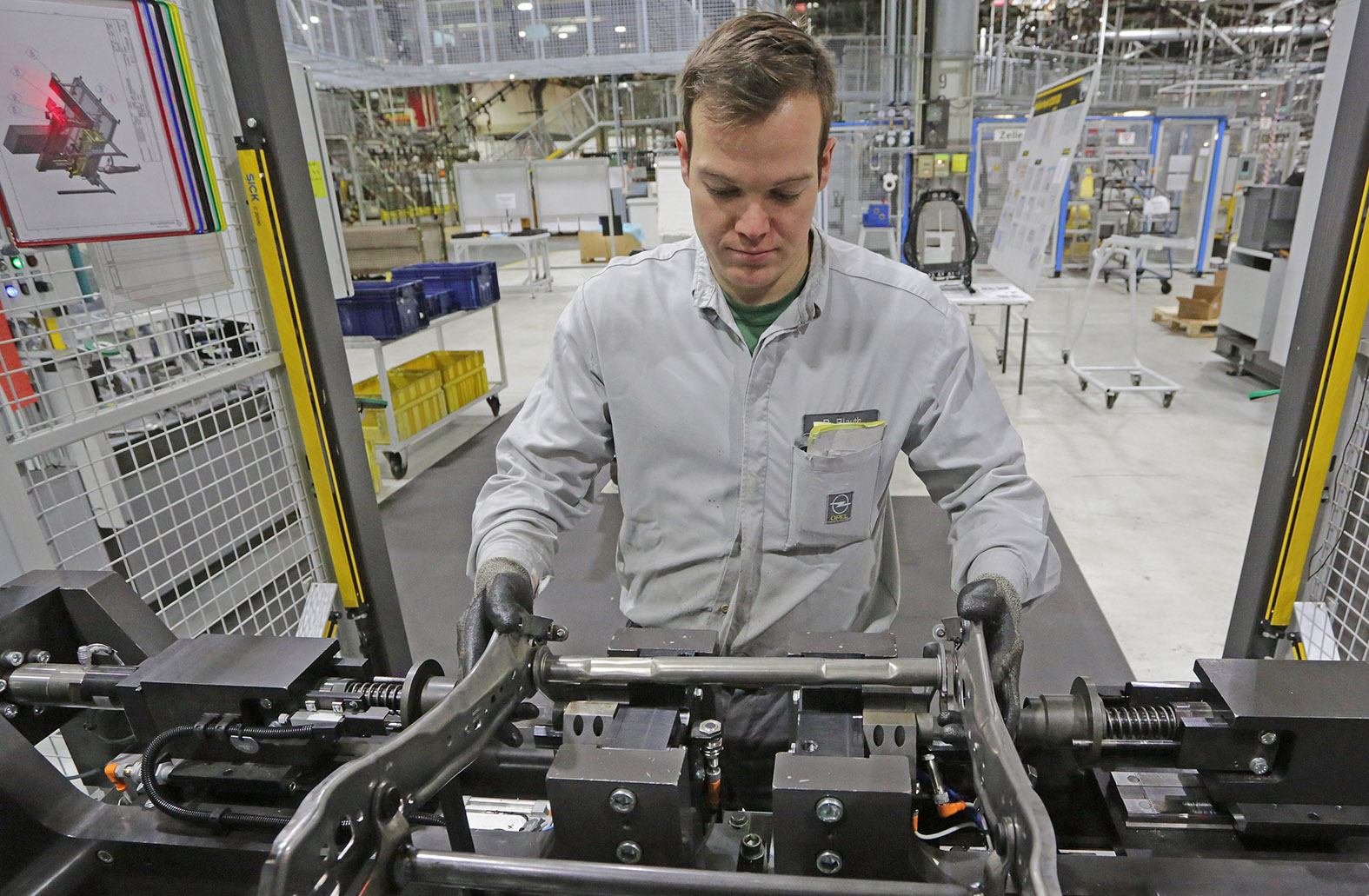
Sitzfertigung total: Patrick Blauth am Einzelarbeitsplatz.
„Nach über 40 Jahren Erfahrung in der Herstellung von Sitzkomponenten ist es das erste Mal, dass wir in Kaiserslautern Sitzrücken und Sitzauflagen nicht nur schweißen, sondern auch montieren“, erklärt Michael Schmitt, Area Manager Chassis- und Sitzkomponenten. Um die Herausforderung produktiv und qualitativ auf höchstem Niveau zu meistern, beschreiten die Pfälzer gleich in mehrerer Hinsicht neue Wege – sowohl bei Technik und Abläufen als auch in puncto Qualifikation des Personals.
FERTIGUNGSFACHARBEITER: KONZEPT MIT PILOTCHARAKTER
Die „Keimzelle“ des Bereichs bilden die Jungfacharbeiter, neben Patrick Blauth sind das Hans-Sebastian Wilhelm, Carsten Schweitzer, Julian Adrian, Felix Heinen, Florian Koning und Carsten Müller.
Sie sind Werker, Instandhaltungsmitarbeiter und zum Teil auch Teamleiter in einer Person. „Damit folgen wir einem neuen Konzept, das Geschäftsleitung und Betriebsrat vereinbart haben, und das in der Sitzfertigung nun Pilotcharakter hat“, erklärt Area Manager Michael Schmitt.
Die Sitzfertigung kommt mit jeder Menge Erneuerungen daher, eine davon: Jeder Sitz wird nach Fertigstellung gelabelt. Der Strichcode enthält exakte Informationen, wer das Bauteil wann und mit welchen Vorgaben hergestellt hat.
WEG VON DER LINIE – EINE INNOVATION?
Insgesamt soll es in dem Bereich rund 24 solcher Fertigungsfacharbeiter geben. „In der Endausbaustufe sollen in jedem Team mindestens zwei von ihnen eingesetzt werden“, sagt Schmitt. „Gibt es an einer Anlage ein Problem, tauscht der Fertigungsfacharbeiter einfach seinen Arbeitsplatz mit dem des Werkers, wo er sich um die Behebung des Problems kümmert.“
Natürlich ist auch die Kerninstandhaltung des K 20 in das Projekt eingebunden. Sie wird den Fertigungsfacharbeitern in der Anlaufphase unterstützend mit Rat und Tat zur Seite stehen und auch bei größeren Wartungs – oder Reparaturarbeiten während der Serienfertigung zum Einsatz kommen.
Der Einzelarbeitsplatz, an dem gegenwärtig Hans-Sebastian Wilhelm und Patrick Blauth Sitze montieren, ist die augenfälligste Innovation in dem neuen Bereich. Weg von der Linie – eine Innovation? Ist das nicht viel eher ein Sprung zurück in die ganz frühe Phase industrieller Produktion, als Henry Ford das Fließband noch nicht erfunden hatte?
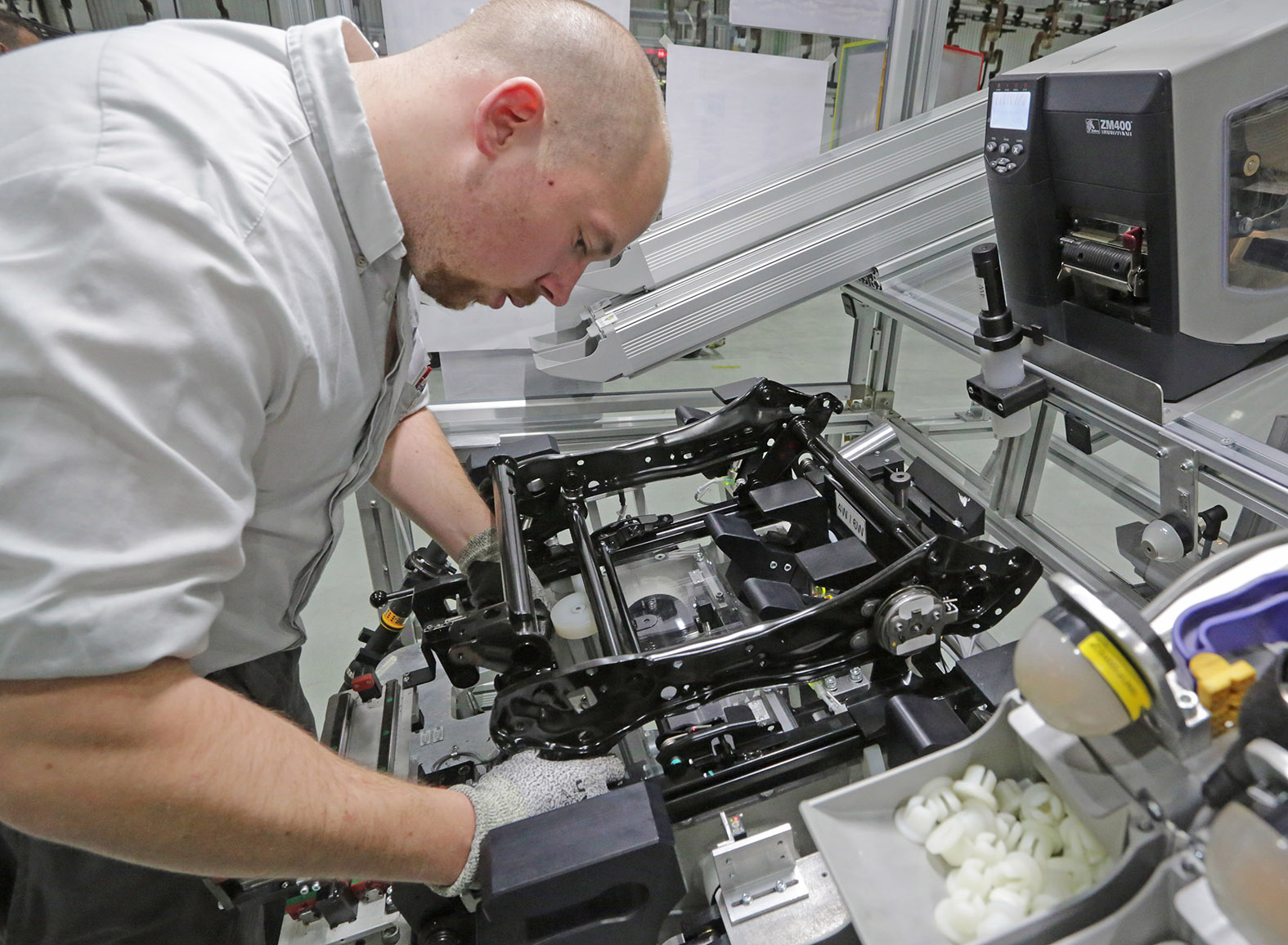
Alles muss passen: Hans-Sebastian Wilhelm schaut genau hin.
EINZELARBEITSPLÄTZE: VIELE VORTEILE GEGENÜBER DER LINIE
„Nur, wenn man es ganz oberflächlich betrachtet“, schmunzelt Schmitt. „Technisch sind wir absolut zukunftsweisend in Bezug auf eine moderne Sitzstrukturfertigung, gerade auch bei den Themen Dokumentation und Fehlervermeidungssysteme.“ Bei dem Projekt bieten Einzelarbeitsplätze laut Schmitt gleich mehrere Vorteile gegenüber einer Linienfertigung. Zum einen seien sie besonders kostenfreundlich. „Eine Linie muss zum Produktionsstart komplett aufgebaut sein. Einzelarbeitsplätze kann ich, wenn die Anlaufkurve ansteigt, nach und nach installieren.“ In der aktuellen Validierungsphase sind zwei Stationen in Betrieb, in der Endausbaustufe werden es sieben sein.
Eine Linie muss stets auch mit einer festen Anzahl von Werkern bestückt sein, damit sie effizient arbeiten kann. Schmitt: „Bei Einzelarbeitsplätzen dagegen kann ich flexibler auf steigende oder sinkende Nachfragen reagieren. Wenn ich am Wochenende Zusatzschichten fahre, kann ich mir vorher in Ruhe ausrechnen, ob ich wirklich jede Station besetzen muss.“ Ein weiterer Vorteil ergibt sich beim Anlernen neuer Mitarbeiter: „Eine Linie kann immer nur so schnell produzieren wie das langsamste Glied in der Kette. Das ist bei Einzelarbeitsplätzen nicht der Fall. Aber selbstverständlich brauchen neu angelernte Mitarbeiter anfangs etwas mehr Zeit.“
Ein weiterer Vorteil des Prinzips Einzelarbeitsplatz ergibt sich beim Anlernen neuer Mitarbeiter, erläutert Schmitt: „Eine Linie kann immer nur so schnell produzieren wie der langsamste Werker. Bei Einzelarbeitsplätzen ist es nicht weiter schlimm, wenn jemand etwas mehr Zeit zum Einarbeiten braucht – sofern die anderen die geforderte Taktzahl halten.“
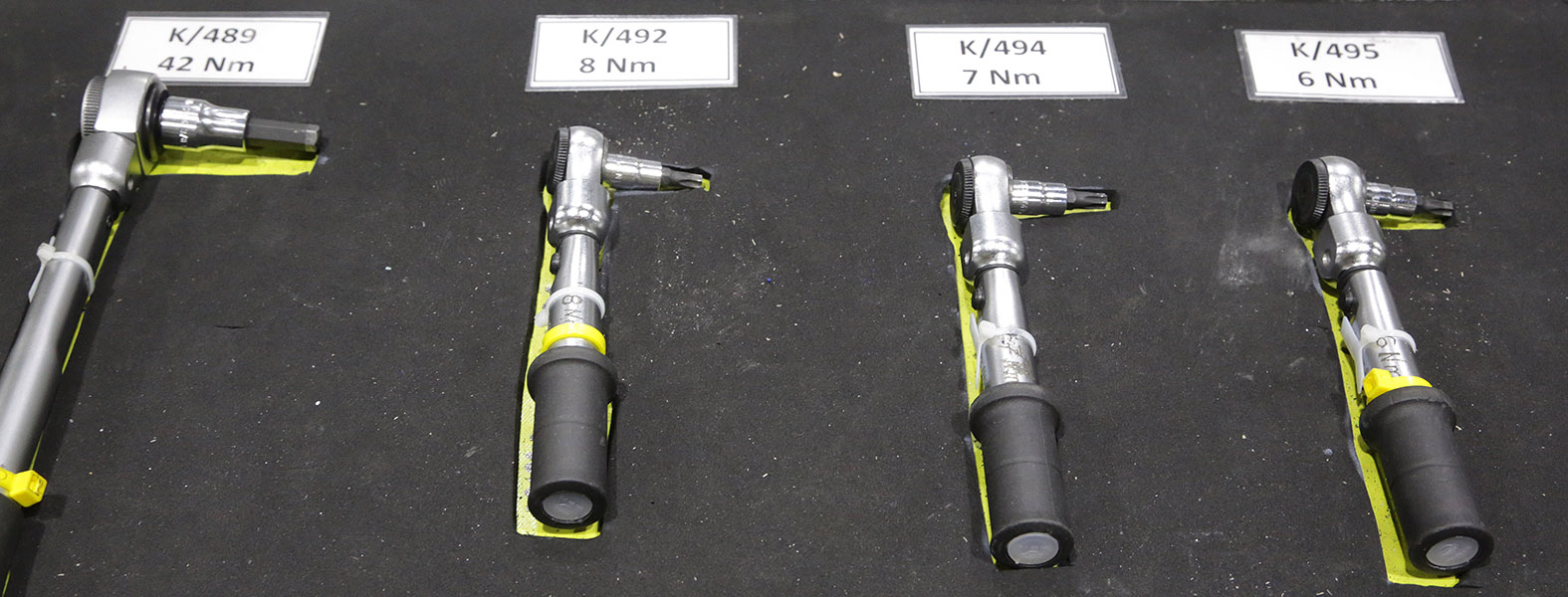
Millimetergenaue Präzision ist angesagt: Die Prüfmittel helfen, sie zu gewährleisten.
MOTIVATION UND VERANTWORTUNG ZUGLEICH
Ein weiteres Plus, das der neue Bereich mitbringt: die besondere Identifikation der Mitarbeiter mit dem Produkt. Den kompletten Sitz montieren und am Ende das – bis auf die Polsterung – fertige Produkt in Händen halten zu dürfen, das motiviert in spezieller Weise, wie auch Hans-Sebastian Wilhelm bestätigt. Wenngleich damit auch eine norme Verantwortung einhergeht. Denn jeder Sitz wird nach Fertigstellung gelabelt. Der Strichcode enthält exakte Informationen, wer das Bauteil wann und mit welchen Werten wie Drehmoment, Drehwinkel oder Verfahrkräften hergestellt hat.
Darüber hinaus punktet der Bereich mit technischen Innovationen. Ein Beispiel: Die Einzelteile für die Höhenverstellung werden in der neuen „Tube End Forming“-Anlage (TEF) zusammengefügt. Sie befestigt ohne Schweißen oder Kleben, sondern, indem sie Stahl verformt, staucht und verpresst – ein enorm effizientes und präzises Verfahren. „Die Höhenverstellung am TEF-Rohr darf sich beim Crash auf keinen Fall verformen“, erklärt Area Manager Schmitt. „Bei der Qualitätsprüfung des TEF-Rohres überprüfen wir das mit Kräften von 400 Newtonmetern, also mit der Power eines Lauterer Dieselmotors.“
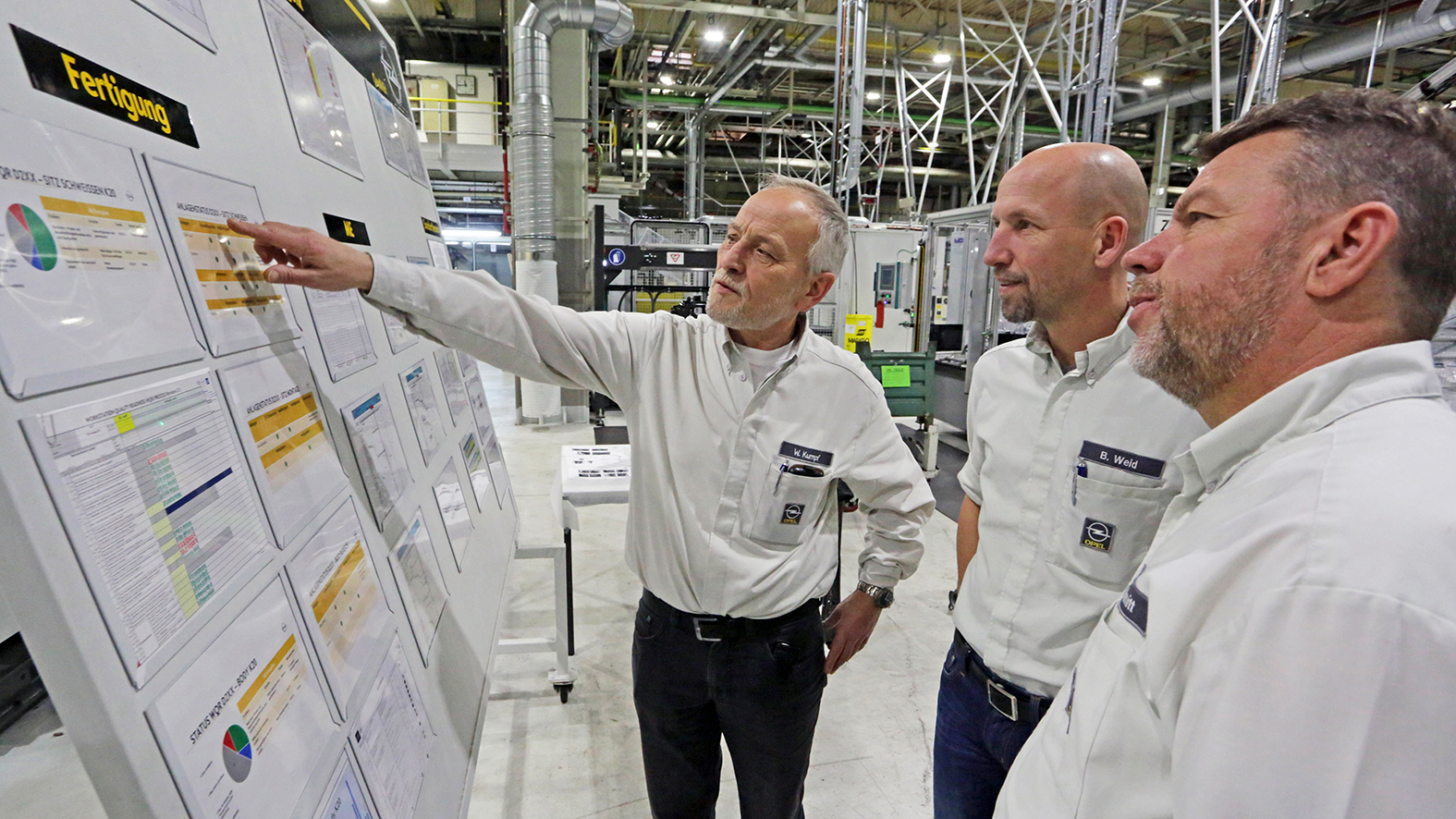
Lagebesprechung: Area Manager Chassis-Sitzkomponenten Michael Schmitt (rechts) mit Werner Kumpf (links), der für den Launch der Sitzfertigung zuständige Betriebsleiter, und Bernd Weid (Mitte), Betriebsleiter Schicht in diesem Bereich.
FEHLER SIND AUSGESCHLOSSEN
Auch diese 100-prozentige Endkontrolle der Sitze ist neu in Kaiserslautern. Dabei werden auch sämtliche Verfahrkräfte exakt gemessen, hinzu kommt der Leichtgängigkeits-Check der Entriegelungen. Schließlich sind es auch solche Details, durch die Kunden ein Produkt als qualitativ hochwertig empfinden.
Beim Bestücken der Transportgestelle für die Kunden in Gliwice und Ellesmere Port wird ebenfalls nichts dem Zufall überlassen. Eine grüne Lampe signalisiert dem Mitarbeiter, in welchen Behälter er die jeweilige Sitzvariante zu platzieren hat. Vergreift er sich, leuchtet sofort ein rotes Licht auf. Handwerklich umgesetzt haben dieses „Pick-to-Light“ das Team um Michael Klaffke, das für Kontinuierliche Verbesserungen (KVP) im Schweißbereich K20 verantwortlich zeichnet, sowie die Lehrlinge, die gegenwärtig in der Instandhaltung des K20 ausgebildet werden. Der stylische Würfel an der Hallendecke, der den Bereich optisch kennzeichnet, soll dafür sorgen, dass die neue Lauterer Sitzfertigung nicht nur technisch und organisatorisch, sondern auch optisch zukunftsweisend für den Produktionsort ist.
Die neue Sitze kommen übrigens zuerst in der neuen Astra-Generation zum Einsatz.
März 2015
über 40 Jahren
Hätten Sie’s gewusst? Die Sitzfertigung hat in Kaiserslautern eine längere Tradition als der Motorenbau. 2013 feierte die Opel-Pfalz den 40. Jahrestag ihres Produktionsstarts.
Über 38 Millionen Sitzkomponenten wurden seither in Lautern gebaut. Damit dies Mitarbeitern und Besuchern im Bewusstsein bleibt, hat Michael Schmitt, Area Manager Chassis und Sitzfertigung, ein kleines „Museum“ in seinem Bereich eingerichtet, in dem die verschiedenen Sitzgenerationen nebeneinander zu bestaunen sind.
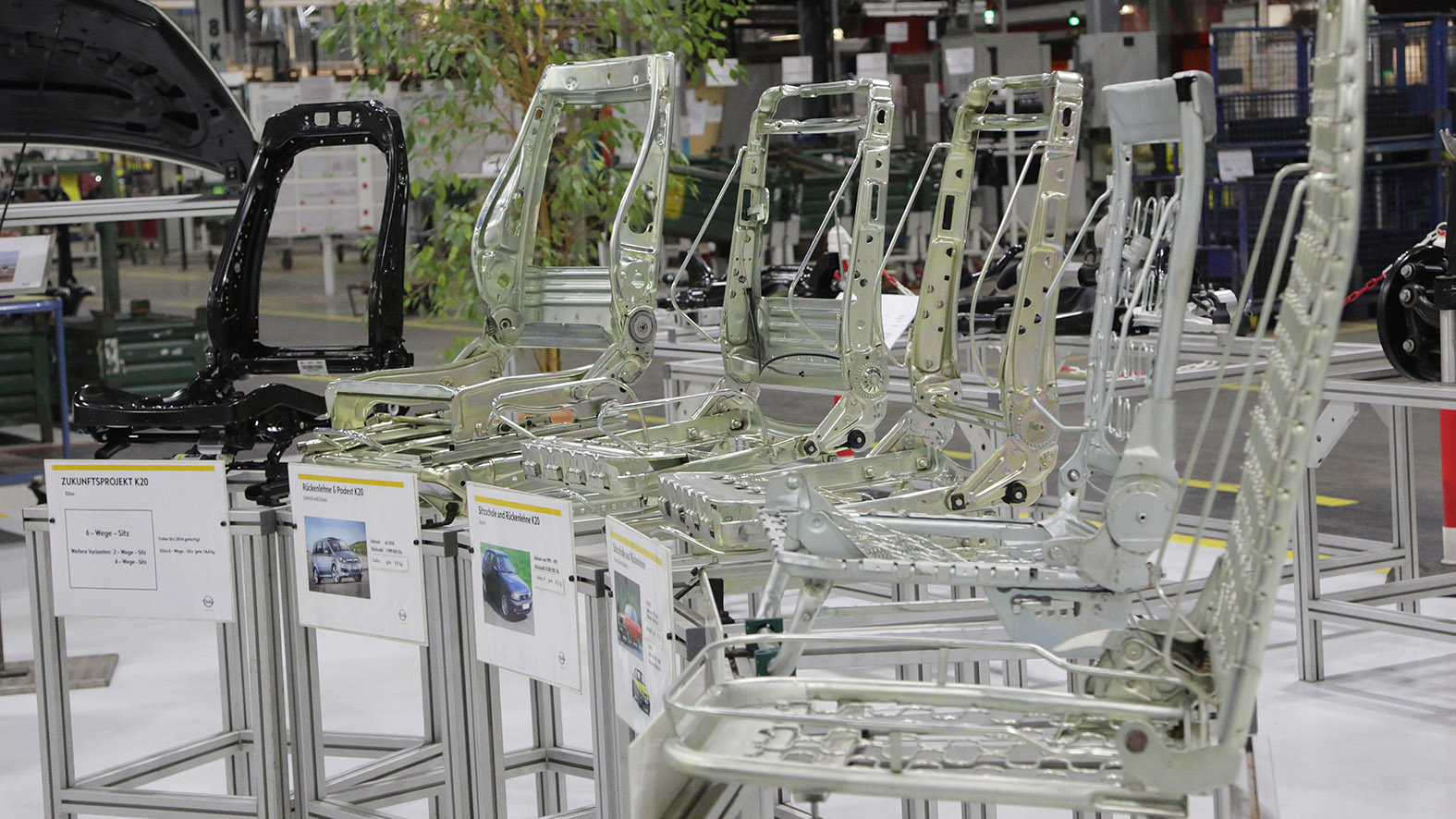
Eine kurze Geschichte des Sitzens: Eine kleine Ausstellung lässt über 40 Jahre Lauterer Sitzfertigung Revue passieren
Zum Einsatz kamen sie in Opel GT, Ascona, Manta, Kadett und Astra. „Vor allem dokumentiert die kleine Reihe, wie rasant sich die Opel-Sitze konstruktiv entwickelten“, sagt Michael Schmitt.
An den ersten Modellen wurden noch drei Millimeter dicke Bleche verwendet. „Heute“, so Schmitt, setzen wir auf hochfeste Stähle, die teilweise gerade mal 0,6 Millimeter dick sind.“ Um diese zu verarbeiten, braucht es ein Team mit viel Erfahrung – „und das haben wir im Werk Kaiserslautern, wie die Ausstellung eindrucksvoll dokumentiert.“