The first practical tests
have shown that
this electronic assistant significantly
boosts ergonomics.
From the very beginning, this new robot colleague sees the bigger picture, is happy to help his human coworkers, and impresses with his strength. He reaches toward the conveyor system, effortlessly lifts a roughly 40 kg door, and passes it on to the assembly line. There, he works at Sascha Hahn’s side, securely and patiently holding the door until Hahn has finished with fine-tuning and installation. The door is then secured to the chassis. Later on in the production process, this chassis will become a full-fledged Insignia.
“The two of us have done a very good job of mastering the door installation process,” says Hahn, praising his new colleague: Fanuc R-2000iB, a heavy-duty robot. “We developed specialized technology that lets our robot colleague speed up the assembly process. It makes assembly easier and, even more importantly, ensures that the process is completely safe for employees,” reports Hahn, who is a 30-year-old engineer and Production Planner and member of an Opel team that is laying the groundwork for human-robot collaboration in the Production division.
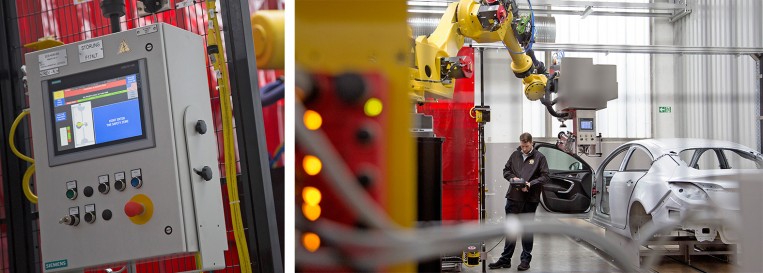
We censored our robot’s heart (its controls) in this image.
We need to respect his privacy!
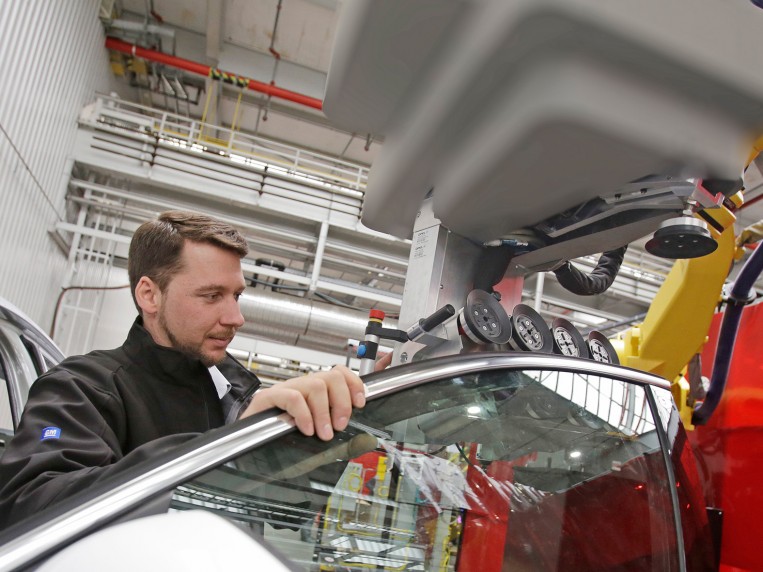
High-tech support: Sascha Hahn, a Production Planner from Rüsselsheim, Germany,
tests the innovative door mounting concept.
The new door mounting system project …
… has been underway since the end of 2012. Many employees are involved. Judith Apold and the main Production Planning team are working hard on the technological side of the project, along with robotics experts from the Fraunhofer Institute for Factory Operation and Automation in Magdeburg, Germany. The project team is addressing (occupational) safety concerns with the help of industrial trade associations as well as the Workplace Safety departments in Rüsselsheim and Eisenach, Germany. Apold and her colleagues are overseeing the technical implementation of the project concept together with the Production Planners at the Eisenach plant.
The first practical tests have shown that the new electronic assistant, whose activities are precisely defined and monitored by light barriers, significantly boosts ergonomics. Production employees are currently using handling equipment on a suspension rail system to transport doors from the storage area where they are suspended to the assembly station where they are mounted to the chassis. The extremely strong Fanuc robot spares employees the hard physical labor involved in accelerating and braking goods weighing up to 180 kg. An additional benefit: The robot curtails the door installation process by up to 20 seconds. “We are currently looking into how employees can make productive use of this shortened processing time,” says Apold.
Apold is the Opel Project Engineer for new production technologies, and is in charge of implementing the new door mounting concept. The new high-tech assistant should be in place to support employees on the assembly line in Eisenach for the first time by the end of the decade. Moreover, this assistance will not require the safety fences that were previously necessary for separating humans from robots in cases where the latter were lifting heavy loads or had a radius larger than one meter. “Until now, robots of that size were only used in automotive manufacturing in isolated cases, such as for paintwork,” says Apold. “Now, we want to break through that barrier.”
— 20 —
Seconds
Saved on the Door Mounting Process
This new project reduces processing times and boosts ergonomics. It also brings enormous advantages in terms of organizing production. “Firstly, using the robot means we do not need as much storage space at the assembly station for the technical handling equipment and the mechanisms we use to suspend the doors,” reports Apold. “Secondly, using the robot allows us to reduce the efforts required for making conversions along the assembly line.” This is crucial, since in some cases Opel produces several different types of models on a single assembly line.
↑ Making introductions at the pilot plant: GM Executive Vice President & President Europe Karl-Thomas Neumann listens to a detailed explanation of this new development.
← How does it work? The qualified electrical engineer wants a precise description.
“Realistically speaking, robots could also lend a hand with installing parts such as sunroofs and windows.”
– Harald Schenk –
Automation improves production processes, which in turn benefits employees as well as the company as a whole. Moreover, according to Harald Schenk, door installation is not the only process that could benefit from automation. “Realistically speaking,” says the Rüsselsheim-based Production Planner, who is also involved in the project, “robots could also lend a hand with installing parts such as sunroofs and windows.” Schenk reports that over 95 percent of the value-adding processes at the assembly stations in Opel plants are still implemented by hand. “This means there are still plenty of opportunities to use robots, particularly in the cases of assembly operations that involve heavy loads.”
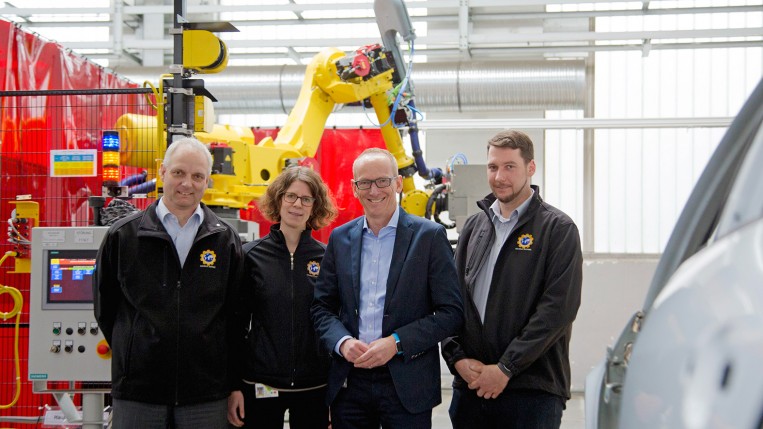
Group photo with the new employee in the background: Harald Schenk (from left), Judith Apold, Karl-Thomas Neumann, and Sascha Hahn.
Last update March 2016