- Monozukuri-Spezialist Ricardo Ralon-Contreras schaut drauf, dass die richtige KLT-Größe gewählt wird.
Monozukuri…
… bedeutet so viel wie „Sachen herstellen“ und wird auch oft mit „Handwerkskunst“ übersetzt.
… kommt aus der japanischen Automobilindustrie (Toyota).
In der Betriebswirtschaft beschreibt Monozukuri die Kunst sorgfältiger und schneller zu produzieren als die Konkurrenz, wobei die Fähigkeiten und Talente der Menschen im Mittelpunkt jeglichen Tuns stehen.
„Monozukuri bezieht sich auf die ‚total landed costs‘, also alles, was sich auf die Kosten unsere Produkte auswirkt, inklusive Material- und Transportkosten“, erklärt Ricardo Ralon-Contreras, seit Mitte 2018 Monozukuri-Koordinator bei Opel Wien. Nach rund einem Jahr seit der Einführung von Monozukuri ist die Ausbeute dieser ganzheitlichen Betrachtungsweise beeindruckend.
Der Monozukuri-Experte holt aus: „Zuerst haben wir intern Maßnahmen gesetzt. Wir starteten mit Themen, die uns vom Engineering her bekannt waren. Zusammen mit Manufacturing Engineering durchforsteten wir die Typenvielfalt der drei in Wien-Aspern gefertigten Produkte. Und hinterfragten, welche Typen sinnvollerweise weiterhin produziert werden sollten. Motto: Weniger ist mehr. Denn je weniger Typen gefertigt werden, desto weniger Einzelteile sind nötig. Die Lagerhaltung reduziert sich und Abläufe werden einfacher. In Summe hilft eine Reduktion der Typenvielfalt Kosten sparen.“
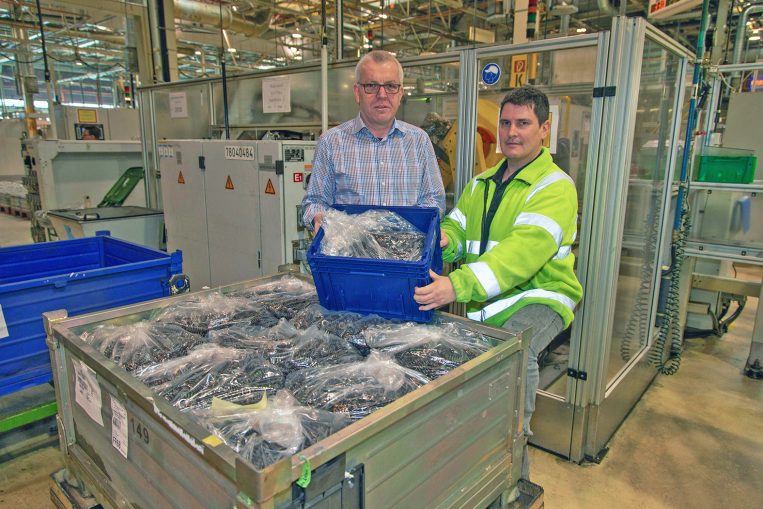
Änderungen bei der Verpackung helfen Kosten sparen (Johann Engelmann (l.), Gerald Poppinger, beide Verpackungsabteilung).
Anders verpackt
ist’s günstiger
Die nächsten Maßnahmen galten Fragen der Verpackung. Auch noch mit einem internen Analyse-Prozess. „Wir – Manufacturing Engineering, Quality Management und die Logistik – haben uns in Workshops überlegt, wie Verpackung günstiger gestaltet werden könnte. Dazu sind wir durch die Linien gegangen und haben Möglichkeiten aufgespürt, um die Verpackungsdichte zu erhöhen.“
Die Lösungen waren meist verblüffend einfach: Einmal ging es darum KLT/Kleinlastenträger (so heißen die Kunststoffboxen, in denen Schrauben, Federn und andere kleine Teile transportiert werden) richtig – statt nur halbvoll – anzufüllen. Ein anderes Mal machte der Verzicht auf KLT Sinn: wenn zum Beispiel Teile sowieso in einen Bunker geschüttet werden. Da erwies es sich als günstiger die Teile in Plastiksäcken in Containern heranzuschaffen.
Oder die „Verpackungsgröße“ wurde geändert: indem statt eines kleinen – 30 mal 20 mal 15 Zentimeter großen – KLT ein doppelt so großer KLT gewählt wurde.
„Was wir dabei zu beachten hatten“, erklärt Ralon-Contreras, „waren das Gewicht – ein KLT darf nicht schwerer sein als 15 Kilogramm -, dann die Frage, ob das angelieferte Material in der veränderten Verpackung in der Montage angestellt werden kann, und schließlich das Thema Ergonomie.“ Ersparnisse können sich dadurch bei den Mietkosten für KLT, bei den Beschaffungskosten für Verpackung und bei den Transportkosten ergeben. Im Werk selber werden Material Handling-Abläufe vereinfacht und Lagerflächen reduziert.
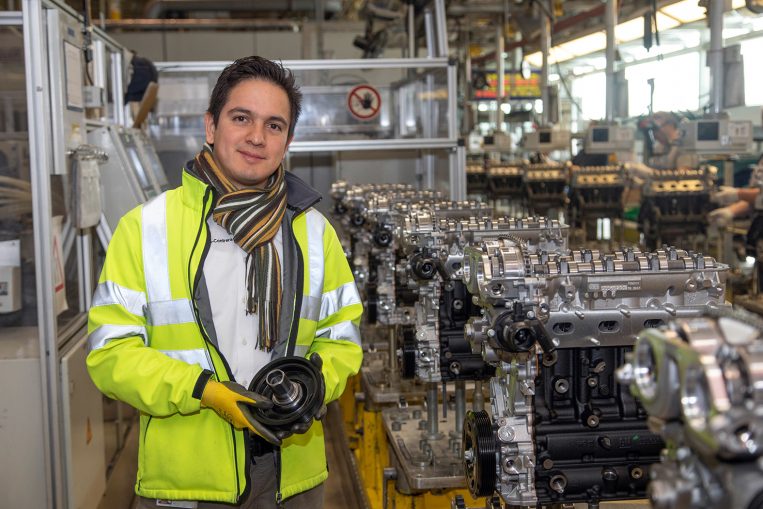
Monozukuri-Überlegungen zahlen sich aus, wie das Beispiel Torsionsschwingungsdämpfer zeigt.
Kooperation
mit den Lieferanten
Die dritte Etappe der Monozukuri-Maßnahmen brachte die Kür: Jetzt ging es darum gemeinsam mit Lieferanten Verbesserungen herbeizuführen. Wieder mit Workshops. Und so weit als möglich vor Ort in den Werken der Lieferanten.
Ricardo Ralon-Contreras erzählt: „Wir haben uns auf Lieferanten mit mittlerem bis größerem kostenmäßigem Lieferumfang konzentriert.“ Ein Projekt zum Beispiel galt der Firma Vibracoustic, von deren Werk in Trebechovice pod Drebem in Tschechien Torsionsschwingungsdämpfer (Torsional Vibration Damper) für Motoren nicht nur nach Wien-Aspern, sondern auch in das Motorenwerk in Tichy in Polen und die PSA-Motorenwerke in Tremery und Douvrin geliefert werden.
„Dazu sind wir in das tschechische Werk gefahren“, sagt der Monozukuri-Spezialist. „Wir“ war in diesem Fall Kurt Henecker/Koordinator Motormontage, Alice Tran/Einkäuferin PSA, Markus Kilian/Manufacturing Engineering, Dominique Jobard/ Monozukuri-Koordinator Tremery/Metz. Danach folgten zahlreiche Telefonkonferenzen.
Das sich für den Torsionsschwingungsdämpfer ergebende Verbesserungsprogramm umfasst: Materialänderungen und Änderungen der Beschichtung am Teil sowie Maßnahmen zur Taktzeitoptimierung beim tschechischen Lieferanten. „Vor allem für den EB-Motor, der aktuell in Tremery, Douvrin und in Tichy – und ab 2020 in Szentgotthard – produziert wird, haben sich dadurch beträchtliche Einsparungen ergeben. Die Maßnahmen werden zurzeit validiert. Ab Herbst startet die Umstellung“, berichtet Ricardo Ralon-Contreras.
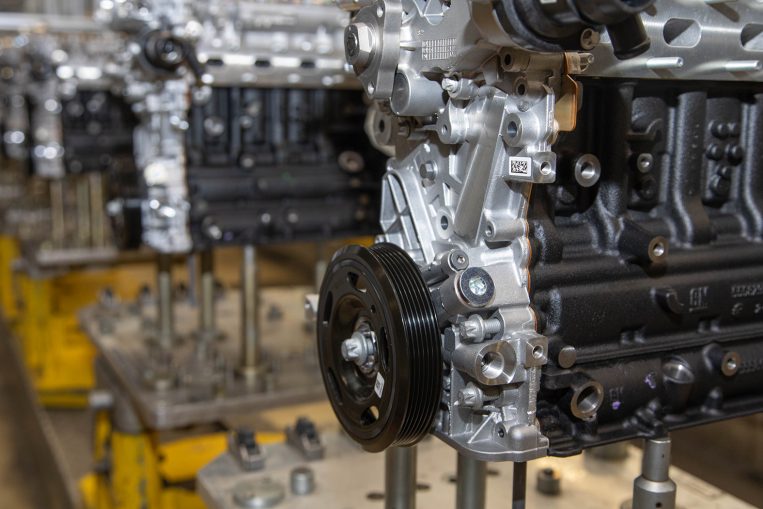
Torsionsschwingungsdämpfer
Gegen
Transportkosten
Ein weiterer Monozukuri-Workshop galt den Zahnrädern von O-Oka in Takaoka/Japan. Dazu kamen Vertreter des Unternehmens von ihrem Standort in Frankfurt am Main nach Wien. „Hier ging es vor allem um Transportfragen. Wir haben uns mit der Auslastung der Container befasst und schließlich etwa 30 Container pro Jahr eingespart.“ Die Zahnräder von O-Oka werden aus Japan nach Wien überwiegend per Schiff transportiert.
Aus Györ – von der Firma NEMAK – werden Zylinderköpfe an Opel Wien geliefert. „In diesem Fall haben wir uns bemüht, das Gewicht der Teile zu reduzieren“, nennt Ricardo Ralon-Contreras ein weiteres Beispiel. „Das ist für unsere Familie 0-Motoren wichtig, aber auch für die kleinen Benzinmotoren und die Dieselmotoren, die in Szentgotthard produziert werden.“
Im Jahr 2018 wurden insgesamt 92 Monozukuri-Aktivitäten bei Opel Wien gestartet und bereits auch großteils umgesetzt.