The first engineers to take an interest in airflow were – of course – aircraft makers. But aerodynamics have been part of automobile development for longer than most people think. Back in 1914, a Count named Marco Ricotti had an Alfa Romeo made that was based on an airship back– the 40-60 hp “Aerodinamica”. He had realised that cars are faster and use less fuel when they generate as little wind resistance as possible.
It simply made sense to use the knowledge of aviation pioneers – and this soon became the rule in the industry. After World War I, many brilliant aircraft designers moved into the car business, bringing their knowledge with them. The “coefficient of drag” – Cd – became increasingly important in the development of automobiles. However, for many years most people hardly took any notice – only those interested in motor racing or particularly sporty cars. Then Opel hit the headlines around 30 years ago with the Calibra. At that time, the drag coefficient of 0.26 was so sensational that the media crowned the Calibra as the “World Champion of Aerodynamics.”
Speed is no longer everything – the focus today is on CO2 emissions
Development progressed quickly. Every Opel that followed achieved similarly high results in the wind tunnel. With Cd values of 0.26 and 0.25 respectively, the Astra and the Insignia are among the best in their class. With these cars it was no longer just about gaining more top speed through a streamlined shape. More importantly, their optimised aerodynamics should help to reduce fuel consumption. Increased efficiency and meeting CO2 targets have long been the focus of our work.
Shapes can be further improved, but not fundamentally changed
In the car business, we aerodynamicists have to live with the shape of the object we are given. Small cars or big sedans, hatchbacks, notchbacks, coupés or SUVs – all body styles are defined by certain characteristics that customers want. In terms of aerodynamics, we can only optimise these shapes but never fundamentally change them. That is why much of our work consists of a continuous quest for optimisation; and that is only possible by working in close cooperation with our colleagues from Design and Engineering.
In comparison to a classic sedan, a crossover like the Mokka is taller. It also has bigger wheels with correspondingly bigger wheelarches that are emphasised with additional trim. The shorter overhangs are also features that make it more difficult to achieve a low Cd value. Nevertheless, during the development of the new Mokka we set ourselves the target of reducing the drag factor to 0.32 from the previous model’s 0.35 Cd.
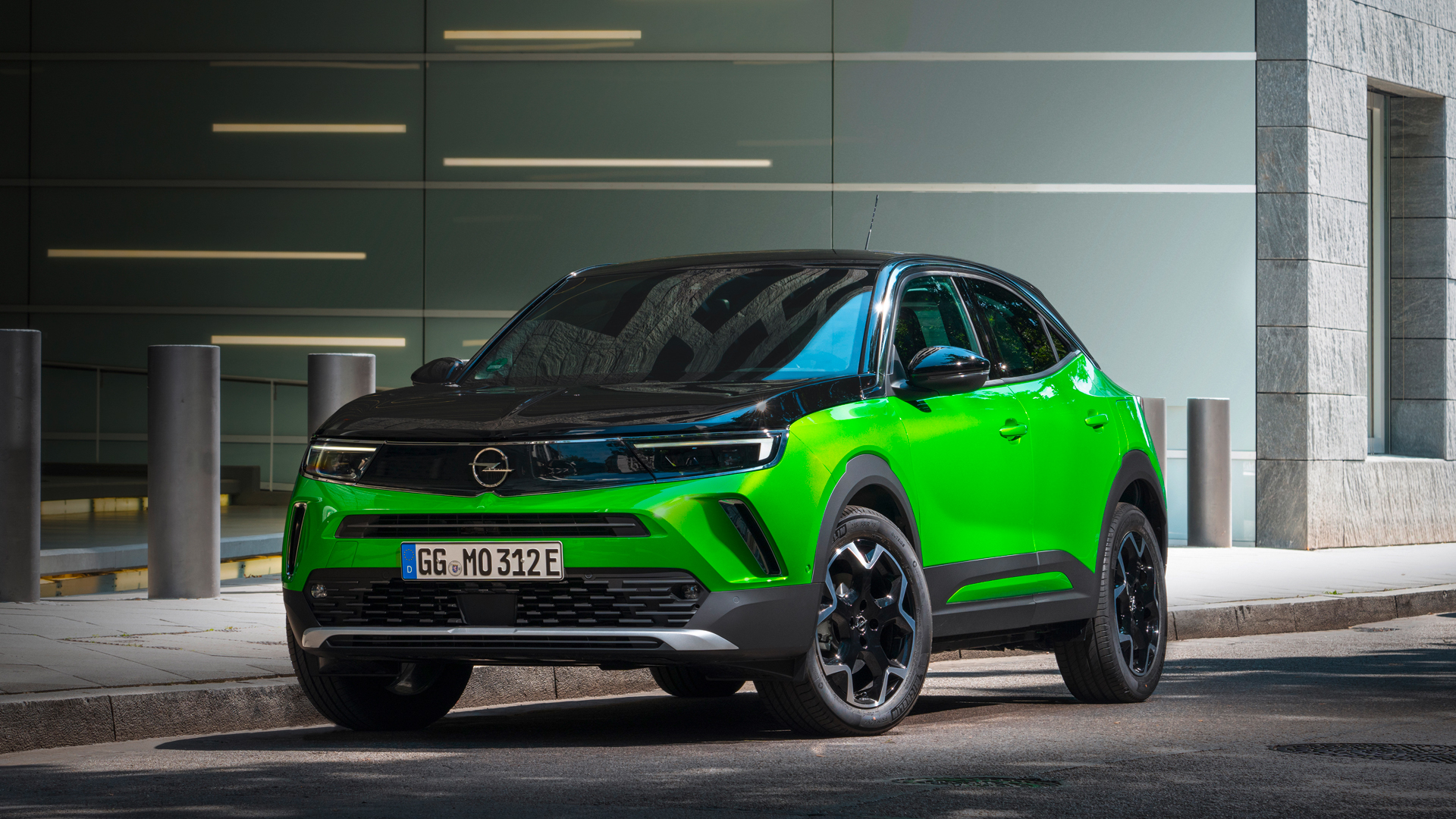
„In terms of aerodynamics, we can only optimise these shapes but never fundamentally change them.“
Smooth surfaces are important – also on the underbody
So we had to concentrate on the details while at the same time continuously asking ourselves, how can we retain the Mokka’s shape and achieve our aerodynamic targets. Most important of all is to create smooth surfaces, especially on the underbody. We developed our first ideas with the help of “Computational Fluid Dynamics” (CFD). That gave us very precise data with which we could then make models for testing in the wind tunnel. We use the FKFS wind tunnel in Stuttgart.
We make the models ourselves in our workshop in Rüsselsheim. The basic structure is made of steel and aluminium, as it has to carry the engine. For the exterior shape, we use clay, which is easy to mill and modify by hand. That enables our modellers to make further optimisations between tests in the wind tunnel. We make various versions of the exterior mirrors or underbody panels, so that we can identify the most aerodynamically efficient.
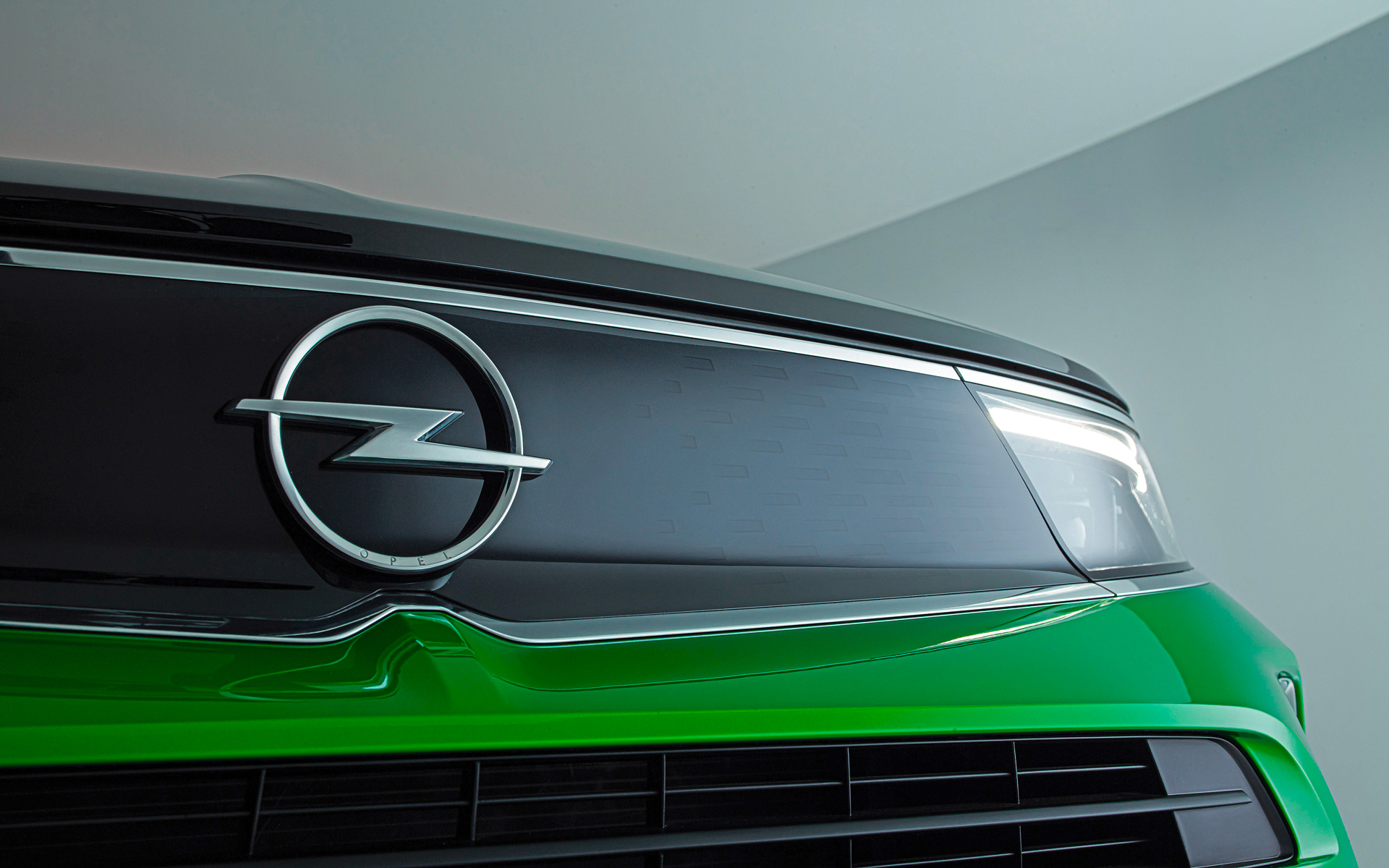
Aerodynamically easy to integrate: “Opel Vizor”
A wind tunnel session often lasts several days, while an individual test takes only two or three minutes – that alone shows how many variants we test and how intensively we optimise, especially during the initial development phase. In the end, we have identified the slightest adjustments with which we can lower the drag, and report our findings back to Design and Engineering.
It was relatively easy to integrate the “Opel Vizor”, the new face of our brand. It covers the front of the car like an integral helmet, combining grille, headlamps and the Blitz into a single element. We already knew the “Vizor” from the GT Experimental design study. For the Mokka we mainly had to shape the transition from the “Vizor” to the engine bonnet, so that no airflow separation occurred. The same goes for the transitions to the sides, such as from the headlamps to the fenders.
The “Aero-Shutter” – the jalousie that controls airflow
We adopted the concept of the active aero shutter from other models. The shutter is open when the car is driving up a hill or in hot cities. It automatically closes the frontal opening when cooling air is least needed, for example at urban-road speeds. When closed, the shutter system enhances aero performance by redirecting airflow around the front of the vehicle and down the sides, rather than through the less aeroynamically efficient engine compartment.
The Mokka is the very first Opel to feature “air curtains” on either side of the cooling intakes. They are an important styling element of the car’s front end, making the car look wider and emphasising its sporty character. We used the designers’ idea to integrate intakes that guide the air through ducts into the wheelarches and then out again across the surface of the front wheels. These “air curtains” reduce the amount of turbulence in the area of the wheels and combine an eye-catching design element with optimum aerodynamics.
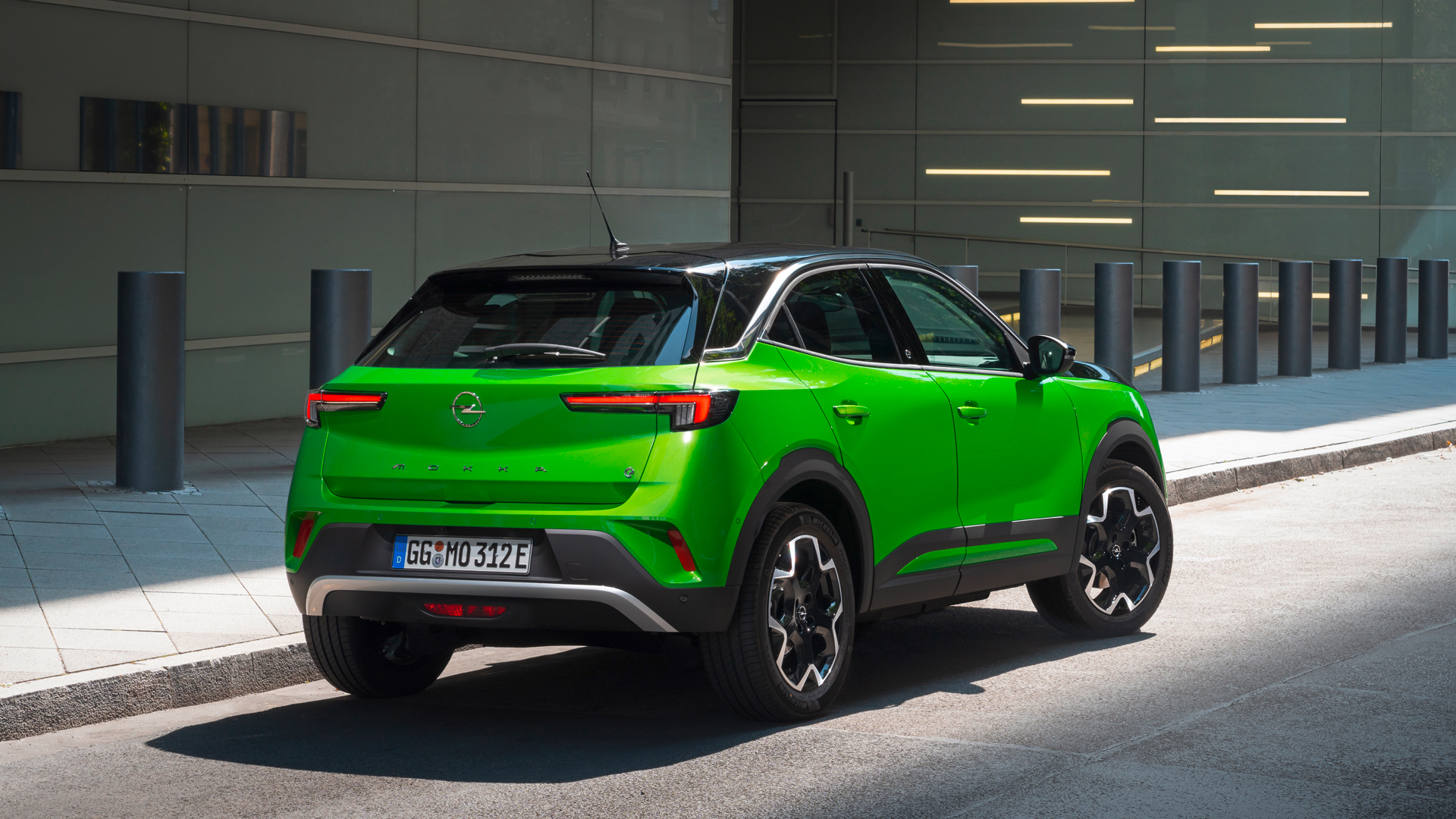
… ultimately, it all comes down to emotions – as always
At the rear of the car, we worked very hard on the roof spoiler and the fins on either side of the rear window. These components helped us to achieve good airflow separation and prevented the turbulence that causes drag and lift.
The results speak for themselves. The frontal area of the new Mokka covers only 2.27 square metres and gives the new model a dynamic appearance – emotional as well as efficient. The Mokka not only looks fantastic, we also achieved our goal in terms of aerodynamics as well, with a drag coefficient of 0.32. That means 16 per cent less drag on the autobahn and around nine grams lower CO2 emissions per kilometre than the previous model.
As Engineering Group Manager Aerodynamics, I would like to thank the entire aerodynamics team and especially my predecessor, Rainer Weidemann, who made a big contribution to the project.
March 2021