Die Anlage ist mächtig: Der Ofen 36 Meter lang, der dazugehörige Pressentisch 80 Tonnen schwer. Stahlplatinen rollen bei 930 Grad durch den Heizofen, um anschließend während des Verpressens schlagartig abgekühlt zu werden. „Beim Warmumformen wandelt sich die Gefügestruktur des Metalls, komplexe Formen sind möglich“, erklärt Thomas Stasiewicz über das Zischen und Stampfen der Anlage hinweg. Der Betriebsleiter des Presswerks streift Handschuhe über, greift ein fertig geformtes Teil. Knapp zwei Meter lang, gebogen, hochfest: „Das“, sagt er, „ist eine Dachstrebe, eine Verstärkung für die A-Säule des neuen Grandland.“
Die Strebe ist eines von mehr als 100 Pressteilen, die im Werk Kaiserslautern für das neue Top-SUV von Opel gefertigt werden. Vom fingergroßen Getriebehalter bis hin zum komplexen, aus fünf Einzelteilen zusammengeschweißten Tunnel: In der Karosserie des neuen Grandland steckt jede Menge Know-how aus der Pfalz. Ob Längsträger, Radkasten, Achsteile oder Türaufprallträger – in Summe werden im Schnitt über 18.000 Bauteile pro Woche aus der Pfalz nach Eisenach geliefert. Dorthin, wo der neue Grandland auf Basis der STLA Medium-Plattform gefertigt wird.
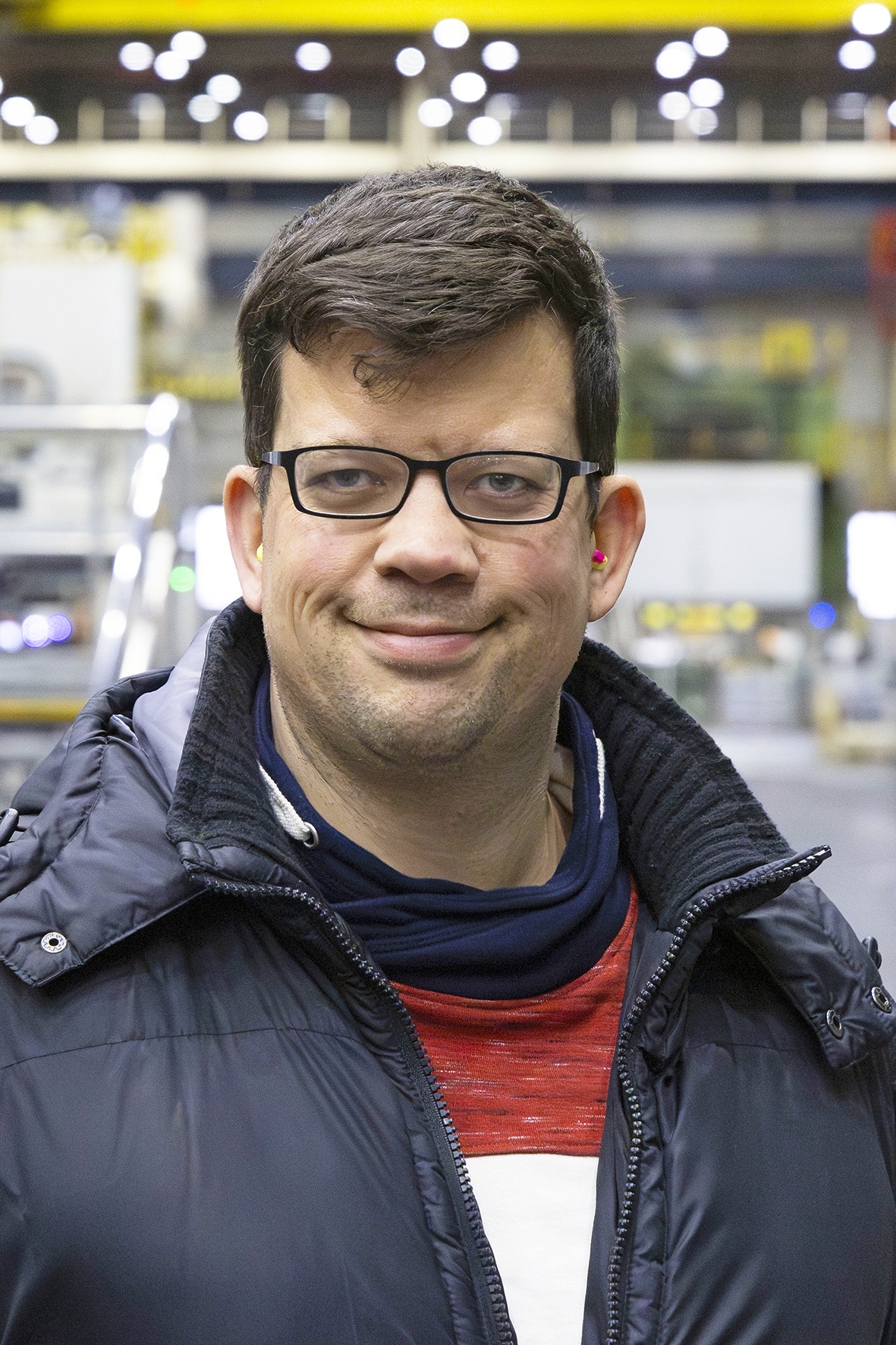
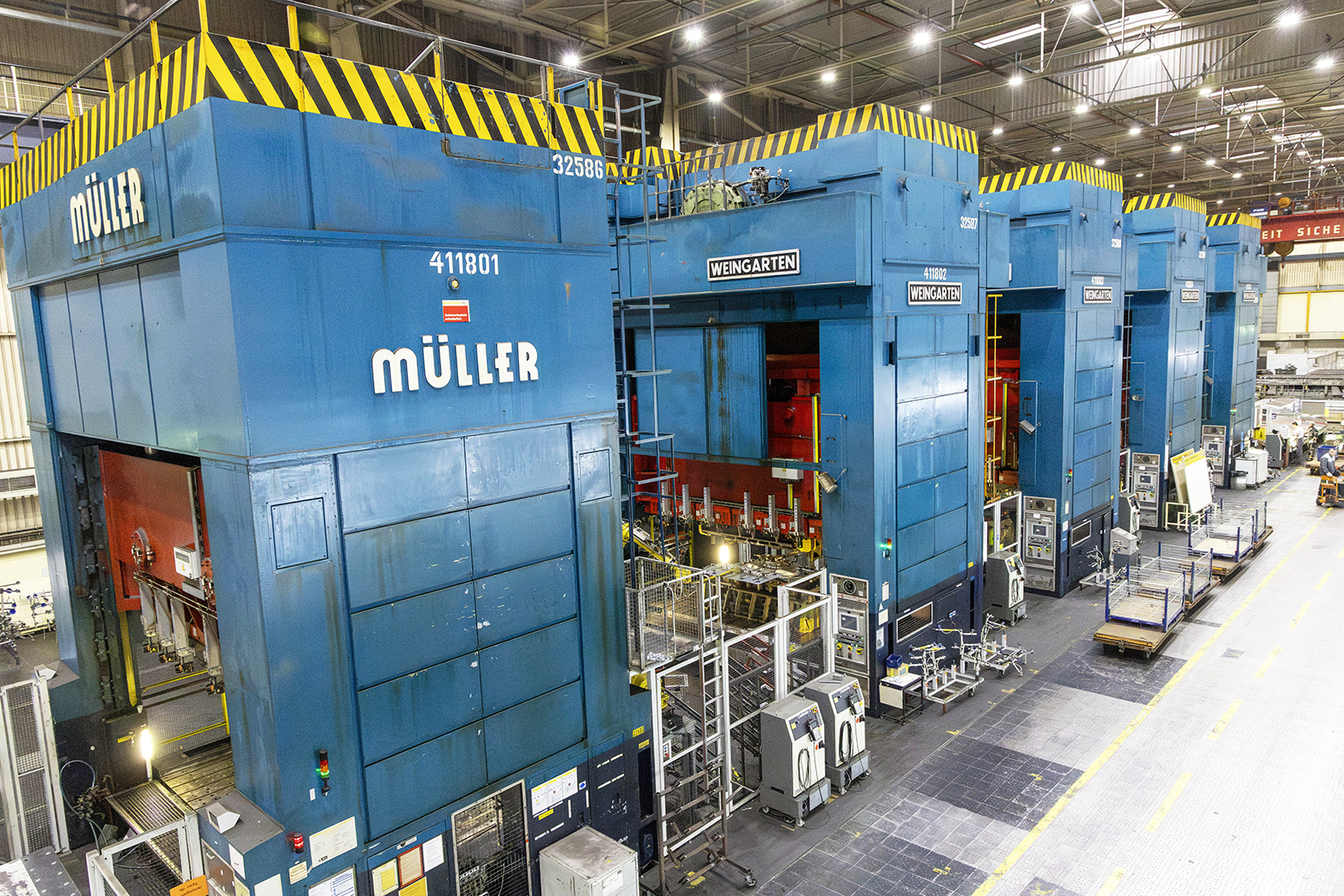
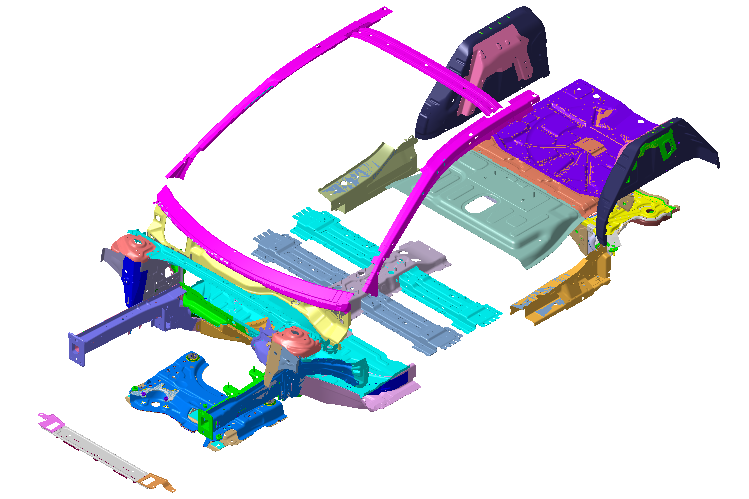
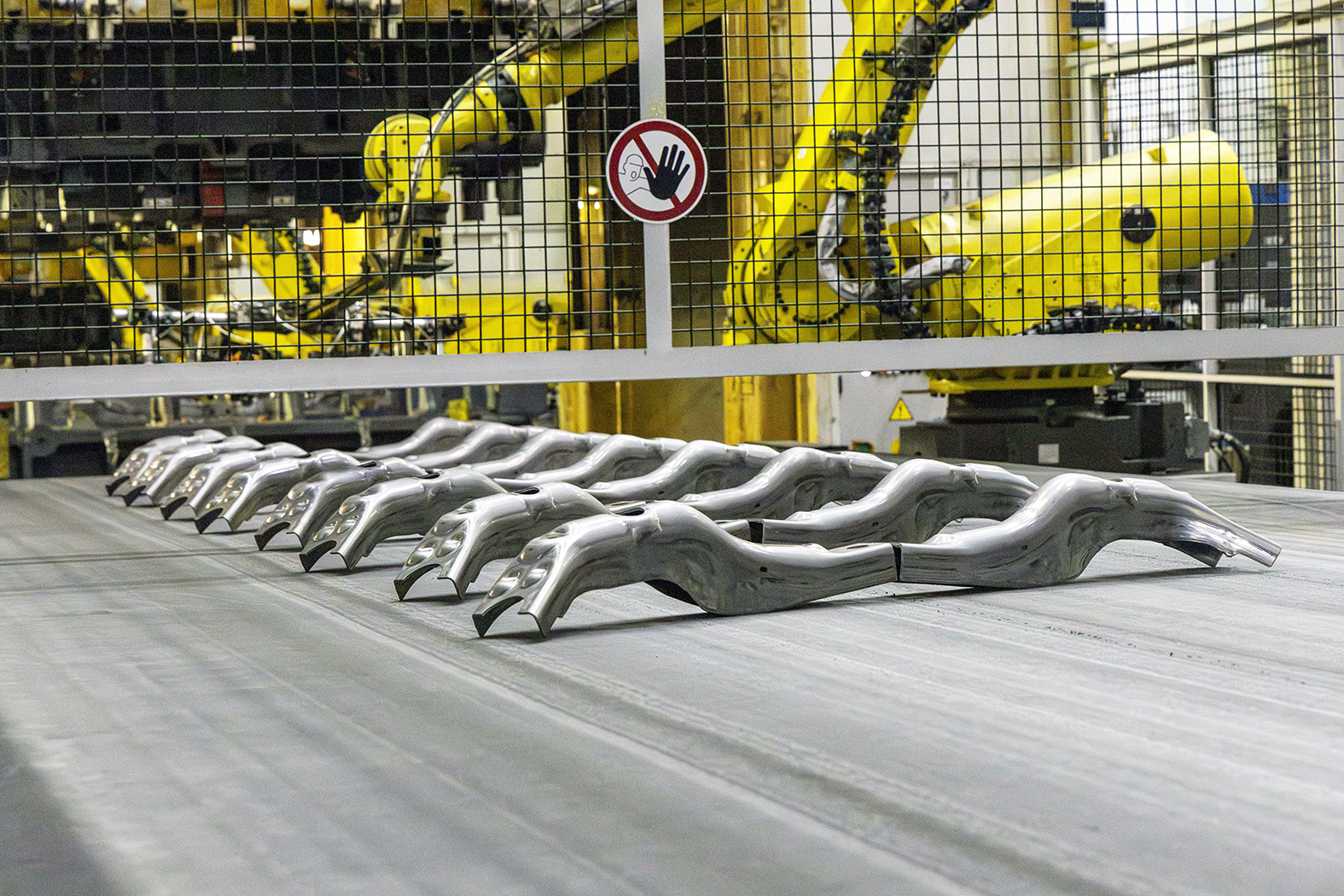
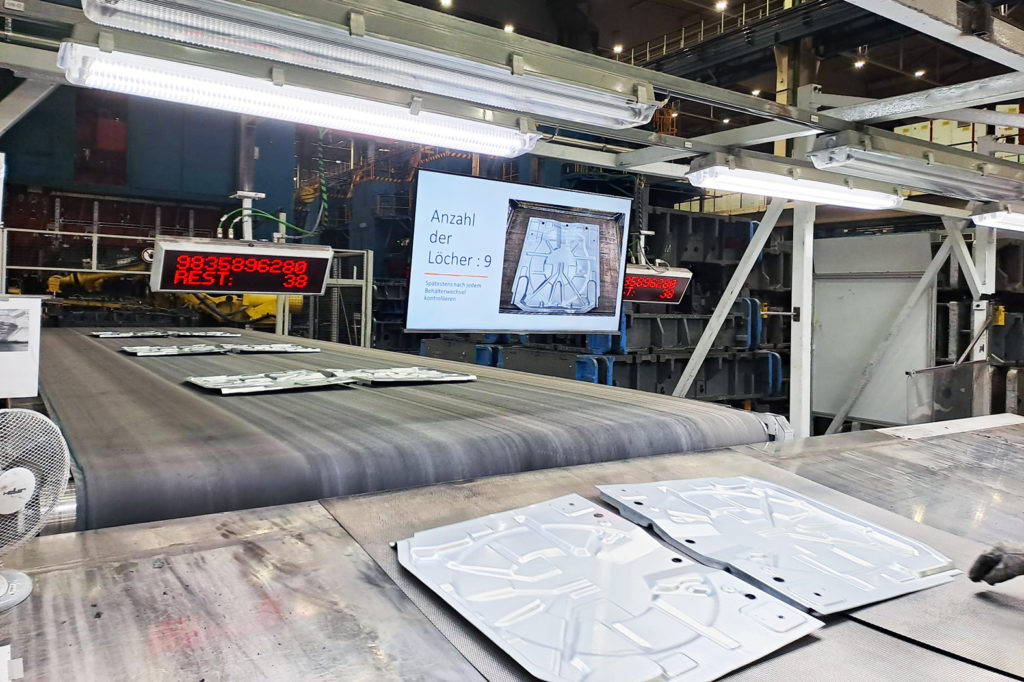
Besonders crashrelevante Bauteile – wie die Dachstrebe – kommen aus der Warmumformanlage. Sie ist vor vier Jahren in Kaiserslautern eingezogen. „Hohe Festigkeit kombiniert mit vergleichsweiser dünnwandiger Konstruktion bedeuten: ein Plus an Sicherheit und wenig Gewicht“, erläutert Stasiewicz. Der 35-Jährige ist das, was man ein „Eigengewächs“ nennt. Vor 20 Jahren kam er zu Opel in die Pfalz, um sich zum Zerspanungsmechaniker ausbilden zu lassen. Heute verantwortet er den Betrieb des Presswerks. Rund 260 Mitarbeitende gehören zu seinem Team. Demnächst wechselt er ins Presswerk nach Rüsselsheim.
Pressen für jede Gelegenheit
Unter seiner Verantwortung nehmen die Bauteile für den Opel Grandland im K19 Form an. Ein Großteil wird klassisch kaltgepresst, also bei Raumtemperatur mit gewaltigen Zug- und Druckkräften. Der Maschinenpark ist divers: Es gibt Kleinpressen für Kleinteile, andere Pressen sind im Verbund hintereinander zusammengeschlossen. Roboterarme heben die Arbeitsstücke von einem Umformschritt zum nächsten. Die langen Pressenstraßen sind die Giganten unter den Umformanlagen: An einem Ende wandert die Stahlplatine hinein und kommt fünf hintereinander ausgeführte Presshübe später als fertiges Bauteil heraus. In diesem Fall: als Kofferraumboden für den Grandland.
Ob Pressteile oder Zusammenbauten – Kaiserslautern beliefert aktuell mehr als 20 Stellantis-Werke in Europa.
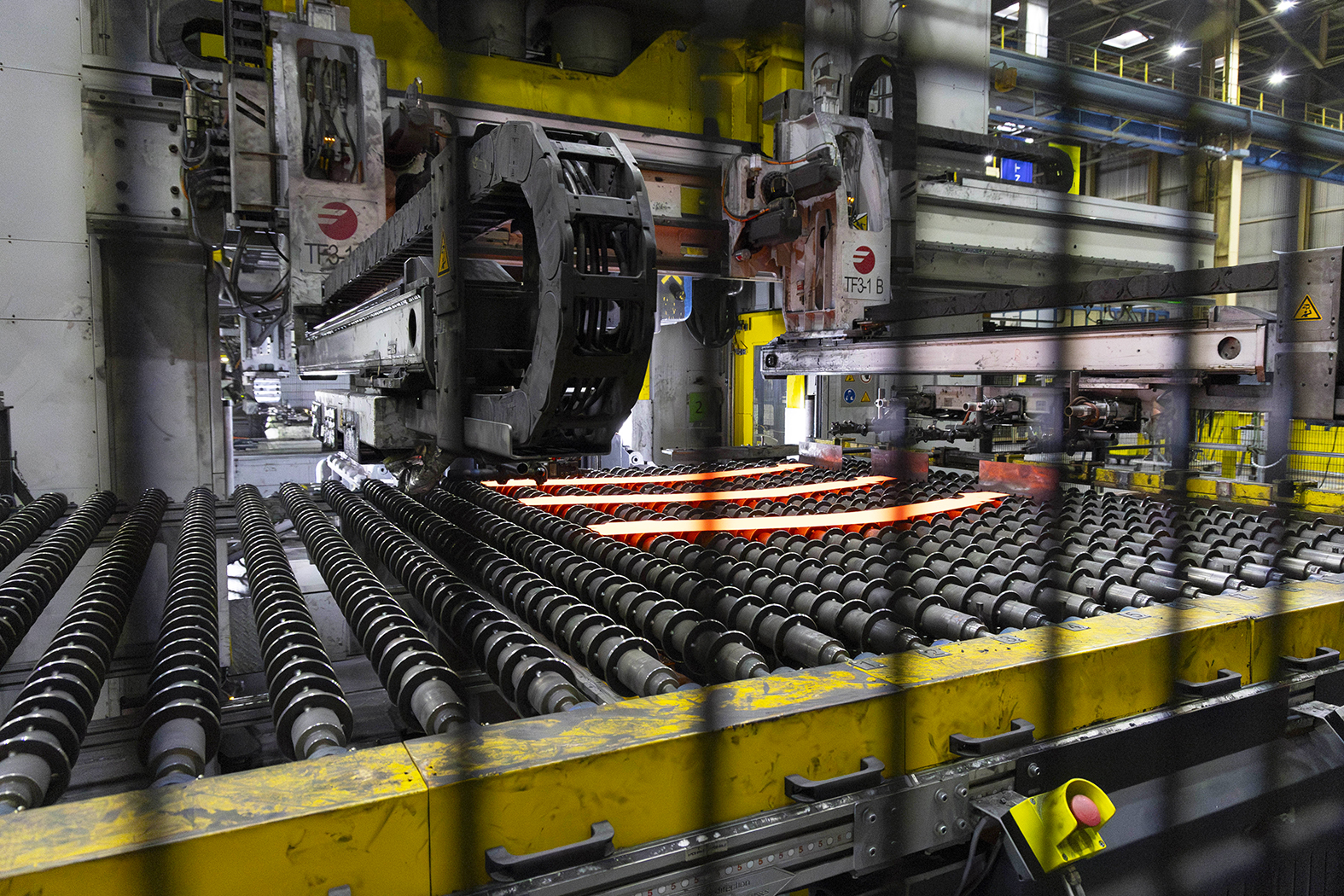
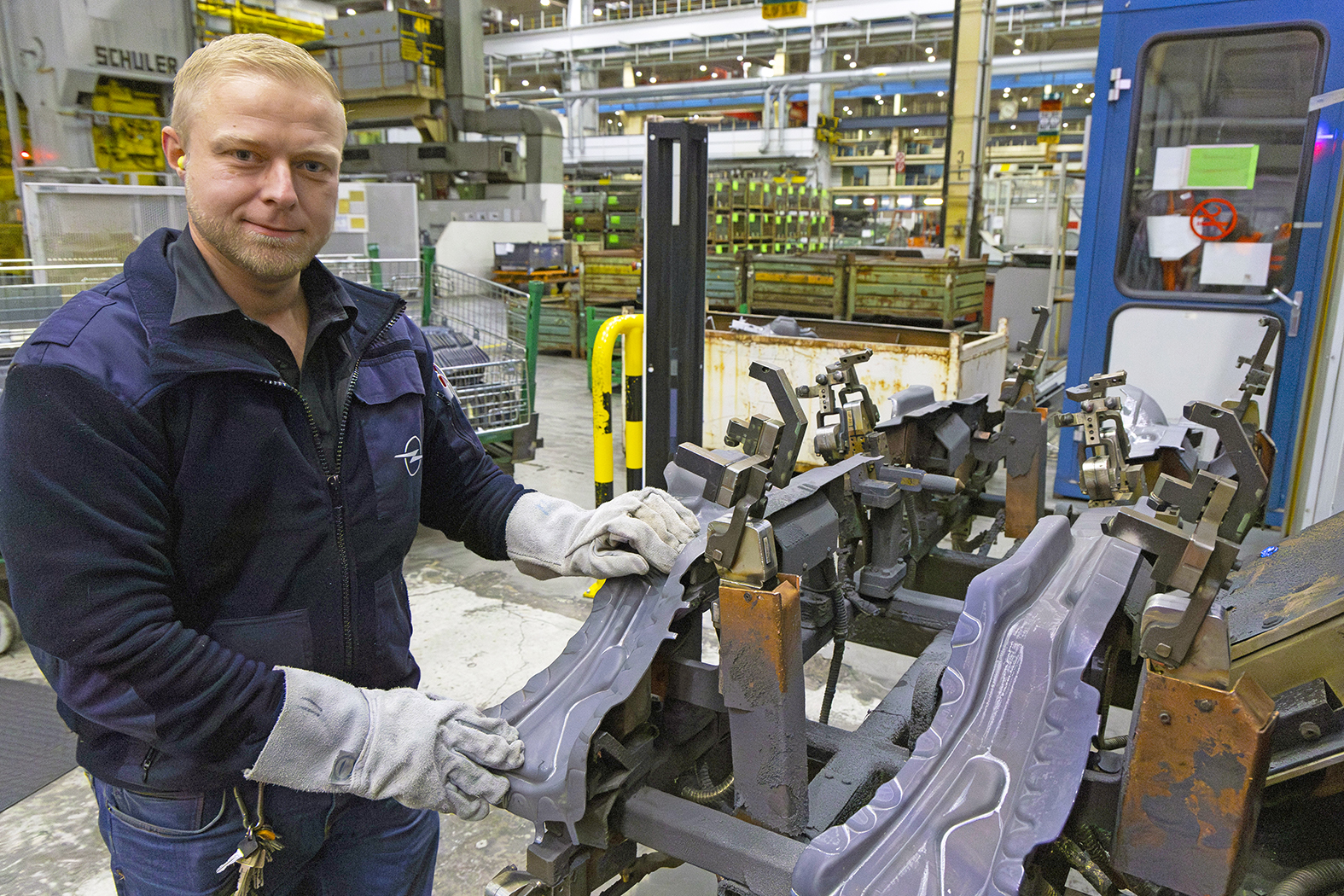
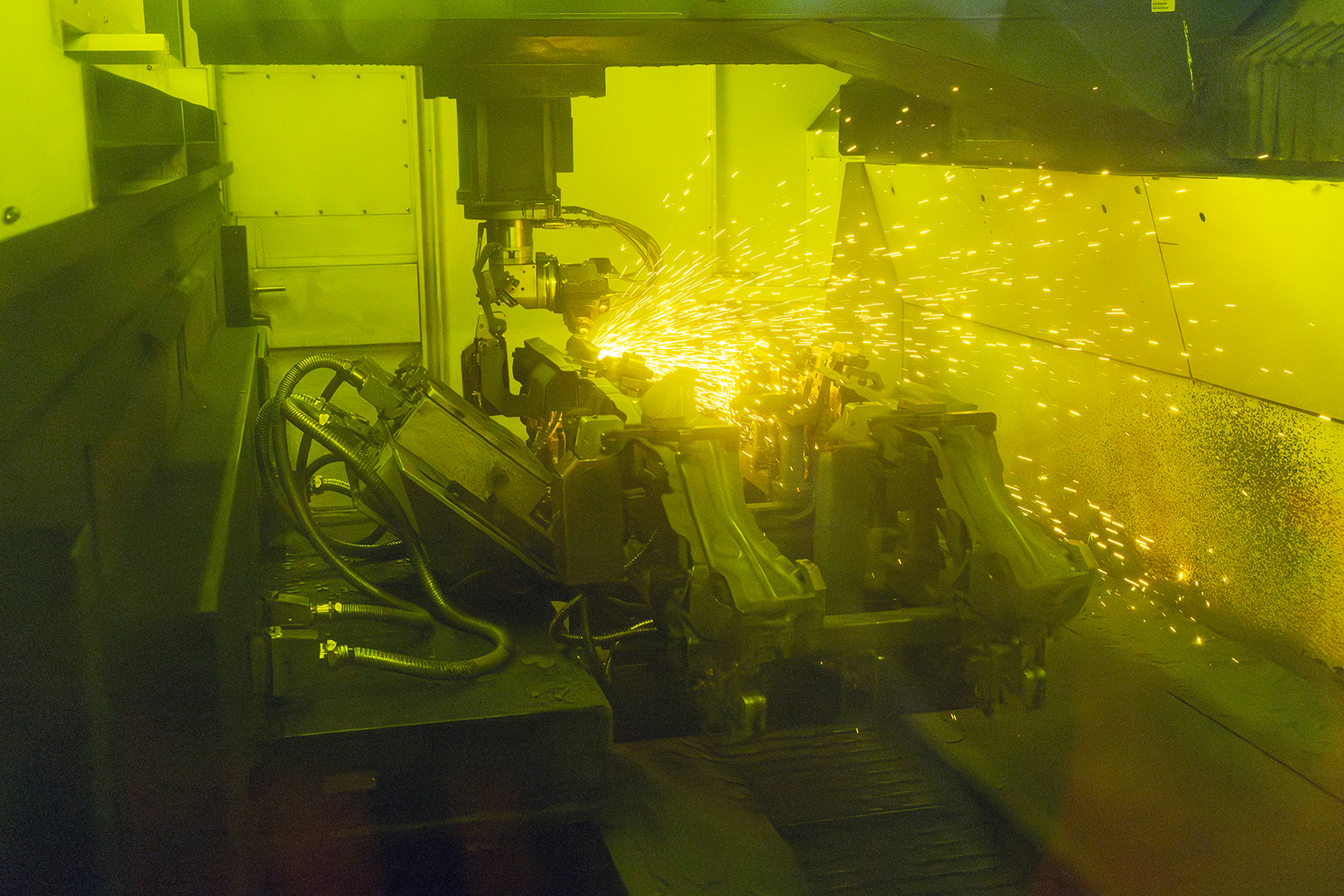
Die beiden Krananlagen an der Stirnseite der Halle liefern unablässig Nachschub: Bis zu 23 Tonnen schwere Stahlcoils. Maschinen wie die Large Progressive Press werden direkt mit den aufgewickelten Metallbändern bestückt. „Abrollen, schneiden, pressen – das läuft von A bis Z automatisiert“, sagt Stasiewicz. Es schwingt Faszination mit. Auch nach 20 Jahren noch. Egal wohin man im K19 blickt, es herrscht Hochbetrieb. Aus der Großtransferpresse rollen Verstärkungsstreben. „Ein Highrunner“, kommentiert der Betriebsleiter. Heißt: „Die Strebe wird in hoher Stückzahl produziert und nicht nur im Grandland verbaut, sondern in vielen weiteren Modellen.“
„Made in Lautern“ europaweit
„Die Auslastung ist zurzeit sehr gut“, bestätigt Robert Leitner, unter anderem zuständig für die Planung der Volumina im Werk. Die vollen Auftragsbücher werden aktuell nicht nur im Presswerk im Dreischichtbetrieb abgearbeitet. Ob Pressteile oder Zusammenbauten – „Lautern“ beliefert mehr als 20 Stellantis-Werke in Europa. Nicht nur der neue Opel Grandland ist Abnehmer, in mehr als 30 Stellantis-Modellen stecken Bauteile aus Kaiserslautern. Rund 500 Teilenummern sind im System hinterlegt. Sprich: 500 unterschiedliche Bauteile gehören zum Lauterer Portfolio.
„Neue Technologien und Methoden sind Pflicht. Sie machen uns wandlungsfähig – und effizient.“
– Robert Leitner –
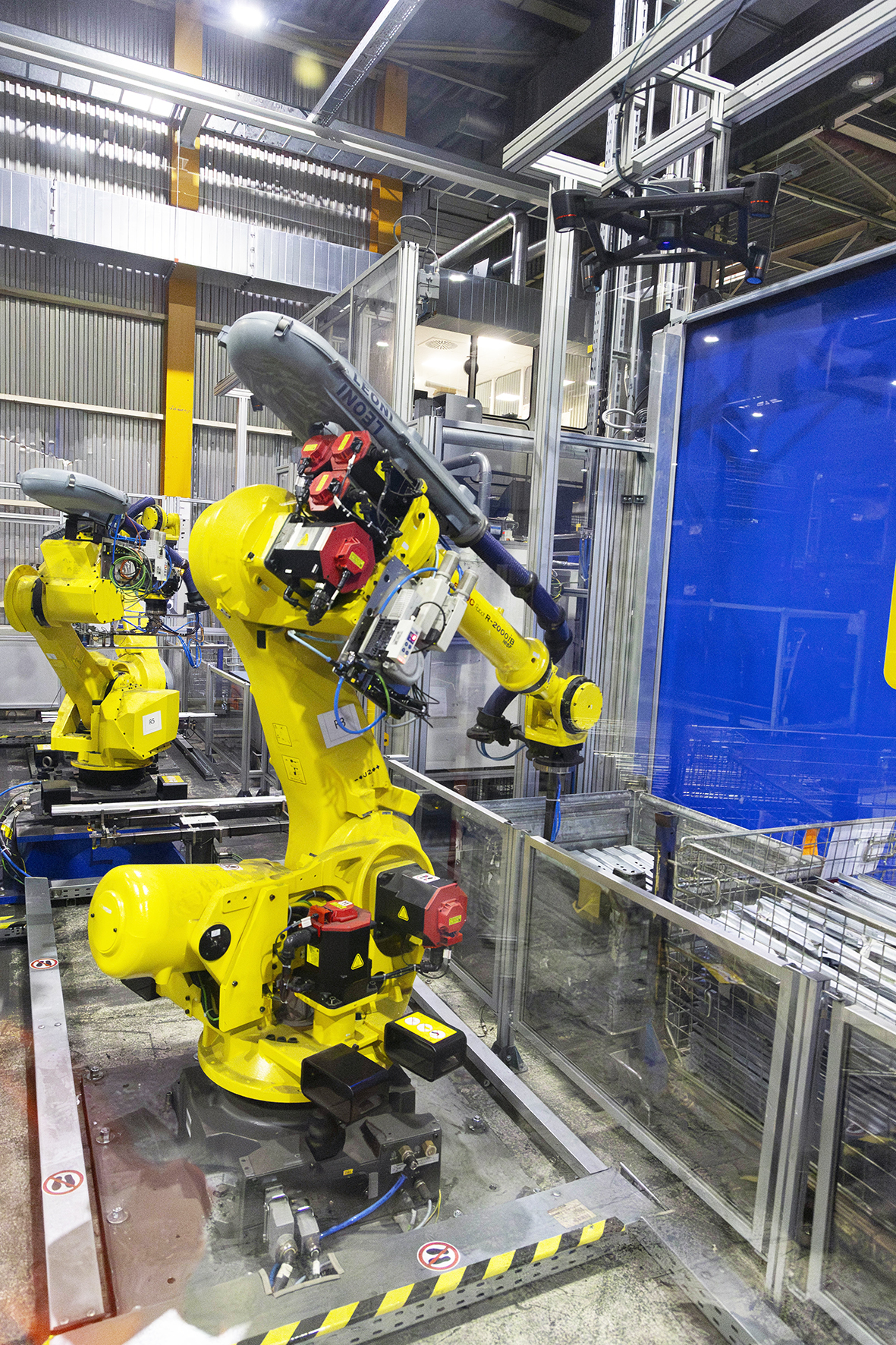
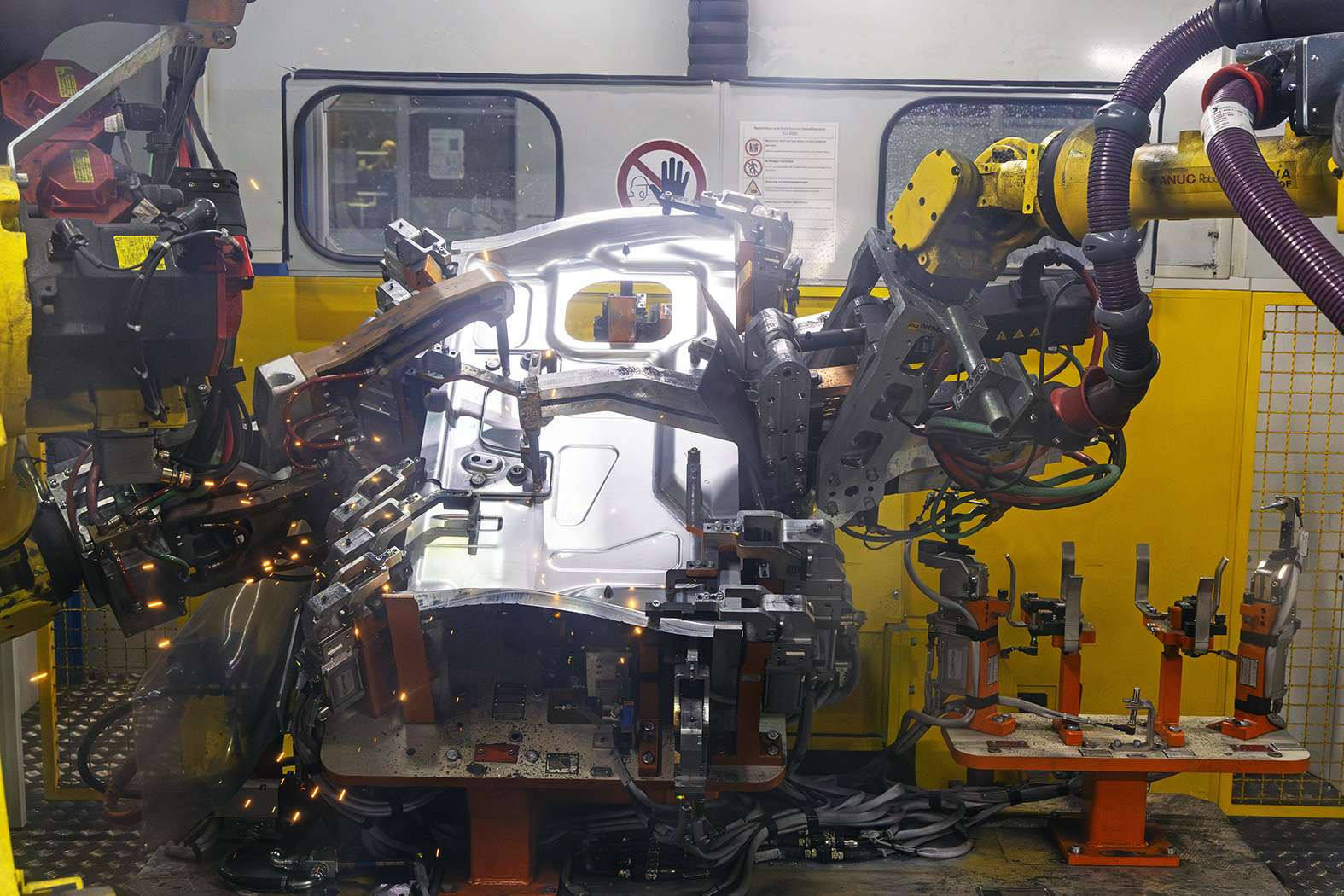
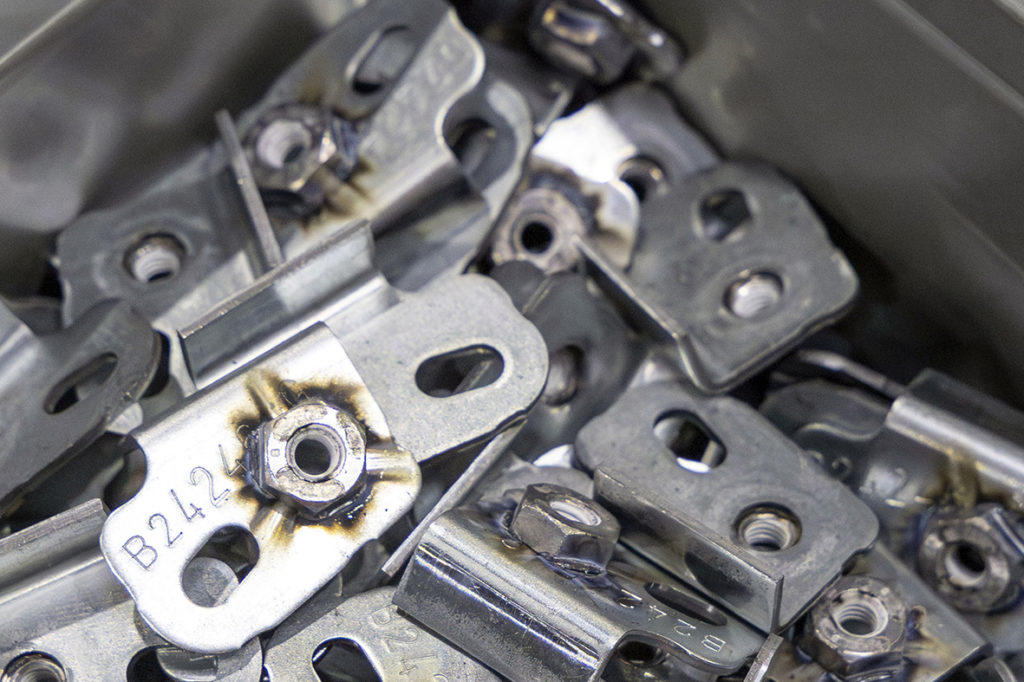
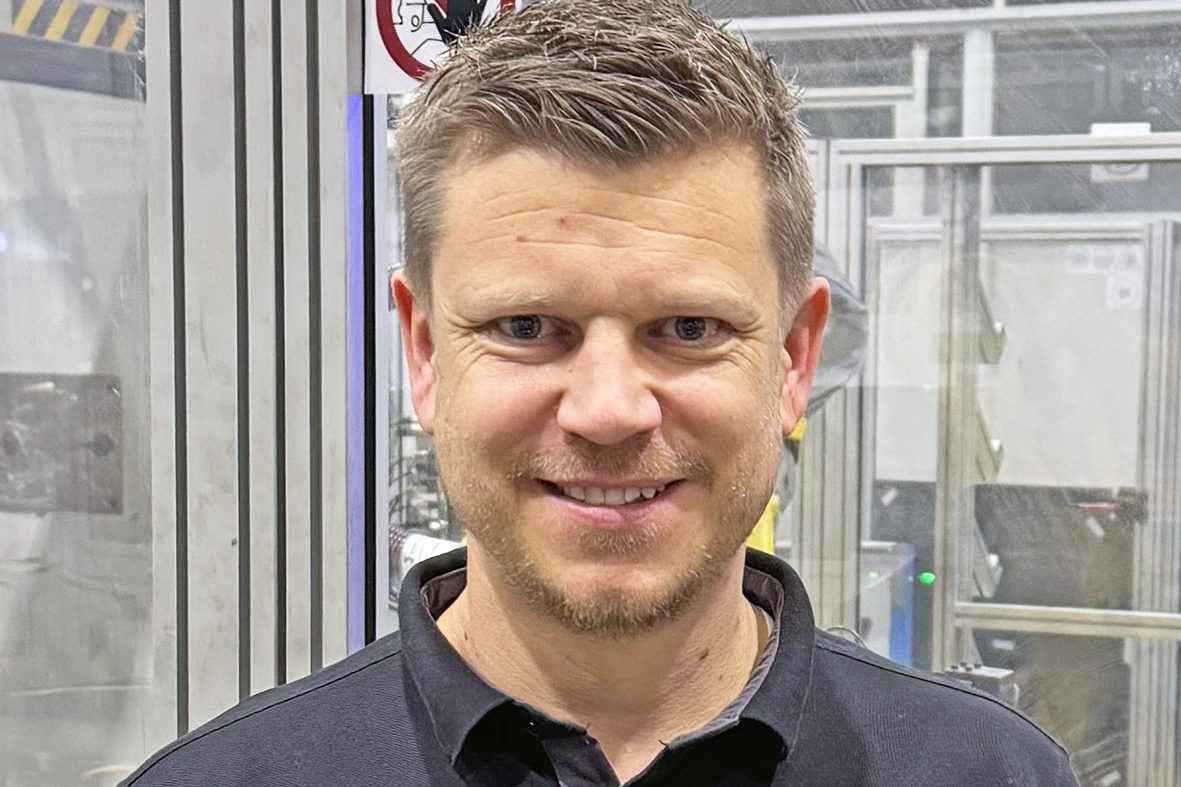
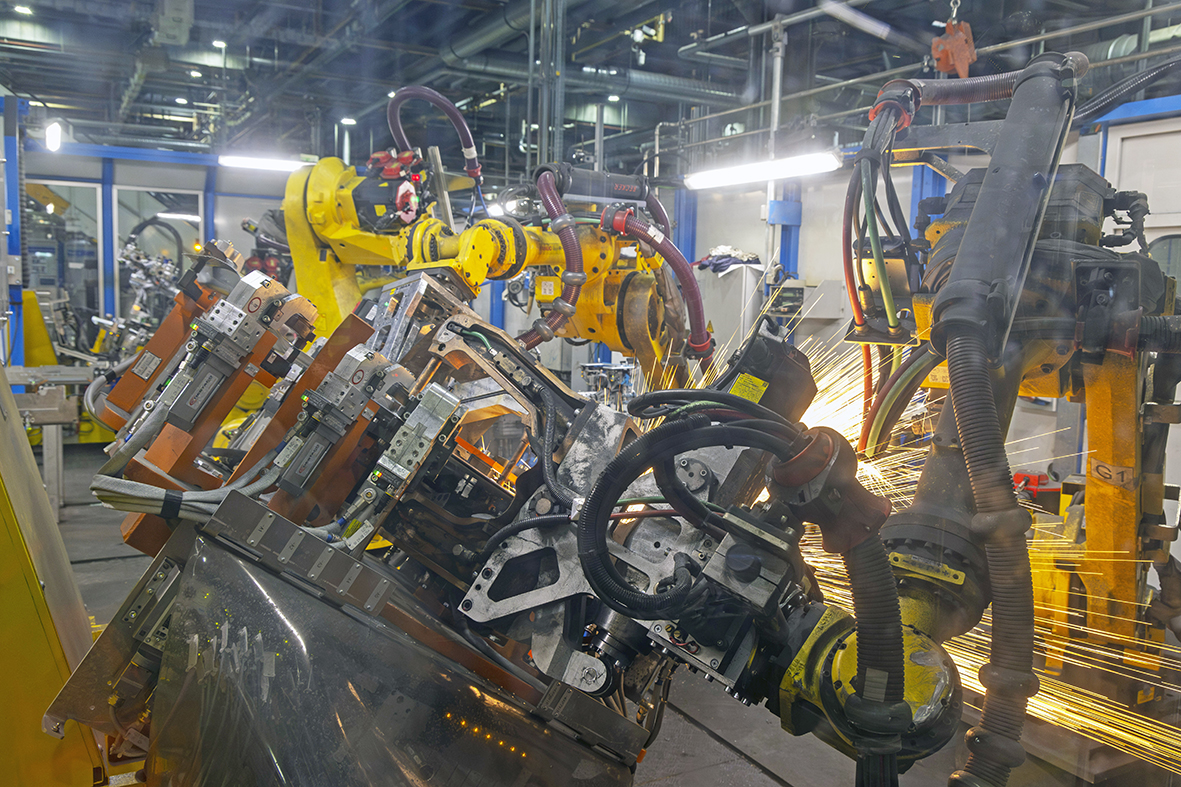
Auch Leitner hat seine Profession von der Pike auf am pfälzischen Standort gelernt, seit 30 Jahren ist er dabei. Als einstiger Instandhalter kennt er den Maschinenpark bestens, zu seiner Expertise zählt inzwischen auch die Prozessoptimierung, das so genannte Advanced Industrial Engineering. „Neue Technologien und Methoden sind bei uns am Standort Pflicht. Sie machen uns wandlungsfähig – und effizient“, sagt er. Ein wichtiger Hebel ist die weitere Automatisierung. Wie weit fortgeschritten das autarke Arbeiten des Maschinenparks bereits ist, lässt sich auch im K25 beobachten. In jener Halle, in der die Pressteile bei Bedarf weiterverarbeitet werden.
Maschinen arbeiten autark
Es ist ein faszinierendes Schauspiel: In 54 geschlossenen Kabinen, den sogenannten Schweißzellen, vollführen Roboterarme einprogrammierte Bewegungen. Sie setzen Schweißnähte und Schweißpunkte, tragen Kleber auf, fügen Bauteile zusammen. 28 weitere Zellen sind spezialisiert auf das „Buckelschweißen“; eine Technologie, um Verbindungselemente wie Muttern oder Bolzen aufzubringen. Einige Zellen werden von außen von Mitarbeitern permanent per Hand bestückt, bei anderen ist selbst das nicht mehr nötig. „Es reicht, einmal die Stunde einen Shooter bereitzustellen“, sagt Florian Klinker, Gruppenleiter des Engineering-Teams.
„Die Automatisierung schreitet voran. Speziell für den Anlauf des Grandland haben wir die Anlagen umgebaut und optimiert.“
– Florian Klinker, Gruppenleiter Engineering –
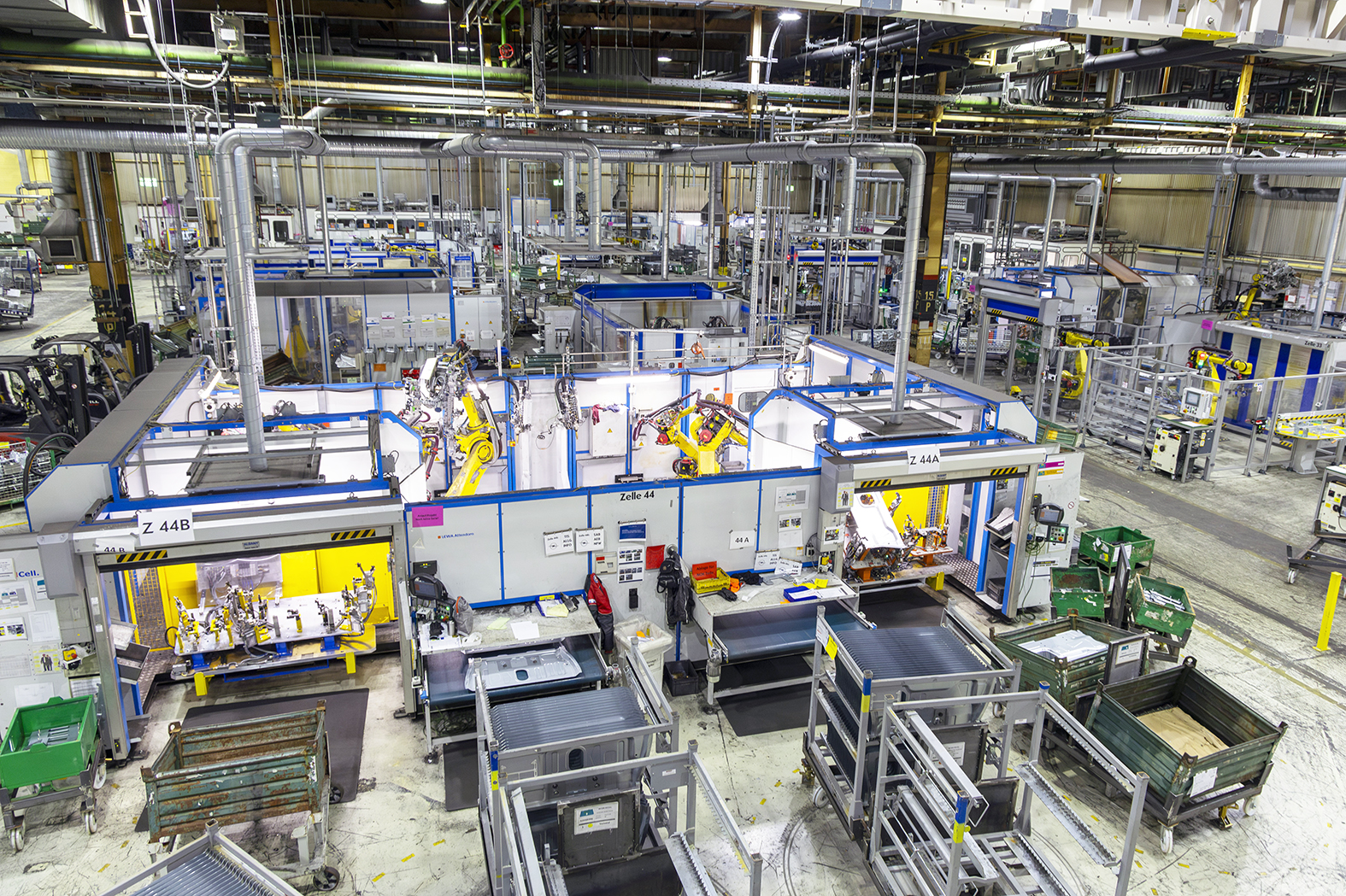
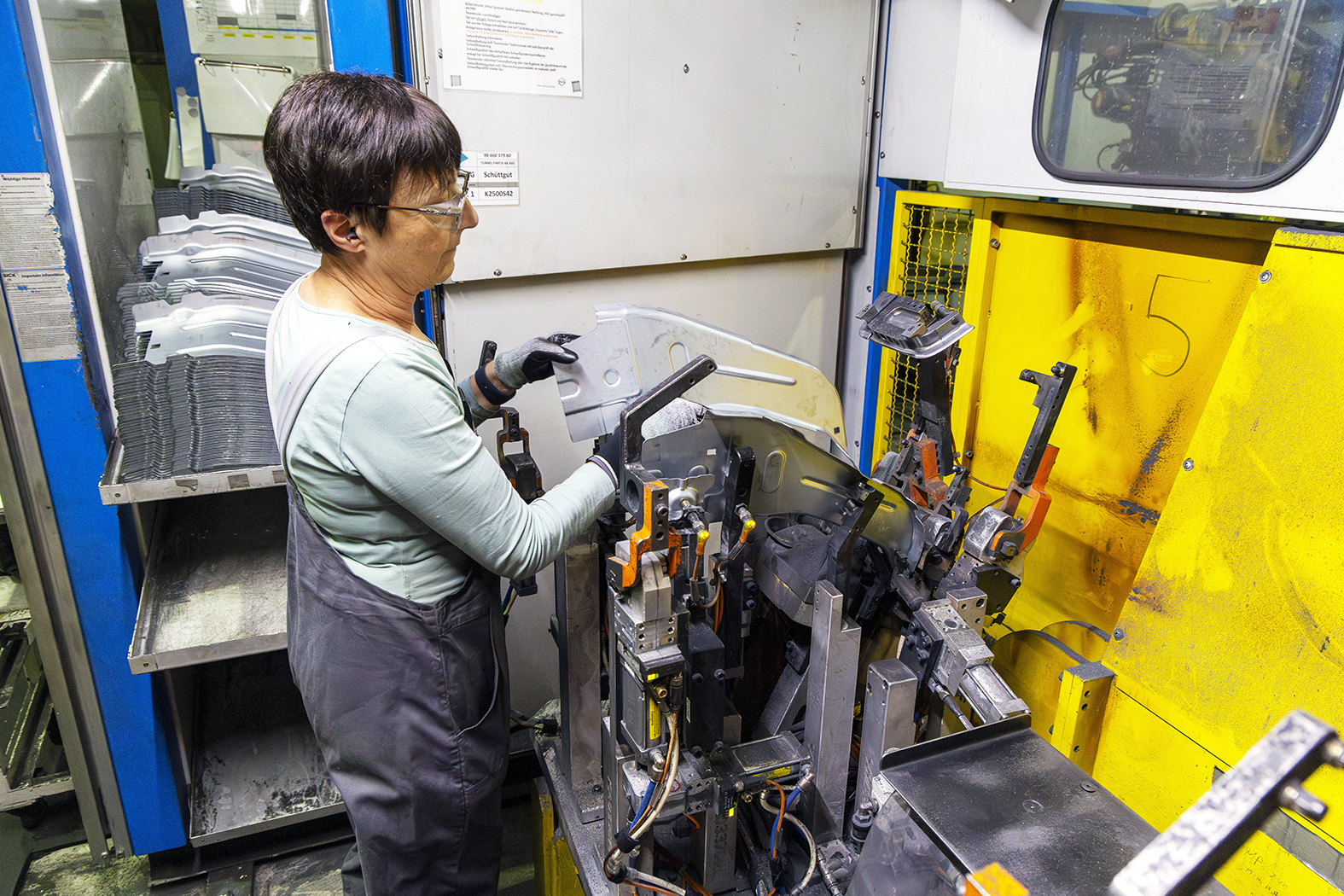
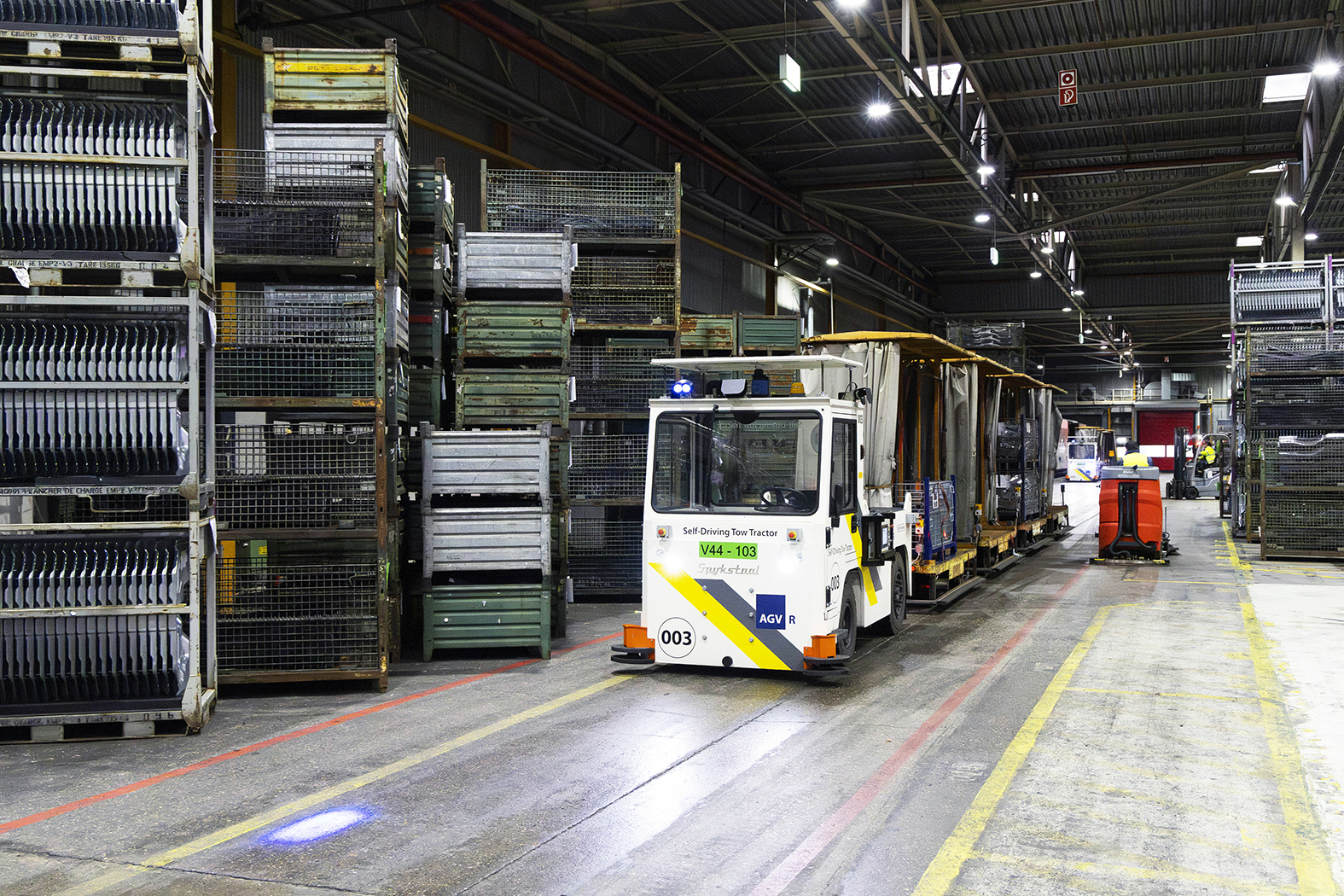
Der „Shooter“ ist ein großer Korb. Pressteile für die Weiterverarbeitung liegen darin bereit, nach keinem Muster platziert, sondern zufällig. Der Roboterarm greift mit Hilfe einer 3D-Kamera präzise zu, platziert das Werkstück auf der Arbeitsfläche – und der Schweißprozess startet. „Vier weitere Zellen werden demnächst vollautomatisiert arbeiten“, kündigt Klinker an. Ohnehin seien die Anlagen stets im Fluss. „Speziell für den Anlauf des Grandland haben wir vieles umgebaut und optimiert.“
Weitere Aussichten: Hochbetrieb
Zwischen 280 und 310 Tonnen Fertigteile verlassen die Hallen – jeden Tag. Der Abtransport erfolgt weitestgehend automatisiert. Am Rand der Halle steht ein selbstfahrender Schlepper, Induktionsschleifen im Boden und eine intelligente Sensorik führen das fahrerlose Transportsystem sicher ans Ziel. Alle paar Minuten heißt es: Abfahrt in Richtung K70, den Versandbereich. Von hier aus geht es nach Eisenach – und in weitere Werke. Robert Leitner kann in seiner Funktion mehrere Wochen in die Zukunft schauen: „Die Auftragsbücher – sie bleiben voll.“
März 2025