–––––
Roboter schieben sich Haut und Gerippeteile zu.
Grünes Licht signalisiert nicht nur „Freie Fahrt“, es ist besser geeignet als jedes andere, um Fehler auf glatten Oberflächen zu identifizieren. Aus diesem Grund wandern im Lauterer K25 frisch gefertigte Aluminium-Motorhauben zur Stichprobenkontrolle in den „Grünlicht-Raum“, wo sie sich den kritischen Blicken der Qualitätsprüfer stellen müssen. Ein erfahrener Betriebsleiter wie Volker Spang erkennt jede noch so kleine Ungenauigkeit sofort. Und erst, wenn er zufrieden nickt, hat die Haube tatsächlich „Grünes Licht“ für den weiteren Produktionsablauf.
Mittlerweile ist er zufrieden. „Wenn wir uns in ein neues Projekt einarbeiten, muss zu Beginn immer viel Zusatzarbeit geleistet werden“, erklärt der Betriebsleiter. „Seit dem offiziellen Produktionsstart aber läuft diese Haube im grünen Bereich.“ Und in den Fertigungszellen des K25 brummt’s wie in den Jahren zuvor: Roboter schieben sich Haut und Gerippeteile zu, fügen sie in Sekundenschnelle zusammen. Es scheint, als habe sich gegenüber der Arbeit an der Haube des Vorgängermodells nichts geändert.
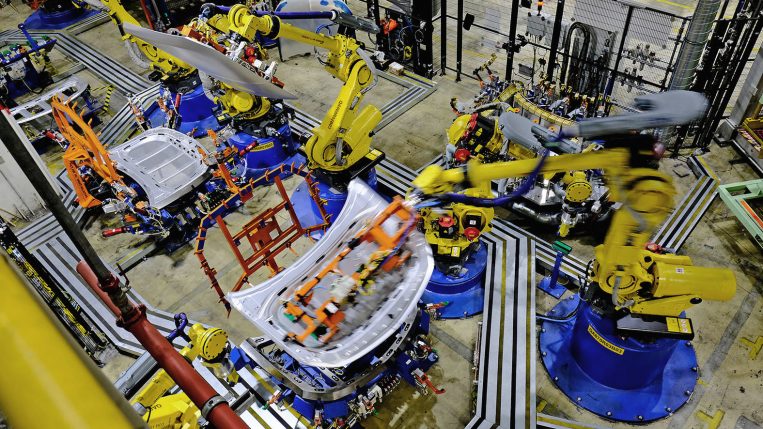
Hauben im K25 Der technische Fortschritt steckt im Detail.
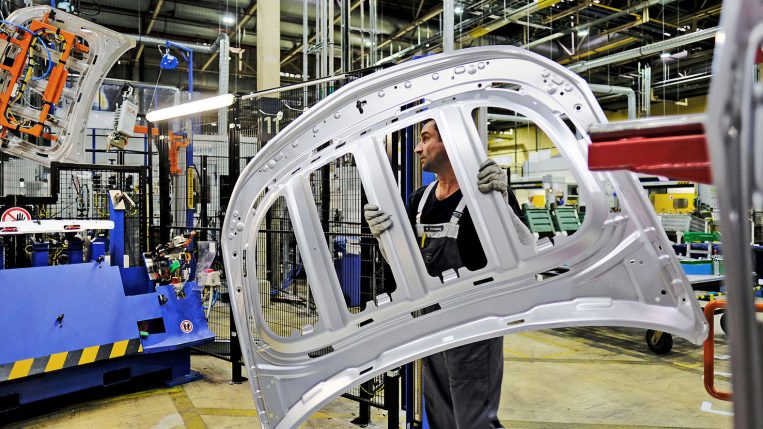
Bereit für Innovation Das Gerippe wird mit der Haube in einem neuartigen Verfahren verschweißt.
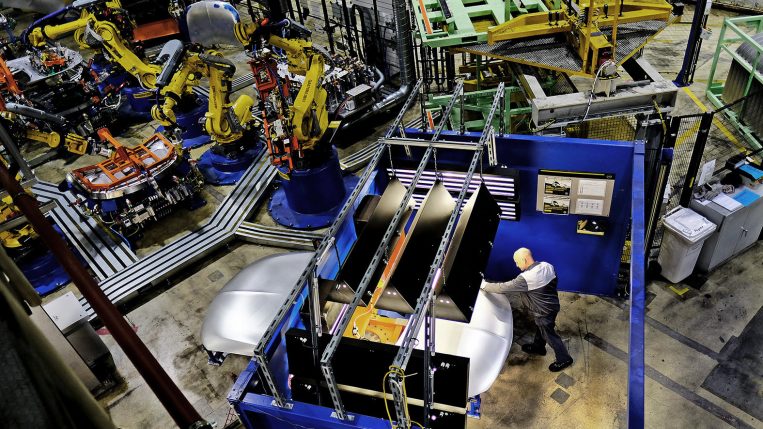
Händchen für Aluminium Know-How und Erfahrung sind das A und O im Umgang mit dem sehr speziellen Werkstoff
Auf den ersten Blick vielleicht. Der technische Fortschritt steckt im Detail. Jeder Modellwechsel setzt neue Maßstäbe, hält für die Fertigung neue Herausforderungen und neue Technologien bereit, die es erforderlich machen, die bereits erlernten Fähigkeiten weiterzuentwickeln.
Kompetenz in Sachen Aluminium
Für die Montage der neuen Insignia-Haube beispielsweise bedienen sich die Pfälzer – als erstes Werk in Europa – eines neuen Punktschweißverfahrens, das den sehr speziellen Eigenschaften des Werkstoffes Aluminium gerecht wird. Dazu mussten neue Schweißzangen und Fräsmesser installiert und eingearbeitet werden, auch das Konzept zur Qualitätssicherung wurde entsprechend angepasst. „Dabei haben wir eng mit dem Schweißlabor in Rüsselsheim zusammengearbeitet“, berichtet Lauterns Launch Manager Michael Müllenbach.
Erfahrung mit dem Leichtmetall haben die Lauterer schließlich schon einige gesammelt: Die Pressenstraße 11 im K19 fertigt bereits seit 2001 Alu-Teile, im Wechsel mit Stahl. Besonderer Benefit: Ihre Schnittabfälle werden im Keller des Presswerks sortenrein getrennt, was sich beim Weiterverkauf auszahlt. Für Alu können auf dem Recycling-Markt hohe Preise erzielt werden.
––––––
„Neben Motorhaube, Vordersitzstruktur sowie Vorderrad- und Hinterradträger fertigen wir über 50 Einzelteile der Insignia-Karosserie.“
– Launch Manager Michael Müllenbach –
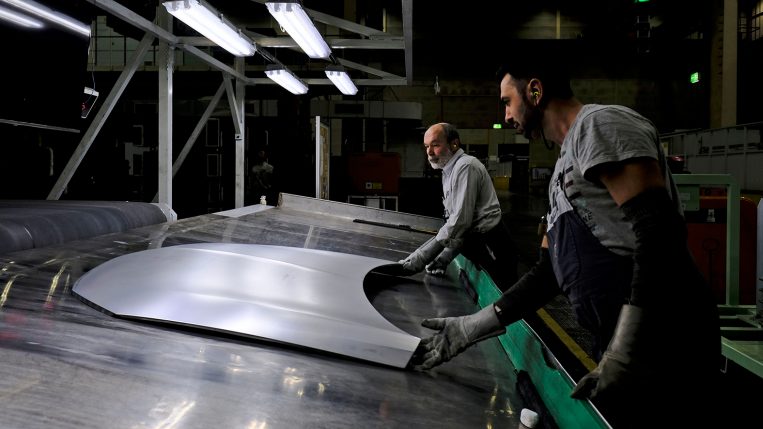
Genau hingeschaut Noch an der Pressenstraße 11 unterziehen Gunter Heinz (links) und Fidan Herqishta die gepresste Haube einem ersten Check.
––––––
Das zu verarbeitende Blech ist kaum dicker als ein Blatt Papier.
Die Fähigkeit, mit Metall sensibel umgehen zu können, bringen die Lauterer auch an anderer Stelle ein. Dann, wenn es um Beiträge zur Gewichtseinsparung am neuen Insignia geht. Immerhin ist das neue Flaggschiff in der Sports Tourer-Variante bis zu 200 Kilogramm leichter. Um die Einsparung zu erreichen, hat Opel auch den Einsatz „hochfester Stähle“ weiter kultiviert. „Wir haben jetzt überwiegend mit Blechdicken von 1,5 Millimeter zu tun“, erklärt Michael Müllenbach. Dafür müssen die Presswerkzeuge entsprechend ausgelegt sein – und Werkzeugmacher wie Pressenfahrer ihr Handwerk beherrschen. „Nach dem ersten Verformen verfestigen sich diese hochfesten Stählen umgehend. Das bedeutet: Der erste Schlag muss sitzen.“
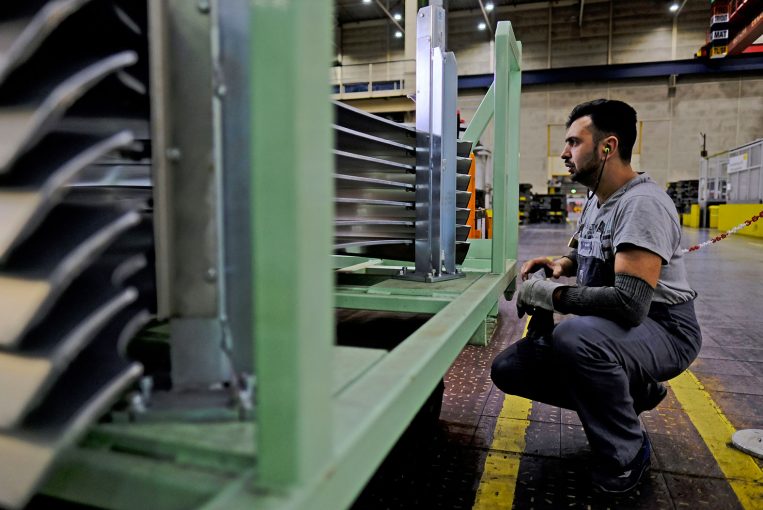
Vor dem Abtransport ins K25 Fidan Herqishta unterzieht die gerade gepressten Hauben einem weiteren Check.
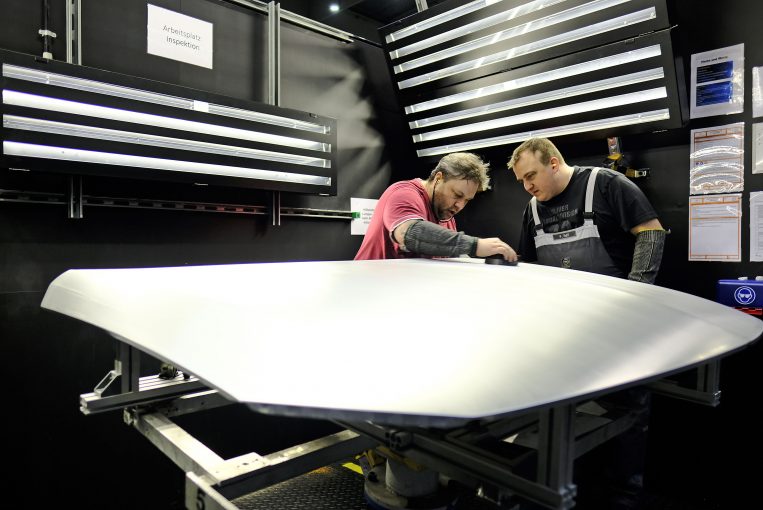
Hochwertiges Qualitätsgefühl Mario Rossello (links) und Patrick Pfaff akzeptieren nur perfekt glatte Oberflächen.
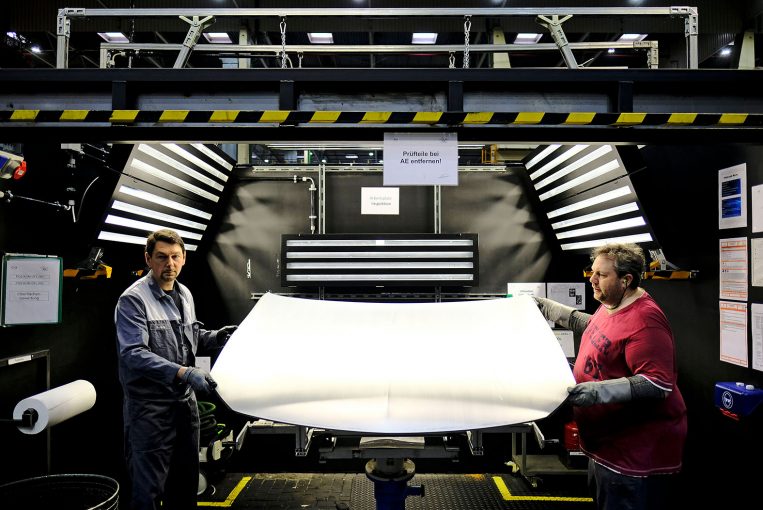
Haube des Flaggschiffs Bernd Klag und Mario Rosello (rechts) mit einem Top-Produkt „Made in Lautern“.
Eine besondere Herausforderung stellt die neue Hinterachse des Insignia dar, an der ebenfalls Gewicht eingespart wurde. Und die sich jetzt „feuerverzinkt“ präsentiert, was einen noch besseren Korrosionsschutz gewährleistet. „Beim Schweißen verzinkter Teile besteht allerdings die Gefahr, dass der Zink verdampft“, weiß der Launch Manager. Um dieses Risiko zu minimieren, braucht es die Sorte Erfahrung, über die Klaus Dieter Mayer verfügt, einem im Werkzeugbau, der Schweißtechnik und der Instandhaltung erfahrenen Meister. Auch seine Teamleader haben ihr Handwerk von der Pike auf gelernt.
Weltweit unterwegs
Zudem hat sich die Mannschaft in speziellen Workshops bei Zulieferern vorbereitet, und war zum Anschauungsunterricht in den USA. Überhaupt sind die Pfälzer weltweit unterwegs, wenn es darum geht, sich mit neuen Produktionsanlagen vertraut zu machen und Know-how weiterzuentwickeln: „Wohl kaum jemand im europäischen Automobilgeschäft arbeitet länger mit Unternehmen in China und in Korea zusammen als wir.“
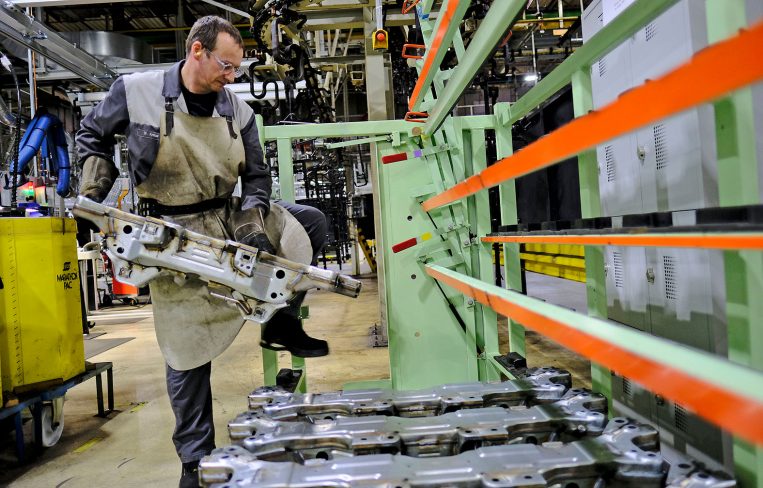
Bestens vorbereitet Die Kollegen in der Achsfertigung.
––––––
Um das Schweißen verzinkter Teile zu bewerkstelligen, braucht es die Sorte Erfahrung, über die das Lauterer Team verfügt.
Ebenfalls schon seit Jahren eine Pfälzer Spezialität: Der „Cross Car Beam“, der Querträger der Armaturentafel. „Ein Stück Qualität, das jeder Opel-Fahrer auch optisch wahrnimmt – und zwar im Innenraum, in dem wir uns im neuen Insignia besonders viel vorgenommen hatten.“ Der Auftrag für die Lauterer Kollegen hieß also: Die hochkomplexe Komponente, an die 40 Einzelteile geschweißt werden, so filigran wie nie zu fertigen inklusive makellosen Oberflächen und Spaltmaßen im Null-Toleranz-Bereich. Gesagt, geplant, getan.
Null-Toleranz für das Spaltmaß
Die Spezialisten in der Sitzfertigung agieren nach wie vor auf höchstem Niveau. „Die Sitzanmutung im neuen Insignia ist beeindruckend“, konstatiert Michael Müllenbach. „Die Bauart der Sitzschiene ist im neuen Modell etwas anders, die Herstellung aber im Wesentlichen wie für den Astra.“ Der Bereich im K20 wurde um zwei neue Montagestationen erweitert, damit die Nachfrage für beide Modelle gestillt werden kann.
In der Karosserie verbaut werden zudem noch rund 50 weitere Strukturteile aus Pfalz. Etwa 55 Millionen Euro hat Opel in Kaiserslautern investiert, um das Werk „fit“ für den neuen Insignia zu machen. Dass auf höchstem Niveau produziert wird, dafür garantiert die komplette Lauterer Mannschaft.
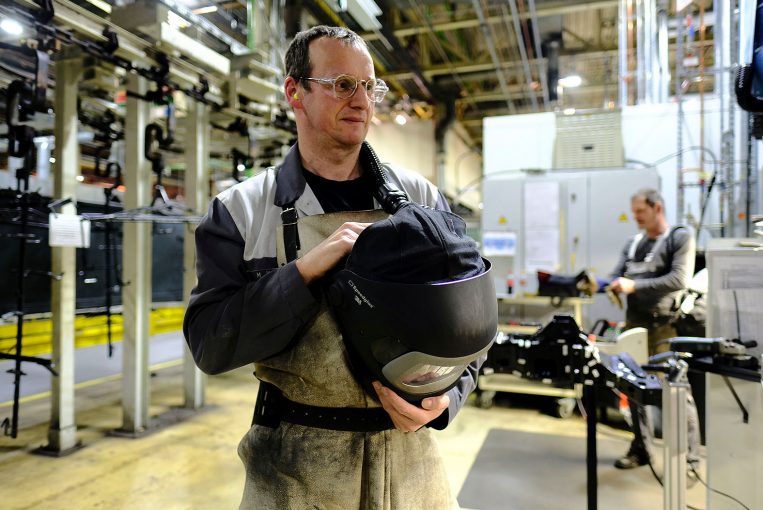
Durchatmen Mario Kraus ist einer der Spezialisten, der das Schweißen verzinkter Teile beherrscht.
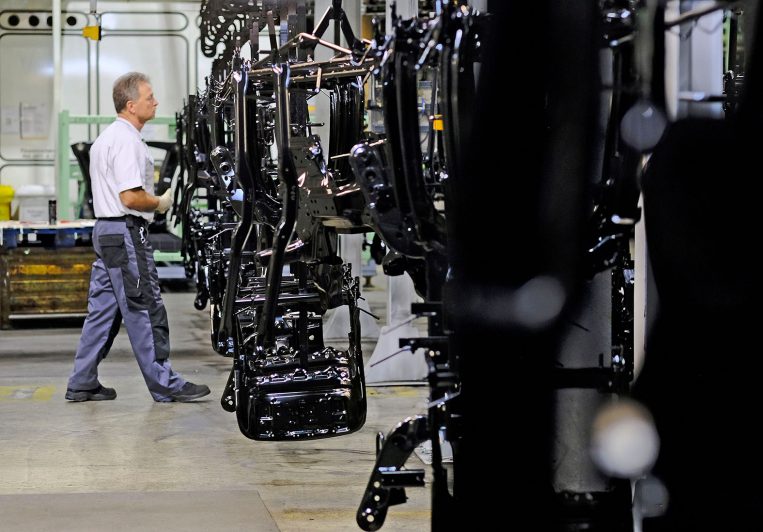
Back in black Die Sitzlehnen kehren aus dem Tauchlackierbad zurück.
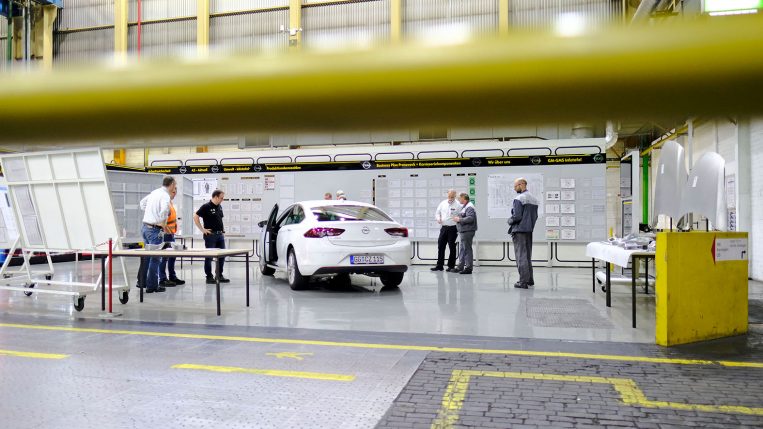
Das große Ganze Auf der Ausstellungsfläche im Presswerk begutachten die Fertigungsfachleute, wie sich ihre Komponente ins Gesamtbild des neuen Insignia fügen.
Stand Mai 2017