––––––
Das „Presswerk 4.0“ ist nicht allzu weit entfernt. Einzelne Elemente bewähren sich bereits im täglichen Betrieb.
––––––
Dr. Niels Koch hat eine Vision. Ein Presswerk, in dessen Produktion es keine Nacharbeit mehr gibt. In dem das absolut denkbare Mindestmaß an Schnittabfällen anfällt. In dem jedes Stück Blech in optimaler Qualität geschnitten und geformt wird. In dem 1A-Qualität zu einhundert Prozent exakt vorhergesagt werden kann, weil man sie in die Anlagen einprogrammieren kann. Und in der Pressen in der Lage sind, auf sich verändernde Anforderungen selbstständig zu reagieren und sich permanent selbst zu verbessern.
Eine Utopie? Keinesfalls. Eigentlich handelt es sich noch nicht einmal mehr um eine Vision. Sondern um eine sehr konkrete Vorstellung, wie das „Presswerk 4.0“ funktioniert. An dessen Umsetzung wird längst nicht mehr nur intensiv gearbeitet – im Rüsselsheimer Presswerk bewähren sich einige Elemente dieser Zukunftsversion bereits im täglichen Betrieb. Und noch in diesem Jahr werden weitere große Schritte in Richtung „Presswerk 4.0“ unternommen.
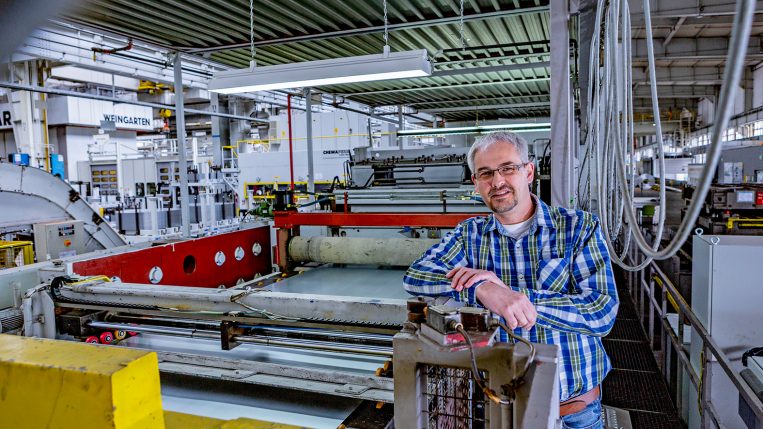
Niels Koch an der Zuschnittanlage: Das Projekt „Presswerk 4.0“ startete im Jahr 2015. In den beiden Folgejahren folgte die aufwendige Konzeptarbeit sowie eine Testphase. Dieses Jahr nun hat das Team damit begonnen, die Zukunft im Stammwerk Realität werden zu lassen.
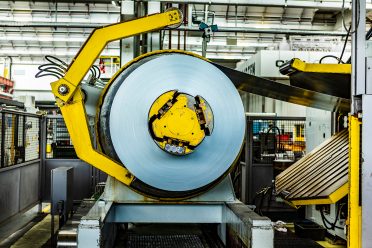
Auch die Beschaffenheit des Blechs, aufgewickelt zu Coils, wird mit Hilfe von Sensoren erfasst.
WARUM VIERTE INDUSTRIELLE REVOLUTION?
Wasser und Dampf gaben den Maschinen erstmals die Kraft, Produkte in großen Mengen zu produzieren – die Grundlage für die erste industrielle Revolution. Elektrizität und das Fließband waren die Säulen der zweiten Stufe, bevor Elektronik und IT die Industrieproduktion weiter optimierten. Mit dem Einzug digitaler Technologien steht aktuell nicht nur die vierte Umwälzung bevor – gleichzeitig findet ein Paradigmenwechsel statt. Haben die ersten drei industriellen Revolutionen die Produktionsmaschinerie optimiert, kehren sich nun die Vorzeichen um: Nicht die Maschine fertigt ein Produkt, das Produkt teilt der Maschine mit, wie es produziert werden möchte und steuert sich selbst durch die Fertigung. Das Schlagwort lautet Industrie 4.0.
Niels Koch ist bei „Advanced Manufacturing Technologies“ (AMT) für die Entwicklung neuer Technologien für die Opel-Presswerke zuständig. Unter der Leitung von Dr. Petra Krammer arbeitet der gesamte Bereich am Idealbild der „Smarten Fabrik“, in der Menschen, Maschinen, Werkzeuge und Ressourcen perfekt vernetzt sind und einander zuarbeiten.
––––––
Münzgroße Sensoren und Scanner, die verbaut werden, machen die Pressen smart.
––––––
Für den oberflächlichen Betrachter wird davon im Presswerk eines Tages vergleichsweise wenig zu sehen sein. Denn an der äußeren Gestalt der monströsen Pressenstraßen wird sich nicht viel ändern. Die entscheidenden Verbesserungen zu Qualität in Kontinuität und Perfektion wird in der Hauptsache auf elektronischen Wegen gewährleistet. Die nötige Basis an Daten dafür liefern bisweilen nur münzgroße Sensoren und Scanner, die in den Anlagen verbaut werden.
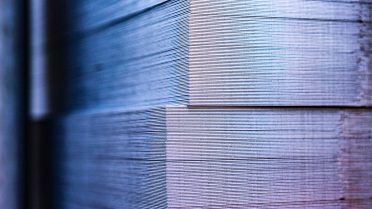
Im Presswerk 4.0 werden präzise Informationen zur Beschaffenheit jeder einzelnen Platine gesammelt, bevor die Umformung beginnt.
A und O dieser Industrie 4.0-Version ist die Materialeingangsprüfung. Die „Coils“, die großen Blechrollen, die im Presswerk angeliefert werden, sind von Lieferanten innerhalb vorgegebener Toleranzwerte gefertigt worden. „Über Veränderungen, die sich während des Transport oder der Lagerung an der Oberfläche oder beim Ölauftrag ergeben haben, wussten wir bislang nicht viel“, erklärt Niels Koch. „Im Presswerk 4.0 müssen wir daher erst einmal absolut präzise Informationen zur Beschaffenheit jedes einzelnen Coils sammeln, bevor wir mit Zuschnitt und Umformung beginnen.“
Sensoren und Scanner für eine präzise Messung von Ölauftrag und Blechdicke sind in Rüsselsheim bereits installiert. Ein Verfahren zur Bestimmung der Werkstoffkennwerte des Blechbandes konnte bereits erfolgreich getestet werden und soll in diesem Jahr im Presswerk installiert werden. Zudem müssen alle Informationen auch auf jedem Teilstück abrufbar sein. Daher wird jede Platine mit einem Code versehen, ehe sie ihren Weg durch die Pressen antritt.
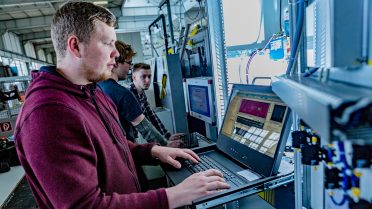
Auswertung: Am Rechner wird die Ölverteilung dargestellt und gespeichert. Im Hintergrund sieht man die Auswerteeinheit, an der die Blechdicke erfasst wird.
––––––
Jede Platine wird mit einem Code versehen, ehe sie ihren Weg durch die Pressen antritt.
––––––
Einige der innovativen Verfahren, die die Vorausentwickler konzipiert haben, sind mittlerweile zum Patent angemeldet. Studenten, die Examensarbeiten vorbereiten, unterstützen bei der Grundlagenforschung. Und bevor im Presswerk 4.0 etwas zur Hardware wird, ist es bereits mit Hilfe eines „digitalen Zwillings“ simuliert worden.
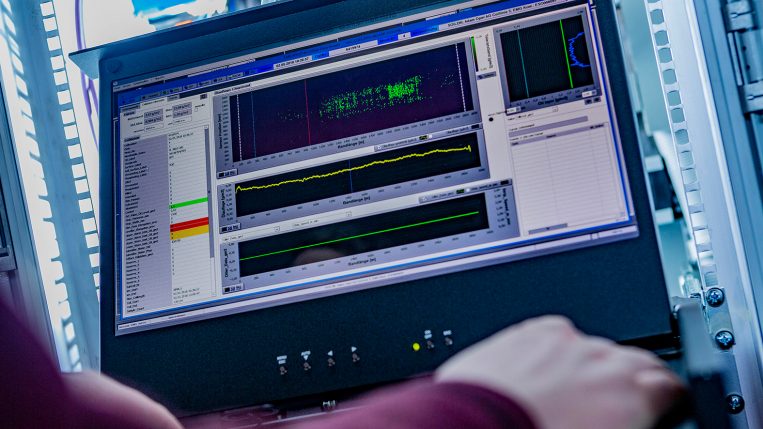
Mit dem bloßen Auge nicht zu erfassen: Die Ölverteilung auf einer Platine.
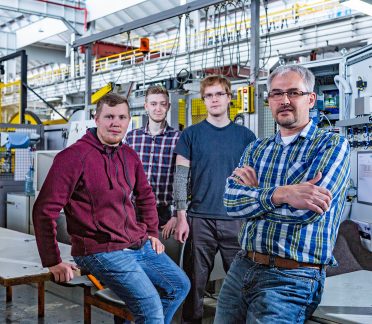
Das Projektteam: Max Morlock, Julius Bremer und Leon Kallenbach, alle drei sind Duale Studenten, haben unter der Leitung von Niels Koch das Presswerk 4.0 auf den Weg gebracht (von links).
––––––
Die Maschinen melden selbst, wenn eine Instandhaltung notwendig wird.
––––––
Die Daten, die bei der Materialeingangsprüfung erhoben werden, halten Einzug in das Programm, das anschließend den gesamten weiteren Prozess steuert, insbesondere das „Feintuning“ der weiterverarbeitenden Werkzeuge. Weitere im Ablauf installierte Einheiten sind in der Lage, Meldungen an die Instandhaltung abzusetzen, sobald sie Bedarf erkennen – inklusive eines entsprechenden Lösungsvorschlages. Die „vorausschauende Instandhaltung“ ist also ebenso wenig eine Utopie wie das selbstständige Dazulernen der Anlagen.
Presswerk vernetzt sich
In der Endausbaustufe werden die Presswerksdaten mit den angrenzenden Fertigungsbereichen vernetzt. Denn präzise Informationen über die Beschaffenheit eines Blechteils bilden wiederum die beste Grundlage für ein hundertprozentig genaues Verarbeiten im Karosseriebau und anschließend eine perfekte Lackierung.
So entsteht die „Smarte Fabrik“ Stück für Stück – und bis Jahresende werden es noch einige Puzzleteile mehr sein. „Die reibungslose Implementierung wäre ohne die tatkräftige Unterstützung der Mitarbeiter des Presswerks und der Produktionsplanung in Rüsselsheim nicht möglich gewesen“, richtet Niels Koch seinen Dank an die Kollegen.
Stand Mai 2018