- Dbamy o środowisko.
Myślimy globalnie, działamy lokalnie!
Dbanie o środowisko to nie tylko wielkie projekty, ale także codzienne nawyki – w trosce o środowisko przykładamy wagę do segregacji odpadów.
W zakładzie w Gliwicach na co dzień wykorzystujemy kosze z etykietami w czterech kolorach. Do koszy z etykietami białymi wrzucamy m.in. wszystkie śmieci komunalne – czyli resztki jedzenia (również fusy) i zabrudzone opakowania po nim (papier, folia, kubeczki) oraz szkło. Do koszy z czerwoną etykietą wędrują odpady niebezpieczne – sorbenty i materiały zanieczyszczone substancjami niebezpiecznymi, np. czyściwa, rękawice robocze. Żółta etykieta zarezerwowana jest dla tworzyw sztucznych – plastikowe butelki, kubeczki po jogurtach (umyte – ze względu na zapachy!) i metalowe (np. puszki po napojach – pamiętajcie, by je zgnieść). Niebieskie etykiety oznaczają kontenery przeznaczone na papier i karton – pousuwajcie zszywki, taśmy klejące i rozłóżcie karton, gdy jest to możliwe.
-
-
System do segregacji odpadów w Gliwicach.
W zakładzie w Tychach stosuje się dwa kolory etykiet. Pomarańczowe oznaczają pojemniki, do których należy wrzucać odpady niebezpieczne, np. zużyte czyściwo, czy opakowania zanieczyszczone niebezpiecznymi chemikaliami. Białe etykiety znajdują się na koszach przeznaczonych na odpady inne niż niebezpieczne np. papier i tektura, odpady komunalne.
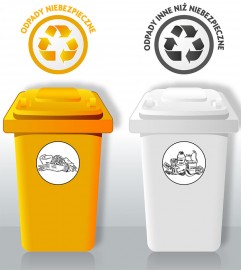
System do segregacji odpadów w Tychach.
Zrealizowaliśmy kilka nowych projektów, które w znaczący sposób pozwalają na oszczędności surowców – wyjaśnia Mateusz Kubiński, inżynier z działu Facilities, odpowiadającego za dostarczanie i nadzorowanie mediów, niezbędnych do funkcjonowania fabryki. – Jednym z nich jest zainstalowanie specjalnych palników gazowych do bezpośredniego ogrzewania powietrza w wentylacji. Jest ich pięć i są w stanie podgrzać aż 1 milion metrów sześciennych na godzinę!
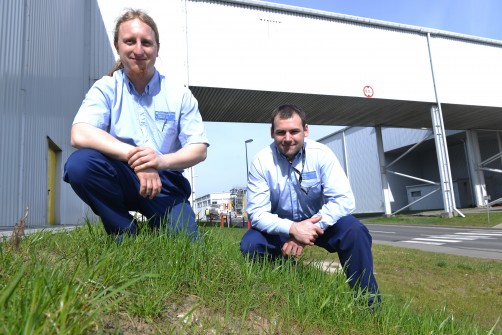
Mateusz Kubiński i Michał Lepieszko z działu Facilities.
Palniki pozwalają zaoszczędzić na wodzie grzewczej dostarczanej z elektrociepłowni, która dotąd była źródłem ciepła. Jest ona bardzo droga, a i jej dostawy obarczone są dużymi stratami w transporcie. – Tymczasem sprawność palników oceniamy na 99 procent, co oznacza, że praktycznie nie notujemy strat surowca – zaznacza Mateusz Kubiński. – Paliwo do nich czerpiemy bezpośrednio z sieci gazowej. Jest tańsze i w ostatecznym rozrachunku efektywniejsze.
Palniki zainstalowano tak, by pracowały na potrzeby lakierni. Wyglądają imponująco. – Z dumą mogę powiedzieć, że jesteśmy prekursorami tego typu rozwiązań w plantach GM – wyjaśnia Mateusz Kubiński. – I już widzimy, że instalacja bardzo się opłaciła.
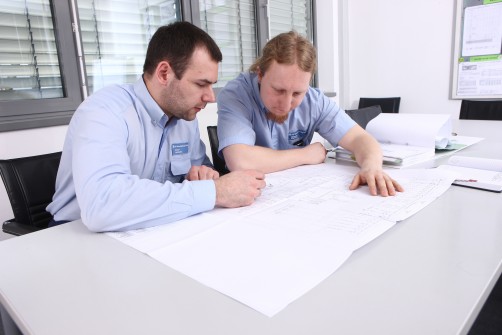
Michał i Mateusz pracują nad kolejnymi projektami.
Dział stale szuka miejsc, w których można zwiększyć efektywność wykorzystywanych narzędzi, coś poprawić. Niedawno wymieniono światła na drogach ewakuacyjnych z energochłonnych na dużo efektywniejsze typu LED i trwają prace nad wymianą lamp sodowych nad linią produkcyjną na LED-owe.
Wymieniono też sterowniki kompresorów pracujących na rzecz fabryki. Kompresorów jest 5 (4 duże, jeden mniejszy) i nie zawsze wykorzystywano racjonalnie ich moce. Teraz system monitoringu analizuje zużycie energii i uruchamia najodpowiedniejsze do aktualnych potrzeb kompresory tak, by pracowały przynajmniej na 80 proc. swojej mocy. – Falowniki regulujące zużycie energii w procesie woskowania wstępnego i końcowego w lakierni to też nasz pomysł i realizacja – mówi z dumą Michał Lepieszko, także pracujący w Facilities. – Moc silników jest zawsze adekwatna do oczekiwań.
Przeciętne wydatki na realizację projektu ekologicznego zamykają się w kwocie od 800 tys. do 1 mln zł, a zwracają najczęściej w ciągu 9-12 miesięcy. Korzyści dla środowiska są bezcenne.