- Begutachten ein neues Presswerkzeug: Paul Hüttenberger, Thomas Schäufle, Anel Bajric, Danny Rohrig und Andreas Henke.
“Our pressing tools can be manufactured with greater precision, and we can deliver more quickly than ever.”
– Andreas Henke –
Head of Central Functions in the central workshops
The central workshops in Rüsselsheim have heralded in a new era. In addition to their other core businesses of machine and fixture construction, pressing tool engineering is now set to manufacture tools for large shell components up to 4.5 meters in length, such as those used in a complete side body panel of the Insignia. What’s more, it had simply not been possible to attain these sizes within the company, now delivered at a level of precision not available in the past. The new ‘Heynuform 4000’ is a five-axis milling facility that is responsible for this quantum leap in engineering.
LARGE AND INTELLIGENT
The facility is not only large, it’s also intelligent. It can automatically change five machining heads and up to 200 tools. And the Heynuform will not be toiling away on its own for long. There will be a second facility set up in October to provide deliveries to the pressing plants in Europe more quickly, more intelligently, and more precisely than ever before.
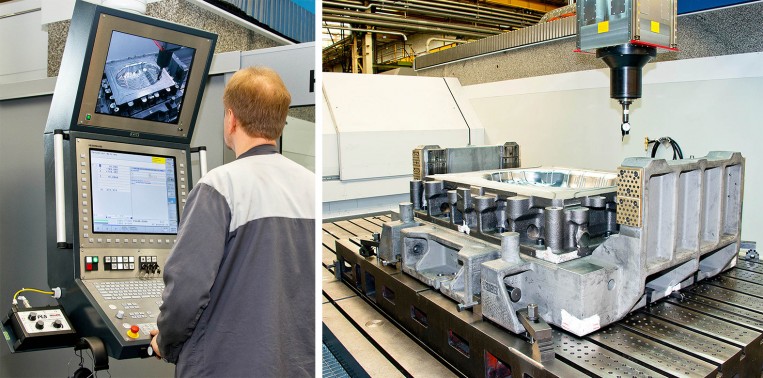
Heralding in a new era: the Heynuform. The milling monster can also scan. Thomas Schäufle monitors activities on his display.
Thomas Schäufle trained as a tool maker, but while working at the central workshops he also learned more about controlling activities and programming for complex machines. “We have several machines in our department that can automatically change tools stored in their magazines, but the Heynuform tops everything.” Schäufle completed an on-site training course with nine others to learn how to operate the new facility. “There were many new things that we needed to learn. It’s similar to learning how to navigate a new operating system for a computer, but it was so much more exciting.”
SCANNING A BASE COMPONENT
The pictures here show Thomas Schäufle working on a milling order. He scans a base component using the measuring sensor located on the milling head to compare the data with information gained from the simulation. “We then send the data to Development. This way, we can both profit from the theoretical and the actual information, which enables us to continually improve the components.”
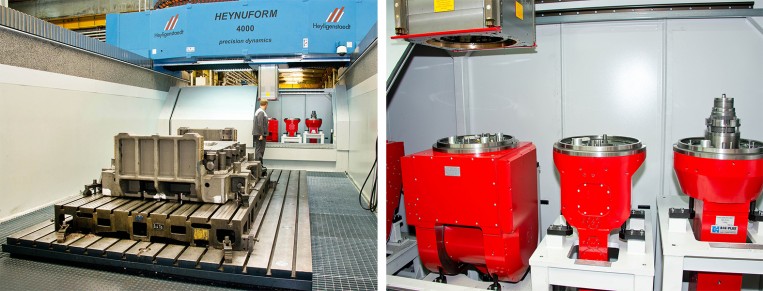
Time to change the milling head? No problem. There is a selection of tools available, and the machine takes what it needs.
“We have several machines in the central workshops that can automatically change tools, but the Heynuform tops everything.”
– Thomas Schäufle –
Responsible for Controlling and Programming
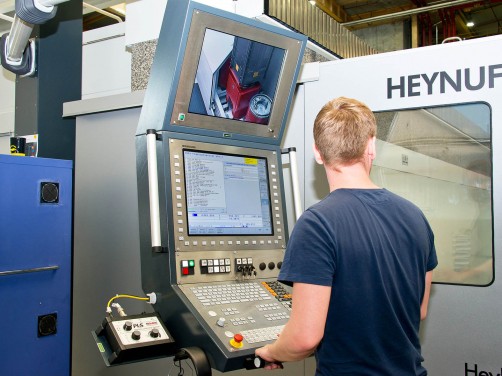
How are things? You might be able to see every detail on the display, but sometimes it makes sense to peer through the window.
The Heynuform is capable of milling pressing tools for especially large shell components. Yet, it can also manufacture components with left- and right-side components, like a door, that are pressed together at the same time. It not only means that we process orders more quickly, “we can meet the increasing need of our other pressing plants in Europe to manufacture more and more double parts,” explains Knut Mittendorf, who is responsible for new technologies used in the central workshops. “When you can manufacture two components in one pressing machine, it increases productivity, and it saves space.”
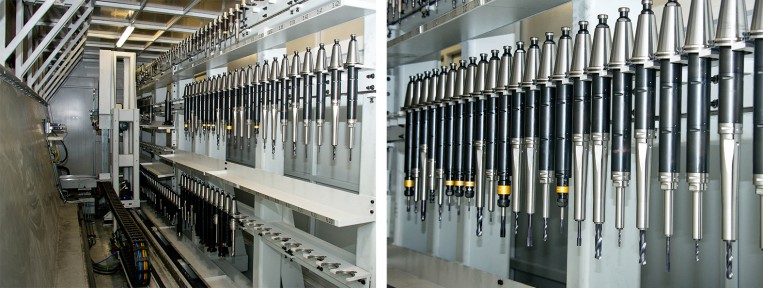
In rank and file: Nearly 200 tools await use and can be changed automatically.
Weighing in at nearly 40 metric tons, the Heynuform’s crossmember, where the machining head is situated, is movable. Heyligenstädt, the manufacturer of this innovative product, developed it for Opel. There are two monolithic slabs of granite on the left and right of the housing, ensuring stability. Each measures 12 meters in length and weighs 20 metric tons.
WITHOUT PRODUCING VIBRATION
“The machinery needs to be able to operate without producing vibration in order to ensure precision within thousands of a millimeter,” explains Andreas Henke, head of Central Functions in the central workshops. “Plus, we’ve seen that granite has better thermal conductivity than concrete. Our milling facility cannot become excessively hot.”
The party is over: The machining head returns the measuring sensor to the magazine, automatically.
“When you can manufacture the left- and right-side components in one pressing machine, it increases productivity, and it saves space. Plus, we can meet the current trend in our pressing plants.”
– Knut Mittendorf –
Responsible for New Technologies
in the central workshops
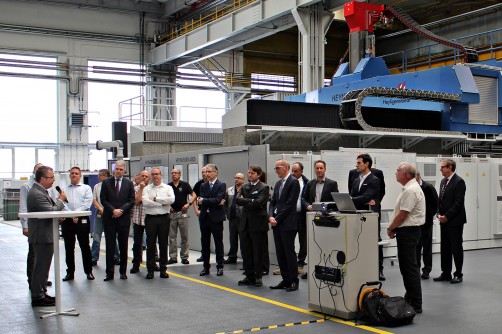
Small inauguration ceremony: The central workshops show off their newest feat to Opel’s management.
The new milling facility was also presented to Opel’s management, which was a matter of pride for the central workshops. “We see it as a commitment to pressing tool engineering at our company that the management decided to invest in these facilities,” proudly states Andreas Henke. He adds that, “It makes complete sense, too. Now we can better network the simulation experts over in Development with our pressing plants spread around Europe, all the while manufacturing pressing tools faster than ever before, with more precision than ever before.”
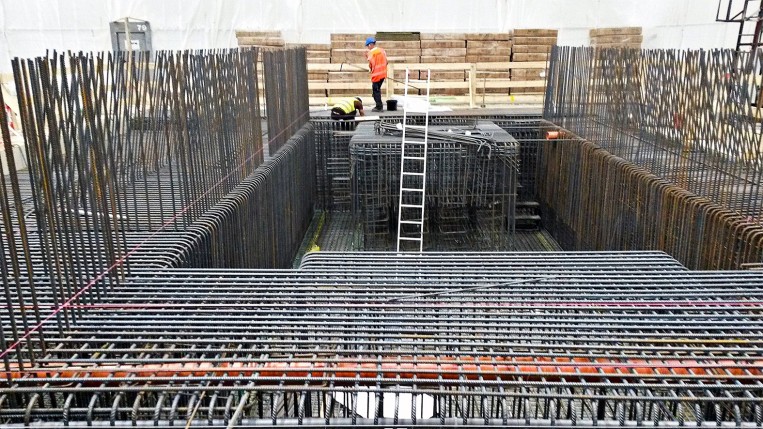
The facility needs to have a secure foundation to operate without producing vibration. The ditch that had to be dug for Heynuform was four meters deep. It was filled with 510 cubic meters of concrete and 70 metric tons of steel. The foundation for its ‘twin,’ which arrives in October, was dug at the same time.