Wie verkehrt man einen Engpass in sein Gegenteil? Das Team des Productivity Workshops „F 17-Hauptwelle“ hat es vorgezeigt.
„Das Ziel war, Störungen an den Engpässen zu verringern und dadurch die Uptime zu verbessern“, schickt Andreas Salomon/Kaizen-Teamleiter, der den Productivity Workshop moderierte, voraus. „Wir wollten durchschnittlich 110 Stück pro Stunde erreichen.“
Von 91 auf 117 Stück pro Stunde gesteigert
Doch das ursprüngliche Ziel wurde bei weitem übertroffen: Eine der beiden Engpassmaschinen, auf der bei der Weichbearbeitung unter anderem die Tieflochbohrung gefertigt wird, konnte sogar auf eine Ausbringung von 117 Stück pro Stunde gebracht werden.
Zum Vergleich: Die Ausgangswerte betrugen 91 Stück pro Stunde im Weichbearbeitungsbereich, 100 Stück pro Stunde im Hartbearbeitungsbereich.
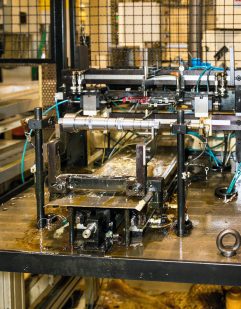
Messstation für die Hauptwelle.
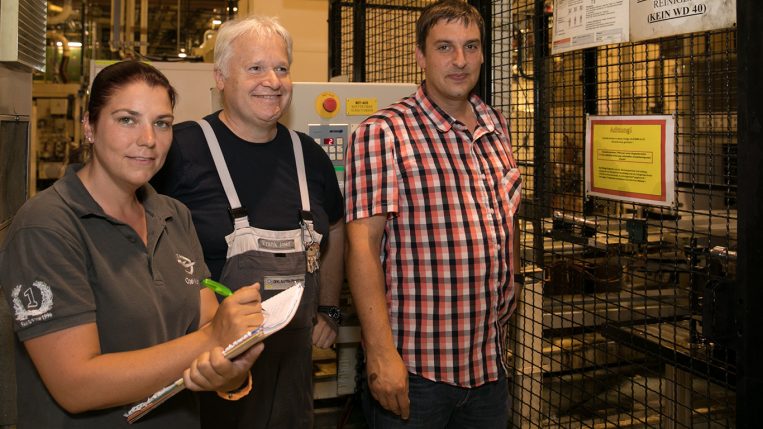
Karin Kalchbauer, Josef Frank und Ronald Wührer (v.l.n.r.) analysieren die Hauptwellen-Messstation.
Wie wurde das phänomenale Ergebnis erreicht?
„Wir haben den Workshop sehr intensiv geplant“, sagt Andreas Salomon. „Die sehr gute Zusammenarbeit mit dem Bereich und mit dem Simulationsteam aus Rüsselsheim halfen dabei. Außerdem haben wir bereits jahrelange Erfahrungen mit Productivity Workshops.“
So funktioniert ein derartiger Workshop: Methodische Anleitungen (theoretisch und praktisch, am ersten Tag) werden an drei Folgetagen in den Linien umgesetzt. D.h. einzelne Stationen werden bis ins letzte Detail analysiert und die Erkenntnisse daraus in Simulationsberechnungen widergespiegelt. Am fünften Tag findet die Ergebnispräsentation vor dem Management statt.
„Die gesamte Hauptwellen-Linie – insgesamt 32 Anlagen – wurde mithilfe von Simulation untersucht. Zwei Engpassmaschinen wurden definiert; eine im Weichbereich, eine im Hartbereich“, berichtet der Kaizen-Spezialist. „Am Ende stand fest: 36 Ideen wurden generiert. Jetzt kommt es darauf an diese auch nach Möglichkeit umzusetzen.“ Dazu wird es in regelmäßigen Abständen Reviews geben, um den Status der Verbesserungen zu überprüfen.
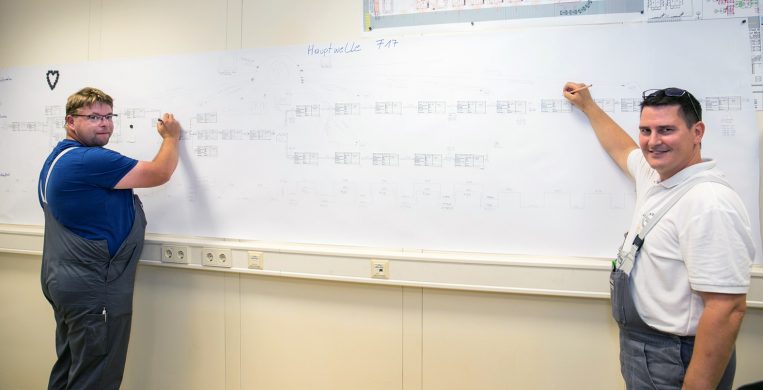
Oliver Rieger (l.) und Gerald Poppinger zeichnen den Wertstrom.
Spezialisten sind gefragt
Als wesentliches Erfolgsgeheimnis bezeichnet Andreas Salomon das Zusammenspiel der Spezialisten im Bereich. „Ohne die jahrelangen Erfahrungen der Mitarbeiter in der Linie, das Know-how der Instandhaltung, den Einsatz der Planung und die Koordination durch den Workshop-Leiter – in diesem Fall Thomas Aininger – ist es nicht möglich solche Ergebnisse zu erzielen. Nur als gemeinsames Team, in dem jeder seinen Beitrag leistet, kann man so effektiv arbeiten.“
Für den Engpass im Hartbearbeitungsbereich (hier erfolgen Schleifarbeiten) sind ähnliche Maßnahmen vorgesehen. An den zugehörigen Analysen wurde Anfang Juli noch gearbeitet.
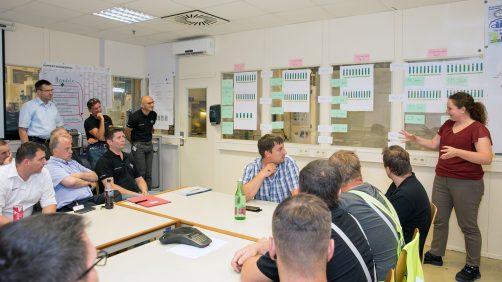
Was Marina Hettich (ganz r., stehend) von den Simultionsdaten zu erzählen hat, interessiert sichtlich (v.l.n.r.): sitzend: Rafal Trojca/Stellvertretender Werksdirektor, Generaldirektor Paul Staes, Michael Salomon/Fertigungsleiter Getriebebau, dahinter stehend: Oliver Räbiger, Andreas Salomon, Hans-Jörg Frommknecht/Fertigungsleiter Motorbau, am Tisch sitzend: Ronald Wührer/Planung.
Uptime-Projekt F 17-Hauptwelle
Productivity Workshop von 26. bis 30. Juni 2017
Die Teilnehmer: Workshop-Leiter Thomas Aininger/Produktionsmeister F 17-Räderfertigung, Planer Ronald Würrer, Johann Koller/Teamsprecher, Josef Frank/Teamsprecher, Karin Kalchbauer/Zylinderkopf-Fertigung, Javad Mohseni/F 17-Getriebebau, Jürgen Wolf/F 17-Getriebebau, Peter Brzobohaty/Material Handling, Oliver Rieger/Kaizen-Team, Florian Schieb/Kaizen-Team, Daniel Esser/Kaizen-Team, Peter Zandt/Kaizen-Team, Oliver Räbiger/Simulations-Team, Marinia Hettich/Simulations-Team
Die Ergebnisse: 35 Ideen; Steigerung der Weichbearbeitung-Uptime auf 117 Stück pro Stunde.