Die deutsche Ingenieurskunst, sie ist gerade in der Automobilbranche begehrt und ein Gütesiegel. Bestes Beispiel dafür ist der Insignia, entwickelt und produziert im Stammwerk, ein ausgezeichnetes Fahrzeug „Made in Rüsselsheim“. „Bemerkenswert ist zudem die Tatsache“, sagt Stefan G. Weitzel, Manager im Einkauf, „dass in unserem Flaggschiff jede Menge Europa steckt, genau genommen sind es Bauteile aus insgesamt 19 Ländern.“
Jedes Fahrzeug besteht aus rund 3000 teilen
Luftansaugung aus Schweden, Scheinwerfer aus Slowenien, Tankfüllung aus Portugal – Weitzel kennt die Beschaffenheit des Insignia bis ins kleinste Detail. Er koordiniert die Zusammenarbeit zwischen der Fahrzeugplattform, also der technischen Basis eines Modells, und den Zulieferern, die Opel mit den erforderlichen Komponenten versorgen. Ein ereignisreicher Job, der alle Phasen des Entwicklungsprozesses und der Serienfertigung abdeckt. Immerhin geht es nicht nur um etliche Zulieferländer, sondern um rund 3000 Neuteile, aus denen jedes einzelne Fahrzeug besteht.
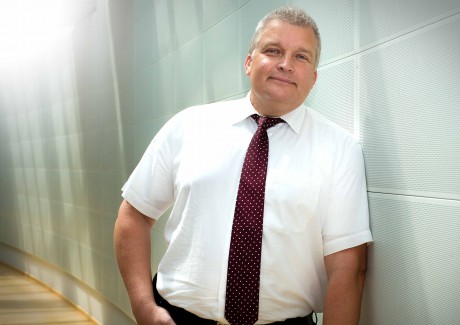
Stefan G. Weitzel koordiniert die Zusammenarbeit zwischen der Fahrzeugplattform, also der technischen Basis eines Modells, und den Zulieferern.
„Tech Reviews“ bei den Lieferanten vor Ort
Weitzels Arbeit beginnt bereits, während die Bereiche Design und Entwicklung das Konzept für ein neues Modell erarbeiten. Die Akteure legen fest, welche Spezifikationen ein bestimmtes Bauteil haben muss. Dann gilt es, bereits in einer frühen Projektphase die Kooperation mit strategischen Lieferanten zu ermöglichen. Das ist Weitzels Aufgabe. Er steuert die Beschaffungsvorgänge, um die Nominierung eines Lieferanten zum richtigen Zeitpunkt sicherzustellen. „Im Vordergrund stehen immer Qualität, Technologie, Service und Preis“, sagt er. Bevor es zu einem Vertrag mit einem Zulieferer kommt, machen die Opel-Einkäufer gemeinsam mit den Ingenieuren „Tech Reviews“: Prüfungen, in denen es darum geht, ob der Dienstleister alle geforderten Kriterien erfüllt.
Das Lenkrad ist fertig, die Auspuffanlage noch nicht
Doch wie funktioniert der Einkauf, wenn das Bauteil Tausende Kilometer entfernt zu bekommen ist, aber pünktlich benötigt wird? „Die Supply Chain, also die Beschaffungskette, ist ein entscheidendes Detail im Automobilbau“, sagt Weitzel und verweist auf die Logistik-Planung, die unterschiedliche Ansätze verfolgt. Die Insignia-Türverkleidung zum Beispiel wird in der Tschechischen Republik gefertigt und dann in den gewünschten verschiedenen Varianten direkt ins Werk geliefert – und das in Einbausequenz (Long Range SILS). Die Auspuffanlagen hingegen, ob aus Polen oder Österreich, werden erst im Werk zusammengefügt. Das ist mit Blick auf die Produktionskosten zwar aufwendiger, aber angesichts deutlich geringerer Verpackungs- und Transportkosten die insgesamt bessere Lösung.
Es zählt mehr als nur der bestmögliche Preis
Die Erkenntnisse aus der für das laufende Modell aufgebauten Logistikkette leisten einen entscheidenden Beitrag für die Strategie der nächsten Fahrzeuggeneration. „Sich verändernde Rahmenbedingungen und Optimierungspotenziale werden dabei berücksichtigt und führen wieder zu Veränderungen“, erklärt Weitzel. Über die multinationale Einkaufstour für den Insignia sagt er: „Wesentlich für den wirtschaftlichen Erfolg ist es, nicht nur die Teile selbst in optimaler Qualität zu besten Preisen einzukaufen, sondern auch die Kosten für Verpackung, Transport, Lagerhaltung und Sequenzierung im Griff zu haben.“
SILS (supply in line sequence) sind Bauteile, die der Zulieferer in der Reihenfolge herstellt und zustellt, wie sie in der Opel-Fertigung montiert werden.
Long Range SILS (LRS) werden über weite Entfernungen aus ganz Europa in Sequenz zugeliefert. Opel plant und organisiert den Transport. Sie erreichen das Werk in der Reihenfolge, wie sie eingebaut werden.
LRS-Teile werden von einem Dienstleister vom Wareneingang bis zur Fertigungslinie transportiert.
Beispiel Kabelsätze: Jedes Fahrzeug erhält einen individuellen Kabelsatz. Nach den in optimaler Reihenfolge geplanten Aufträgen werden sie gebaut und in ebendieser Reihenfolge ins Werk und an die Linie gebracht.