Kiedy Arkadiusz Bober, kierujący Działem Inżynierii Produkcyjnej oprowadza po dziale Karoserii, w jego głosie czuć satysfakcję.
– Mogę powiedzieć, że to, co dokonało się tutaj w czasie letniego zamknięcia (shut-down), to prawdziwa rewolucja – opowiada. – Zmiany jakie zaszły są największe spośród tych, jakie miały miejsce w ostatnich 10 latach.
Rzut oka na linię główną i już pierwszy ślad modernizacji – nowiutkie roboty zgrzewające karoserię w akcji. Wymieniono ich aż 30.
– Pozwolą one na jeszcze bardziej niezawodną i precyzyjną pracę – tłumaczy Arkadiusz Bober. – Przy okazji zmieniliśmy położenie 18 innych robotów i wielu stanowisk produkcyjnych. Zrobiliśmy też miejsce na nowe.
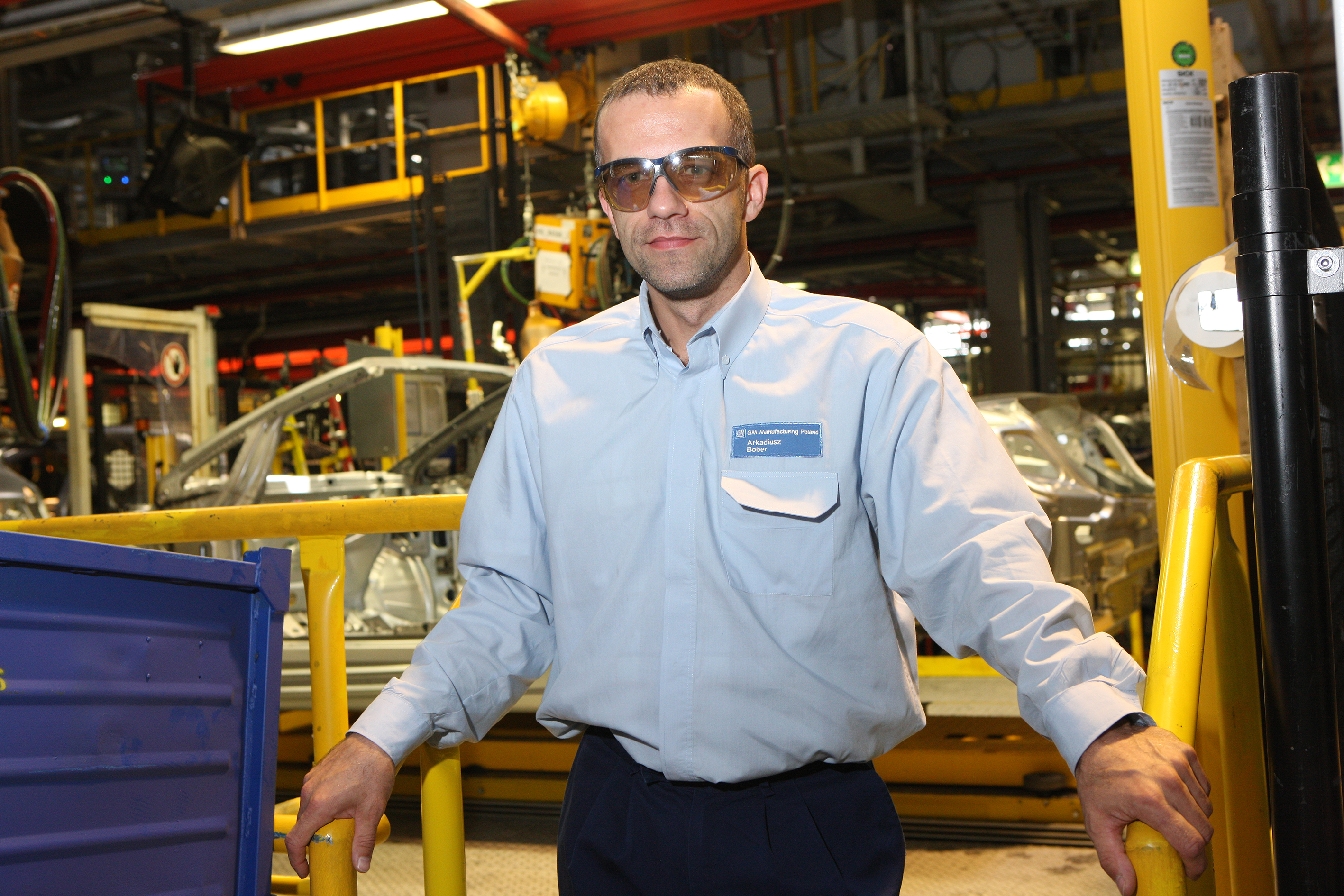
Arkadiusz Boberek z dumą opowiada o zmianach.
Ale to wcale nie koniec nowinek. Kolejną jest metamorfoza linii do wzmacniania podwozia wraz z komorą silnika (Framing 1 Respot). Cała została rozmontowana i nową postawiono zupełnie od zera. Jest w pełni zautomatyzowana. Także we wcześniejszym etapie procesu – na linii Framing 1 Tack – został dołożony robot nakładający klej na karoserię. Poza tym wymieniono jednostki trzymające karoserię w poszczególnych procesach (tzw. underbody clamping). Framing 2 może z kolei pochwalić się zupełnie nowym, zrobotyzowanym montażem nadkola. To innowacja w fabryce.
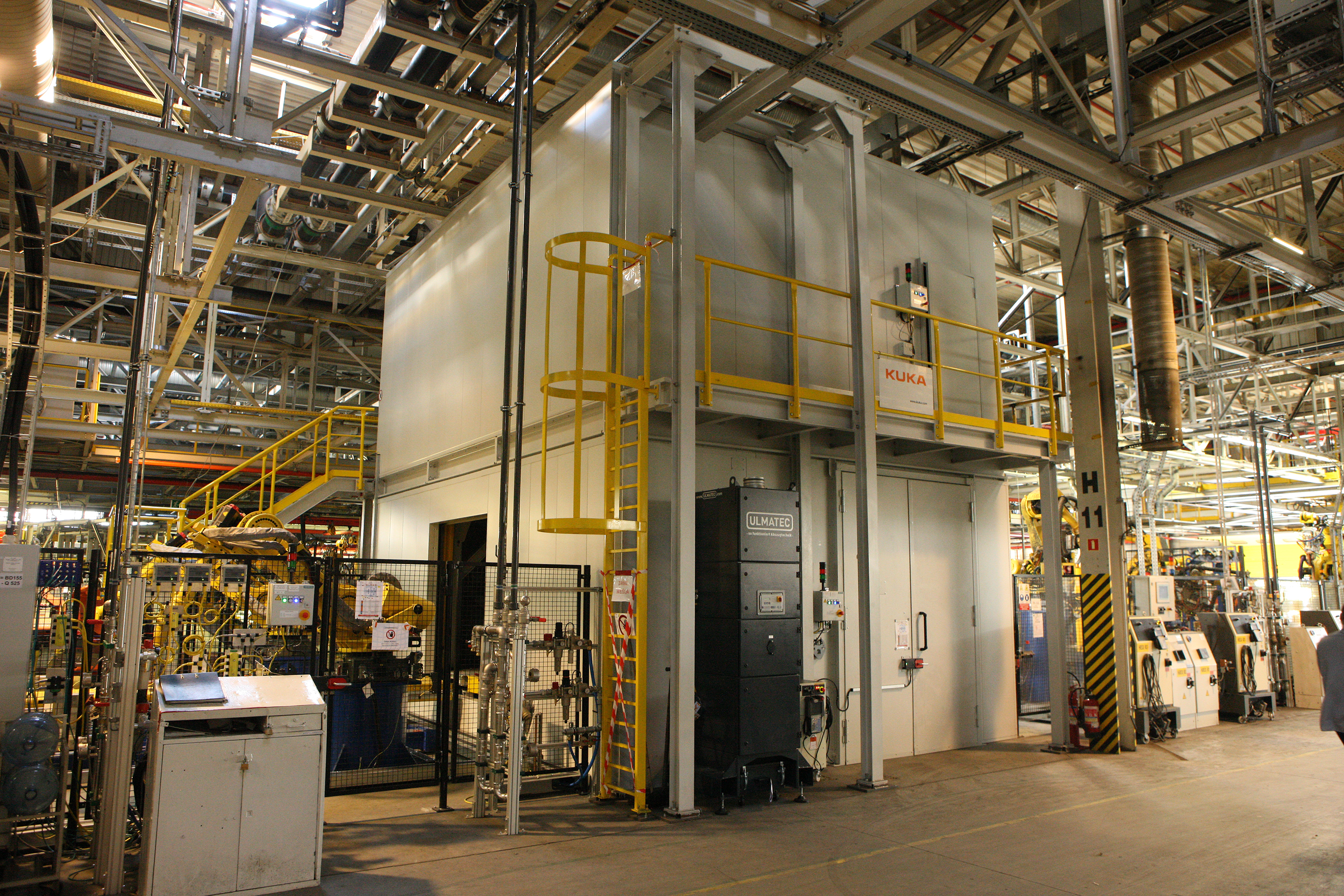
Nowość – kabina do laserowego spawania dachu.
– Kluczową inwestycją jest jednak to miejsce – Arkadiusz Bober pokazuje ogromny, tajemniczy, szary obiekt stojący w hali. – To kabina, w której znajdzie się główne stanowisko laserowego spawania dachu. Laserowe spawanie gwarantuje wyjątkową wizualną jakość powierzchni łączonej, ale ze względów bezpieczeństwa musi znajdować się właśnie w takiej komorze.
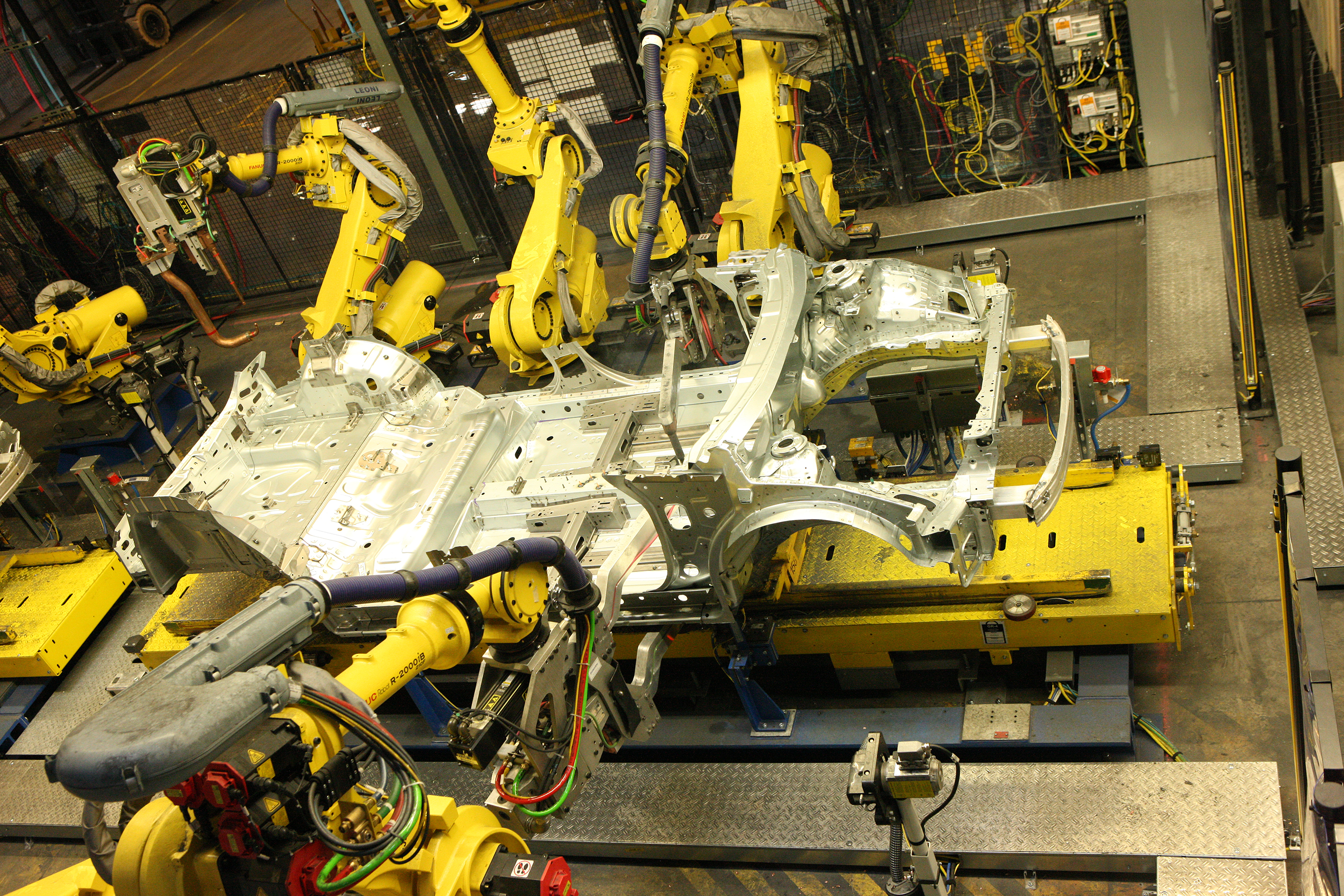
Zmiany zostały wprowadzone błyskawicznie.
Aż trudno uwierzyć, że większość tych przemeblowań dokonała się w ciągu zaledwie trzech tygodni letniej przerwy. Ekipy pracowały całą dobę, by postawić nowe elementy, a przy okazji sprzątnąć pozostałości po linii pracującej dla Astry III.
Przy tak wymagającej operacji wręcz zadziwiające jest to, że dało się zdążyć ze wznowieniem bieżącej produkcji bez żadnych poślizgów.
– Ogromną część prac mamy już za sobą – zapewnia Arkadiusz Bober. – Jednocześnie jednak wiele pozostaje jeszcze do zrobienia.
Inne wydziały po metamorfozie
W Tłoczni zmodernizowano tzw. trzecią linię, a konkretnie system sterowania nią. Odpowiada on za jakość tłoczenia paneli (ścian zewnętrznych i drzwi zewnętrznych). –Zastosowaliśmy nowa technologię – tłumaczy Krzysztof Roczek, inżynier automatyk. – Przenieśliśmy wizualizację z panela operatorskiego bezośrednio na serwer i czterech tzw. klientów, czyli komputery przemysłowe. To daje większą stabilnośc pracy. Linia już funkcjonuje w oparciu o ten system, choć trwają prace „dopieszczające”.
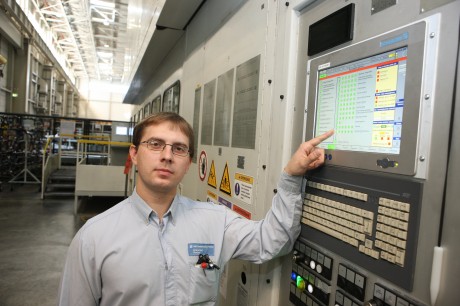
Technologia zastosowana przy wizualizacji procesów jest o wiele praktyczniejsza.
Marek Biskup z działu ME tłoczni dodaje, że poważną inwestycją jest też budowa nowego budynku. Powstaje on na wysokości warsztatu utrzymania ruchu matrycy, obok samej tłoczni, od strony lakierni. – Znajdzie się w nim, m.in. nowa obracarka do wykrojów – wyjaśnia. – Pozwoli to ograniczyć liczbę matryc na linii cięcia A. W budynku zmieszczą się też maszyny pomiarowe w specjalnie stworzonym obszarze jakości. Odbiór budynku planowany jest w styczniu, a prace już trwają.
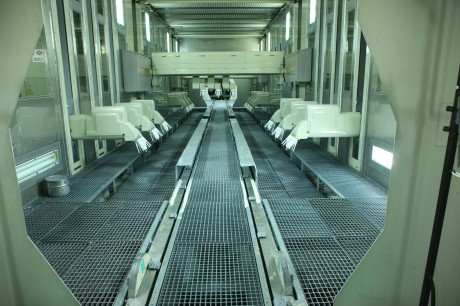
W lakierni zasadnicze zmiany zaszły w częście, gdzie nakładany jest tzw. primer.
Szymon Liczberski, kierownik działu ME w lakierni (Paint) opowiada z kolei o modyfikacji maszyn lakierniczych pod kątem efektywniejszej pracy przy nakładaniu bazy (primera). – Dzięki wyeliminowaniu płukania pomiędzy zmianami kolorów, zwiększyliśmy płynność nie tylko u siebie, ale i nie będziemy jej zaburzać na GA. Karoserie będą układane pod sekwencję koloru. Modyfikujemy też linię fosforanowania.
Michał Mazur, z Inżynierii Produkcji, odpowiedzialny za przenośniki i automatykę pokazuje rozbudowane już BDC (Body Distribution Center). – Powstał tu zupełnie nowy obiekt – wyjaśnia. – Rozmiarowo jest identyczny z dwoma pozostałymi, ale udało się nam jeszcze efektywniej wykorzystać przestrzeń.
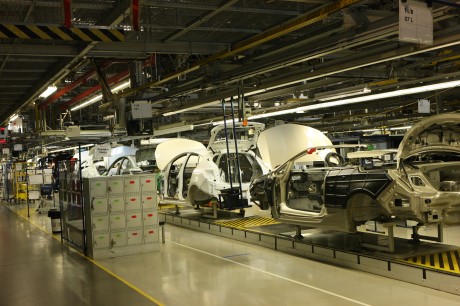
Część DVT zostanie przygotowana do wprowadzanie systemu GTS.
Marcin Kozub, kierownik ME na wydziale Montażu GA zaznacza, że w części, za którą odpowiada, zmiany dokonały się lub dokonają wkrótce w każdym obszarze linii produkcyjnej. – Największą ciekawostką jest chyba to, co zmieni się na linii trimowej – opowiada. – Modyfikacji zostanie poddana część, na której do samochodu wkłądany jest akumulator. Będzie on umieszczany za siedzeniem pojazdu. Dotąd montowanie akumulatora odbywało się na linii chassis. Także w części trimowej zainstalowana zostanie maszyna do nabijania numeru VIN. Obecnie robi się to na w. Karoserii. – Do tego dochodzą kolejne zmiany, jak choćby adaptacja zawieszek kokpitu – dodaje Marcin Kozub. – No i na linii chassis mamy zmianę miejsca umieszczania układu wydechowego. Na Chassis będą też testowane pasy bezpieczeńśwa i przeprowadzona zostanie adaptacja palet. Przełomem będzie instalowanie w pojazdach nowego systemu GTS (Global Test Systems). Wiązało się to z koniecznościa zmian na DVT.
Kilka liczb, które najlepiej obrazują zmiany:
• 620 metrów kwadratowych liczyć sobie będzie powstający budynek na potrzeby tłoczni
• 20 proc. – o tyle spadło zużycie rozpuszczalnika dzięki zmianom w lakierni. A to wyniki dopiero z fazy testowej!
• 99,5 proc. – przez tyle czasu na każdej zmianie musi działać bezawaryjnie system urządzeń w nowym pomieszczeniu BDC, co oznacza maksymalnie 2 minuty przrwy na 8h!
• 12 sekund – o tyle (ze 102 sekund do 90) skrócił się czas cyklu układnic w BDC dzięki zmianom