The lettering “HYDROGEN” gives it away: these are no ordinary Opel Vivaro-e parked in front of M55 on the Rüsselsheim factory premises – they are small electricity power plants on wheels. The electricity that powers the vans is not stored in large batteries either. Instead, it is generated during the journey, which is why there are three hydrogen tanks on board (in the underbody) and a fuel cell (under the bonnet). An externally rechargeable battery is also part of the system. Fuel cell drive plus charging option via the plug socket – is Opel reinventing the plug-in hybrid? We are curious.
During a test drive with Dr Lars Peter Thiesen we want to learn more about the alternative electric drive à la Opel. And the head of the hydrogen and fuel cell introduction strategy is in high spirits as he takes his seat behind the steering wheel. No wonder, ever since he joined the company in 1998, he has been working towards this goal. “With the Vivaro-e HYDROGEN, we are the first manufacturer to put a hydrogen LCV on the road – a milestone!” he says.
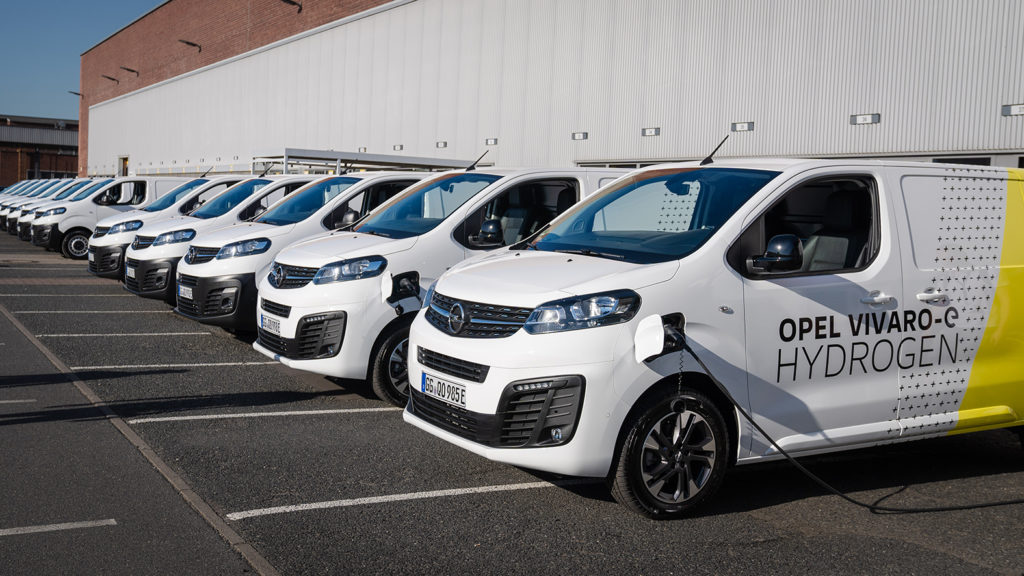
“With the Vivaro-e HYDROGEN, we are the first manufacturer to put a hydrogen LCV on the road – a milestone!”
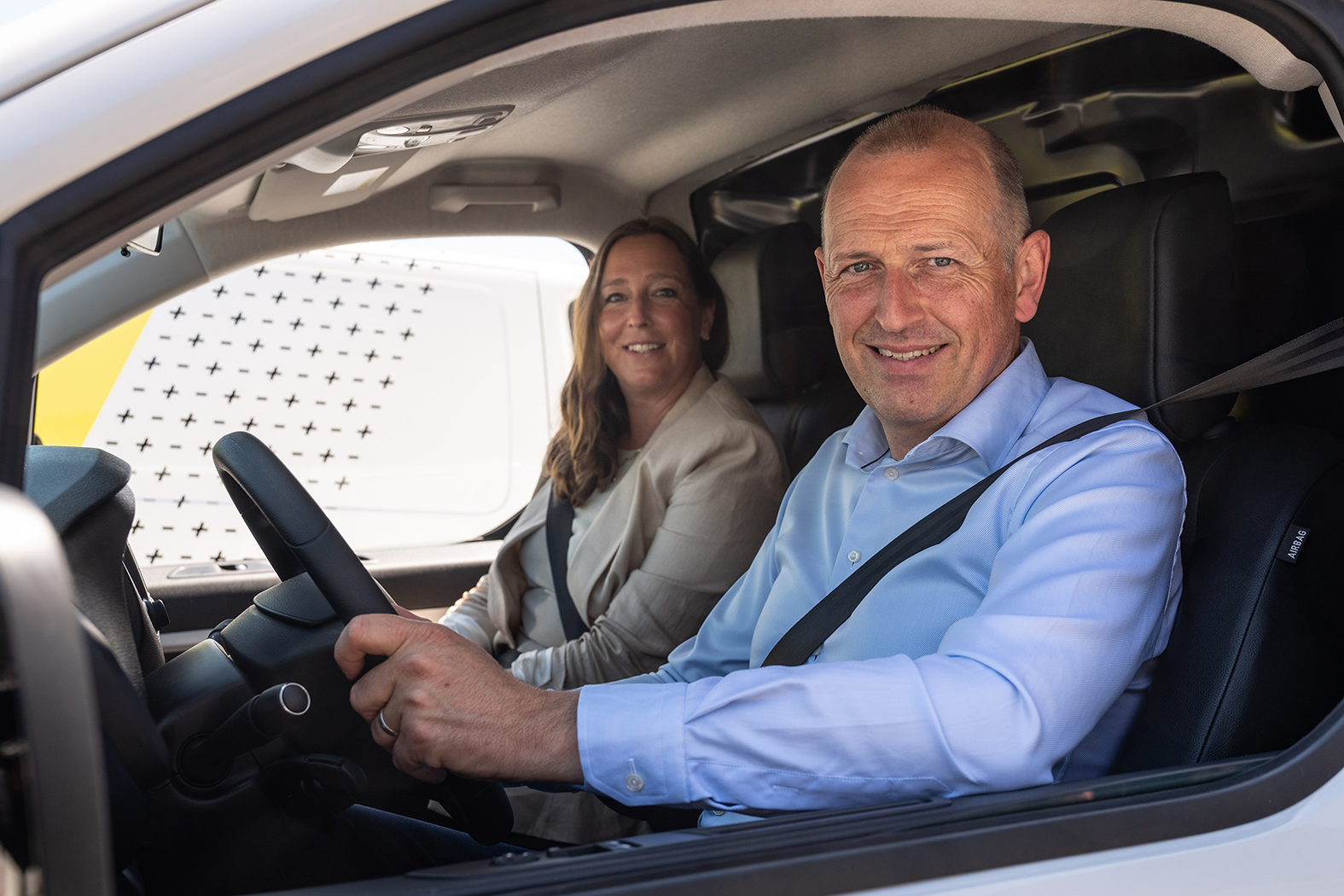
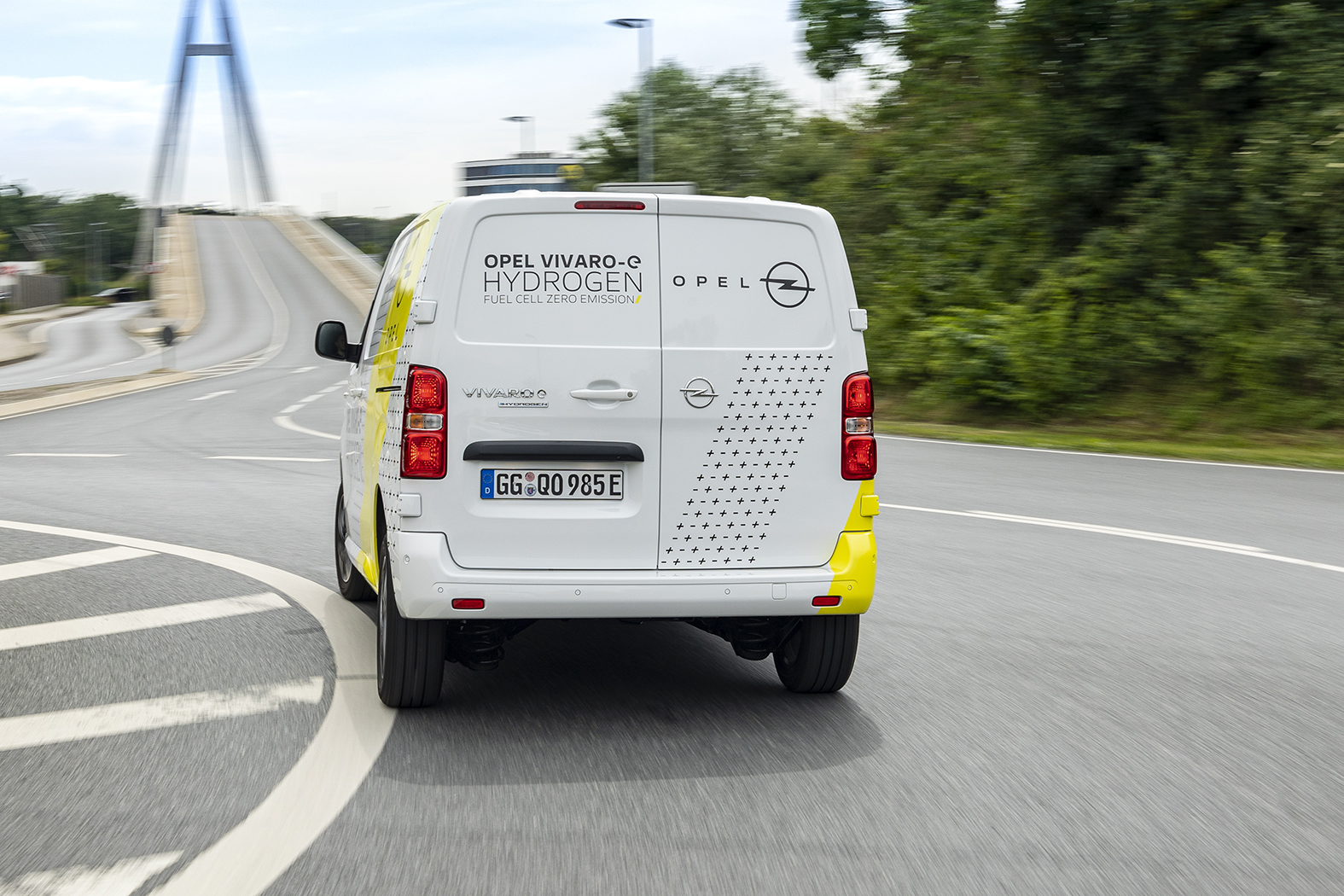
The power plant moves off silently. Thiesen explains the interaction between the fuel cell and the battery unseen. Hydrogen is fed from the tanks towards the fuel cell, reducing the pressure from 700 to about 1 to 2 bar. In the meantime, the battery under the front seats takes care of moving the van for the first few metres; it also provides support during peak loads, for example when accelerating. Thus, the combined plug-in fuel cell approach not only provides more power, the fuel cell can also always be operated under optimal conditions. “This offers advantages in terms of service life,” says Thiesen. “And hybridisation also means we can recover braking energy.” But the biggest plus, he says, is the clever packaging that the mid-power concept makes possible.
Nothing but dynamic gliding
The bodywork, for example, is unchanged. “The cargo capacity of up to 6.1 cubic metres remains the same, as do the one-tonne-payload and towing capacity- essential parameters for a van,” says Thiesen. Last but not least, the battery provides an extra 50 kilometres of range. A soft whirring starts. “The compressor is starting up,” Thiesen comments. We learn that the compressor is now supplying outside air to the fuel cells. The chemical reaction with the hydrogen that generates the electricity starts. And the transporter – it just drives. No jerking, no noise. Nothing but quiet, smooth, dynamic gliding. “And the only by-product of the reaction is pure water vapour from the exhaust – so we drive emissions-free.”
“And the only by-product of the reaction is pure water vapour from the exhaust – so we drive emissions-free.”
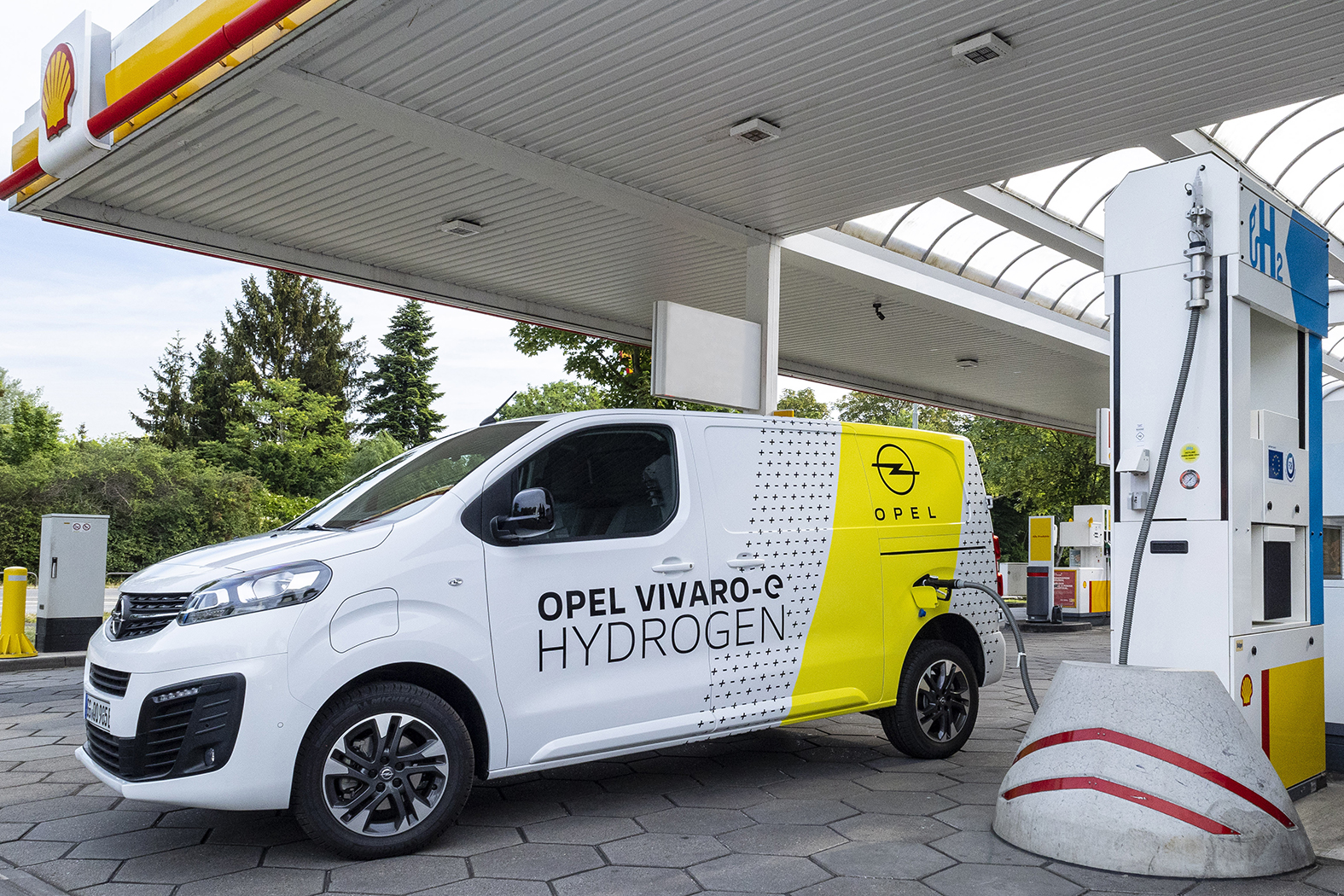
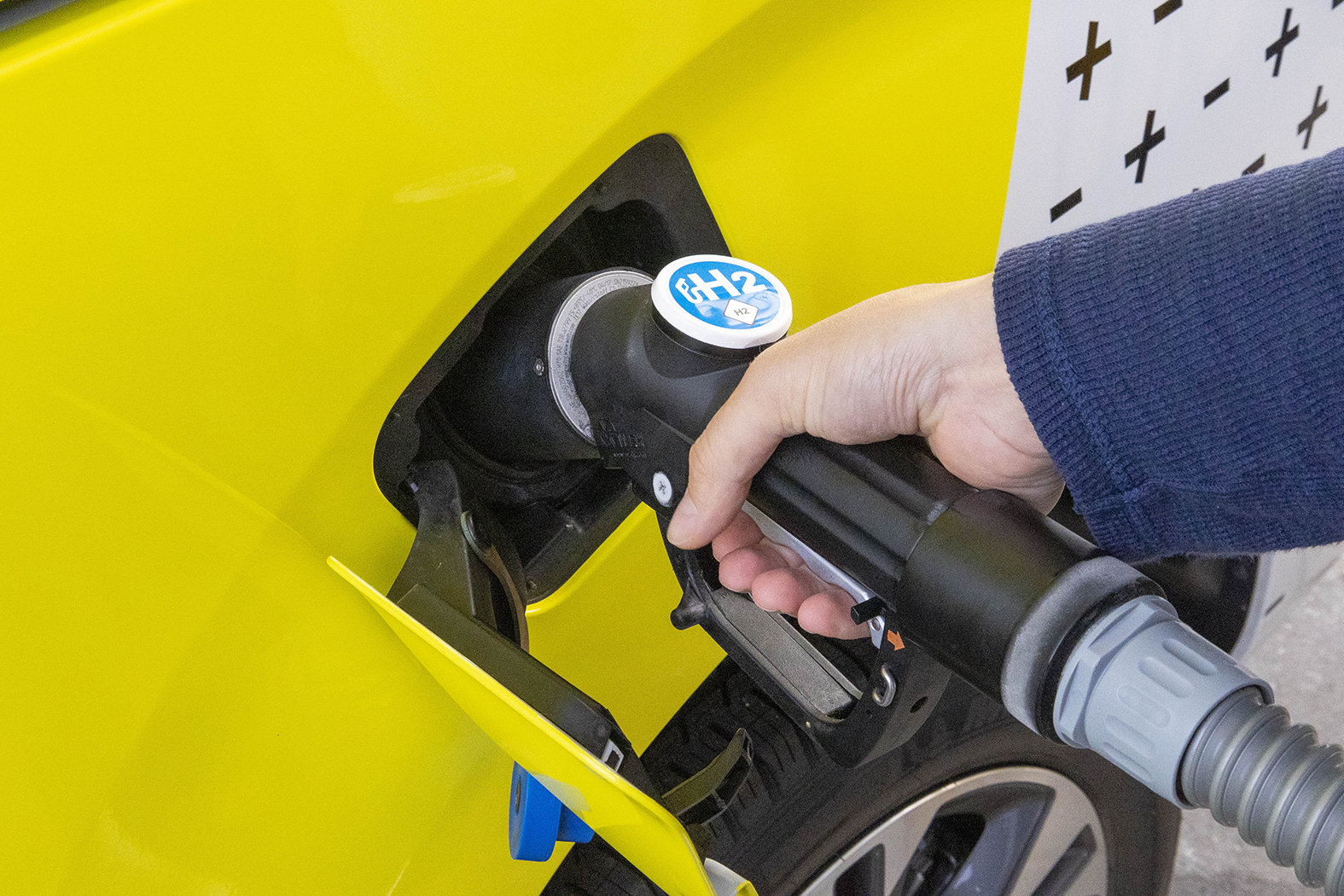
The emissions-free plug-in fuel cell vehicle that Lars Peter Thiesen lets glide along the motorway at a top speed of 110 km/h is the result of decades of hydrogen expertise. For more than 20 years, the company has gathered experience with the “cold combustion” of hydrogen, conducted basic research and set industry standards in the process. Thiesen remembers the first prototype, the HydroGen1, which was at the start of the 2000 Olympic Games in Sydney as a pace car in the marathon, the HydroGen3, which was the first car in the world to have a 700 bar tank system, or the HydroGen4, which six years later proved its suitability for everyday use in the hands of customers in an internationally important market test. “High range, zero emissions, short refuelling stops; the advantages were and are obvious. And we have always remained convinced of the technology.” The biggest problem at the time was the lack of a filling station network. Nobody wanted to build one as long as there were no hydrogen vehicles on the road. But this chicken-and-egg dilemma has been overcome.
Decisive advantage: Quick refuelling
H2 MOBILITY GmbH, a consortium consisting of energy companies and car manufacturers, currently operates 95 hydrogen filling stations in Germany alone, and the number is rising. In the Rhine-Main region, for example, there are two filling stations in Frankfurt, one in Offenbach and one in Wiesbaden. We are currently heading for the latter. After all, a test drive in the Vivaro-e HYDROGEN would not be complete without a demonstration of the decisive advantage of the technology: refuelling within minutes for a long range – in the case of the Opel 400 kilometres according to WLTP.
And it really is quick: open the filler cap, attach the fuelling nozzle, press the green start button, and with a quiet hiss, gaseous hydrogen is pumped into the tank at 700 bar. After three minutes, the refuelling process is complete, confirmed by the hydrogen display in the cockpit – the only detail, by the way, that distinguishes the fuel cell Vivaro from an ordinary Vivaro-e in the interior.
Made in Rüsselsheim
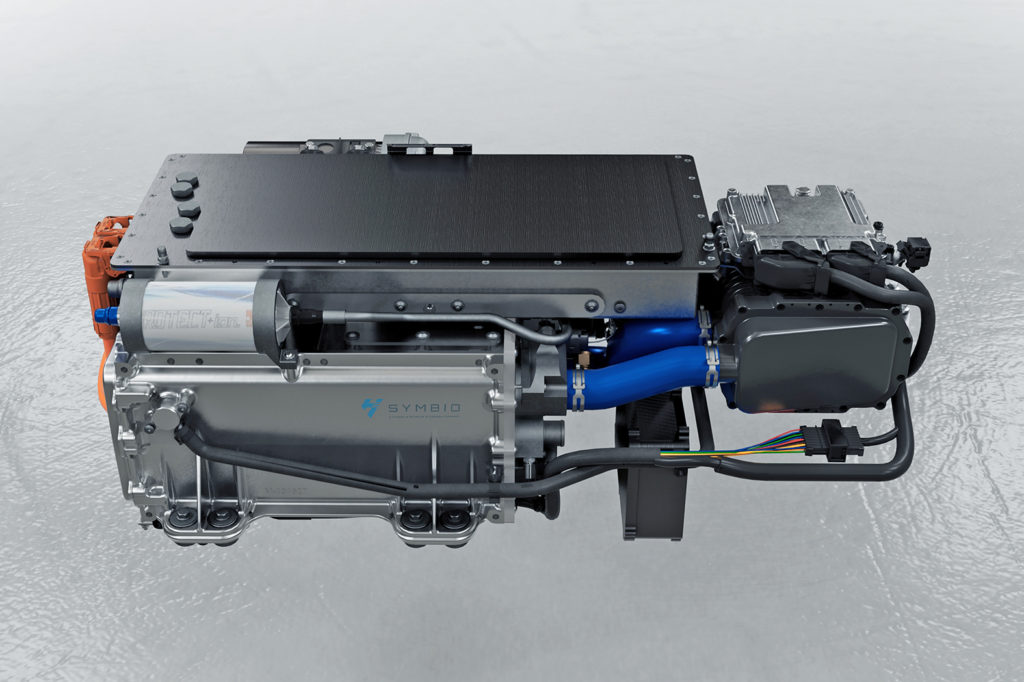
The Opel Vivaro-e HYDROGEN and its Stellantis siblings are manufactured at Opel Special Vehicles (OSV) in Rüsselsheim. In the 1,500 square metre production area with 70 employees, several hundred units of the emission-free van can be produced per year. The Vivaro-e’s traction battery is replaced by three 700-bar hydrogen tanks made of carbon fibre with a combined capacity of 4.4 kilograms. The 45 kW fuel cell drive is so compact that it fits under the bonnet together with the 100 kW/136 hp electric drive. When starting or accelerating, as well as at top speed, the 10.5 kWh lithium-ion battery housed under the front seats assists. It can be charged externally so that the vehicle can cover 50 kilometres purely battery-electrically.
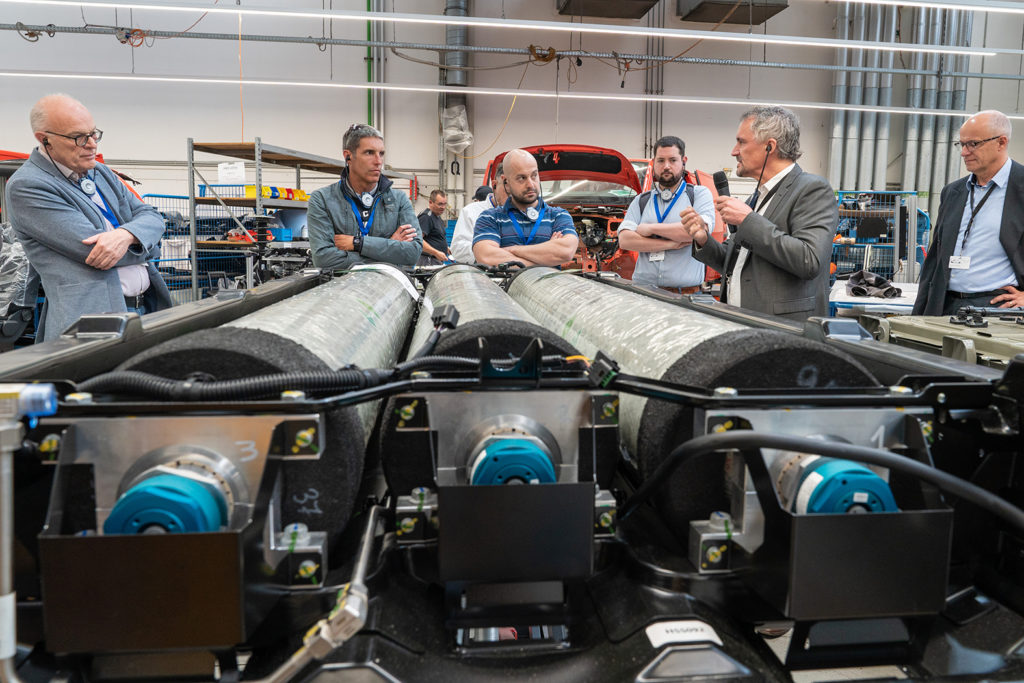
Advantages of the plug-in fuel cell approach: the body structure does not have to be changed and the load volume also remains unchanged. The transporter, which is optionally available in the lengths M and L (4.96 and 5.30 metres), has cargo compartments of 5.3 and 6.1 cubic metres, identical in size to the diesel or battery-electric Vivaro variants.
Production of the Vivaro-e HYDROGEN is currently being ramped up in close cooperation with the suppliers. OSV already supported the engineering department in the development and design of prototypes. This is because the know-how gained in Rüsselsheim will be used for future series production in plants. The Opel parent company Stellantis, for example, has announced that the fuel cell will also be installed in a larger vehicle.
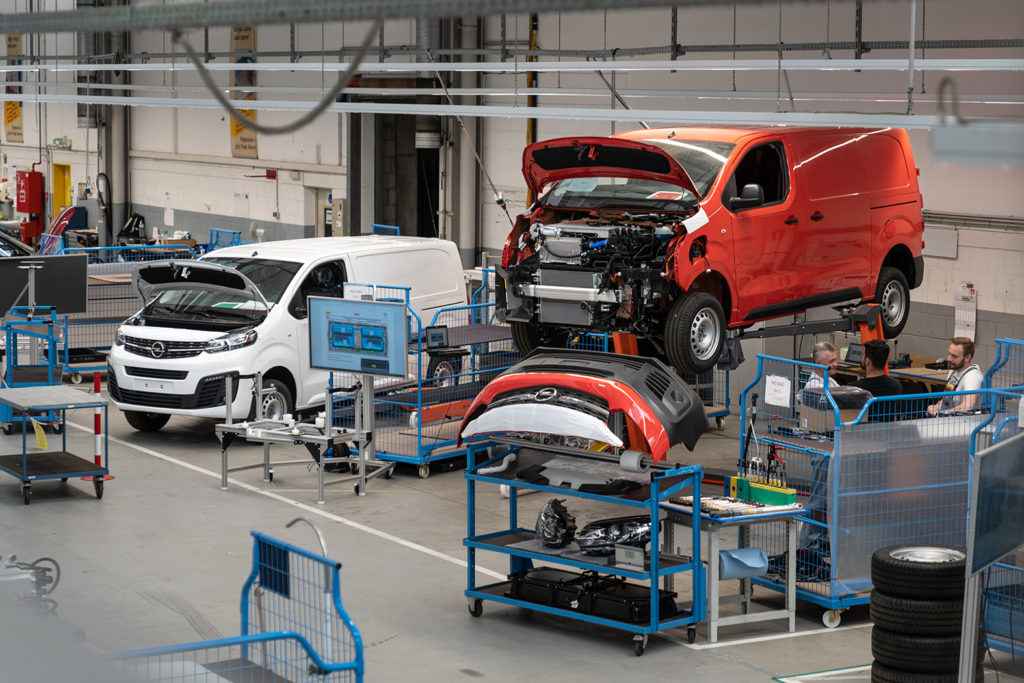
“We always believed in the technology.
It was only a question of time. And now the production version is here.”
Three years ago, the decision was made to develop the Vivaro-e HYDROGEN, Thiesen recounts on the way back to Rüsselsheim. “That was a special moment, we always believed in the technology. It was only a question of time. And now the production version is here,” he says. The German government also sees the potential and has meanwhile created an important funding instrument for the market introduction of commercial vehicles with fuel cells. In addition, hydrogen is an excellent storage medium for electricity from renewable sources, adds Thiesen, pointing to the great importance of hydrogen for the overall energy system of the future.
Contribution to electrification offensive
“The fuel cell does not compete with the battery for vehicle propulsion”, says Thiesen. Each technology can play to its strengths depending on the requirements. “Since range and time savings play a major role, especially for fleet customers and in delivery traffic, we decided to launch the fuel cell drive for light commercial vehicles,” he explains. And the more customers decide in favour of a fuel cell vehicle, the further the costs will be reduced. The household appliance manufacturer Miele is one of the first customers to use the emissions-free Opel van. Service technicians are already using them in the Rhine-Main region. According to Thiesen, the hydrogen fuel cell drive could also be used in additional vehicle classes – “if the market and the hydrogen ecosystem develop as expected”.
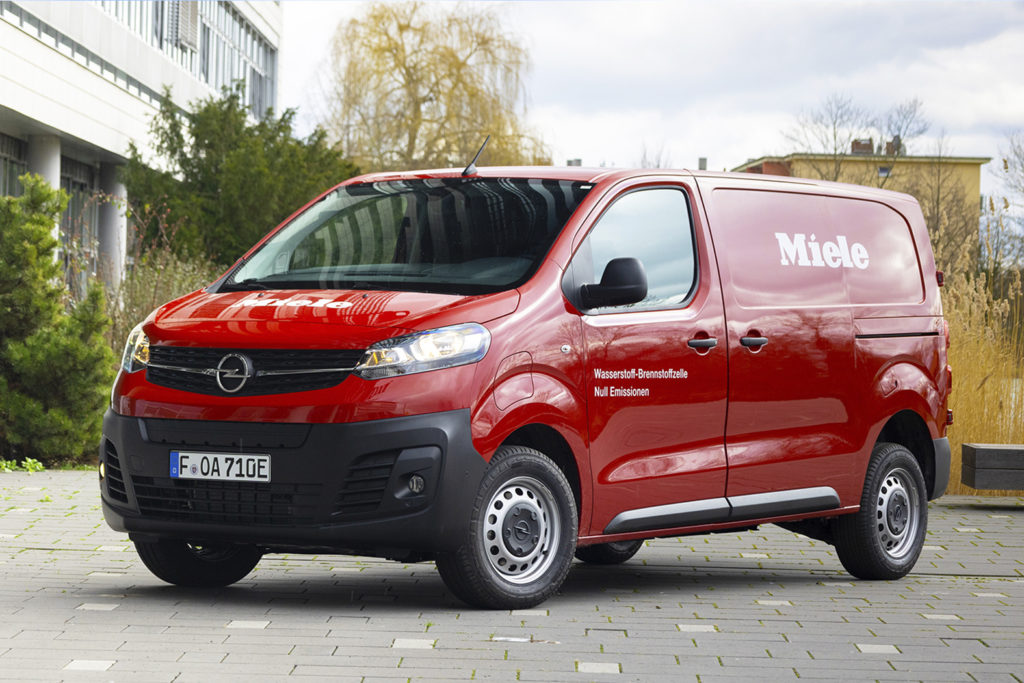
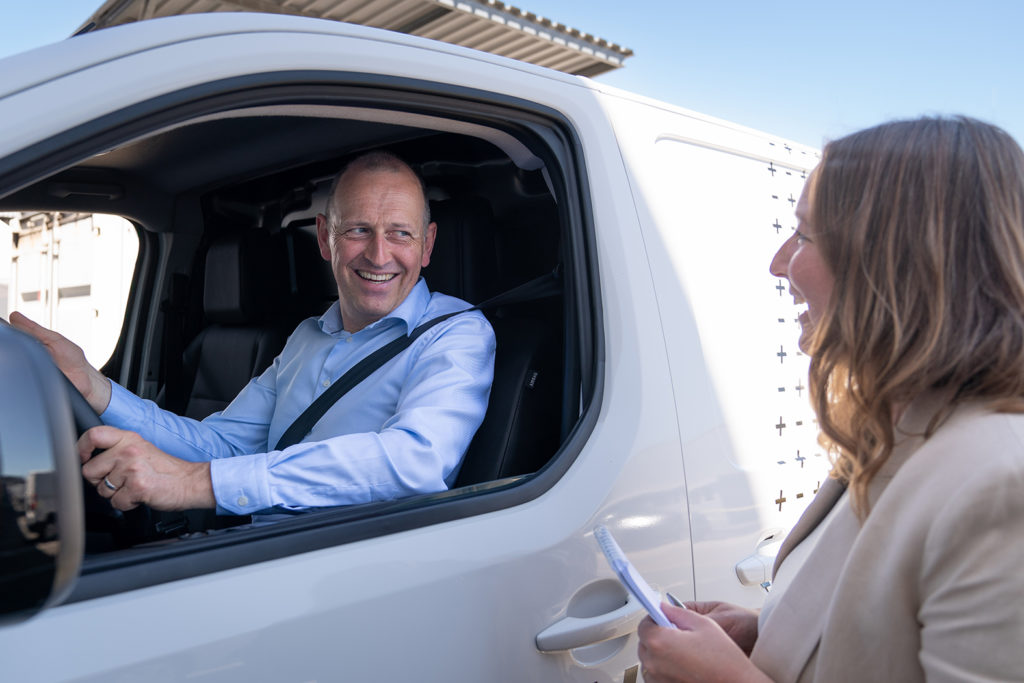
Juni 2022