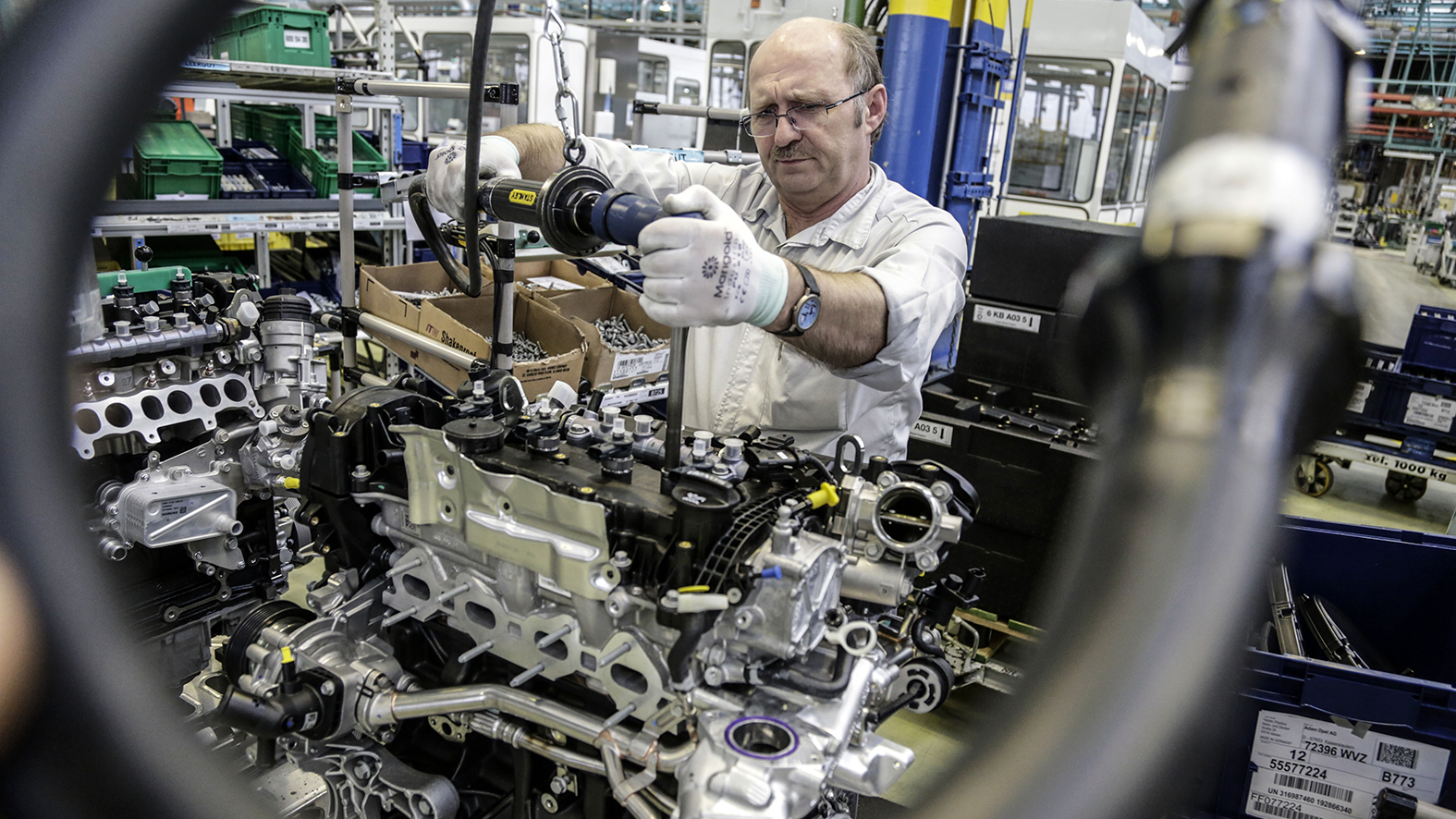
Precision is key: Production employee Günter Rahm takes measure.
The Opel product offensive is in full force – and the engine competence center in Kaiserslautern, Germany is contributing one of the major highlights: the LDE Euro 6, a two-liter diesel engine that is raising the bar in terms of consumption, smooth operation, and comfort in the segment for large-volume engines – naturally, all in compliance with the Euro 6 emissions standard. The staff in Kaiserslautern has a lot to be proud of: Their new drive system is a top-of-the-line product, and they have done exemplary work in integrating this engine into the existing manufacturing system instead of building a new production line, thereby saving the company a small fortune in investment costs.
Kaiserlautern: prominent status, distinguished guests
The Opel plant in Kaiserslautern enjoys a prominent status in the world of GM, and this can be seen in the number of distinguished guests who traveled to the facility to attend the start of regular production (SORP) and wish the team well. Jim DeLuca, Executive Vice President Global Manufacturing, Peter Küspert, Vice President Sales and Aftersales for the Opel Group, Christian Müller, Vice President GM Powertrain Engineering Europe, and Marc Schiff, Executive Director Manufacturing, attended alongside numerous employees from the Quality and ME units of the Powertrain department in Rüsselsheim and employees from the development center in Turin, who have been working closely with their fellow workers in Kaiserslautern over this past year to launch the new drive system.
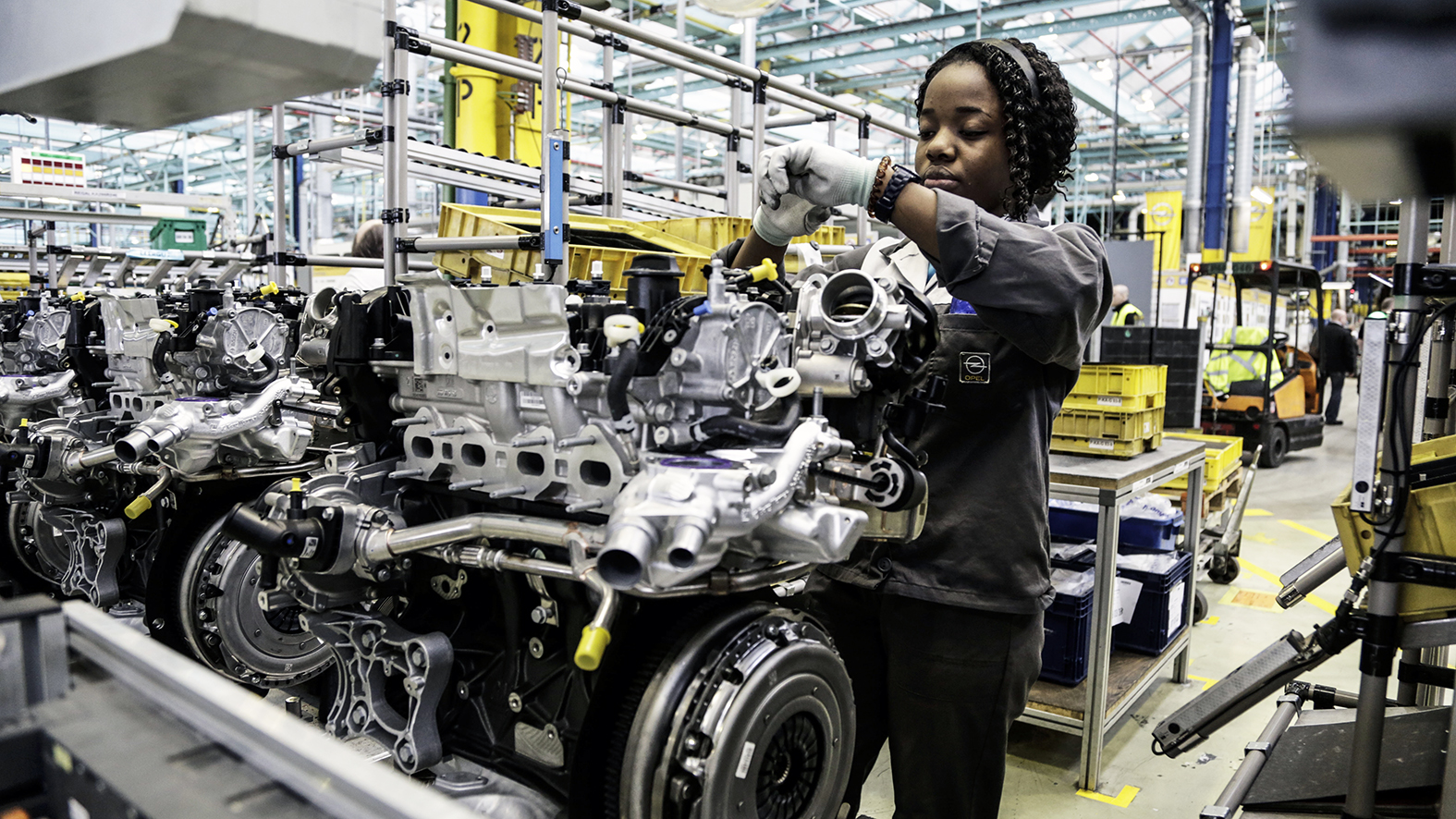
The injection pipe is pre-mounted.
enough time to learn all of the necessary gripping positions
“In September 2011, the new large diesel engine (LDE) was presented in Kaiserslautern, and just a year later, we installed the first machines for single-item production in Hall K30. By the end of 2013, we had already assembled our first Euro 6 engines on our production line in Hall K1,” says Plant Director Peter Winternheimer, listing off the most important milestones of the project. Being able to use the serial production equipment so early on in the process offered enormous advantages. For example, the teams had enough time to learn all of the necessary gripping positions and production workflows, and to identify and implement potential improvements. The employees in Kaiserslautern have now been producing sales-ready Euro 6 engines since October.
The real show-stopper was when the team integrated the new engine into the manufacturing process without stopping production on the current B-Diesel model. In order to make this possible, the maintenance team at the Kaiserslautern plant extended the assembly line by around ten meters. “This allowed us to move the existing workstations further apart so that we could place the workstations we needed for the new motor in between them,” explains Launch Manager Dietmar Weber.
New developments dampen vibrations and reduce noise
B-Diesel and LDE are both two-liter engines, but the two models are very different on a structural level. Add to that the new engine has a few more components than the B-Diesel. One such component, which can be seen at first glance, is the balance shaft flanged to the underside of the engine block. This is designed to dampen the vibrations of the engine block. The oil sump is now divided in two, which helps to reduce noise. In addition, the LDE is equipped with a new, more efficient injection system and an innovative exhaust gas treatment system, which breaks down nitric oxides and other pollutants.
Because the plant began introducing the LDEs onto the line last year, the employees of the assembly team were able to familiarize themselves with the new engine piece by piece. “On top of that, each team was provided with an engine on a type of dry line. This allowed them to have a close look at each new detail of the model,” reports Dietmar Weber.
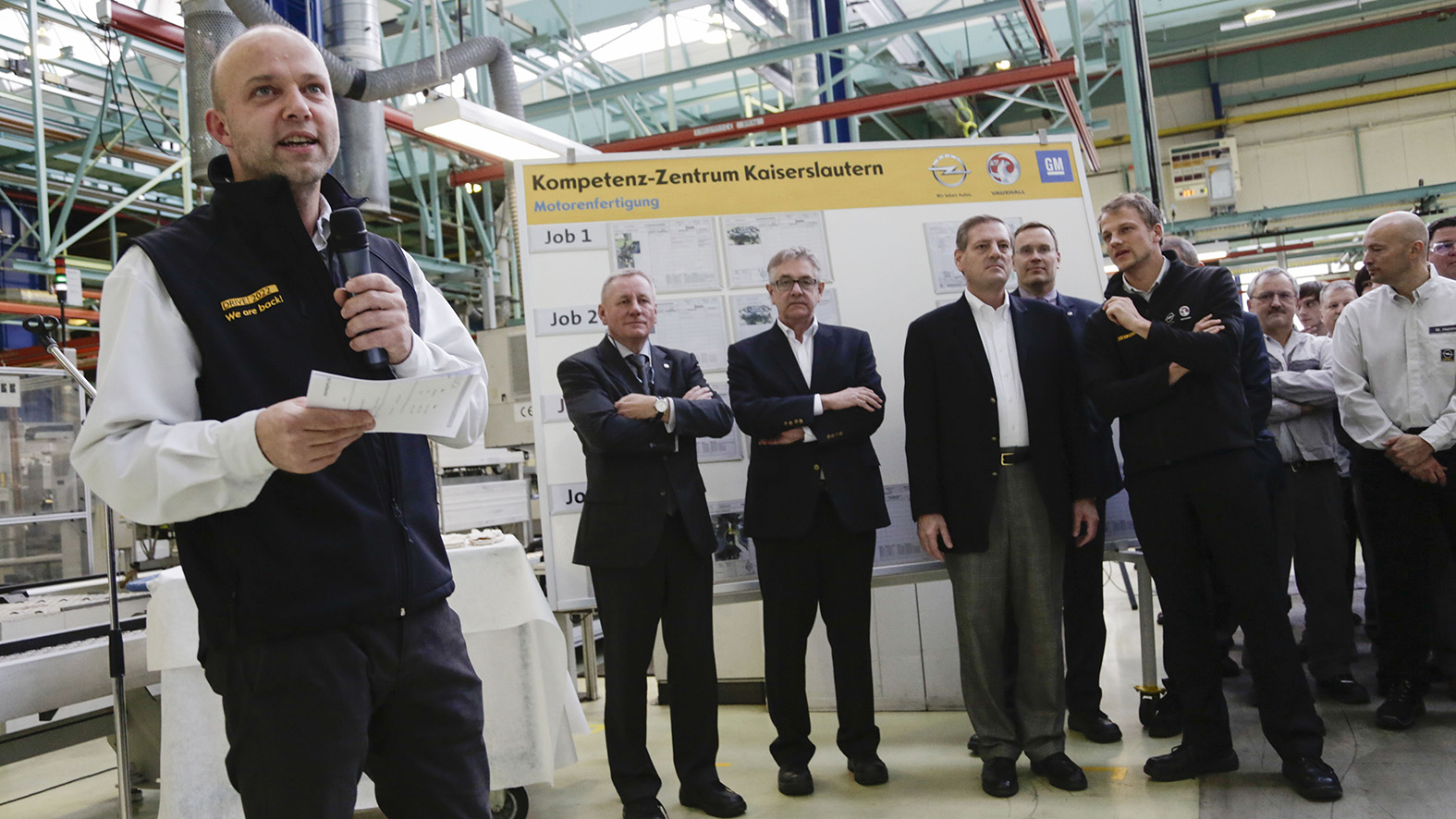
Final countdown: Acting plant manager Peter Winternheimer is waiting for the start signal.
The team made all of its own changes
At the same time, the project team worked to identify which components of the existing serial equipment could be incorporated in the new manufacturing line, and which components would have be to modified. “We made all of the changes on our own,” says Dietmar Weber. “At the end of the day, nobody knows this line as well as we do.” This resulted in dramatic savings for the production facility and earned the team the GM Transformer Award, a prize introduced by top management at GM to single out employees who have found new ways to help promote the goals of the company.
“The engine is great, and so are the people who work on it,” sums up Peter Küspert. For Jim DeLuca, it was “an honor and a privilege to be in Kaiserslautern for the event.” He goes on to say: “This project is a wonderful example of the values of General Motors in practice.” Together with Marc Schiff, Peter Küspert, and Christian Müller, Jim DeLuca personally “put the finishing touch” to the official premiere model “made in KL.”
The next project has already been determined
The new engine will be installed in the Insignia and in the Zafira Tourer. Alongside the Opel product offensive, in which the company aims to present 27 new models, the Opel Powertrain department will also be introducing 17 new engines on the market. “This will allow us to revamp 80 percent of our product portfolio,” observes Christian Müller. As part of this initiative, the team in Kaiserslautern will be adding yet another new engine to the line within the next ten years. GM will be investing a total of €500 million in its manufacturing facilities in Rüsselsheim, Kaiserslautern, and Tychy, Poland. These plans were recently revealed by GM CE Mary Barra during her visit to Germany’s Mainspitze region.
While idling, the engine is already five decibels quieter than its predecessor. “Our mid-sized engines have already been dubbed ‘quiet diesels’ by the press,” says Launch Manager Dietmar Weber. “Let’s see what they think of the LDE.”
Summary of the technical specifications presented by Christian Müller, Vice President GM Powertrain Engineering Europe, and Jens Wartha, Chief Engineer and Program Manager:
Power
125 kW/170 hp
Displacement
1,956 cm3
Torque
400 Nm