It is a massive construction: the furnace is 36 metres long and the associated press table weighs 80 tonnes. Steel plates roll through the heating furnace at 930 degrees and are then abruptly cooled down during the pressing process. “During hot forming, the microstructure of the metal changes and complex shapes are possible,” explains Thomas Stasiewicz predominating the hissing and pounding of the system. The press shop manager puts on gloves and grabs a finished moulded part. Almost two metres long, bent, high-strength: ‘This is a roof strut, a reinforcement for the A-pillar of the new Grandland,”he says.
The strut is one of more than 100 pressed parts that are manufactured at the Kaiserslautern plant for Opel’s new top-of-the-line SUV. From a finger-sized transmission mount to a complex tunnel welded together from five individual parts: the body of the new Grandland contains a lot of know-how from the Palatinate. Whether it is side rails, wheel arches, axle parts or door impact beams – on average, more than 18,000 components per week are delivered from the Palatinate to Eisenach where the new Grandland is manufactured on the basis of the STLA Medium platform.
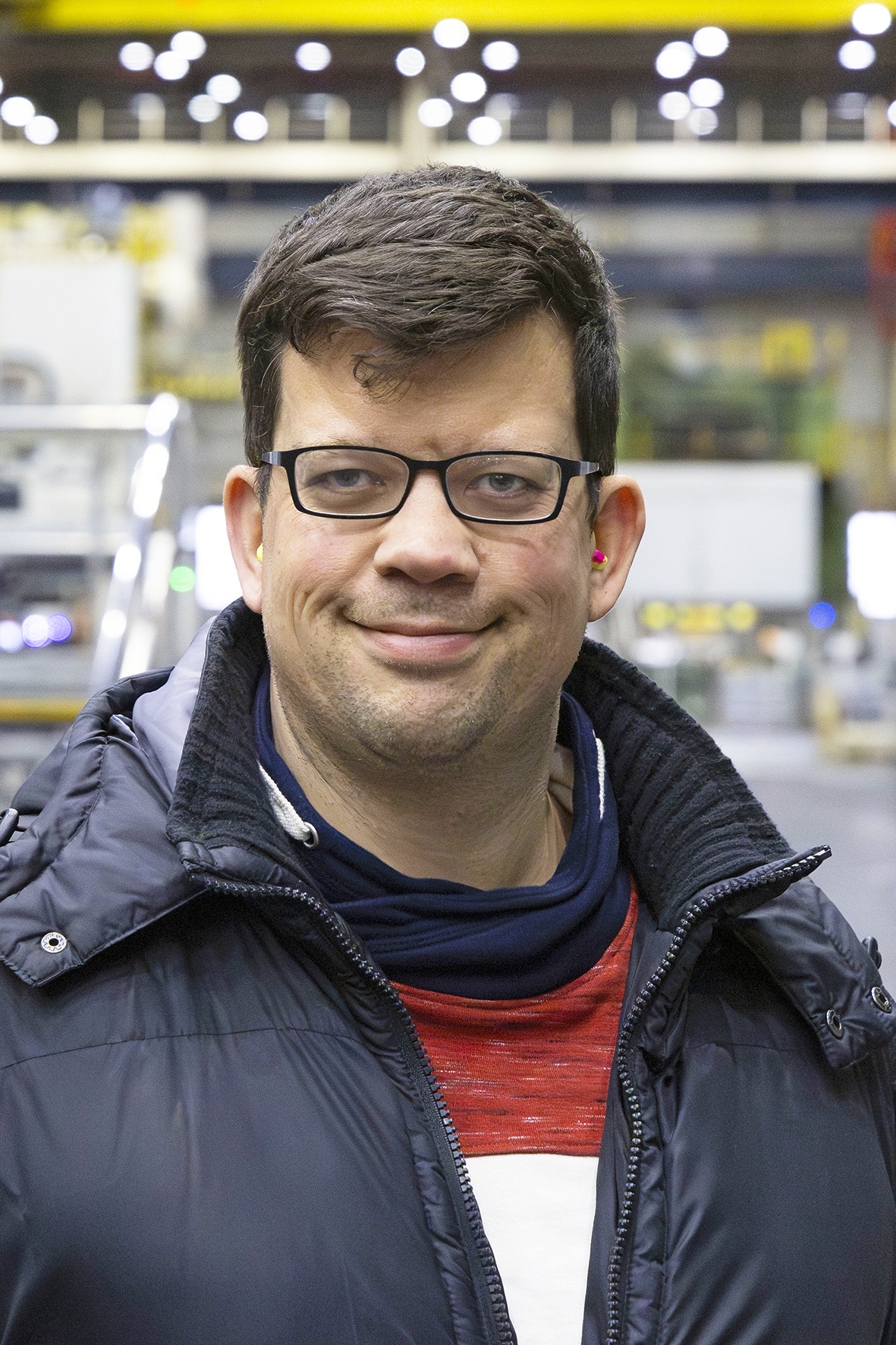
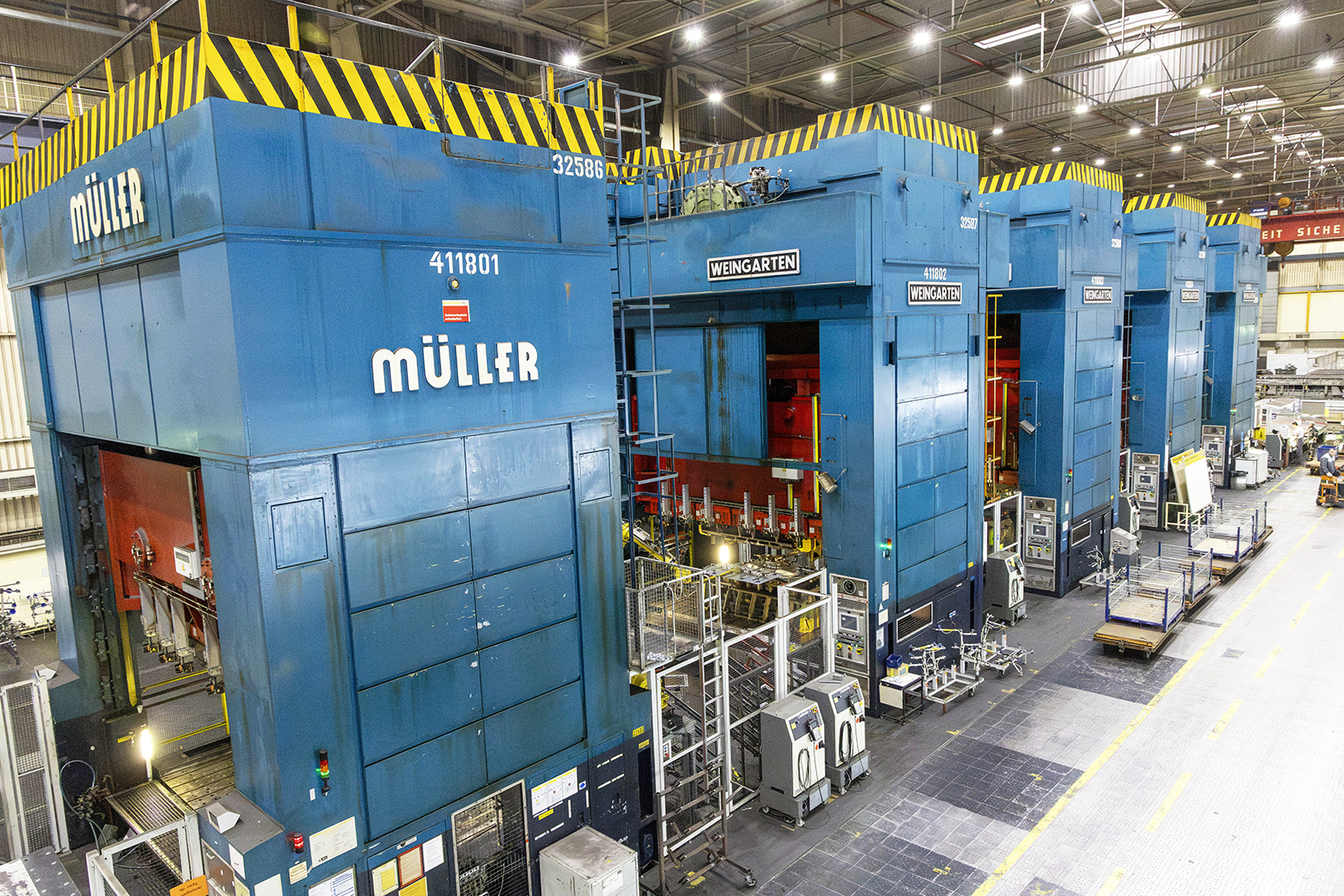
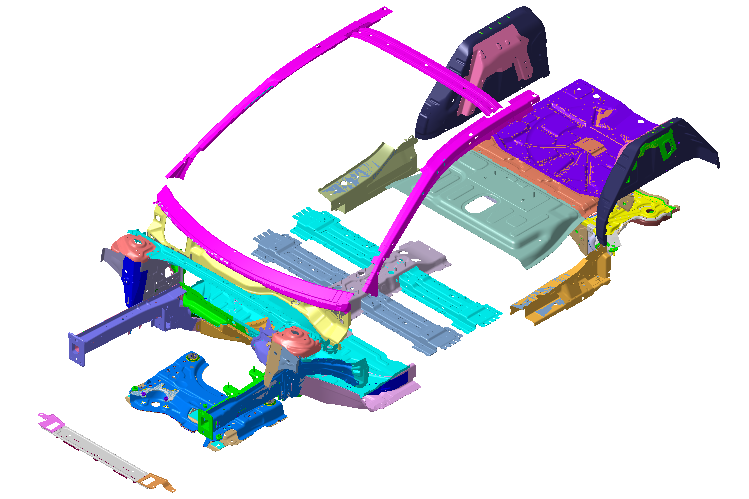
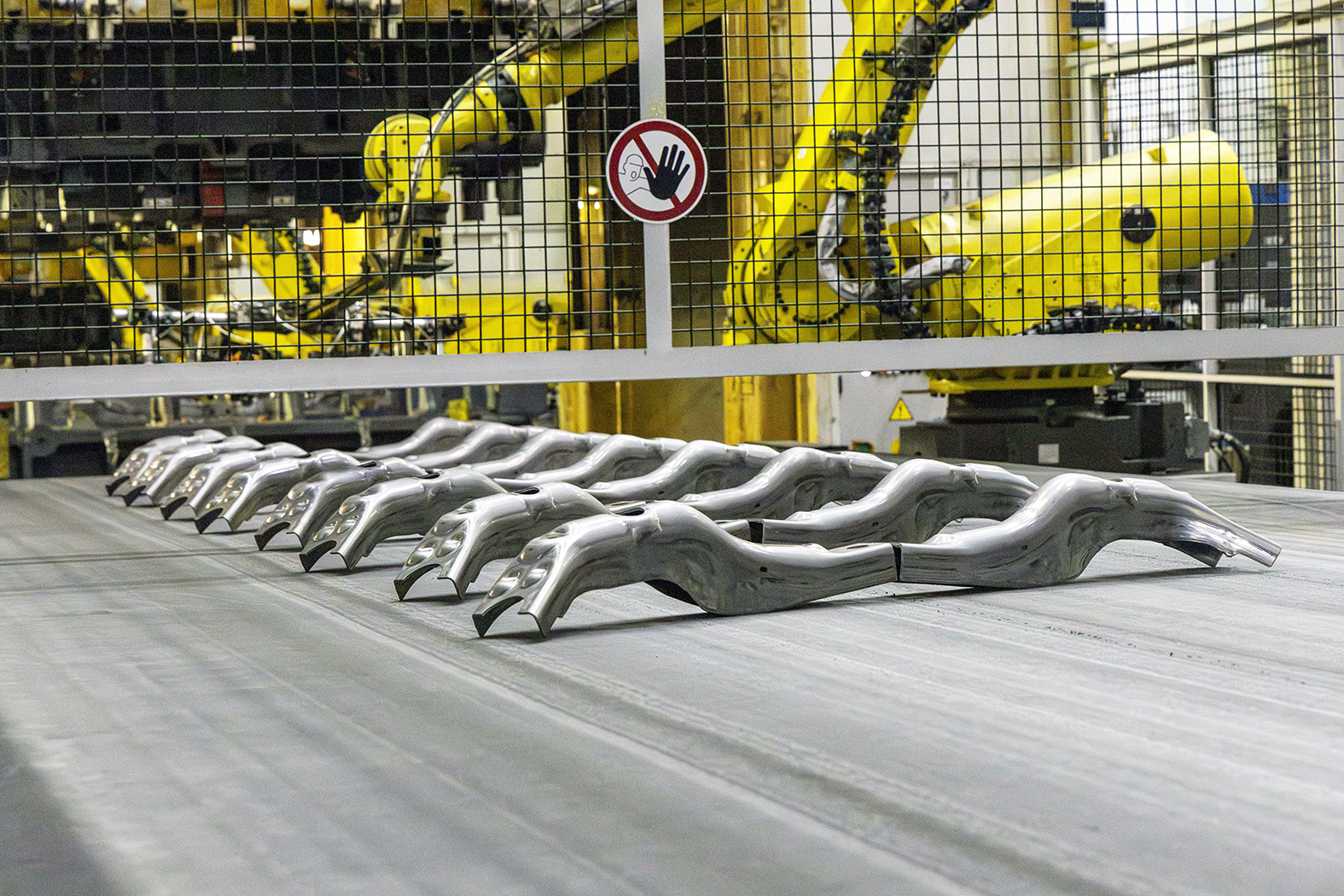
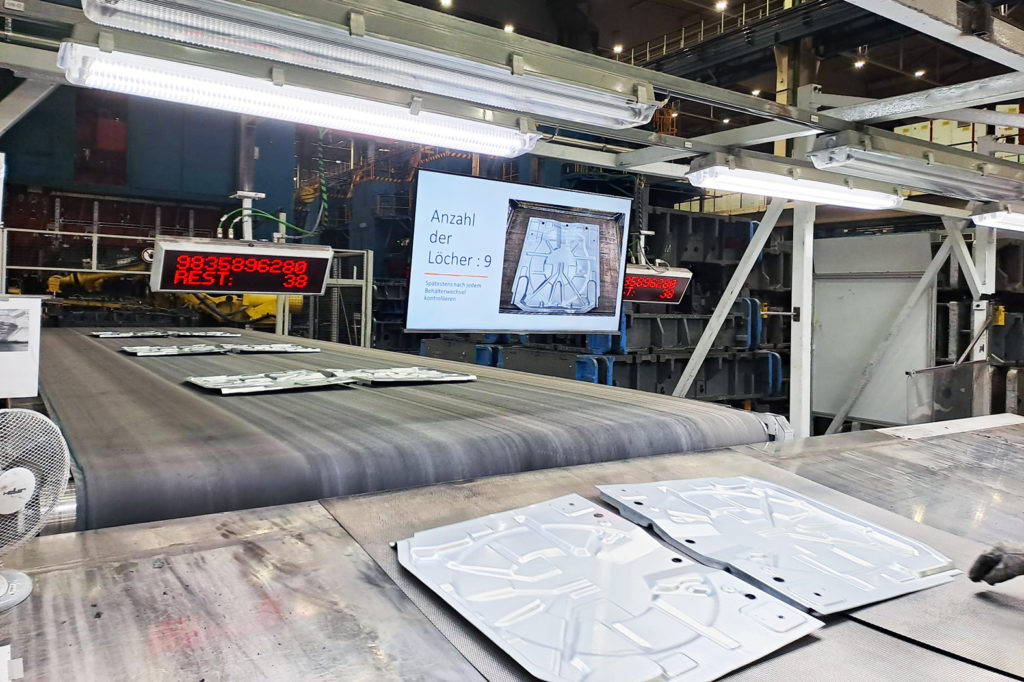
Particularly crash-relevant components like the roof strut come from the hot forming plant which was established in Kaiserslautern four years ago. “High strength combined with a comparatively thin-walled construction means increased safety and low weight,” explains Stasiewicz. The 35-year-old is what you would call a ‘home-grown’. He came to Opel in the Palatinate 20 years ago to train as a cutting machine operator. Today, he is responsible for the operation of the press shop. Around 260 employees are part of his team.
Presses for every purpose
Under his responsibility, the components for the Opel Grandland take shape in K19. The majority are cold-pressed, i.e. at room temperature with enormous tensile and compressive forces. The machinery is diverse: there are small presses for small parts, while other presses are connected in series. Robotic arms lift the pieces from one forming step to the next one. The long press lines are the giants among the forming lines: the steel plate moves in at one end and comes out five consecutive press strokes later as a finished component. In this special case as a boot floor for the Grandland.
Whether pressed parts or assemblies – Kaiserslautern currently supplies more than 20 Stellantis plants in Europe.
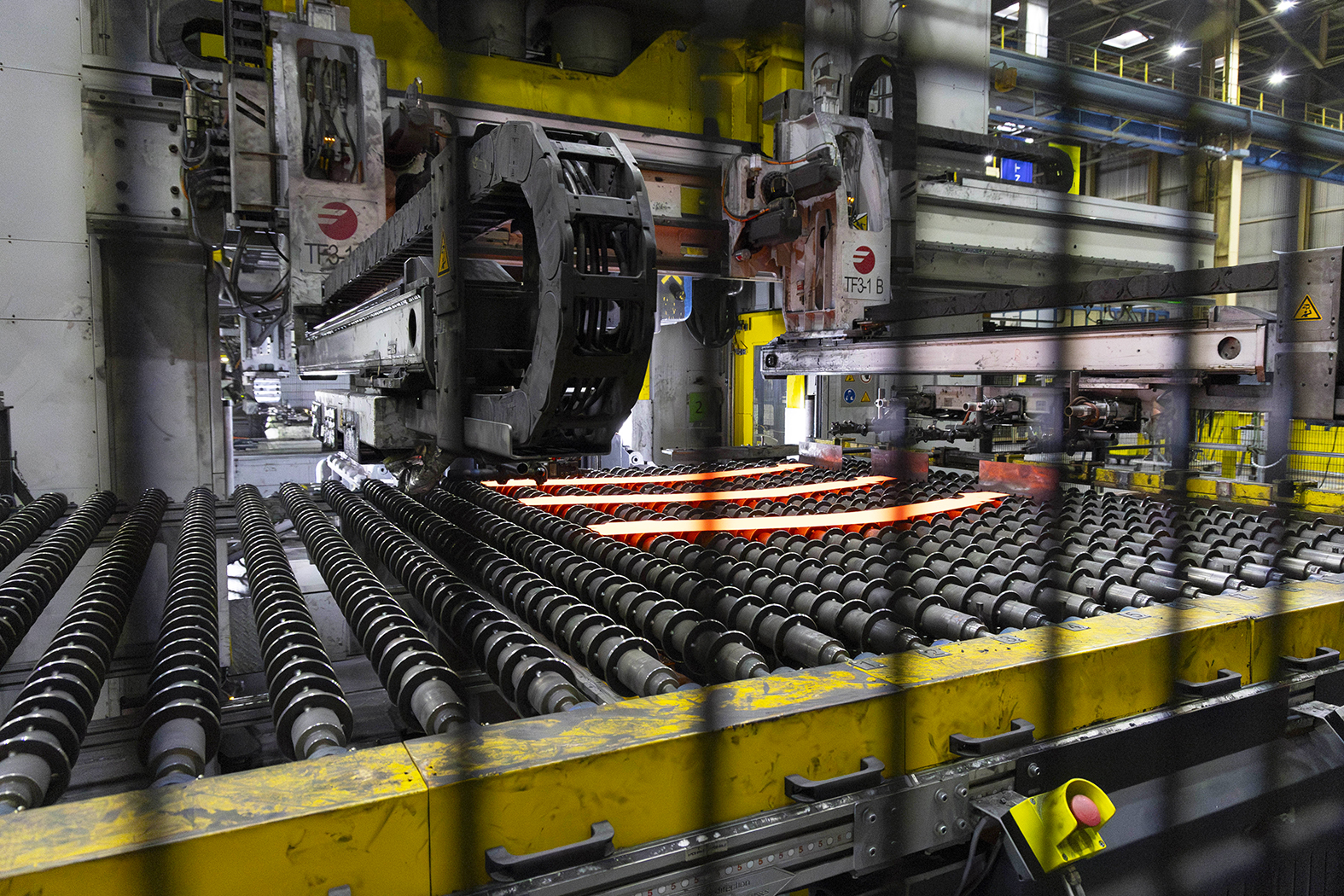
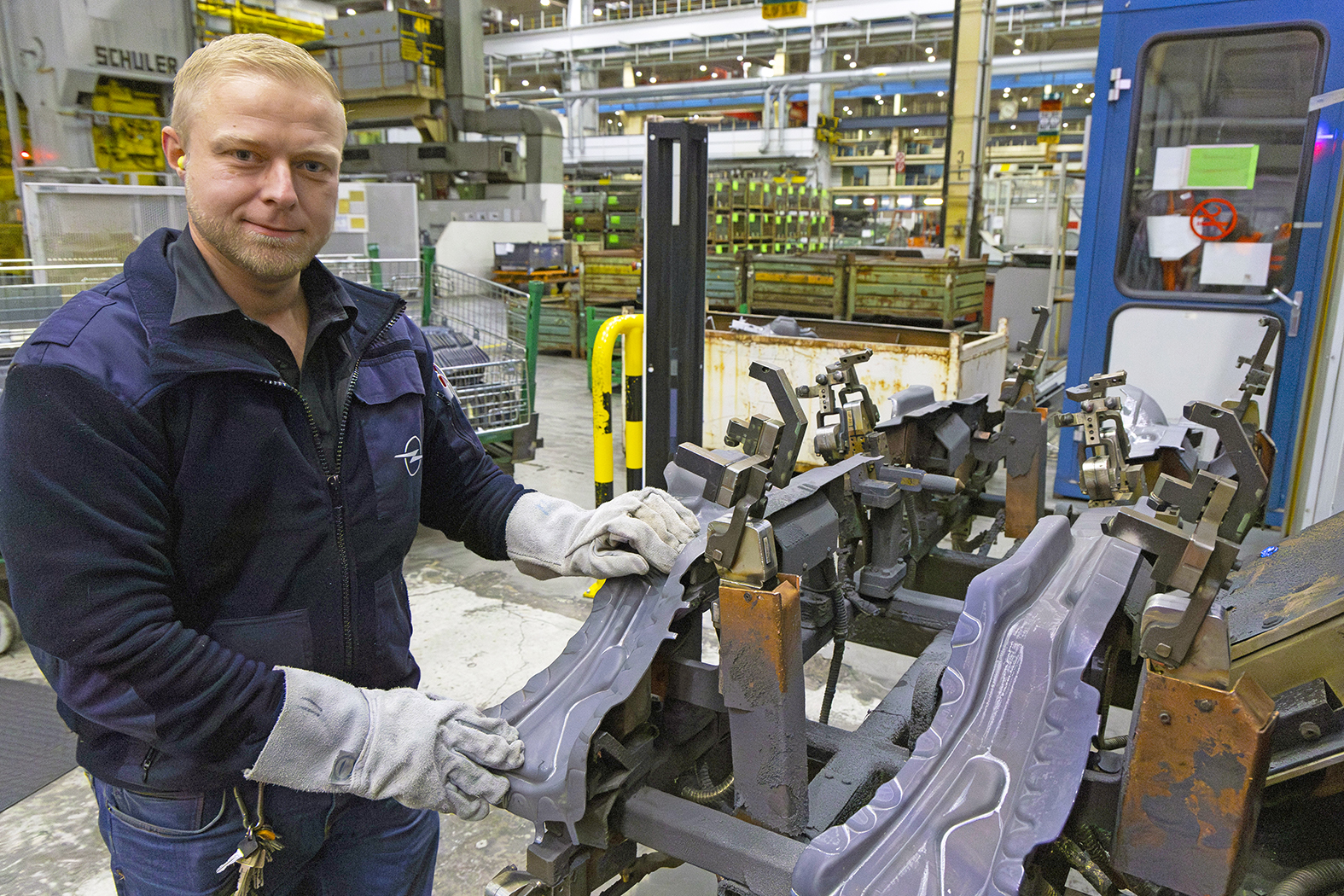
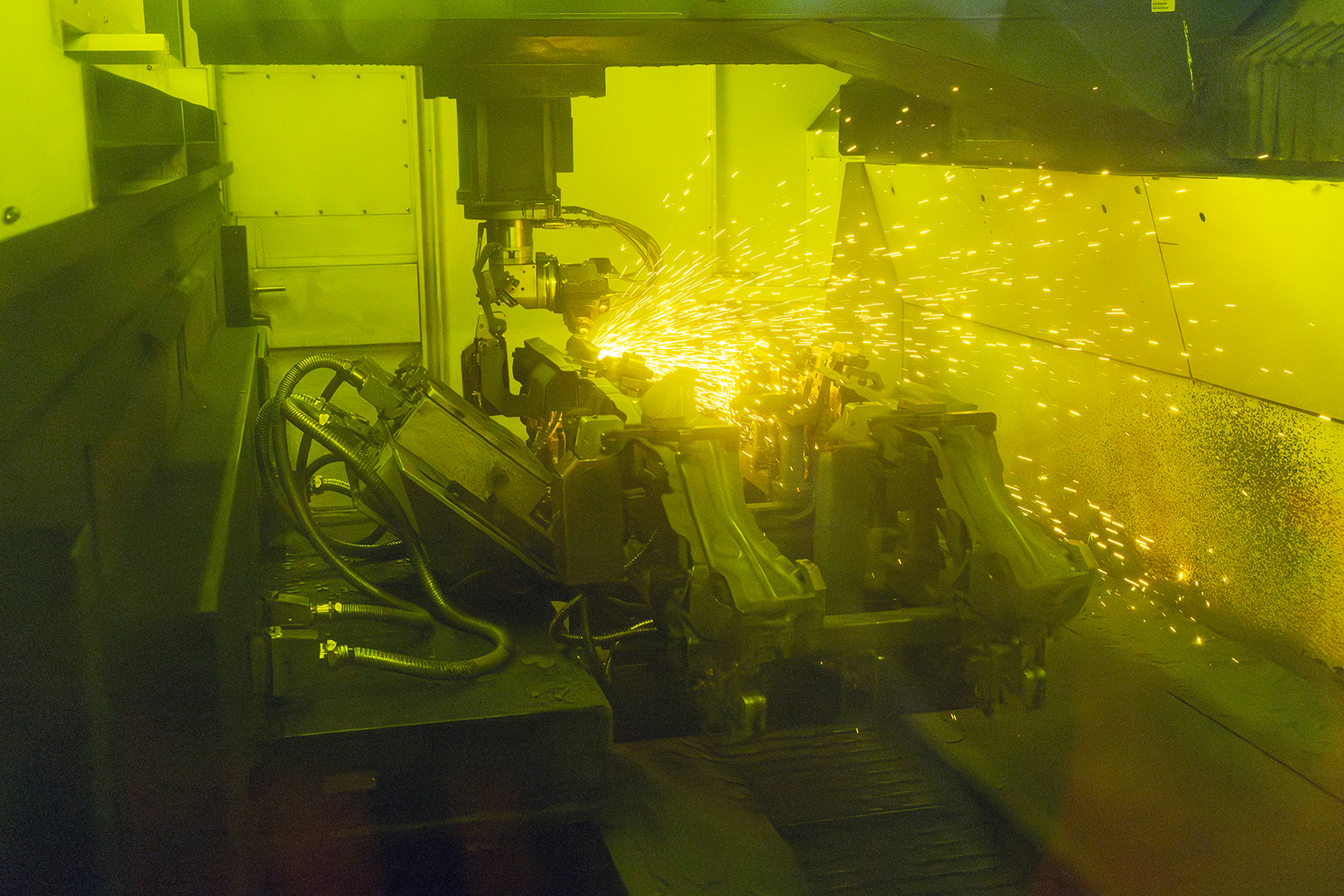
Both crane systems at the front of the hall constantly deliver fresh supply in the form of steel coils weighing up to 23 tonnes. Machines such as the large progressive press are directly loaded with the coiled metal strips. “Uncoiling, cutting, pressing – each step is automated from A to Z,” says Stasiewicz with fascination even after 20 years. No matter where you look in the K19, there is a lot of activity. Reinforcement struts roll out of the large transfer press. “A real high-runner,” comments the press shop manager. In other words: “The struts are produced in large numbers and are not only installed in the Grandland, but in many other models.”
‘Made in Lautern’ throughout Europe
“The degree of capacity utilisation is very good at the moment,” confirms Robert Leitner, who is, among other things, responsible for volume planning at the plant. The full order books are currently being processed in three shifts, and not only in the press shop. Whether pressed parts or assemblies, Kaiserslautern supplies more than 20 Stellantis plants in Europe. Not only the new Opel Grandland, but more than 30 Stellantis models contain components from Kaiserslautern. Around 500 part numbers are stored in the system. In other words: 500 different components are part of the Palatinate portfolio.
“New technologies and methods are a must. They make us adaptable – and efficient.”
– Robert Leitner –
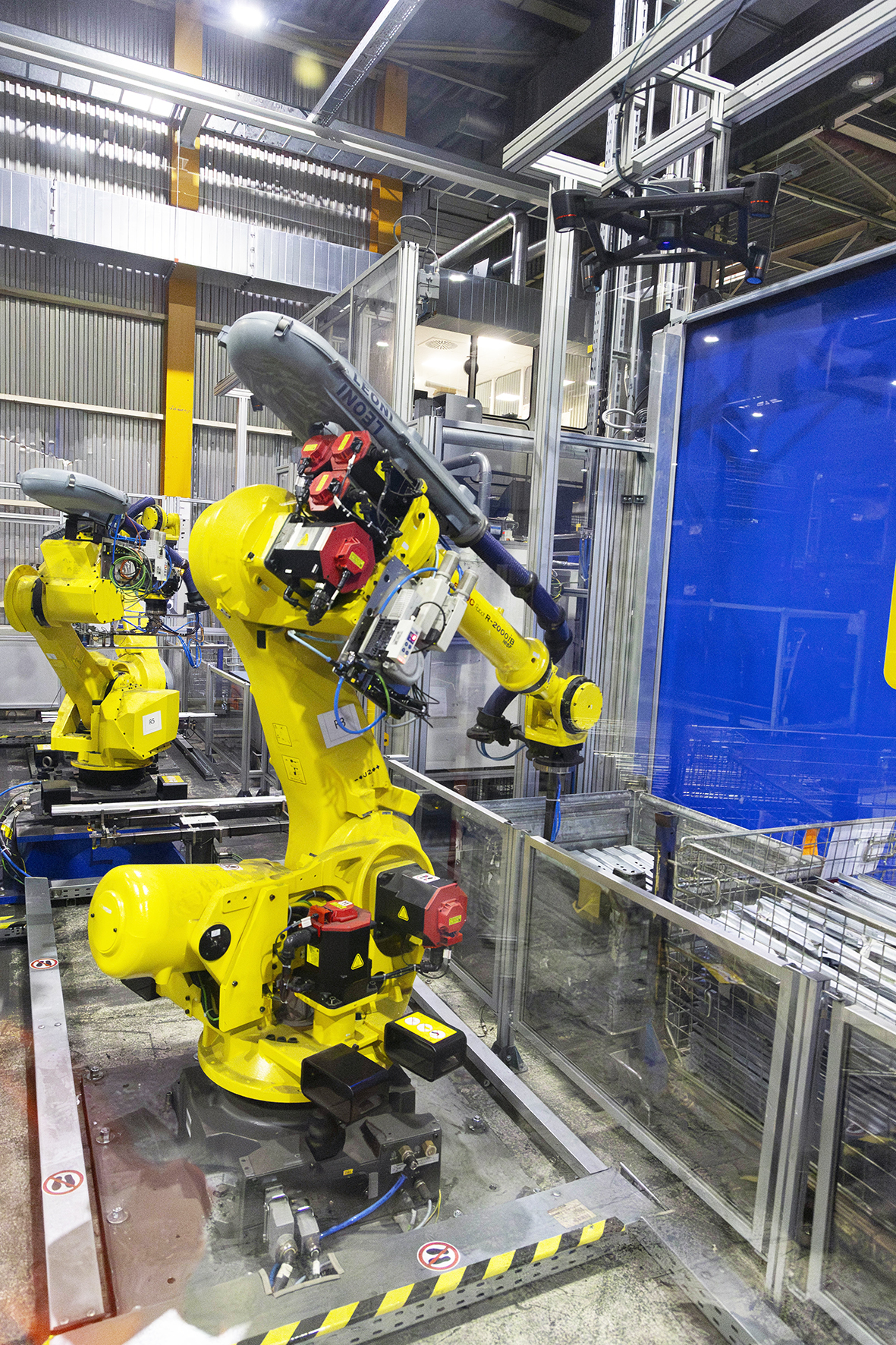
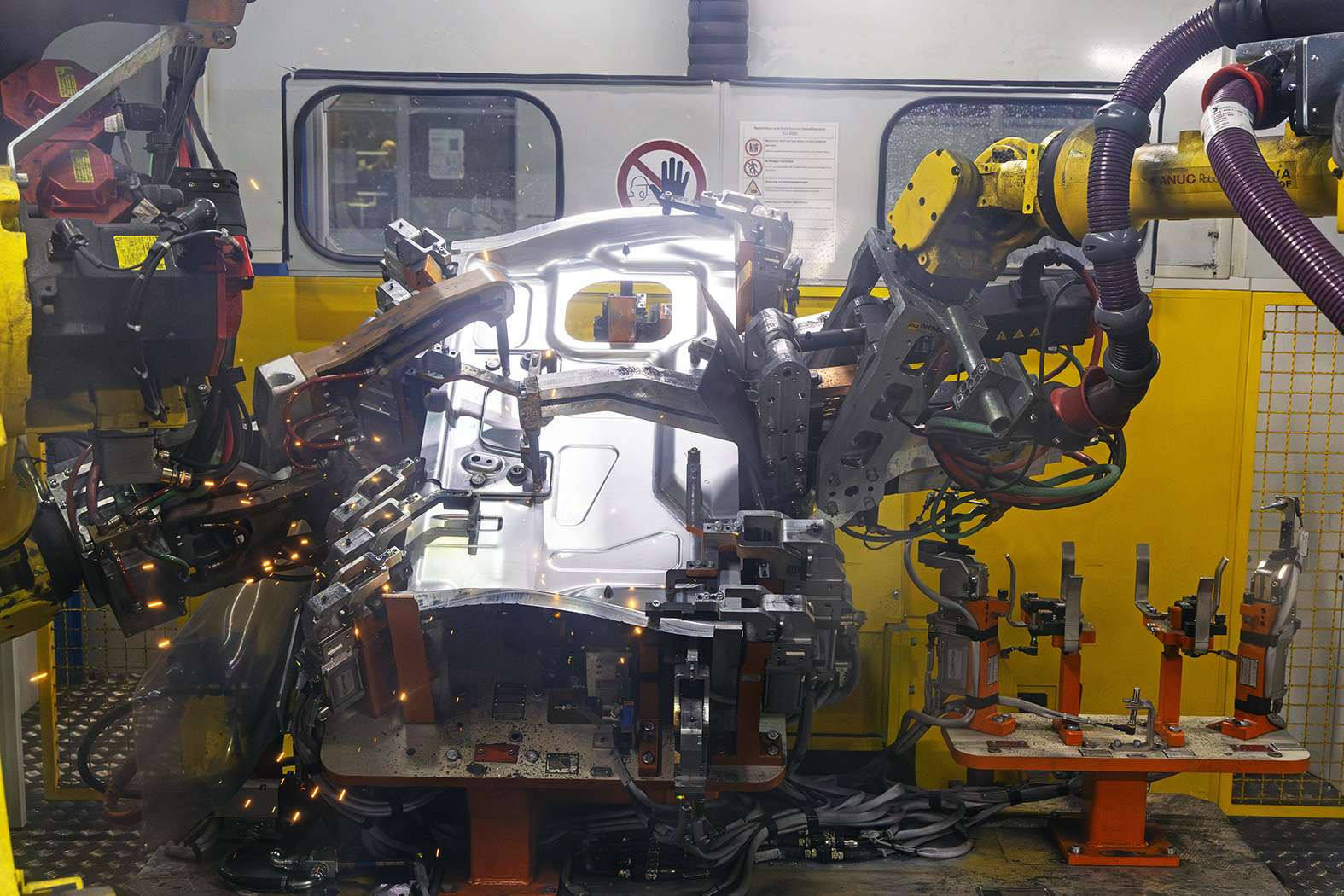
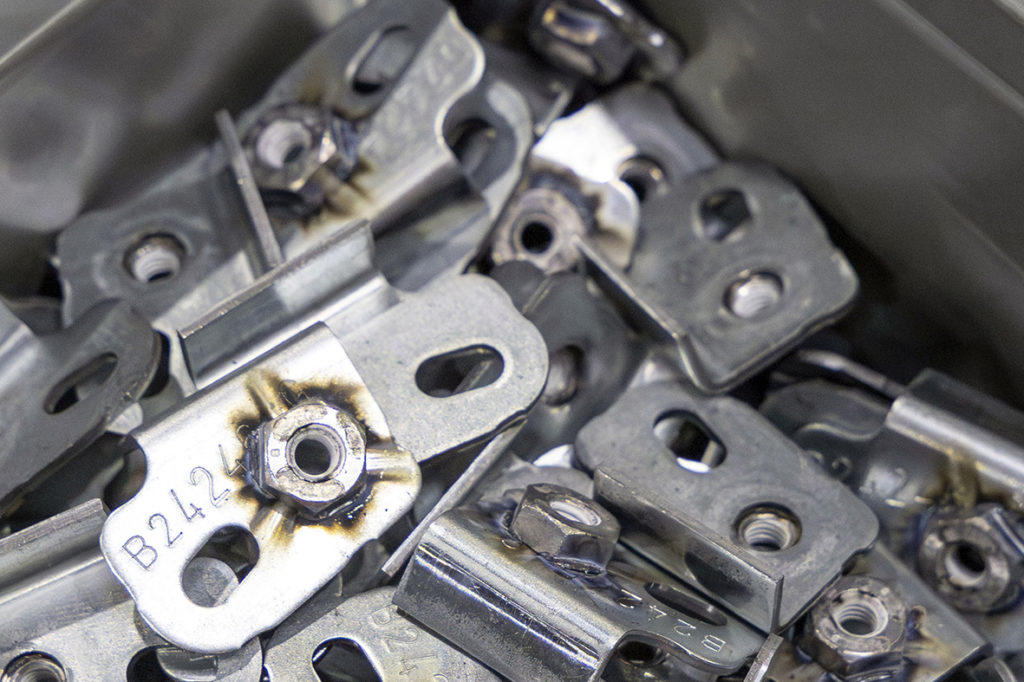
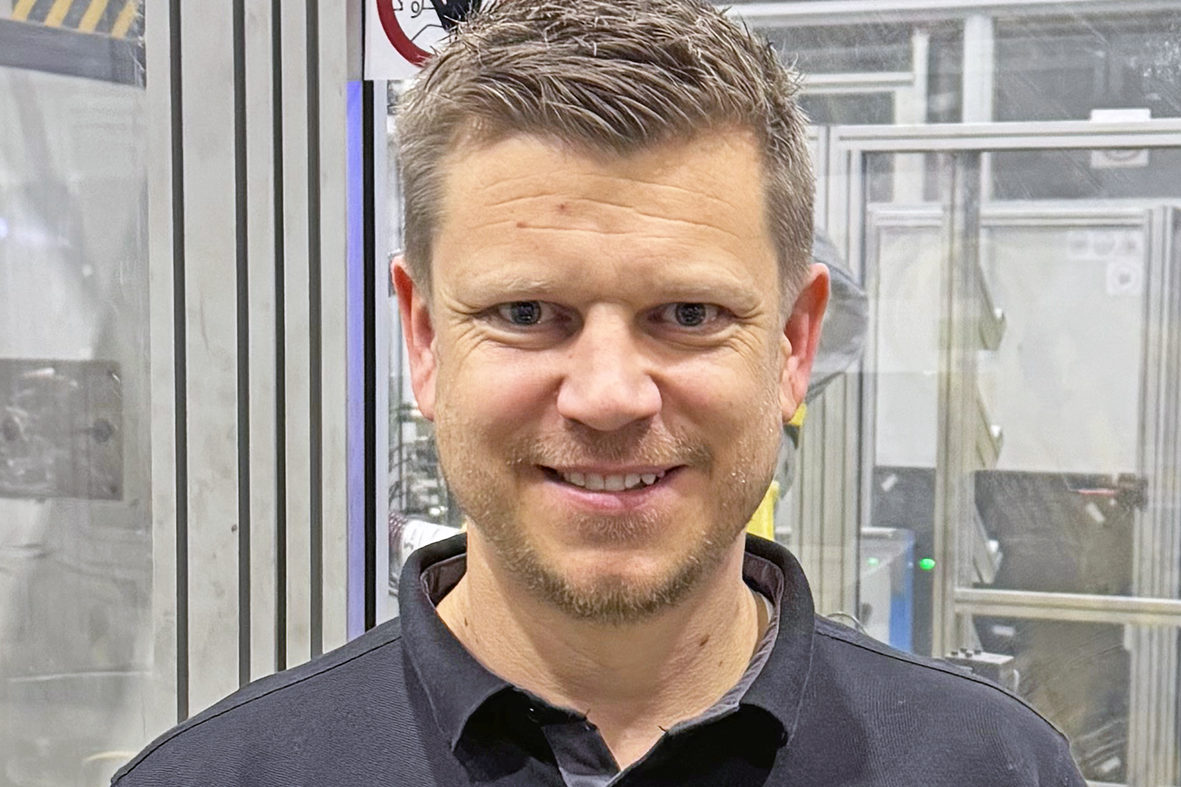
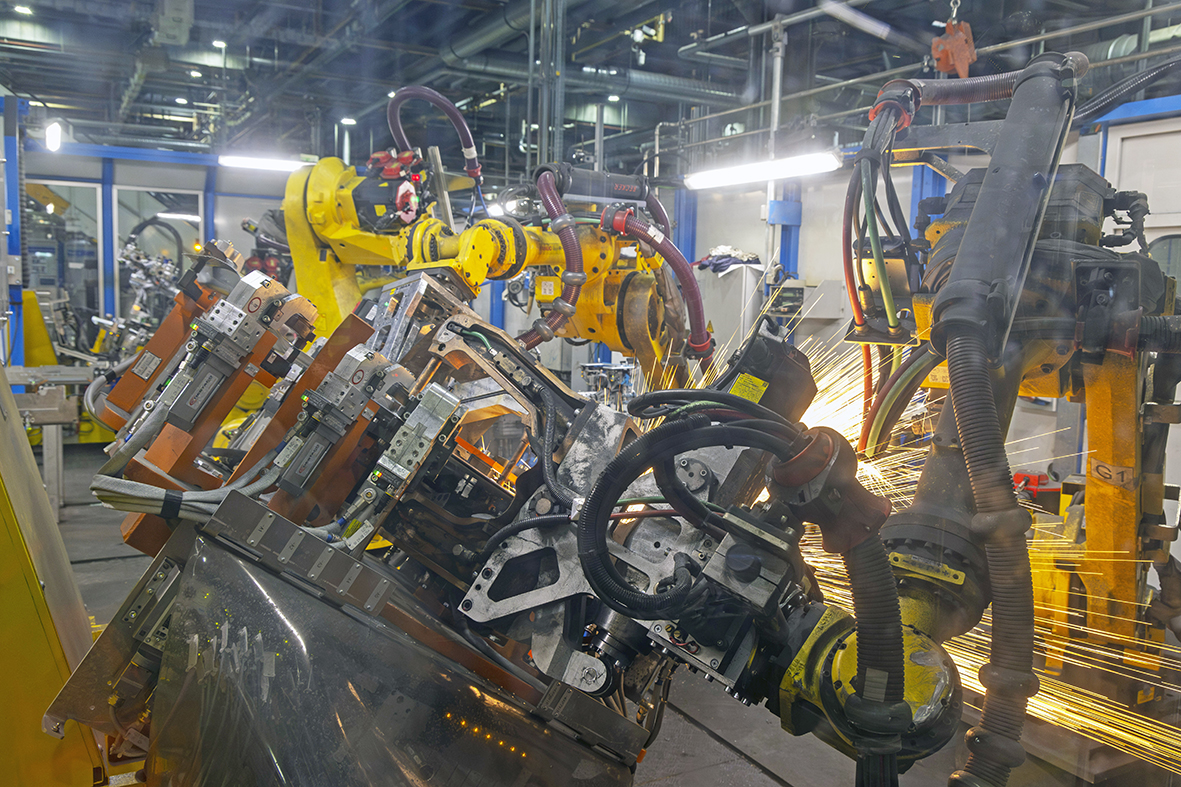
Leitner also learnt his profession from scratch at the Palatinate site and has been with the company for 30 years. As a former maintenance technician, he knows the machinery inside out, and his expertise now also includes process optimisation, known as advanced industrial engineering. “New technologies and methods are a must at our site. They make us adaptable – and efficient,” he says. One important driver is continuing automation. How far the autonomous operation of the machinery has already progressed can also be seen in K25 where the pressed parts are further processed as required.
Machines work autonomously
It is just fascinating: In 54 closed cabins, the so-called welding cells, robotic arms carry out programmed movements. They set weld seams and welding spots, apply adhesives and assemble components. A further 28 cells specialise in projection welding, a technology used to apply connecting elements such as nuts or bolts. Some cells are permanently fitted by hand from the outside by employees, while for others even this is no longer necessary. “It is enough to provide a shooter once an hour,” says Florian Klinker, group leader of the engineering team.
‘Automation is progressing. We have rebuilt and optimised the facilities especially for the start-up of the Grandland.’
– Florian Klinker, group leader engineering –
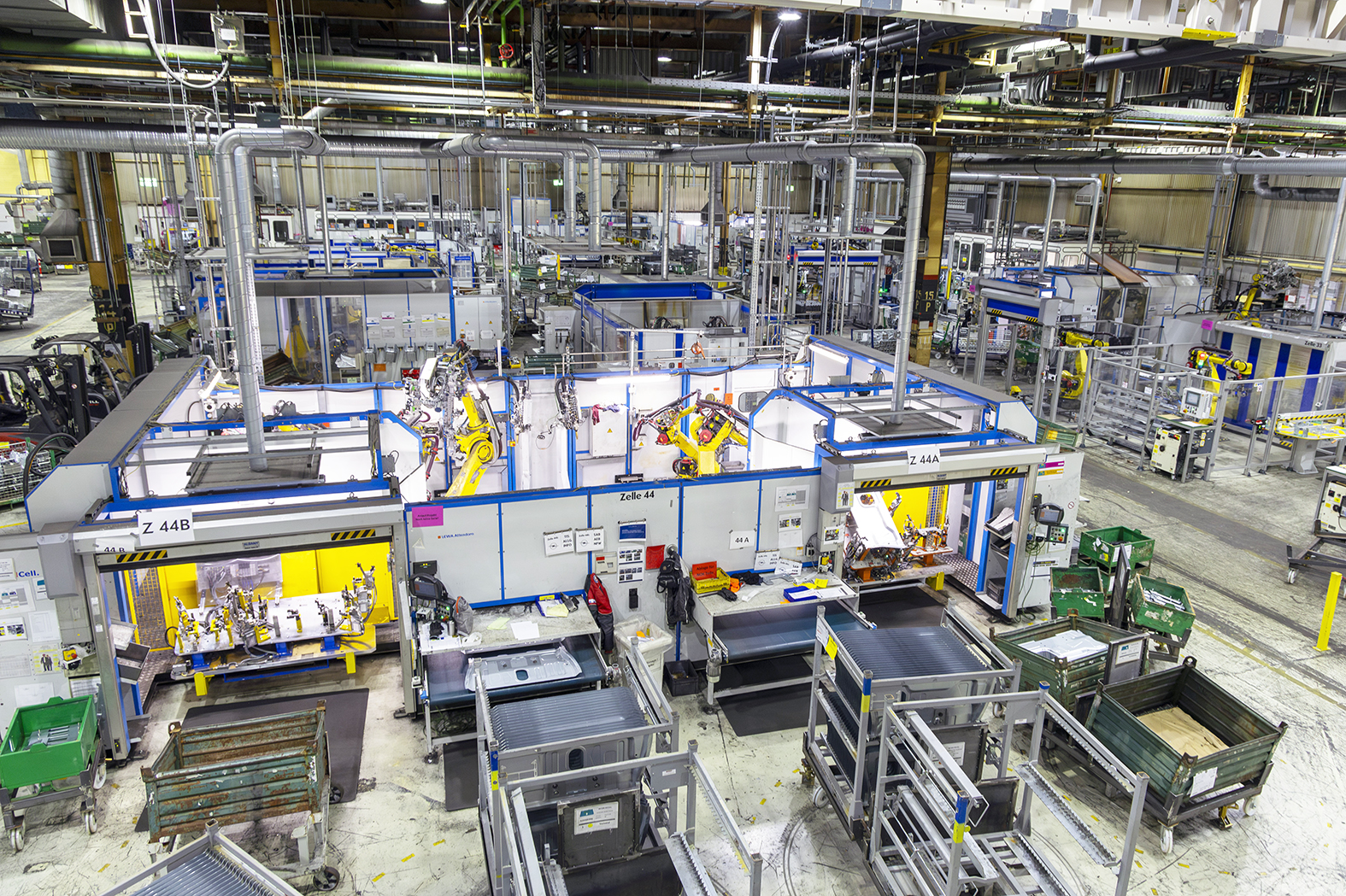
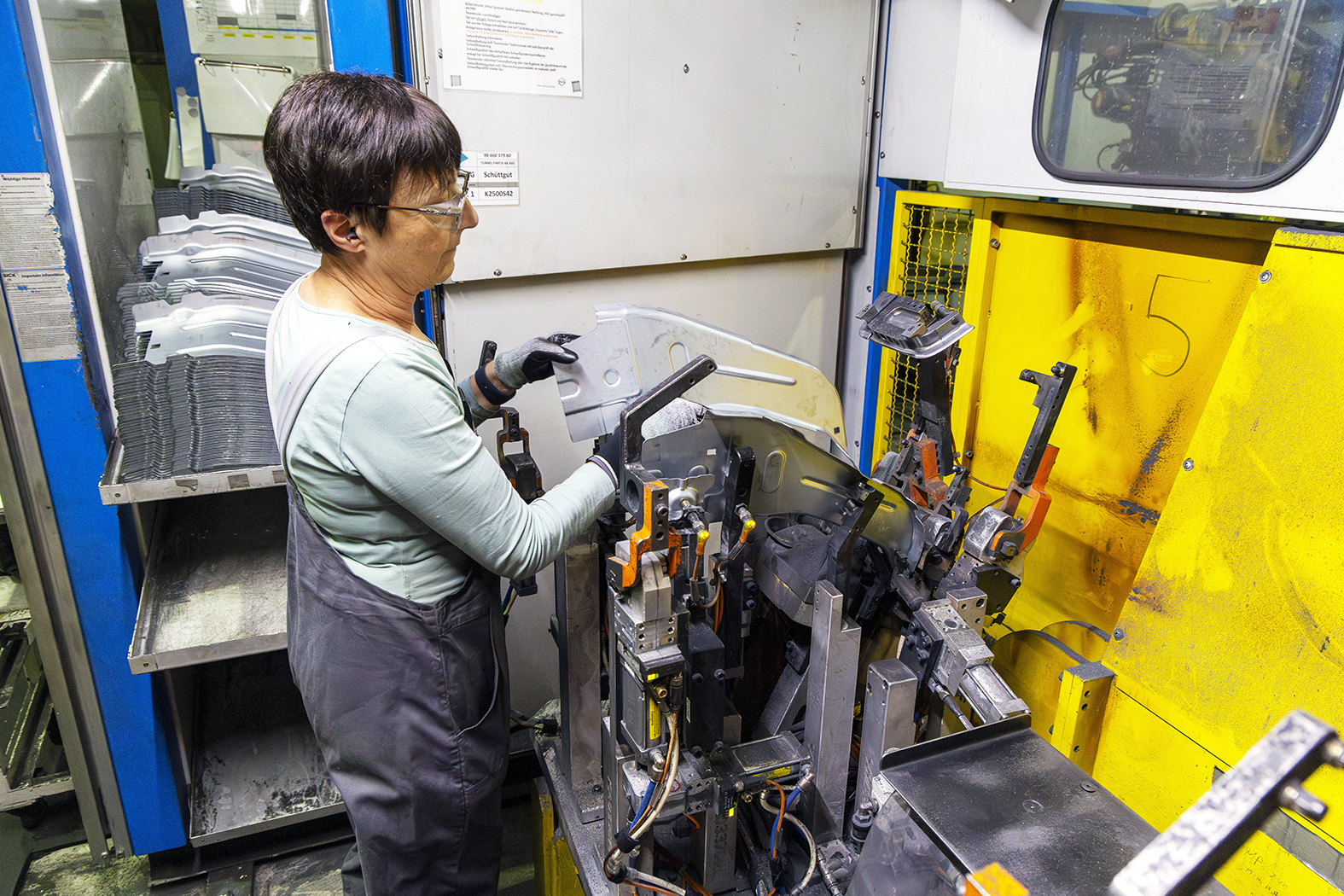
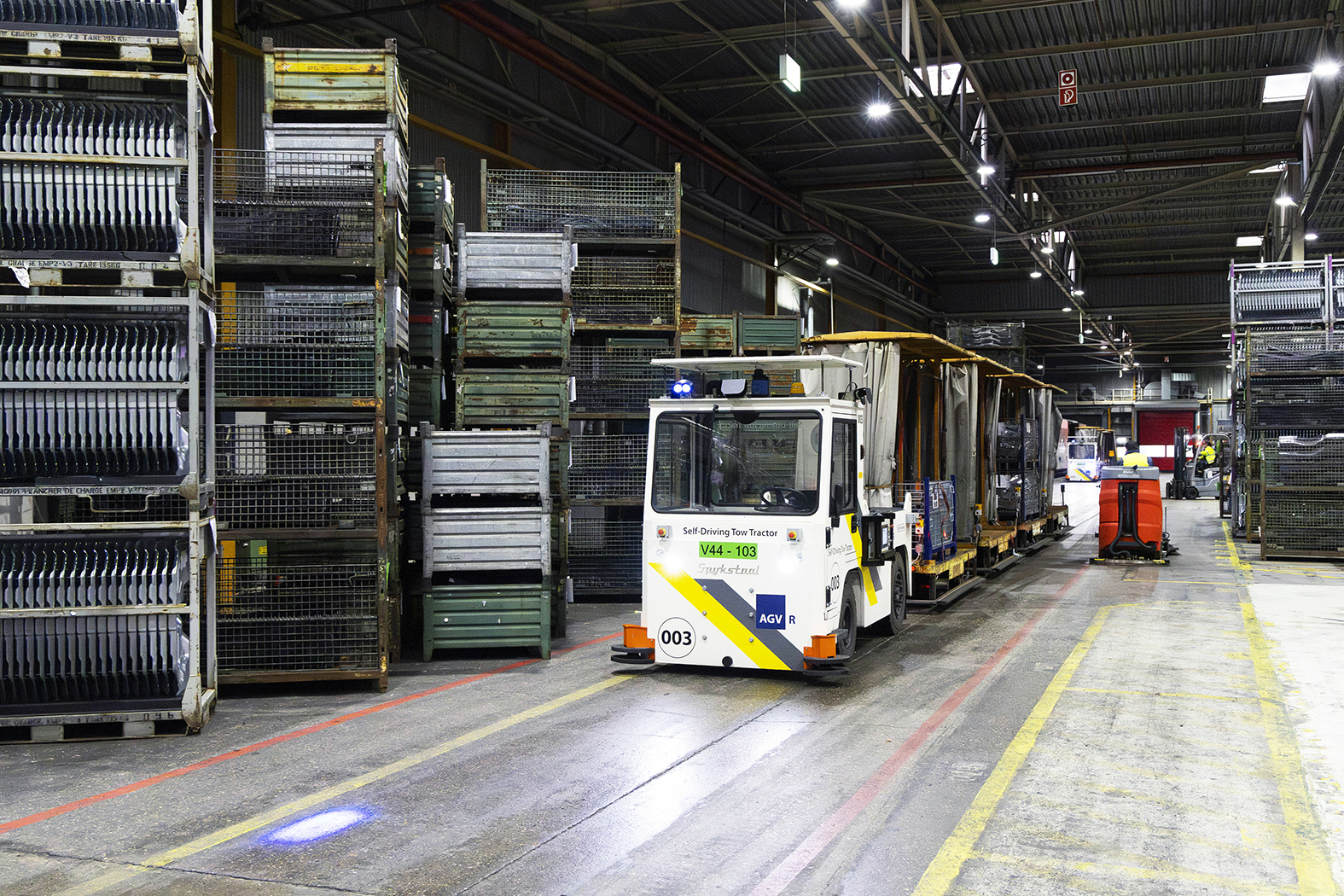
The ‘shooter’ is a big basket. It contains pressed parts for further processing, placed randomly rather than according to a pattern. With the help of a 3D camera, the robot arm precisely grips the item, places it on the work surface and the welding process begins. “Four more cells will soon be fully automated,” Klinker announces. Anyway, the systems are continuously developing. “We have rebuilt and optimised a lot especially for the Grandland start-up.”
Further prospects: Busy times continue
Between 280 and 310 tonnes of prefabricated parts leave the halls – every day. The removal process is largely automated. A self-propelled tractor stands at the edge of the hall, induction loops on the floor and intelligent sensors guide the driverless transport system safely to its destination. Every few minutes it is time to exit in the direction of K70, the dispatch area. From here, all goods are sent off to Eisenach and to other plants. In his role, Robert Leitner can look several weeks into the future: “The order books remain full.”
March 2025