- Hermann Groß (links) und Hermann Sabotta (rechts) arbeiten seit 1,5 Jahren mit Augmented Reality.
- Mit Hilfe des AR-Systems vergleichen sie das Mockup mit den Konstruktionsdaten.
- Um das System zu kalibrieren, fährt man drei Marker-Punkte an der Karosserie ab.
- Das System arbeitet positionsgenau und in Echtzeit.
- Mit einem Schwenk über den Motorraum wird deutlich, ob alles richtig sitzt.
- Auch GM-Chefin Mary Barra testete während ihres Antrittsbesuchs in Rüsselsheim das AR-Tool.
In einer großen Halle im Internationalen Technischen Entwicklungszentrum in Rüsselsheim (ITEZ) stehen aufgereihte Motorraumböcke mit verschiedenen Motorvarianten, sogenannte Mockups. Wozu diese Vielzahl an Testmodellen? Neben der Armaturentafel ist der Motorraum der komplexeste Bereich im Auto. Elektronik und jede Menge Assistenzsysteme – es gibt keinen Platz zu verschenken. Das Ziel der Ingenieure Hermann Groß und Hermann Sabotta ist es, mithilfe der erweiterten Realität diesen Platz bestmöglich auszunutzen. Hermann Sabotta: „Es wird immer enger im Motorraum, dadurch haben schon kleine Fehler große Auswirkungen.“ Oder um im Fußballbild zu bleiben: Mit dem Augmented Reality-Tool ziehen die Ingenieure der Fahrzeug-Integration „virtuelle Abseitslinien“ in den Motorraum, um zu prüfen, ob alles richtig sitzt.
Das Spielfeld ist ein Mockup
Drei Monate arbeiten die Monteure an dem physisch greifbaren Mockup. Gleichzeitig arbeiten die Konstrukteure weiter an dem virtuellen Model. Bevor Tests an dem gebauten Mockup durchgeführt werden können, müssen Realität und virtuelle Daten also erst einmal auf den gemeinsamen finalen Stand gebracht werden. Hier kann die AR-Anwendung so richtig punkten. Hermann Groß ist überzeugt von den Vorteilen der Technik: „Das System spart uns viel Zeit und beendet langwierige Diskussionen.“
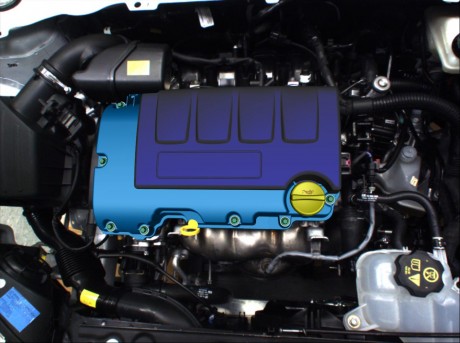
Blick in einen Motorraum mit virtuell eingepasster Motorabdeckung.
Die AR-Spezialisten arbeiten hauptsächlich mit drei Stellen zusammen: internen Abteilungen, externen Ingenieurbüros und Lieferanten. Viele Stellen also, die ihre jeweiligen Teile im Motorraum platzieren. Stimmt die Form oder Position eines Teils nicht, ist häufig unklar, wo der Fehler liegt. Oft scheint alles zu passen, betrachtet man lediglich die einzelnen Komponenten. Ein Blick auf den Bildschirm, auf dem das Realbild mit den digitalen Konstruktionsdaten kombiniert ist, löst dagegen Unklarheiten schnell auf. Das AR-System hilft jedoch nicht nur, Fehler zu suchen, sondern bietet gleichzeitig die Grundlage, Lösungen zu finden.
Im Abseits? Ein Kabelsatz auf dem Prüfstand
Hermann Sabotta gibt mithilfe der AR den Schiedsrichter. Im Motorraum scheint ein Kabelsatz nicht richtig zu verlaufen. Dazu kalibriert er zuerst das Programm. Es orientiert sich an festen Punkten, die an der Karosserie markiert sind, fährt die drei Marker-Punkte ab. So kann das Programm errechnen, auf welchen Achsen sich welche Punkte befinden und das virtuelle Modell entsprechend darauf setzen. Als nächstes fährt Sabotta mit dem Messgerät den Motorraum ab. Die Kamera überträgt das Bild live auf einen großen Bildschirm. Währenddessen werden die Konstruktionsdaten in Echtzeit über das reale Bild des Motorraums gelegt.
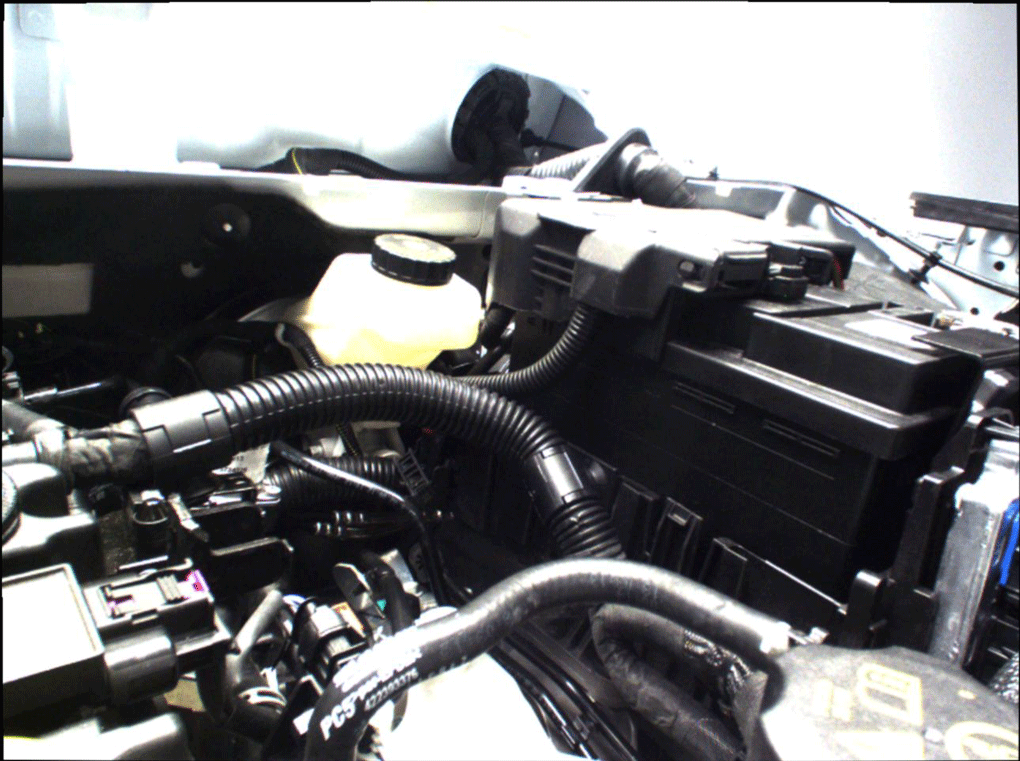
Gut erkennbar sind die Stellen, an denen das Mockup von den Konstruktionsdaten abweicht.
Im System kann man auswählen, was man angezeigt bekommen möchte. Den kompletten Datensatz oder bestimmte Elemente. Ist ein Bereich identifiziert, der nicht mit den Konstruktionsdaten übereinstimmt, kann Herr Sabotta durch Wechsel der Perspektive genau ausmachen, was nicht passt. Ein großes Plus der Technik, denn manchmal wirkt der Verlauf eines Kabels von oben passend, von der Seite sieht man jedoch, dass es anders liegt. Sabotta: „Schläuche oder Kabelsätze laufen in der Realität häufig nicht so wie virtuell konstruiert, da das Material sich anders verhält oder in einem anderen Radius biegt.“ Nun muss geprüft werden, welche Folgen diese Abweichung hat. Dafür gibt Hermann Sabotta seine Erkenntnisse an die Konstrukteure weiter. Die entscheiden, ob die Realität auf die virtuellen Daten zurückübertragen werden kann. Es kann sein, dass ein paar Millimeter Überschneidung dazu führen, dass mehrere Teile neu positioniert werden müssen.
Hard- und Software der AR-Anwendung kosten zirka 100.000 Euro. Betrachtet man die Kosten, die im Automobilbau entstehen, rechnet sich der Einsatz schnell. Hermann Groß: „Das System vermeidet immense Änderungskosten. Die Einsparungen zu beziffern ist allerdings schwierig, da die Fehler ja erst gar nicht entstehen, sondern nur virtuell gemacht werden.“ Was sie finden, ist ganz unterschiedlich. Von kleinen Abweichungen wie der Position der Bolzen bis hin zu solchen, die in der Produktion große Probleme machen könnten. Denn startet erst mal die Serie, lassen sich Werkzeuge nur schwer und kostspielig korrigieren.
Foul oder nicht Foul? Dieser Schiedsrichter kann mehr
Es geht jedoch nicht nur darum, Fehler zu finden oder Daten kontrollieren. Die AR-Bilder eröffnen auch eine gute Möglichkeit, früh Konzepte zu prüfen. So kann beispielsweise ein Opel-Modell mit wenigen Klicks mit einem neuen Stoßfänger ausgestattet werden. Dadurch, dass kein statisches Bild entsteht, sondern die Kamera das Objekt von allen Seiten zeigen kann, bekommen Konstrukteure einen guten Eindruck, ob Erscheinungsbild und Befestigungskonzept passen, und ob die neuen Elemente mit den Umgebungsteilen funktionieren.
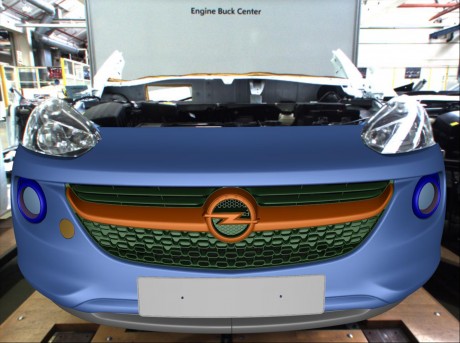
Industrie 4.0: Positionsgenau werden die virtuellen Daten auf das reale Objekt gelegt.
Es spricht sich bei Opel herum, wie hilfreich AR sein kann. Dementsprechend unterstützen Groß und Sabotta regelmäßig andere Bereiche und besuchen sie mit dem mobilen System. Jüngst halfen sie Kollegen vom Powertrain beim Aufbau eines Prüfstands. Manchmal kommen auch Autos aus der Produktion zu Tests in der Fahrzeug-Integration vorbei, wenn etwas nicht passt.
Die Möglichkeiten für den zukünftigen Einsatz von AR sind riesig, nicht nur in der Entwicklung oder Integration. Auch in anderen Bereichen wie dem Marketing oder im Service hält die erweiterte Realität Einzug und kann mit Datenbrillen wie „Google Glass“ zukünftig direkt vor unseren Augen neue Welten entstehen lassen. Bis es soweit ist, genießen wir sie erst mal weiter als virtuellen Schiri, der nie daneben liegt.
Text: Sabrina Künz, Fotos: Martina Sabais (Asterion)
Es besteht aus einem tragbaren Koordinatenmessgerät, dem FARO-Arm, und einer daran befestigten Kamera. Die zwei Schlüsselanforderungen an das System sind, dass es positionsgenau und in Echtzeit arbeitet. Damit aus dem Messsystem und der Kamera eine erweiterte Realität entsteht, braucht es ein spezielles Programm.
Die Software entwickelte Metaio, ein weltweit führendes Unternehmen im Bereich Augmented Reality. Im Falle von Opel war es nicht wirklich Liebe auf den ersten Blick. Hermann Sabotta: „Sie haben uns das System vorgeführt, aber so richtig überzeugt waren wir nicht. Es war noch nicht auf unsere Bedürfnisse eingestellt. Aber ich hatte das Gefühl, das könnte etwas werden.“
Da die Opel-Ingenieure von Haus aus neugierig sind und immer nach neuen Wegen suchen, Arbeitsergebnisse zu verbessern, gaben sie dem System eine Chance. Metaio überließ es ihnen für ein paar Wochen, in denen sie Einsatzmöglichkeiten ausprobierten – und fanden.