- Das Instandhalter-Team der F 17-Wellenfertigung (v.l.n.r.): Franz Nagl, Wolfgang Kienzl, Stanislav Roskar, Frank Rüdinger, Patrick Seewald, Franz Matuschka, Horst Assigal, Jürgen Schulz, Peter Steinmetz, Georg Schmied, Daniel Soukup, Werner Soukup, Benjamin Vorderwinkler, Dieter Majcen, Christian Hoffmann.
- End-of-Line-Puffer in der Zahnradblock-Linie.
- In der Hauptwellen-Linie.
- End-of-Line-Puffer in der Hauptwellen-Linie – vorher … und nachher.
- Hauptwellen-Linie: Roboter-Station.
- Gerhard Rambek vor einer der zwei neuen Powerhon-Maschinen in der Hauptwellen-Fertigung.
Die Nachfrage nach den Asperner Fünfgang-Getrieben ist ungebrochen hoch. Um sie effizient erfüllen zu können, sind Produktivitätssteigerungen nötig. Was gar nicht so einfach ist angesichts des teilweise mehr als zwanzigjährigen Maschinenparks.
Vor allem zwei Bereiche machten bisher Kopfzerbrechen: die Zahnradblock-Fertigung und die Hauptwellen-Linie. Instandhaltungskoordinator Peter Leitner zeigt auf einen Zahnradblock und sagt: „Zahnradblock und Hauptwelle sind eben äußerst komplexe Teile. Der Zahnradblock zum Beispiel besteht aus vier Laufverzahnungen und zwei Steckverzahnungen. Er hat damit das Doppelte an Bearbeitungsschritten wie ein Gangrad.“
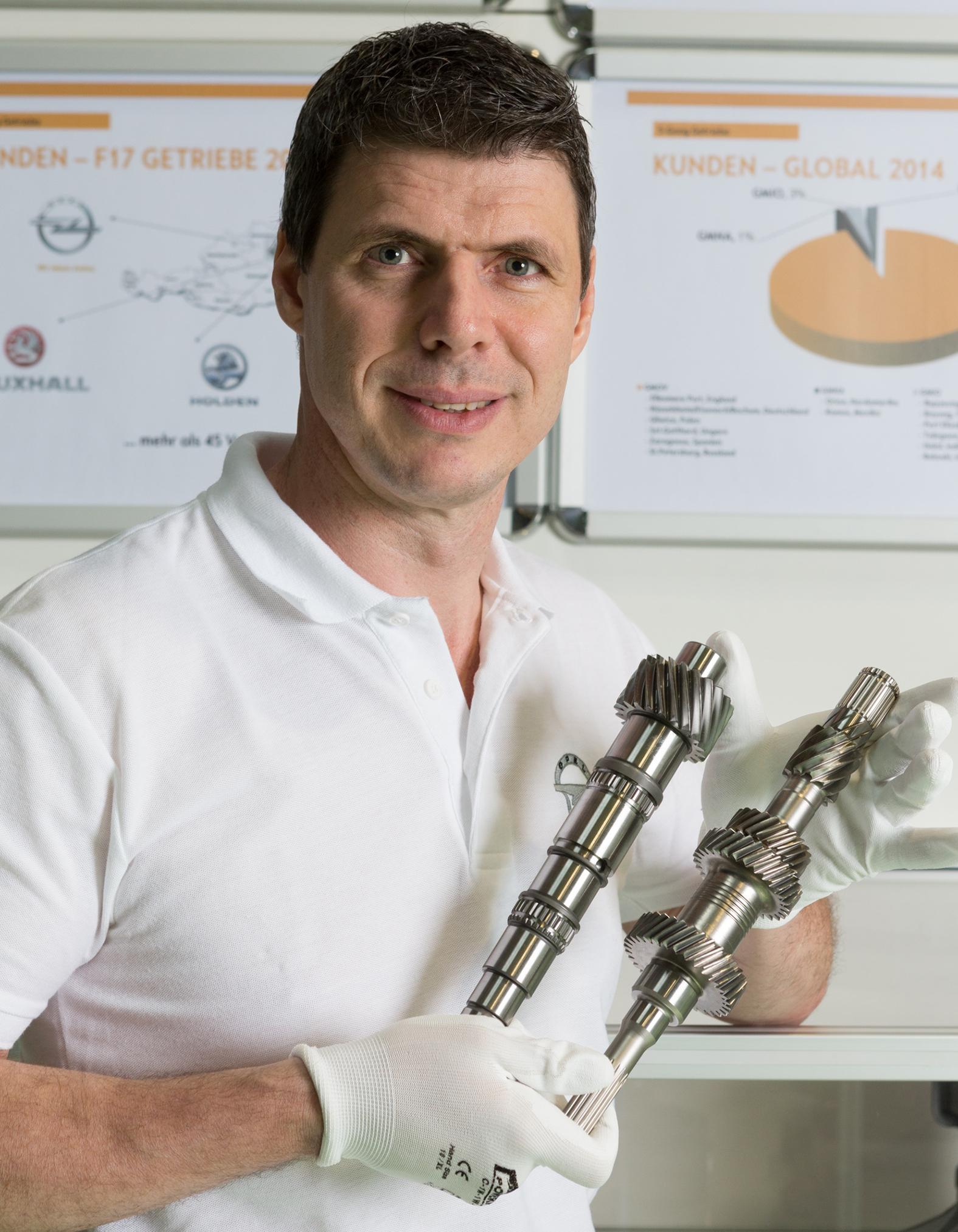
Peter Leitner/Instandhaltungskoordinator im F 17-Getriebebau demonstriert Zahnradblock und Hauptwelle.
Tüfteln und Tauschen
Also galten der Zahnradblock- und der Hauptwellen-Linie in den vergangenen drei Jahren konzentrierte Bemühungen. Mit beträchtlichen Erfolgen: Die Stück-pro-Stunde-Leistung konnte seit 2012 bis Ende 2014 um circa 30 Prozent gesteigert werden. In absoluten Zahlen: von 73 auf 97 beziehungsweise von 86 auf 103 Stück pro Stunde.
Diese Erfolge haben Auswirkungen auf die gesamte Produktivität des F 17-Getriebebaus. Das Geheimnis dahinter: ausgetüftelte Überholungsarbeiten an Engpass-Maschinen und das Austauschen altersschwacher Maschinen gegen neuere Modelle. Die konnten aus dem ehemaligen Bochumer Maschinenpark übernommen werden.
Sorgenkinder-Programm für den Zahnradblock
Zur Weisser-Maschine zum Ablängen und Zentrieren des Zahnradblocks sagt Leitner: „Das war unsere Engpassmaschine schlechthin.“ Er zählt die drei Hauptprobleme, die analysiert und erfolgreich behoben wurden, auf:
1. Die Messmaschine war falsch ausgelegt und musste umgebaut werden.
2. Ein hängen-gebliebener Span verursachte in der Messmaschine zehn Prozent Pseudo-Ausschuss. Die Bearbeitungsschritte wurden geändert – das brachte Abhilfe.
3. Ein Programmfehler hatte zur Folge, dass die Maschine Crash fuhr, und zerstörte wiederholt Maschinenteile. Umprogrammieren war hier die Lösung.
Bei einer fehleranfälligen Verkettung der Zahnradblock-Linie wurde eine neue Technologie der Antriebssteuerung implementiert. Neue Regler wurden vom Schaltschrank direkt zur Maschine versetzt. Außerdem wurden neue robustere Führungsschienen eingebaut. Oder die Position der Richtauflagen an der Richtmaschine ebendort wurde neu positioniert, so dass der Anteil an gerissenen Wellen und dadurch der Arbeitsausschuss reduziert werden konnte.
In der Zahnradblock-Linie gab es kaum eine Maschine, die nicht einer Optimierung unterzogen wurde. Hinzu kam noch ein schrittweises Austauschprogramm: In den Werksferien 2014 wurden zwei alte Fräsmaschinen durch neuere ersetzt, zu Weihnachten zwei Schabmaschinen. Im Frühjahr 2015 folgten vier Drehmaschinen und in den diesjährigen Werksferien soll noch eine Richtmaschine ersetzt werden.
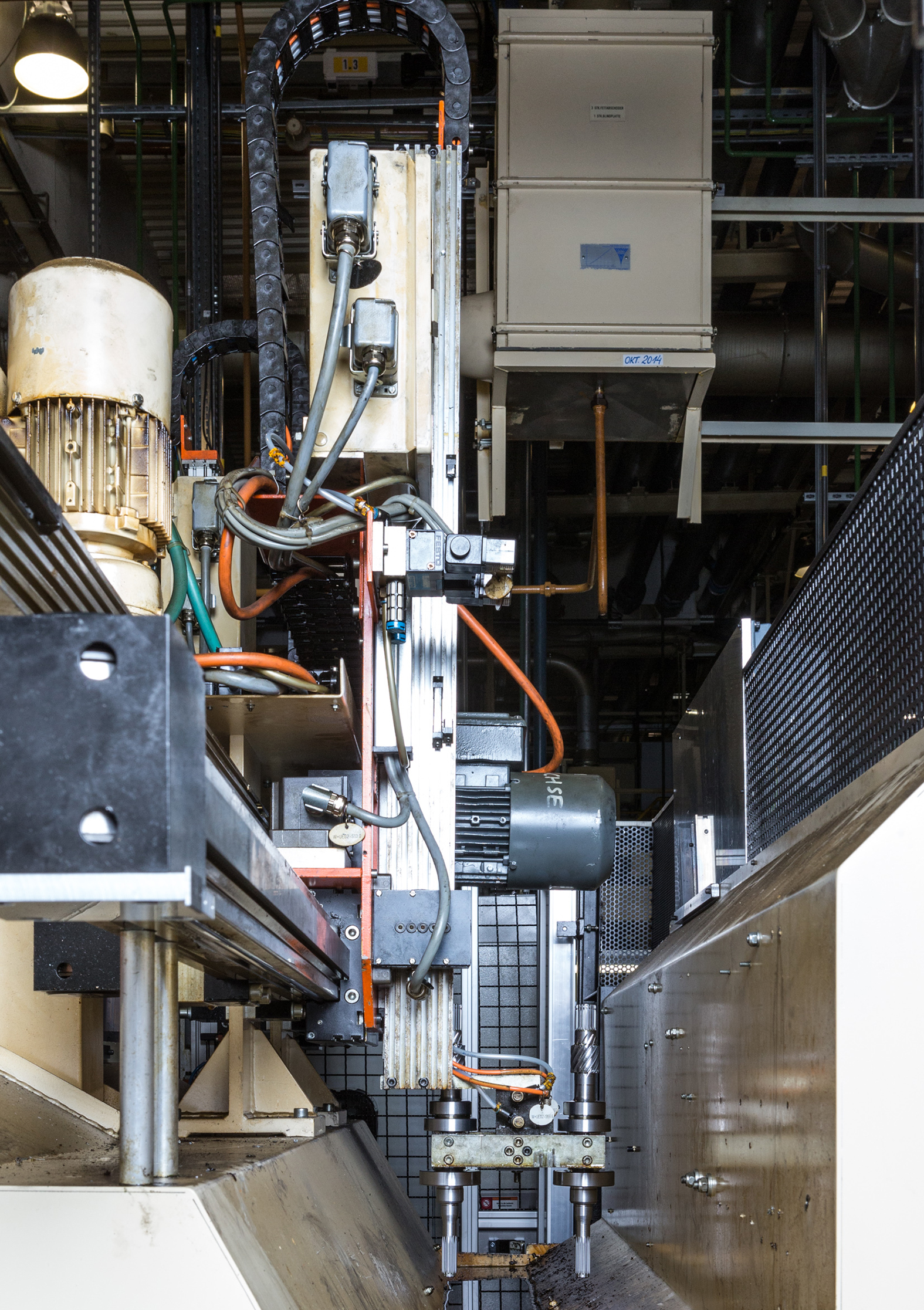
Neue mechanische Führung der Verkettung in der Zahnradblock-Linie.
Puffermanagement
„Das war das erste, was ich gemacht habe“, schickt Peter Leitner zu den Verbesserungen des Puffermanagements voraus – er ist seit März 2013 im F 17-Bereich tätig – und erklärt dessen Bedeutung: „Damit kann ich die Ergonomie und auch den Output wesentlich verbessern.“ Im End-of-Line-Puffer der Zahnradblock-Linie wurden gebrauchte Transportbänder aus Bochum eingebaut, beim End-of-Line-Puffer der Hauptwellen-Fertigung gelang es, den Pufferplatz auf das Dreifache zu vergrößern.
Verjüngungskur für die Hauptwelle
In der Hauptwellen-Linie überholten die Instandhalter die Baiker-Strahlmaschine bis ins letzte Detail. Alle mechanischen Einzelteile wurden akribisch serviciert und die Strahlschläuche zum besseren Tausch nach außen verlegt. „Da gab es viele Ablaufprobleme“, sagt Leitner. „Die haben wir durch die neue Teileanstellung beim Beladen der Maschine auf Null gesetzt.“
Last, but not least ersetzten in der Hauptwellen-Fertigung im Jahr 2014 zwei Powerhon-Maschinen vier Verzahnungsschleifmaschinen. Statt Schleifen und Honen in zwei Arbeitsgängen werden die Teile nun in einem Arbeitsvorgang bearbeitet. Für die dort beschäftigten Mitarbeiter bringen die neuen Anlagen beträchtliche ergonomische Verbesserungen: Statt jedes Teil wie früher sechsmal in die Hand zu nehmen reicht jetzt ein einziger Griff. Der Rest der Maschinen ist nun verkettet.
Verbesserungsprozess im Team
Begleitend zu den maschinellen Verbesserungen gab es seit 2012 auch noch KVP-Projekte; insgesamt 18 an der Zahl. Sie befassten sich unter anderem mit den Themen Arbeitssicherheit, Undichtheiten, Messplätze, Energie, Ergonomie und Standardisierung mit Schattenboards. Wozu Peter Leitner noch hinzufügt: „Hinter den Verbesserungen im F 17-Getriebebau stehen zwei wichtige Faktoren: Einerseits arbeiten wir hier alle gut zusammen. Wir sind ein motiviertes Team aus Produktion, Planung und Instandhaltung. Andererseits ist die wechselseitige Unterstützung zwischen M 20/32- und F 17-Getriebebau sehr wertvoll. So können wir das gemeinsame Wissen um Stärken und Schwächen nutzen, um eine positive Entwicklung voranzutreiben.“ Der Instandhaltungskoordinator fasst zusammen: „All das macht uns zuversichtlich, dass wir im F 17-Getriebebau bald das angepeilte Ziel von 105 Stück pro Stunde erreichen werden.“
Text: Kristin Engelhardt, Fotos: Stephan Huger