Pracowników działu elektrycznego naszego fabrycznego laboratorium można by w skrócie nazwać „Pogromcami wad” – podobnie jak prowadzących znany program w stacji Discovery.
– Może tylko nasze eksperymenty nie zawsze są tak spektakularne i widowiskowe jak ich – zastrzega skromnie Krzysztof Szmal, kierownik laboratorium. – Ale na pewno nie mniej ciekawe. Jego słowom przytakuje Michał Kowalski, jeden z dwóch inżynierów pracujących w „elektryce”.
– Robimy naprawdę interesujące rzeczy – opowiada.
– Takie, o jakich marzy się na studiach: zarazem oryginalne i pożyteczne. Oprócz Michała drugim inżynierem jest Grzegorz Smołka. Współpracują oni z czterema kolejnymi pracownikami działu: Adrianem Schwarzerem, Leszkiem Janiakiem, Zbigniewem Miklaszewskim i Mariuszem Opeldusem.
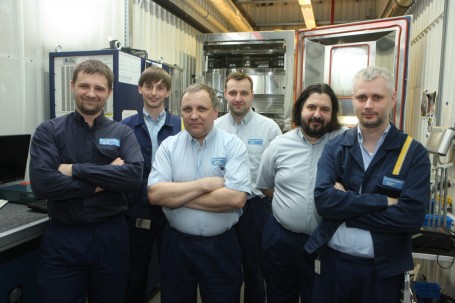
Od lewej: Mariusz Opeldus, Adrian Schwarzer, Zbigniew Miklaszewski, Leszek Janiak, Michał Kowalski, Grzegorz Smołka.
– W nasze ręce trafia rocznie grubo ponad 250 różnych części – tłumaczy Grzegorz Smołka. – I każdą z nich poddajemy bardzo surowym, precyzyjnym testom wytrzymałości i niezawodności. Jeśli któraś z nich ich nie przejdzie, nie ma prawa trafić na linię produkcyjną i wraca do dostawcy, by ten poprawił jej parametry. Potencjalne usterki, brak precyzji – to właśnie ich wykryciu ma służyć wysiłek laboratoryjnych elektryków. – Szukamy ich wszelkimi możliwymi metodami – opowiada Michał Kowalski. – Mamy do dyspozycji nowoczesny sprzęt, np.: oscyloskopy, zasilacze programowalne, karty pomiarowe, wzbudnik elektromagnetyczny, komory klimatyczne i wiele innych. Jesteśmy w stanie wywołać wibracje o przyspieszeniu 100 razy większym niż przyspieszenie ziemskie. Komora klimatyczna wytwarza ekstremalne warunki – temperaturę minus -75 stopni Celsjusza, albo przeciwnie 180 stopni na plusie. Komora może też mieć różny poziom wilgotności – od 0 do 100 procent. Testowne części muszą przejść wszystkie próby bez szwanku. Inaczej są odrzucane. – Tutaj nie ma przebacz, bo i w codziennej eksploatacji pojazd narażony jest na trudne warunki atmosferyczne – tłumaczy Grzegorz Smołka. – W komorze silnika temperatura 140 stopni nie jest niczym wyjątkowym. A z kolei części znajdujące się w kabinie pasażerskiej poddajemy próbom do +85 stopni C. Inaczej nie przekonamy się, czy naprawdę funkcjonują bez zarzutu zawsze i wszędzie. Czasami stosujemy też testy szoków termicznych – dana część może być wielokrotnie i szybko (w 5 sekund) przesuwana między komorą ciepłą (max +180 st C) a zimną (do – 75 st C), na zmianę wychładzając się i rozgrzewając. To dla niej naprawdę ekstremalne doświadczenie.
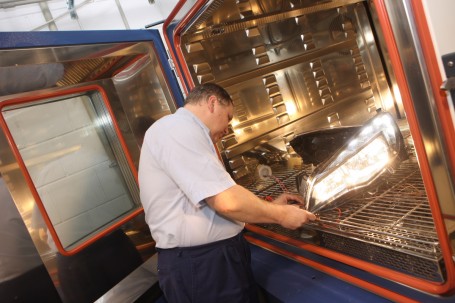
Części poddawane są ekstremalnym testom – elementy silnika muszą przetrwać temperaturę od -40 stopni Celsjusza do +140 stopni.
Oprócz komory klimatycznej, w laboratorium jest wiele innych gotowych urządzeń do badań. Jedno z nich pozwala określić rzeczywistą wydajność akumulatorów. – Świetnie ujawnia wady fabryczne baterii – zapewnia Adrian Schwarzer. – Dzięki staraniom Kierownictwa Quality już niedługo zaczniemy pracę z testerem do symulacji częstego rozruchu. W samochodach z systemem start-stop silnik jest uruchamiany i wyłączany bardzo często. I będziemy mogli ocenić, jak spisuje się w takich warunkach akumulator.
Mariusz Opeldus prowadzi do jednego z pomieszczeń, gdzie na stanowisku stoi… fragment samochodu z przednią szybą. Bez przerwy pracują na niej wycieraczki, usuwając pryskającą z dysz wodę. – Setki tysięcy cykli, zatrzymań, uruchomień… – wyjaśnia działanie mechanizmu. – Dopiero po nich można ocenić, czy wycieraczki i ich napęd trzymają jakość.
Niektóre testy trwają 10 dni, inne dłużej. Są i takie, które zabierają kilka minut, ale przygotowania do nich to wiele dni albo i tygodni. – Tak było, kiedy musieliśmy ocenić czy kierownica nie nagrzewa się nadmiernie – opowiada Grzegorz Smołka. – Musieliśmy umieścić na niej kilka czujników, stworzyć metodę badawczą, całe zaplecze zbierania wyników. Później zebraliśmy ogrom danych w bardzo krótkim czasie. Bywa tak, że jedno badanie daje nam 8 milionów próbek! Analiza trwa bardzo długo, ale jest szczegółowa. Dzięki niej możemy tworzyć wykresy, porównywać starsze dane z nowszymi. Sprawdzać, czy jakość części się poprawiła, czy pogorszyła i wtedy interweniować.
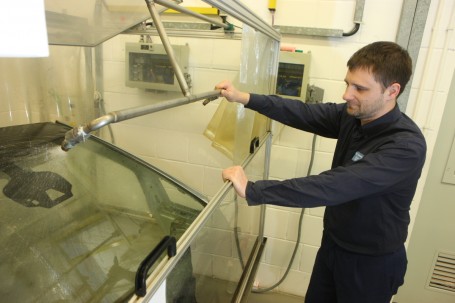
Ile są w stanie wytrzymać silniki wycieraczek? Testujemy je włączając i wyłączając tysiące razy. Muszą usunąć setki litrów wody z szyby, by przejść pomyślnie testy.
Do laboratorium trafiają części ze wszystkich modeli produkowanych w Europie. – O, tu badaliśmy trwałość zaczepów w Cascadzie – pokazuje jedno z urządzeń Leszek Janiak. – A tam prędkościomierz z Astry. Nie tylko sprawdzamy elementy przed wprowadzeniem do produkcji, ale i na bieżąco, w jej trakcie. To ma zapobiec pogorszeniu się jakości. Laboratorium pracuje też na potrzeby zgłaszane od pracowników innych działów. Gdy nagle coś zaczyna szwankować, robi się weryfikację kłopotliwego procesu lub elementu. – Pracy nigdy nam nie brakuje – mówi Zbigniew Miklaszewski. – Bo GM dba o jakość. A bez jej sprawdzania nie sposób ją zachować na wysokim poziomie.
Grzegorz Smołka jest inżynierem specjalizującym się w pomiarach elektrycznych, Michał Kowalski– mechatronikiem i elektroenergetykiem, ale obaj muszą być też programistami.
– Aby sprawdzić pojedynczy podzespół elektroniczny, który w samochodzie komunikuje się z pozostałymi sterownikami poprzez sieć CAN lub LIN, trzeba je zasymulować – tłumaczy Michał. Wykorzystujemy do tego oprogramowanie, które symuluje i wysyła sygnały tak, jak to się dzieje w samochodzie. Nierzadko trzeba napisać fragment programu, który wywoła jakąś funkcje cyklicznie i umożliwi sprawdzenie, czy badana część działa prawidłowo.
Gdyby jednak trzeba było sprawdzić coś bezpośrednio w samochodzie, nie ma z tym też problemu – jest specjalny garaż do badań.
– Ale tak naprawdę, chyba każdemu w firmie zależy, by wszystko funkcjonowało bez zarzutu i byśmy nie musieli wystawiać złych opinii częściom czy dostawcom – podsumowuje Krzysztof Szmal. – Sama świadomość, że jesteśmy i czuwamy, powinna uczulać ich na nasze wysokie wymagania!
15 – tyle lat istnieje laboratorium
1000 A – maksymalna symulowana wartość prądu rozruchowego dla testowanego akumulatora
100 000 S/s – maksymalna liczba pobranych próbek pomiarowych w ciągu sekundy
250 – tyle mniej więcej części rocznie poddaje się różnym testom elektrycznym w laboratorium