“Our department is a great place for students to get an insight into the Opel universe because we are located at the heart of the vehicle plant, interacting directly with suppliers and developers.”
– Sönke Ohls –
The first three days are especially difficult. Looking back, Margarita Grinberg describes her first few days as a whirlwind of information. She shook hands with what felt like 50 people whose names she could barely register, and there was a seemingly endless list of administrative tasks to get on top of. Fetching her work identification card, activating her PC account, procuring her tool belt and writing materials – not to mention what actually goes on in the plant itself, where Opel’s Insignia and Zafira Tourer are made. Everything felt new and unfamiliar – even finding the coffee machine!
Margarita Grinberg would leave the headquarters in Rüsselsheim in the evening feeling overwhelmed but in high spirits. This is how the industrial engineering student describes her entry into the six-month internship at Opel several weeks after the fact. This is her first time working for a company, and she says she learned two important lessons at the beginning of the internship. “First, Opel is a truly enormous organization. Second, making automobiles is a highly complex process.” She had already known these things, of course, “but once you’re in the thick of it, the experience is far more intense than you expected.”
Margarita Grinberg
The 27-year-old student from Mainz is in her eighth semester of studying industrial engineering, with a specialization in mechanical engineering, at the University of Applied Sciences Bingen. She decided to apply for an internship at Opel after attending a talk given by Opel’s Director of Lighting Technology Ingolf Schneider, on the subject of IntelliLux LED matrix light.
“Fascinating people and ground-breaking technology – these are what awakened my curiosity.”
Three Questions For…
– Carsten Brust –
Manager Talent Acquisition
Mr. Brust, in what ways does Opel help students learn about the company?
Our interns get more than just a superficial glance. Every year, up to 400 students work on their theses or do an internship at Opel as part of their bachelor’s or master’s degrees. A 35-hour week is typical, whether they stay for two months or six months.
How do you decide if someone has the potential to contribute to Opel as a full-time employee after their studies?
We first receive notification from the people who directly supervise the interns. They let us know if they think someone stands out with their technical abilities. We then invite the candidate for an interview, with the aim of understanding his or her behavior and conduct. Among other things, we try to get an idea of the person’s social skills and figure out if the candidate would be a suitable fit for the company. If they are, we place them in our talent pool. There are currently 75 former interns in the talent pool who could potentially become members of Opel.
What does it take for a student to make a start at Opel?
English fluency is mandatory, in addition to technical knowledge. Furthermore, we are looking for someone who is always hungry for new knowledge – someone who lives and breathes automobiles.
How to apply for an internship
meinpraktikum.de
faircompany.de
or on the Career page of the Opel website.
Sönke Ohls nods in agreement. Ohls is supervising Grinberg’s internship and is the director of the Electric, Electronic and Air Conditioning department in the Quality Engineering division. He and his three-person team are responsible for the quality of all electrical components that are made in Rüsselsheim. “Our department is a great place for students to get an insight into the Opel universe,” says Ohls, “because we are located at the heart of the vehicle plant, interacting directly with suppliers and developers.”
Here, you come into contact not only with representatives from other companies but also with assembly specialists, designers, and plant management. It is obvious to Ohls what the benefits of this internship are: “At the vehicle plant, you are a direct witness and participant, taking care of all the requirements of all the departments in our global organization in order to bring a car into existence.” The contacts in the Quality Engineering division, whether they are suppliers or fellow workers at Opel, come from many different countries. The English language and the use of specialist abbreviations such as ‘REC’ (Rear Electrical Center – the security box in the trunk) quickly become second nature.
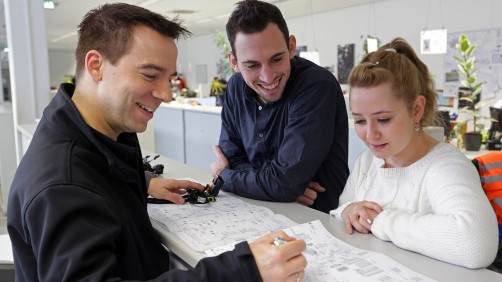
In the office (from left to right): Ohls, Steier, and Grinberg compare the measurements with specifications in the technical diagram.
From databases and e-mails to phone conferences and meetings: there are numerous channels in the Quality Engineering division for exchanging information. Time and again, the primary focus is on the assembly line – on how to bring theory and practice together most effectively. According to Ohls, the interns are put in charge of their own working areas. They learn by doing and by making mistakes, “but without impeding the operational processes.” The aim is to allow the budding engineers to learn how to work independently and to bring in their own ideas. “It is crucial, however,” says Ohls, “that the supervisor shows trust and clearly defines the limits.”
Jan Steier
The 25-year-old lives in Mainz and studies mechatronics engineering at the Technical University of Darmstadt, where he is currently doing his master’s degree in the field of automotive mechatronics. He found out that Opel was offering an interesting internship through ‘konaktiva,’ one of the biggest student-organized job fairs in Germany.
He describes being selected for Opel’s talent pool as “an honor and a serious career option.”
“During the second half of the internship, I began to notice how comfortable I felt with the tasks and people I was working with.”
– Jan Steier –
The student interns are fully integrated into the day-to-day business, which has led to optimal results: The Quality Engineering division receives the support that it needs, and the interns don’t have to worry about idling the day away without any work to do. “The concept is unfolding far better than we expected,” says Ohls. “A two to four week overlap in the internships means the leaving student can show the ropes to the incoming one.”
Jan Steier was the first student to complete the internship. “I spent most of the first three months observing, asking questions, and learning,” the mechatronics engineering student says. “During the second half of the internship, I began to notice how comfortable I felt with the tasks and people I was working with.” A good example is the PowerPoint presentations that Steier had to frequently give during meetings with other departments.“ At first, I needed three hours for preparation, but as time went by I would only require just a fraction of the time.” The reason was that he had “learned how to refine and adapt information to new contexts.” According to Steier, such learning processes are extremely valuable when working for multifaceted companies like Opel.
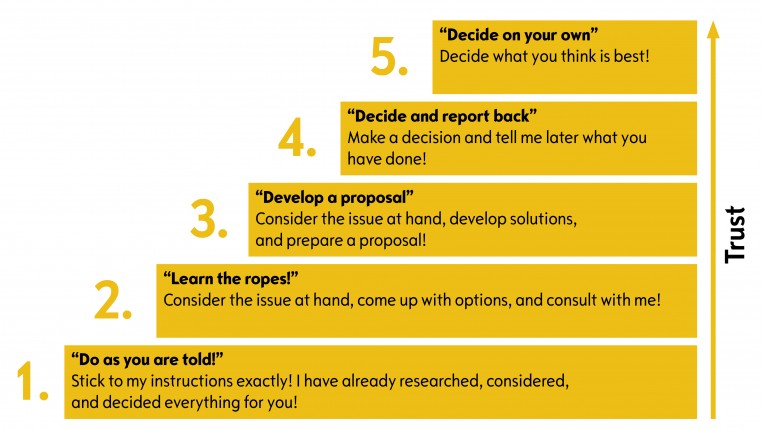
How much trust and autonomy should you give an intern? Sönke Ohls swears by the ‚five levels of delegation,‘ which is a management method created by Bernd Geropp, a management coach based in Aachen, Germany.
“This company not only makes remarkable automobiles, but it is also fun to work for. And I don’t want to omit the fun from my career.”
– Margarita Grinberg –
For Steier, the benefits of the internship have been twofold. Not only did he return to his studies with a vast amount of practical experience, he also ended up receiving a recommendation to be placed into Opel’s ‘talent pool’ where highly promising interns are kept on file. His supervisor had recommended him. “Of course, comprehension skills, intelligence, and personality all play an important role,” says Sönke Ohls, “but an unwavering curiosity is the quality we are looking for the most.”
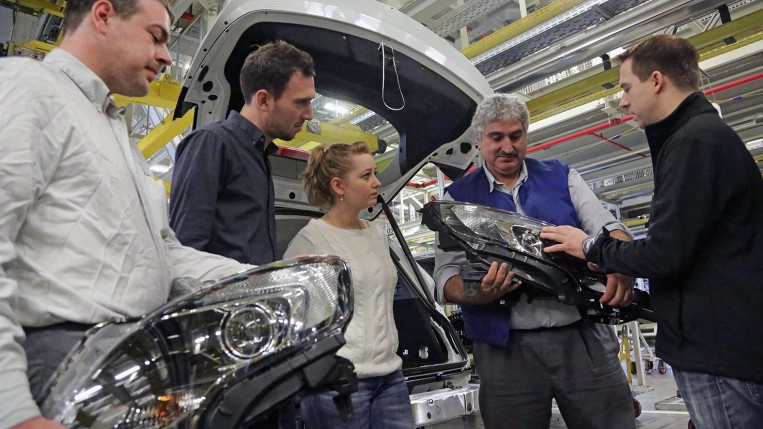
Getting to grips with the technology: Team leader Christian Hellmeister, Jan Steier, Margarita Grinberg, supervisor Ali Yanik, and engineer Sönke Ohls (from left) exchange notes on the production line.
Margarita Grinberg hopes that she will also manage to secure a place in the talent pool during the upcoming months. She says she can imagine being very happy working for Opel: “This company not only makes remarkable automobiles, but it is also fun to work for. And I don’t want to omit the fun from my career.”