“These innovations directly influence the work undertaken by employees in the production facilities. The goal is to reduce the number of work steps that are challenging from an ergonomic perspective.”
– Rudi Spiess –
Executive Director of Production Planning
Would-be visitors are usually denied access to GME Pre Production Operations (PPO) – 365 days a year, without exceptions. This division builds future Opel models with hardware for the first time at the International Development Center once they have left the development phase.
The division includes individual subsections which reflect all of the work steps that are undertaken later on in the production plants. Before actual series production commences, PPO validates individual components, simulates and optimizes later work processes, identifies and addresses potential future problems, and qualifies employees.
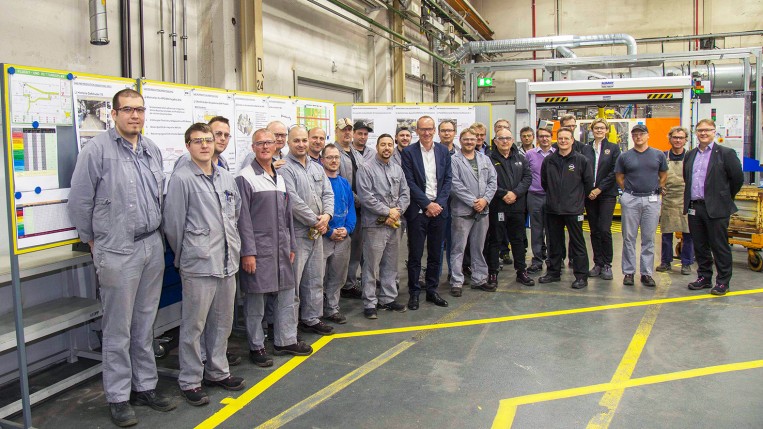
Group photo with the boss: The component manufacturing employees who work in skeleton construction in I13 together with Dr. Karl-Thomas Neumann, the Head of PPO Skeleton Construction Ralf Wolk, and Rudi Spiess, Executive Director of Production Planning.
Outsiders rarely get to take a look behind the scenes at the work undertaken by the 500 employees in this secretive division, which falls under manufacturing, or, more precisely, production planning. Last week, though, a rare opportunity arose: GM Executive Vice President & President Europe Dr. Karl-Thomas Neumann visited GME Pre Production Operations employees in order to personally put the new automated welding cells in chassis prototype construction into operation.
PART OF THE QUALITY INITIATIVE
These two high-tech devices create spot welds on sub-assemblies and are part of the Opel quality initiative. PPO has introduced several projects to simulate workflows and processes in subsequent manufacturing even more precisely. These projects include the two new welding cells – new laser welding, laser wave soldering cells, and an automatic welding station will follow this year.
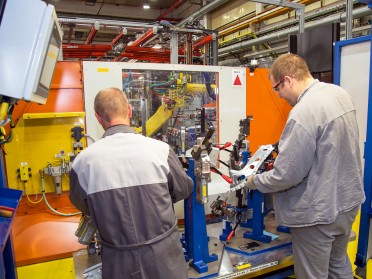
The new welding cells ensure that component manufacturing in skeleton construction mirrors work processes in the production facilities even more precisely.
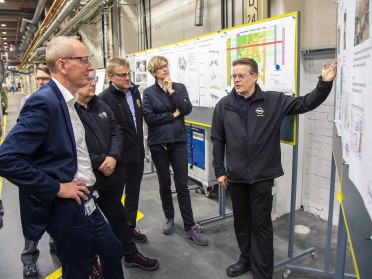
The complete package: Ralf Wolk explains the various innovations that will increase flexibility and capacity in PPO skeleton construction.
THE GOAL: MORE ERGONOMIC OPERATIONS
There are many good reasons behind introducing these innovations. They will allow series processes that arise later on in the manufacturing process to be simulated in the best possible way, and can preliminarily address problems that might occur at these later stages. “The new systems increase flexibility and capacity across PPO skeleton construction,” explains Ralf Wolk. Employees working on subsequent series production will also benefit from these innovations: “One of our main focuses is on reducing the number of work steps that are challenging from an ergonomic perspective.”
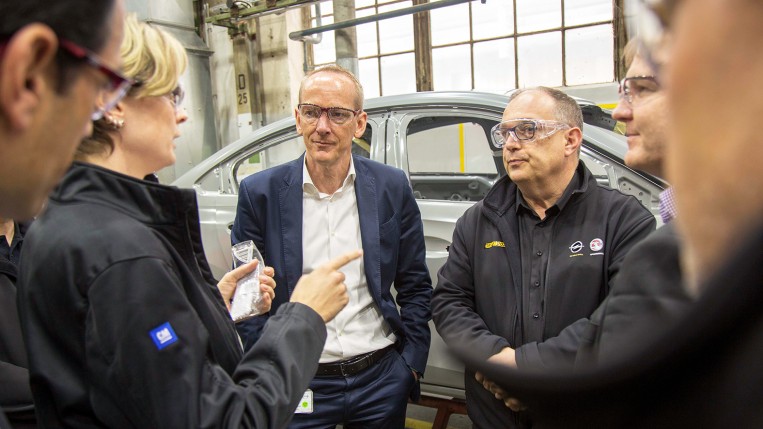
Talking shop: Dr. Karl-Thomas Neumann with Quality Manager Juliane Müller and PPO Director Ziemowit Zakrzewski.
Last update May 2016