- Begutachten ein neues Presswerkzeug: Paul Hüttenberger, Thomas Schäufle, Anel Bajric, Danny Rohrig und Andreas Henke.
„Unsere Presswerkzeuge sind präziser gefertigt denn je – und wir liefern schneller denn je.“
– Andreas Henke –
Abteilungsleiter Zentrale Funktionen
in den Zentralwerkstätten
In den Rüsselsheimer Zentralwerkstätten hat eine neue Zeitrechnung begonnen. Der Presswerkzeugbau, neben dem Anlagen- und Vorrichtungsbau das Kerngeschäft des Bereichs, ist nun in der Lage, auch Werkzeuge für große Außenhautteile bis 4,50 Meter Länge zu fertigen – beispielsweise für die komplette Seitenwand eines Insignia. Und das in einer Präzision, wie sie bislang unterm eigenen Unternehmensdach in diesen Dimensionen nicht möglich war.
GROSS UND INTELLIGENT
Verantwortlich für diesen Quantensprung ist die neue „Heynuform 4000“, ein Fünf-Achsen-Fräsbearbeitungszentrum, das nicht nur durch seine imposante Größe besticht, sondern auch durch seine Intelligenz: Es ist in der Lage, fünf Fräsköpfe und bis zu 200 Werkzeuge selbstständig zu wechseln. Die „Heynuform“ bleibt nicht lange allein. Im Oktober wird noch eine zweite, identische Anlage in Betrieb genommen, um Europas Presswerke so schnell, schlau und genau wie nie zu beliefern.
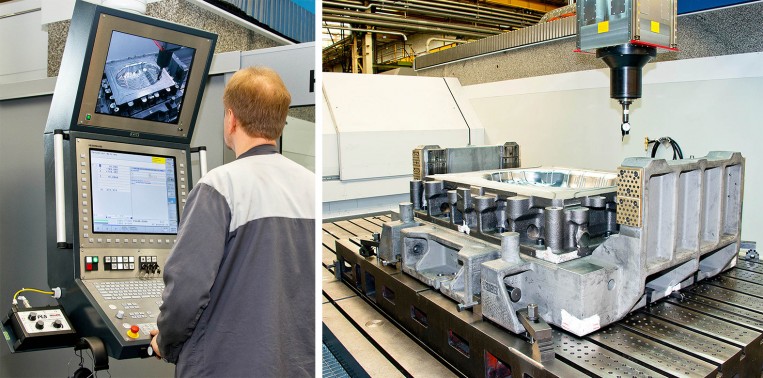
Eine neue Zeitrechnung: Die „Heynuform“ fräst nicht nur, sondern sie scannt – via Monitor hat Thomas Schäufle alles im Blick.
Thomas Schäufle ist gelernter Werkzeugmacher – und hat sich im Lauf seiner Jahre in den Zentralwerkstätten auch auf das Steuern und Programmieren von komplexen Anlagen spezialisiert. „Maschinen, die vollautomatische Werkzeugwechsel beherrschen, haben wir einige in unserem Bereich – aber die Heynuform toppt alles.“ Schäufle hat zusammen mit neun Kollegen eine umfassende Vor-Ort-Schulung durchlaufen, um mit der neuen Anlage vertraut zu werden. „Da haben wir viel Neues lernen müssen – das war ungefähr so, wie sich ein neues Computer-Betriebssystem anzueignen. Aber es war auch ungeheuer spannend.“
SCANNEN UND ABGLEICHEN
Auf unseren Bildern arbeitet Thomas Schäufle gerade keinen Fräsauftrag ab: Mit Hilfe eines am Fräskopf angebrachten Messtasters scannt Thomas Schäufle ein Bodenteil, um die Daten mit denen aus der Simulation abzugleichen. „Die Daten melden wir dann in die Entwicklung zurück. So können Theorie und Praxis können voneinander profitieren – und wir die Teile kontinuierlich weiter verbessern.“
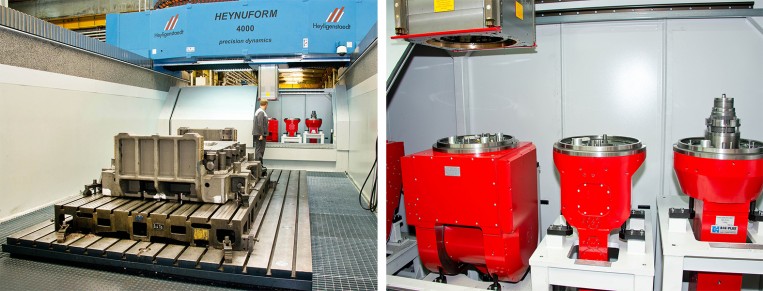
Fräskopf wechseln? Kein Problem: Die Austauschobjekte stehen bereit – und die Maschine holt sie sich selbst.
„Wir haben einige Maschinen in den Zentralwerkstätten, die vollautomatische Werkzeugwechsel können. Aber die Heynuform toppt alles.“
– Thomas Schäufle –
zuständig für Steuerung und Programmierung
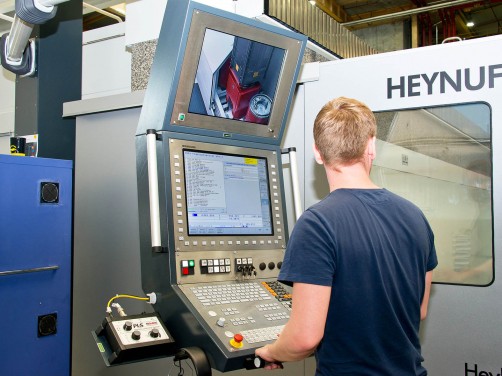
Alles in Ordnung? Auch wenn der Monitor jedes Detail zeigt, lohnt auch schon mal der direkte Blick durchs Fenster.
Die „Heynuform“ kann nicht nur Presswerkzeuge für besonders große Außenhautteile fräsen – es ist auch möglich, Formen herzustellen, mit denen linke und rechte Teile, Türen etwa, gleichzeitig gepresst werden können. Das ermöglicht nicht nur ein schnelleres Abarbeiten von Aufträgen: „Wir kommen damit auch dem Trend in unseren europäischen Werken entgegen, immer mehr Doppelteile zu fertigen“, erklärt Knut Mittendorf, in den Zentralwerkstätten zuständig für neue Technologien. „Zwei Teile in einer Presse fertigen zu können, das ist nicht nur produktiver, es spart auch Platz.“
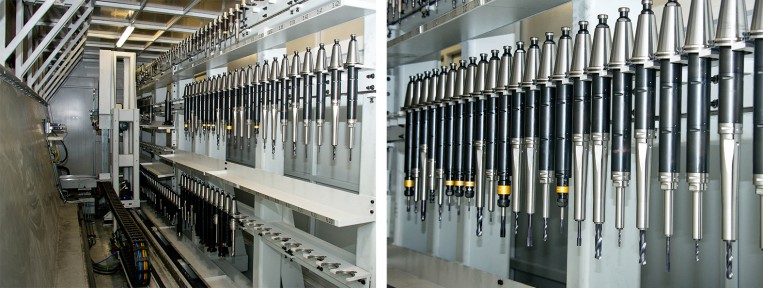
In Reih und Glied: Rund 200 Werkzeuge stehen zum vollautomatischen Wechsel bereit.
Der fahrbare Querträger der „Heynuform“, an dem der Fräskopf angebracht ist, bringt allein rund 40 Tonnen auf die Waage. In seiner für Opel angefertigten Anlage präsentiert Hersteller Heyligenstädt eine Weltneuheit: Links und rechts geben zwei monolithische Granitblöcke dem Gehäuse Stabilität – jeder ist zwölf Meter lang und 20 Tonnen schwer.
HITZEFREI UND OHNE ERSCHÜTTERUNGEN
„Um hochpräzise im Tausendstel-Millimeter-Bereich arbeiten zu können, muss die Anlage absolut erschütterungsfrei arbeiten“, erklärt Andreas Henke, Abteilungsleiter Zentrale Funktionen in den Zentralwerkstätten. „Außerdem hat die Erfahrung gezeigt, dass Granit über eine bessere Wärmeleitfähigkeit verfügt als Beton – und über Gebühr erhitzen darf sich unser Fräsbearbeitungszentrum schließlich auch nicht.“
Schicht im Schacht: Der Fräskopf liefert den Messtaster wieder im Magazin ab – vollautomatisch.
„Doppelteile wie zum Beispiel Türen gleichzeitig in einer Presse fertigen zu können, ist nicht nicht nur produktiver, sondern spart auch Platz.“
– Knut Mittendorf –
zuständig für Neue Technologien
in den Zentralwerkstätten
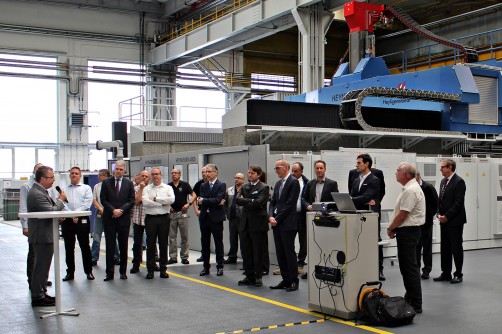
Kleine Feierstunde zur Eröffnung: Die Zentralwerkstätten führen dem Opel-Management, darunter Opel-Chef Karl-Thomas Neumann, die neueste Errungenschaft vor.
Auch dem Opel-Management das neue Fräsbearbeitungszentrum einmal vorzuführen, war für die Zentralwerkstätten natürlich Ehrensache. „Die Entscheidung der Geschäftsleitung, in diese beiden Anlagen investieren, war schließlich auch ein Bekenntnis zum Presswerkzeugbau unterm eigenen Unternehmensdach“, freut sich Andreas Henke. Was auch absolut Sinn mache: „So können wir uns besser denn je mit den Simulationsexperten in der Entwicklung und unseren Presswerken in ganz Europa vernetzen – und noch schneller Presswerkzeuge herstellen, die präziser denn je gefertigt sind.
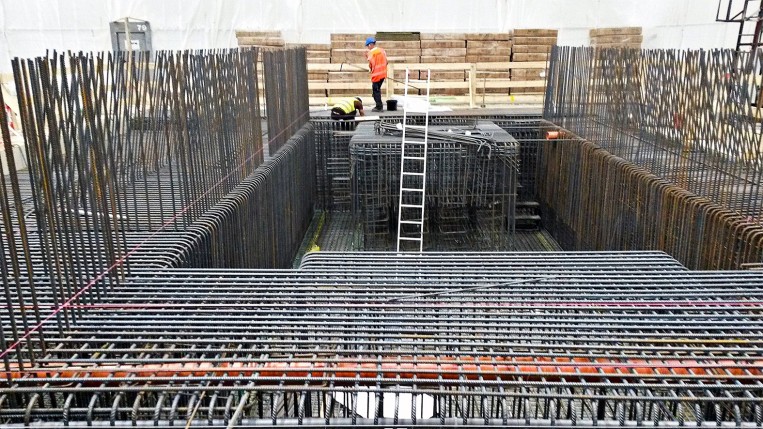
Um hundertprozentig erschütterungsfrei arbeiten zu können, braucht die Anlage ein solides Fundament. Vier Meter tief war die Grube, die für die „Heynuform“ ausgehoben werden musste. Gefüllt wurden sie mit 510 Kubikmeter Beton und 70 Tonnen Stahl. Das Fundament für den „Zwilling“, der im Oktober in Betrieb geht, ist parallel entstanden.