- Michael Lackner/Leiter Manufacturing Engineering M 20/32 und Christian Bartonek/Leiter Manufacturing Engineering F 17 mit ihren Werkzeugplanern (v.l.n.r.): Michael Lackner, Franz Jantzer, Christian Glasner, Jörg Hertel, Christian Bartonek.
Wenn bei Opel Wien von Werkzeug die Rede ist, sind Schleifscheiben, verschiedenste Bohrer, Spannfutter, Wendeplatten und dergl. gemeint. Also hochspezialisierte Hilfsmittel zum Schleifen, Bohren, Drehen, Fräsen, Honen – die natürlich ihren Preis haben. Je länger so ein Werkzeug durchhält, umso besser für die Produktionskennzahlen und das Budget.
Wenn Härte entscheidet
Einsparungen bei den Werkzeugkosten lassen sich nur mit viel Know-how und ausgeklügelten Verbesserungsprozessen erzielen. Wie zum Beispiel bei CBN-Wendeplatten, die zum Bearbeiten gehärteten Stahls verwendet werden. CBN bezeichnet das Material, mit dem gearbeitet wird: kubisches Bornitrid, das zweithärteste Material nach Diamant.
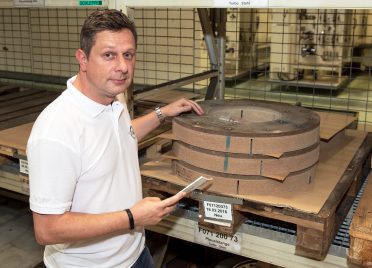
Werkzeugplaner Jörg Hertel mit Schleifscheiben.
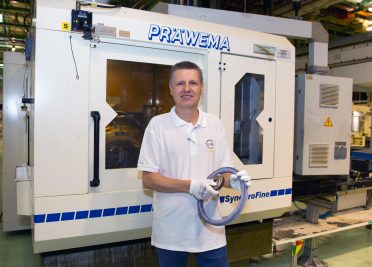
Werkzeugplaner Christian Engl vor einer Honmaschine mit einem Gangrad und einem Honring in der Hand.
Werkzeugplaner Franz Jantzer erzählt: „Wir setzen dieses teure Werkzeug dazu ein, um beim 3. und 4. Gang des F 17-Getriebes einen Durchmesser zu bearbeiten und eine scharfe Kante zu entfernen, damit dort die Kupplungsverzahnung angebracht werden kann. Die Mitarbeiter in der Linie hatten die Idee, dass man das Teil doch schon in der Weichbearbeitung entsprechend bearbeiten könnte.“
Gesagt, getan. Im vergangenen Jahr wurde die Verbesserung umgesetzt: das CBN-Werkzeug „plagt“ sich jetzt weniger und hat eine höhere Standzeit. Das bringt eine jährliche Einsparungs-Ausbeute von 23.000 Euro.
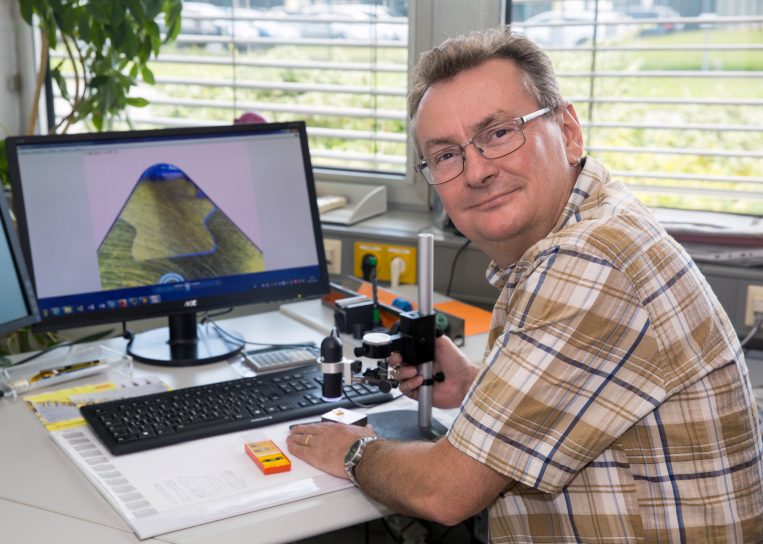
Werkzeugplaner Franz Jantzer vor der Detailansicht einer Wendeschneidplatte auf dem Bildschirm.
Schleifkörner wie Haifischzähne
Bei der Bearbeitung des Pleuels für den Flex-Motor kommen nun Schleifscheiben in völlig neuer Technologie zum Einsatz. 3M, der Hersteller, hat drei Jahre lang an der Entwicklung des innovativen keramischen Schleifkorns gearbeitet. Das Cubitron II-Korn hat – im Gegensatz zum unregelmäßig geformten Vorgänger – die Form dreieckiger Zähne. Schleifprodukte mit diesem Korn „schneiden durch Metall wie kleine Messer und schärfen sich während des Schleifprozesses selbst“. So nachzulesen auf der 3M Website.
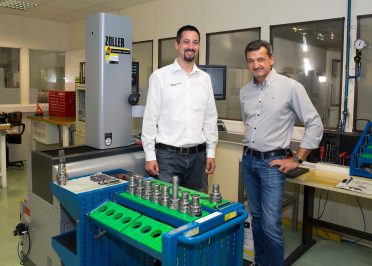
Michael Lackner (l.) und Christian Glasner im Einstellraum vor Mess-Werkzeugen, Bohrern und Reibahlen.
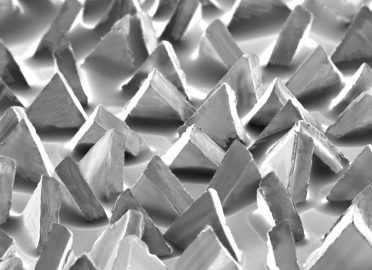
Neuartige Schleifkörner in Großaufnahme: Cubitron II setzt neue Maßstäbe hinsichtlich Zerspanleistung und Standzeit. (Foto 3M)
Werkzeugplaner Jörg Hertel erklärt dazu: „Unsere Aufgabe als Werkzeugplaner ist es mit den Herstellerfirmen in Kontakt zu bleiben, um solche Innovationen für den Einsatz in unserer Fertigung zu prüfen.“ Im speziellen Fall brachte der Wechsel zur neuen Technologie eine Standzeiterhöhung der Schleifscheiben um mehr als das Siebenfache – von 30.000 auf 225.000 Teile je Scheibensatz – und Kosteneinsparungen um 60 Prozent.
In anderen Fällen wurden die Lieferanten gewechselt. Oder andere Lösungen entwickelt. Summa summarum ergaben sich im Jahr 2015 aus Werkzeugverbesserungen Einsparungen in Höhe von 468.000 Euro.
Fortsetzung folgt
Die Werkzeugplaner sind an weiteren Verbesserungen dran; Schritt für Schritt. Zunächst in Gesprächen mit den Lieferanten, dann durch Testen von Versuchswerkzeugen – in Absprache mit Produktion und Instandhaltung – und durch Erproben neuer Abläufe. Sind die Tests zur Zufriedenheit gelaufen, erfolgt die Umstellung: der Einkauf wird beauftragt und die Dispositionsparameter neu definiert. Gleichzeitig bleiben die neuen Werkzeuge weiterhin unter strenger Beobachtung – die Qualität darf auf keinen Fall leiden! Die gute Nachricht: Auch in diesem Jahr konnten bereits erfreuliche Einsparungen umgesetzt werden.
Eine besondere Rolle haben die Werkzeugplaner, wenn es um Produktänderungen und Projekte geht: Ein neues Design braucht eben auch ein neues oder zumindest ein modifiziertes Werkzeug, das mithilfe von Versuchen entwickelt wird. Um dieser Aufgabe noch besser nachkommen zu können, sind die Werkzeugplaner seit Anfang Juli bei Manufacturing Engineering angesiedelt.
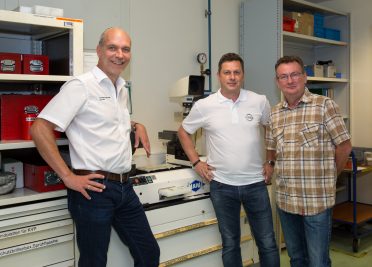
Gute Laune bei den Werkzeugplanern (v.l.n.r.): Christian Bartonek, Jörg Hertel, Franz Jantzer.