Die vierte industrielle Revolution versteckt sich hinter der metallischen Fassade des drei Mal drei Meter großen Gehäuses. Denn die mit modernster Informations- und Kommunikationstechnologie ausgestattete Produktion, in der Menschen und Maschinen – weltweit vernetzt – zusammenarbeiten, ist längst nicht mehr nur Vision, sondern in einigen Unternehmensbereichen von Opel bereits Wirklichkeit geworden, aktuell im Strukturentwicklungslabor (SDL) Chassis des Internationalen Technischen Entwicklungszentrums (ITEZ). In dem Gehäuse verbirgt sich ein neuer Prüfstand für Bremsgeräusche; er eröffnet den Ingenieuren im ITEZ-Direktionsbereich Vehicle Integration bislang ungekannte Möglichkeiten. Und erfüllt alle Voraussetzungen der „Industrie 4.0“.
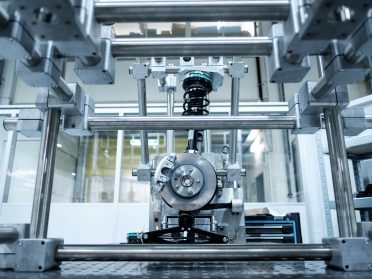
Solo für zwei: Federbein und Bremsscheibe lassen sich testen, als ob sie in einem kompletten Fahrzeug „draußen“ unterwegs wären.
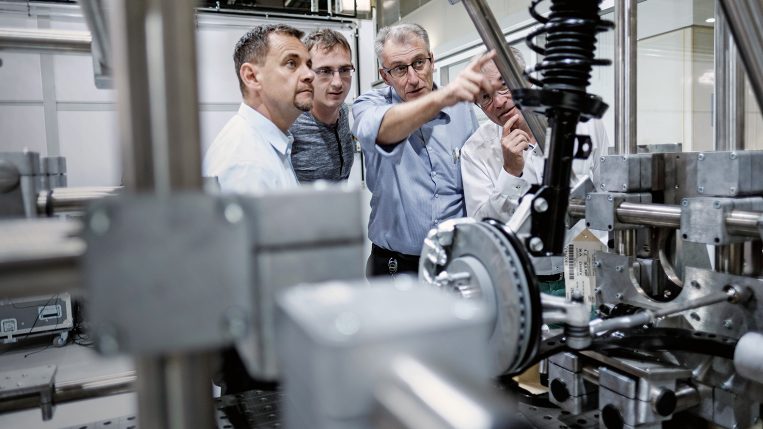
Auf die Details kommt es an: Thomas Neff, Philipp Penther, Robert Thomas Bender und Klaus Osterhage (v.l.) beraten sich.
„Wir sind nun erstmals in der Lage, Bremsgeräusche an den entsprechenden Komponenten reproduzierbar zu erzeugen und objektiv zu analysieren, ohne dazu ein komplettes Fahrzeug zu benötigen“, erklärt Projektleiter Robert Thomas Bender. „Gleichzeitig können wir in der Prüfkammer sämtliche Klima- und Temperaturprofile nachempfinden, die es auf der Welt gibt.“ Im Klartext: Bremsscheiben, Radlager oder andere Elemente einer Bremsanlage werden auf bis zu 2.200 Umdrehungen pro Minute beschleunigt und gebremst, Mikrofone, Laser und Sensoren zeichnen die dabei entstehenden akustischen Schwingungen auf – und das bei Temperaturen zwischen minus 30 und plus 50 Grad sowie Luftfeuchtigkeitswerten zwischen fünf und 95 Prozent.
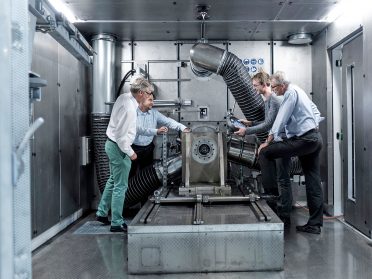
Ohne Lenkrad und Asphalt: So sehen Tests zur Bremsgeräuschentwicklung heute aus.
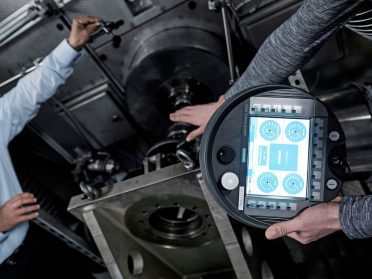
Mobiles Messen: Das Datenaufzeichnungsgerät liefert alle relevanten Informationen zur getesteten Komponente.
Kürzere Entwicklungszeiten
„Früher haben wir bei Opel die Bremsengeräuschentwicklung ausschließlich durch ausführliche Tests mit Fahrzeug-Prototypen durchgeführt, um vergleichbar zuverlässige Ergebnisse zu erhalten“, erklärt Laborleiter Klaus Osterhage. Doch Prototypen sind bekanntlich teuer, gleichzeitig werden die Entwicklungszeiten, die der Markt fordert, immer kürzer.
Der neue Prüfstand trägt somit zu einer schnelleren und kostengünstigeren Fahrzeugentwicklung bei. „Wir können auch noch in der Entwicklung befindliche Muster prüfen, um herauszufinden, wo und inwieweit diese noch weiter optimiert werden können“, ergänzt Testingenieur Philipp Penther. Auch das war früher wesentlich aufwendiger.
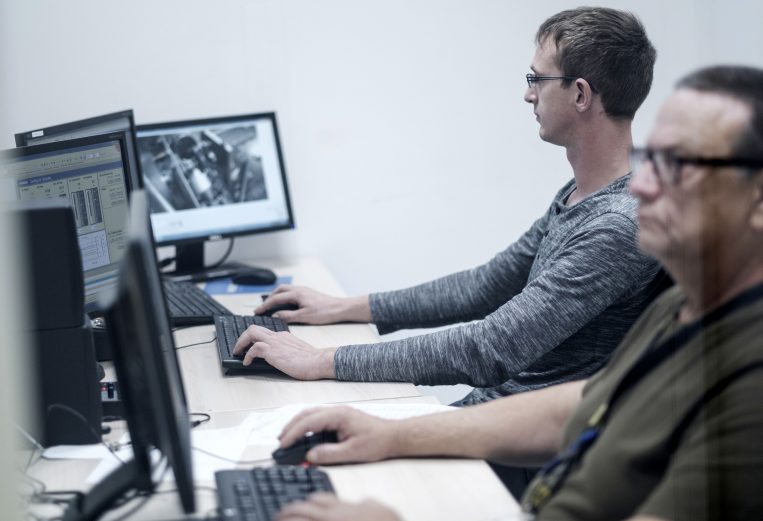
Alles unter Kontrolle: Vom Steuerraum aus verfolgen Philipp Penther (l.) und Joachim Antusch die Testreihen.
„URMETER“ steht in NORDAMERIKA
Das aber sind nicht die einzigen Schritte in die Zukunft, die die neue Anlage markiert. Sie arbeitet obendrein genau wie der GM-Prüfstand in Nordamerika, der im Unternehmen gewissermaßen als „Urmeter“ für Bremsgeräuschanalysen festgelegt ist. „Dadurch können unsere Ergebnisse weltweit akzeptiert werden – und Kollegen in aller Welt können auf sie zurückgreifen“, erklärt Bremsenentwickler Thomas Neff.
Die einzelnen Versuchsabläufe sind ebenfalls in für die gesamte GM-Welt gültigen Prüfvorschriften festgeschrieben. Natürlich gibt es einige davon, und für jede einzelne, die deckungsgleich mit dem „Urmeter“ ausgeführt worden ist, wird ein eigenes Zertifikat ausgestellt. Daher wundert es nicht, dass in dem neu gestalteten Bereich auch eine Wand für Urkunden vorgesehen ist – „und die wird bis Jahresende bereits gut gefüllt sein“, ist sich Robert Thomas Bender sicher.
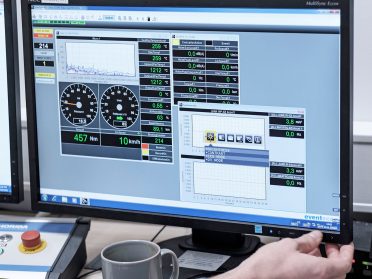
Alles im Blick: Im Steuerraum lassen sich alle Prüfungsergebnisse einsehen.
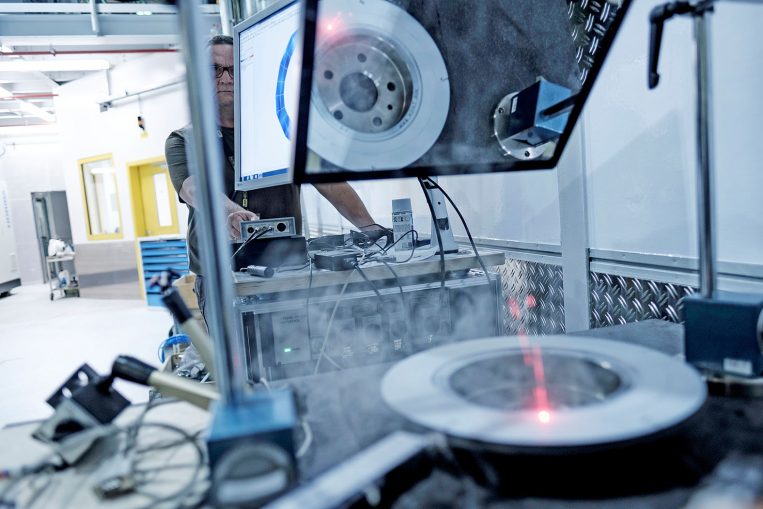
Höchste Präzision: Der 3-D-Laser-Vibrometer zeichnet mechanische Schwingungen an den Komponenten auf. Sichtbar sind die Laserstrahlen normalerweise nicht. Für das Foto wurde extra Rauch erzeugt.
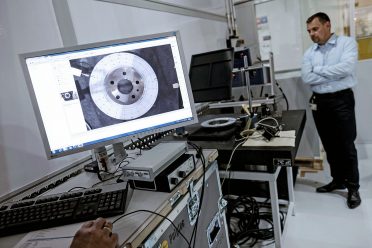
Zufrieden: Bremsentwickler Thomas Neff am 3-D-Laser-Vibrometer.
Doch bei aller globalen Vernetzung: „Wir freuen uns, dass wir den Prüfstand gemeinsam mit der Firma Horiba entwickeln konnten, die in Darmstadt ansässig ist, nur 25 Kilometer von Rüsselsheim entfernt.“ Denn ein persönlicher Gedankenaustausch ist auch in der „Industrie 4.0“ noch was wert.
Das gilt auch für die Planung künftiger Projekte. „Als nächstes planen wir einen Prüfstand der nächsten Generation, um die Leistung unserer Bremsen zu überprüfen“, kündigt Klaus Osterhage an. Jede Menge Hightech also, das die Entwicklungszeiten weiter verkürzen wird.
Stand Oktober 2016