Jedes Produkt kann nur so gut sein wie seine Einzelteile. Wozu Zvonimir Facol/Leiter Quality Engineering sagt: „Unsere Aufgabe ist es dem Werk die benötigten Teile in ordnungsgemäßem Zustand zur Verfügung zu stellen.“ Bei Fünfgang-Getrieben bedeutet das 180 Teilenummern, bei Motoren 204, bei Sechsgang-Getrieben 289; insgesamt also 673 Teilenummern. Von der kleinen Schraube bis zum mehrere Kilogramm schweren Gussteil (Motorblock, Kupplungs-, Getriebe-, Differential-Gehäuse u.s.f.). Im aktiven Verbau werden 542 der insgesamt 673 Teilenummern verwendet.
Strukturierte Feuerwehr
Der Sisyphus-Job des Quality Engineering-Teams resultiert nicht nur aus der Vielzahl der Teile, sondern aus den unterschiedlichen Anforderungen. Da geht es auf der einen Seite darum, fehlerhafte Teile – die in den Produktionsprozess gelangt sind – schleunigst auszuschalten.
Kaum erhält ein Quality Engineer der Abteilung Quality Operations eine NOK-Meldung aus dem Werk, prüft er umgehend, ob die Ursache beim Lieferanten zu suchen ist. Wenn ja, sind Michael Hanreich/Leiter QCC und SQI – und damit Chef des Sortierpools – mit den Qualitätsingenieuren Alfred Menschik und Florian Prinz, die für Lieferantenkontakte zuständig sind, am Ruder. Und zwar schnell. Binnen zwei bis drei Stunden wird – wenn nötig – eine Sortieraktion eingeleitet. Die 23 MitarbeiterInnen des Sortierpools haben dann die Aufgabe jedes fehlerhafte Teil der betroffenen Teilenummern herauszuklauben; in Drei-Schicht-Betrieb.
Im Jahr 2016 gab es 213 derartige Sortieraktionen. „Im Schnitt haben wir fast täglich eine Sortieraktion“, sagt Facol.
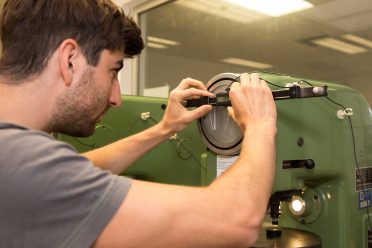
Härtewerte ermitteln (Adrian Zankl).
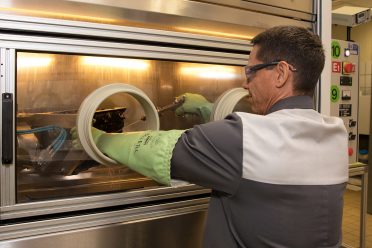
Restschmutzmessung (Christian Schöllerl).
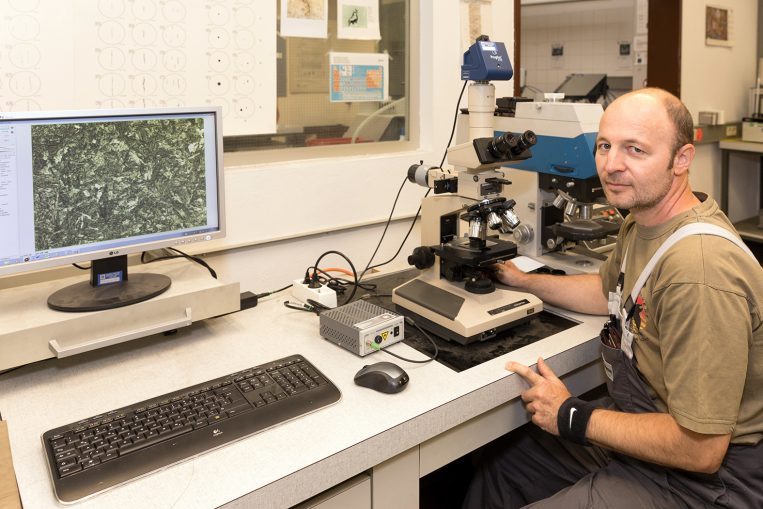
Fotodokumentation (Herbert Bosits).
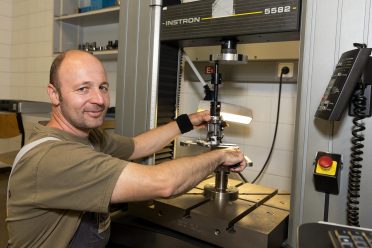
Zugkraftmessung (Herbert Bosits).
Damit alle Bescheid wissen
Zeitgleich mit dem Einleiten der Sortieraktion wird der Lieferant verständigt; und nicht nur er. Denn fehlerhafte Teile werden sofort im „Global Tracking System“ erfasst. Über dieses System erfahren der Lieferant – mit genauer, mit Bildern unterlegter Beschreibung des Fehlers – und alle anderen Werke, die das gleiche Teil verwenden, vom Fehler am betreffenden Zulieferteil.
Der Lieferant muss nun gleichfalls sofort handeln: Binnen 24 Stunden muss er zu den betroffenen Teilen den bei ihm vorrätigen Bestand melden; und dann alle vorangegangenen Bearbeitungsschritte und halbfertigen Teile. Zuerst gilt es also das Auftauchen weiterer fehlerhafter Teile zu vermeiden. Und danach kommt die Ursachenfindung dran; innerhalb von zwei Wochen. Erst wenn der gesamte Fehlerbehebungsprozess abgeschlossen ist, gibt der Asperner Qualitätsingenieur im „Global Tracking System“ ein, dass es keine Probleme mehr mit dem Teil gibt. Die Sortierkosten und die durch das fehlerhafte Teil in der Produktion verursachten Kosten werden dem Lieferanten weiter verrechnet. Fehlerhafte Teile werden verschrottet oder an den Lieferanten zurückgesandt.
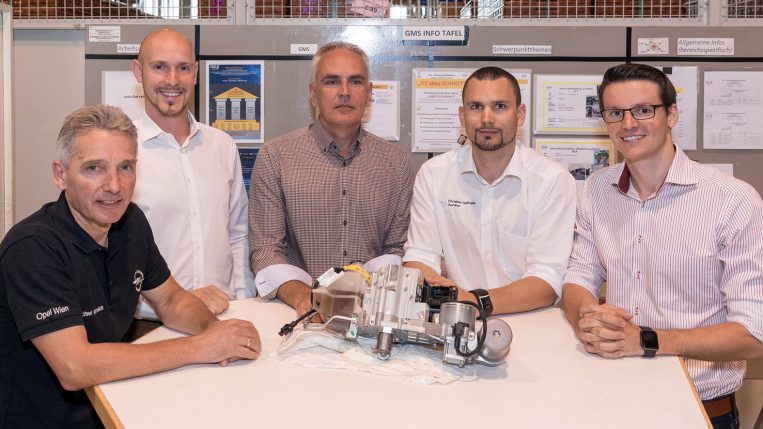
Zvonimir Facol/Leiter Quality Engineering mit seinen Qualitätsingenieuren (v.l.n.r.: Michael Hanreich, Florian Prinz, Zvonimir Facol, Christian Dallinger, Alfred Menschik).
Geprüft und für gut befunden
Nicht nur fehlerhafte Teile sind im Visier des Quality Engineering-Teams: Bevor neue Teile in den Produktionsprozess gelangen, wird akribisch nach Fehlermöglichkeiten gefahndet. Der krönende Abschluss dieser „Aufnahmsprüfung“ ist der Production Trial Run, bei dem das neue Teil erstmals den Produktionsprozess durchläuft und dabei genau beobachtet wird; mit einer „Durchlaufliste“, in der alle Beobachtungen festgehalten werden. „Für Gussteile ist diese Vorgangsweise
immer wieder nötig“, erklärt Zvonimir Facol, „weil die Formen der Gussteile verschleißen. Getriebegehäuse-Formen zum Beispiel halten nur etwa 120.000 Stück.“ Wichtige Teile-Änderungen und Änderungen der Prozesse bei den Lieferanten werden in den alle zwei Wochen stattfindenden Quality Readiness Meetings diskutiert, an denen nicht nur alle Quality Management-Abteilungen teilnehmen, sondern auch Vertreter der Werkslogistik, von Fertigung und Montage sowie Manufacturing Engineering.
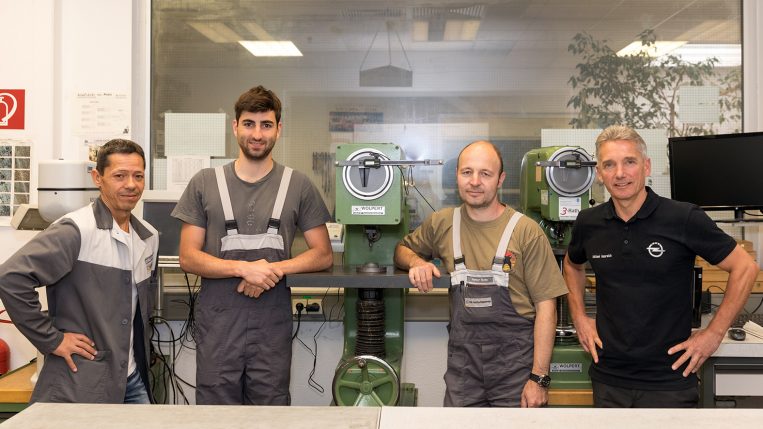
Michael Hanreich/Leiter CCP-Team, chemisches und physikalisches Labor und Sortierpool im Kreise seiner Labor-Mitarbeiter (v.l.n.r.: Christian Schöllerl, Adrian Zankl, Herbert Bosits, Michael Hanreich).
Alltagsgeschäft sind für das Quality Engineering-Team die regelmäßigen Überprüfungen, die alle im Werk verbauten Teile durchlaufen müssen. Im Schnitt werden alle Teile mindestens einmal jährlich überprüft. In streng definierten Losgrößen und mit genau vorgeschriebenen Tests. Im Feinmessraum sowie im chemischen und im physikalischen Labor.
Facol führt Beispiele an: „Zündkerzen werden optisch geprüft, vermessen und dem Salzsprühnebeltest unterzogen (um die Funktion trotz Salzeinwirkung im Winter zu checken). Anders Lockerringe: Da wird eine Sequenz herausgeschnitten, um Härtetests durchzuführen; einmal im Eindringverfahren mit einer Diamantnadel, zum anderen im Zugversuch, um festzustellen, wie gut der auf die Muffe aufgepresste Lockerring hält.“ Solche Prüfvorgaben gibt es für alle 673 Teilenummern des Werks Aspern.
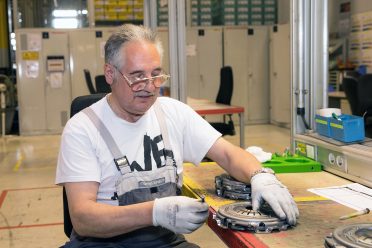
Sortiertätigkeit (Gerhard Schuh).
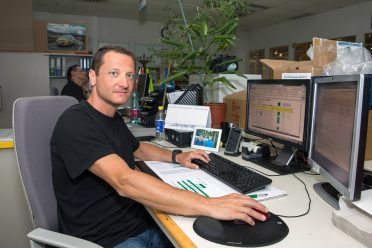
Raimund Brezina/Production Trial Run-Koordinator.
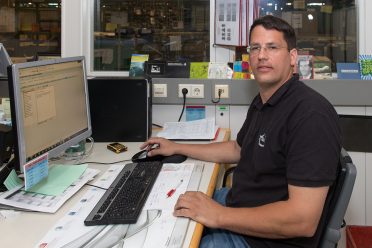
Wolfgang Elend ist für Cost Recovery und Ausschuss-Handling zuständig.
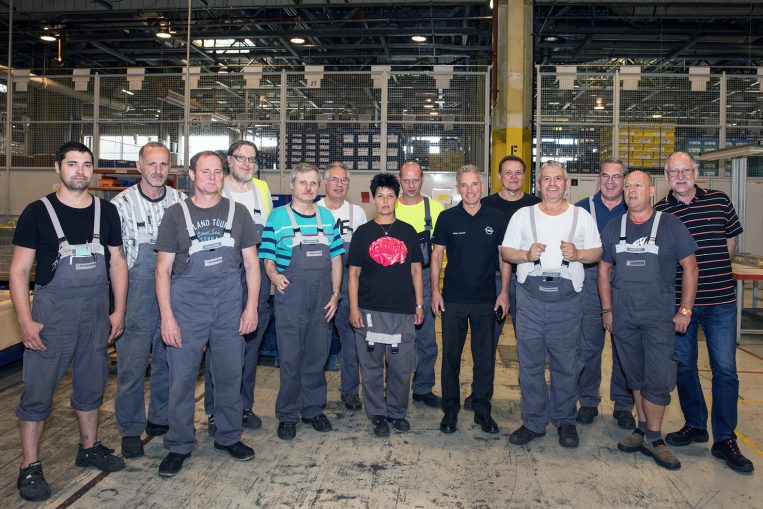
Michael Hanreich im Kreise seiner Sortierpool-MitarbeiterInnen (v.l.n.r.: Severin Bangerl, Hannes Kammerer, Wolfgang Meister, Peter Pfeiler, Christian Belletz, Gerhard Schuh, Dolores Maier, Werner Preissack, Michael Hanreich, Werner Gottschlich, Christian Döltl, Ernst Steffl, Manfred Huber, Heinz Reichenpfader).
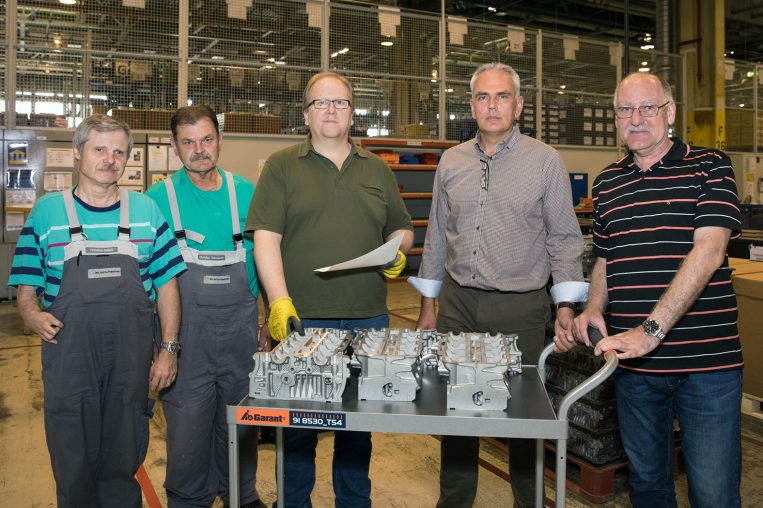
Zvonimir Facol/Leiter Quality Engineering mit Mitarbeitern des Sortierpools (v.l.n.r.: Christian Belletz, Christian Schmierer, Günther Zsivkovics, Zvonimir Facol, Heinz Reichenpfader).