“As a next step, we will start making parts for the Insignia A.”
Hartmut Paulke applies a thumb’s width of black adhesive to the shell of a door. Together with his fellow worker Werner Walmen, the plant worker positions the sheet on a support frame. A robot then springs into action, and places the metal precisely on the interior panel. Two additional machines switch on and fold the edges. This crimping technique is used to create a right rear door for the Opel Meriva every two minutes. This compact van was produced for the last time in June 2017 in Saragossa, Spain.
Paulke and Walmen are two of the 14 employees who are currently working in the new customer service cell in K40. These cells are part of Customer Service Manufacturing, which has returned to the main Opel production facility after over two decades. Pressing plant and paint shop employees also work for this new division. “Production of the customer service parts for the Meriva has gotten off to a very good start,” says Plant Director Michael Lewald. “As a next step, we will start making parts for the Insignia A, another model that is no longer in production. The new customer service cell is highly flexible and provides us with the opportunity to prepare a high variety of required parts for our customers.” After series production of the Meriva in Saragossa came to an end last summer, the corresponding tools in the northeast of Spain were dismantled and brought to Rüsselsheim, Germany. Here, the systems were adjusted and integrated so that production could begin this January.
- Exakte Linie: Waldemar Gordzielik bringt Kleber auf der Außenhaut einer Meriva-Tür auf.
- Teamwork: Ehe zwei Roboter die Blechkanten falzen, positioniert ein dritter Kollege die Außenhaut auf dem Gerippe der Meriva-Tür.
- Produktive Methode: Mithilfe der Bördeltechnik verbinden die Roboter die Innen- und Außenhaut der Meriva-Tür.
“Manufacturing the spare parts in-house again gives us a dual advantage,” says Uwe Baum. The Deputy Chairman of the works council had campaigned intensively for the new system over the past few months. “From a business perspective, this insourcing project pays off: When we outsource production through a service provider, we earn significantly less per unit. At the same time, we can now deploy employees here who have difficulties with the fast pace on the assembly line due to their age or health.” Close cooperation with the Integrationsamt Hessen, an institution that secures employment for persons with disabilities, allowed Opel to also receive a subsidy for deploying these employees, says Baum.
Customer service manufacturing not only requires new systems, but also a new way of thinking: “Old approaches and patterns of thinking need to be discarded,” explains Dr. Michael Rupp of the Manufacturing/Engineering department, whose six-member team is responsible for designing and approving the project. Instead of the familiar high output of mass production, customer service production focuses on achieving high flexibility at small volumes of units. The logistics chain also had to be completely reworked – from ordering the customer service parts from the dealers, to ordering many individual parts in small batches, through to production and delivery to the customer. “We are still in the learning phase as far as this is concerned, and could certainly optimize a great deal more in order to further save on costs,” says Rupp.
“Old approaches and patterns of thinking need to be discarded.”
Most of the components manufactured in Rüsselsheim end up in the Opel goods distribution center in Bochum; some also proceed directly to other European warehouses. From there, the parts are ultimately sent to the dealer.
The Meriva spare parts are only the beginning of customer service production. As Michael Lewald mentions, other components of the first generation of the Insignia as well as the latest generation of the Corsa will soon be made in Rüsselsheim as well. Paulke and Walmen will then welcome additional employees and robots to K40 – if not earlier.
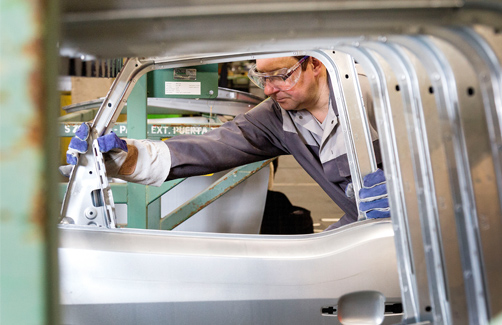
In rank and file: The shells of the Meriva doors are hanging close at hand in their frames.
February 2018