Tension: increases.
Experiences working assembly lines so far: zero.
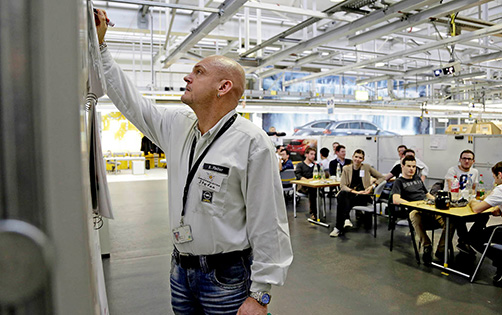
Dry run: Trainer Stefan Fischer explains the tasks of the individual stations.
It’s 7:15 a.m. on Tuesday in K40 at the plant facilities in Rüsselsheim, Germany. I’m meeting up with five trainers and 16 trainees for SWE training. Today I’ll learn what it feels like to work on a conveyor belt. For eight hours. We meet up at the training system in the method training center. This closed roller conveyor system consists of 12 wooden cars on a rectangular conveyor belt and all types of shelves stocked with plastic boxes and wooden blocks. A rope that looks like a clothesline is hanging above our heads. What is all this for? Before we find out, we’ll be getting a lesson on theory.
“‘SWE,’” says Stefan Fischer during his presentation, “stands for ‘simulated work environment.’” Fischer is part of the GMS & Training team, which has led 600 of these types of training sessions since 2005. The trainer expertly clicks through his slides and explains the standard spreadsheet, workplace rules, and business plan. According to this plan, which covers and evaluates (near-)accidents, discipline, punctuality, and errors in workflows, among other things, we need to manufacture 18 vehicles within 20 minutes. If we don’t hit this target output, we won’t stay on budget. The same applies if we don’t finish within 20 minutes. After the introduction, we’re taken straight to the assembly line, for the first of a total of three production runs.
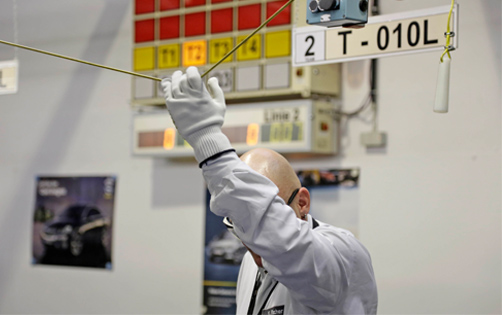
Houston, we have a problem: Pulling on the Andon cord brings the roller conveyor to a halt so that a trainer can come help.
We’re split up into four groups. Groups 1 and 2 attach the components to the vehicle exterior, Group 3 does the same for the interior, and Group 4 disassembles all of the parts and provides the other groups with materials. I’ve been placed in Group 4. Fischer explains: “If you have a problem, tug on the Andon cord. That’ll bring the conveyor belt to a halt, you’ll hear a song play, and the trainers will come help you.” So now we know what the clothesline is for. Is it time to get started?
Thorsten Anderson, my team’s trainer, outlines what’s expected from Group 4: “Two of you will work on the inside the conveyor belt, and two will work on the exterior. On the inside, you’ll use cordless screwdrivers and sort each component into one of the eight plastic boxes. On the outside, you’ll do the same, just without screwdrivers.” The fifth team member isn’t a fifth wheel; they’re responsible for logistics on the outside – in other words, filling and emptying boxes. We need to do that ourselves on the inside. Okay, got it. Now we need to get the sequence down. And we’re off!
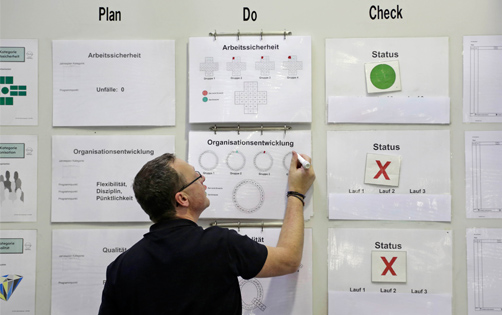
The business plan is strict, and with the help of various KPIs, the trainers review whether all of the specifications have been upheld.
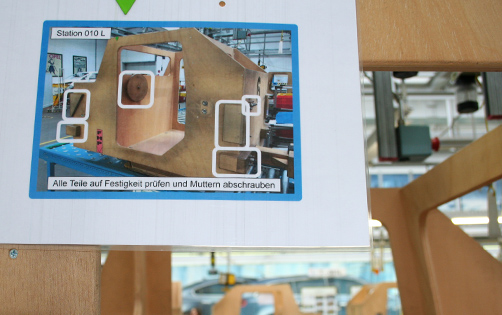
At a glance: Each station’s tasks consist of multiple work steps that need to be efficiently carried out in a defined sequence.
Durchgang eins: Nur zwölf Autos produziert
und zwei Beinahe-Unfälle. Ernüchternd.
I spend the first ten minutes at the station on the outside of the conveyor belt. The greatest challenge when it comes to the pieces of wood, which all look alike, is sorting: What goes where? After a few rounds, I figure it out and establish a kind of routine. Time isn’t an issue. “Switch,” Fischer calls out. Now I switch to the inside of the conveyor belt. I pick up a cordless screwdriver, loosen bolts, store them, remove wooden parts from the car, and sort them. It sounds easy, but it isn’t – in part because the storage boxes here are organized differently. Before I can get my bearings, Group 2 has already pushed the next car into my station. Okay, time to pick up the pace! All my boxes quickly fill up. What now? Time to switch out the parts? But where do I put this stuff again? “Time’s up!” Fischer calls out.
During the subsequent feedback round, the groups report back on their experiences, which were similar to mine. Some stations had less to do and some had more, some had coordination problems, and there was a general sense of time pressure. What does the business plan say? Fischer sums things up: “Only 12 cars were produced instead of 18, the Andon cord got pulled six times, and there were two near-accidents.” So we’ve racked up 74 penalty points. Not exactly encouraging.
After our lunch break, it’s time for round two. It can’t be that hard, now that we’ve already done it once! We brainstorm with Thorsten Anderson about which processes could be simplified, improved, or more efficiently distributed. In order to put away parts more quickly, we modify the way the boxes are organized. To prevent (near-)accidents with the cars, we change the way parts are handed over between the stations. Does this make a difference?
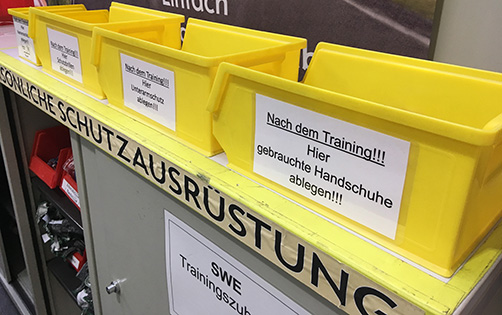
Please clean up: A good organisation is half the battle, even at SWE training.
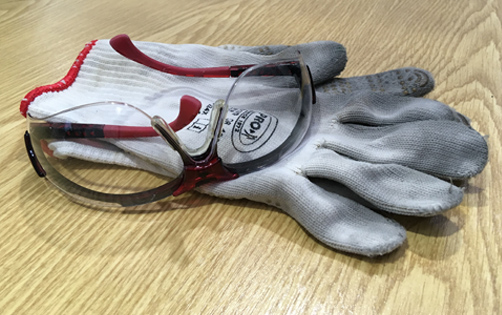
Workplace safety: Gloves and protective goggles are always mandatory around the SWE system.
Round two: The learning curve kicks in.
We fare much better this time around.
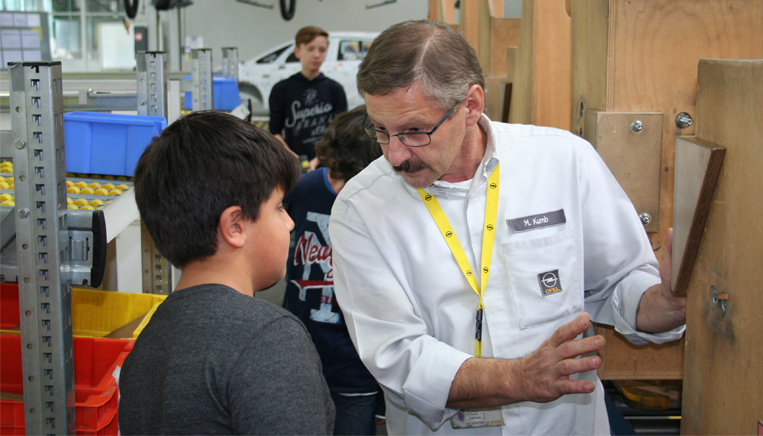
How it’s done: The GMS & Training team offers SWE training for schoolkids as well, for example.
SWE training
for everyone
The GMS & Training team offers SWE training for all interested groups, such as classes of schoolchildren. It is available as advanced training or as a general team-building event – for employees in all departments. Those interested in booking training can sign up by contacting Thomas Wedde at (+49-6142) 778-056 or thomas.wedde@opel.com.
Yes: We fare much better this time around. We’re able to make the full 18 cars, and eliminate most of the errors from the first time around. “Well, well, this looked a lot better,” says Fischer in praise. But then he pours salt on the wound: “But this time, we made different mistakes than we did on the first go. For instance, two employees on Team 3 put their safety gloves on too early.” How annoying – that costs us 16 penalty points. However, there weren’t any errors in the other categories. So all in all, a good result.
We get one last chance to prove ourselves in the third and final round. Apart from an additional component that we have to assemble or disassemble, all the conditions remain the same. We also have the goal not to accumulate any more, unnecessary penalty points. Ten minutes later, we’re done – not without errors, but we successfully pass the SWE training. My takeaway from this experience: Series production requires you to always give your all. You need to always stay focused, alert, and at the ready. You don’t have time to catch your breath – it’s a real challenge. This training doesn’t just teach you how vehicles are assembled; it’s also a great team-building exercise. And it’s fun, too!
Summary of the three rounds: You always need to remain alert and focused.
It’s a real challenge. But it’s a lot of fun, too.
March 2018