- Sorgfaltspflicht: Bei der Endkontrolle im Rüsselsheimer Werk muss jeder Insignia seine Topqualität beweisen.
5 Sterne
konnte der Opel Insignia Grand Sport (2017) beim Euro-NCAP-Crashtest einstreichen – Bestwertung!
Bis heute hat das Flaggschiff
23 von 40 Tests
in europäischen Fachmedien gewonnen.
Endlose Reihen von Nummern laufen über die Monitore der Material- und Produktionssteuerung im Stammwerk Rüsselsheim. Hinter jeder verbirgt sich ein eingegangener Auftrag, ein ganz individuell zusammengestelltes Flaggschiff für einen Kunden aus Deutschland, Spanien oder Polen. 100.000 Bestellungen sind für die zweite Generation des Insignia nicht mal ein Jahr nach dem Produktionsstart bislang aus ganz Europa hier eingetroffen. Und zu jeder Zeit wissen die Mitarbeiter der Steuerung, an welcher Stelle der Produktion sich das Fahrzeug eines jeden Kunden befindet. In der Reihenfolge, in der die Aufträge geplant werden, laufen die fertigen Fahrzeuge nach etwa einem Tag auch vom Band.
Es ist nicht nur eine gewaltige, bis ins kleinste Detail ausgefeilte Planung nötig, damit die 3.600 Kollegen im Stammwerk jeden Tag rund 700 Flaggschiffe in Spitzenqualität fertigen können: Gigantische Pressen machen den Anfang und formen hunderte Einzelteile, die wiederum von über 1.200 Robotern nach einer fest einstudierten Choreographie zur Karosserie verschweißt werden. Nach dem aufwendigsten Part – dem Lackieren (elf Stunden dauert das Procedere) – geht es in die Fertig- und Endmontage, wo viele geschulte Hände der Karosserie ein Innenleben geben. Ob ein Schiebedach für die Limousine, ein Navi 900 IntelliLink für die Kombi-Variante oder die Exclusive-Felge für den Country Tourer – jedes der über 7.500 Einbaukomponenten steht den Werkern hier zum Einbau zur Verfügung. Und zwar genau dann, wenn das entsprechende individuell konfigurierte Fahrzeug des Kunden Meyer, González oder Kowalski vorbeikommt.
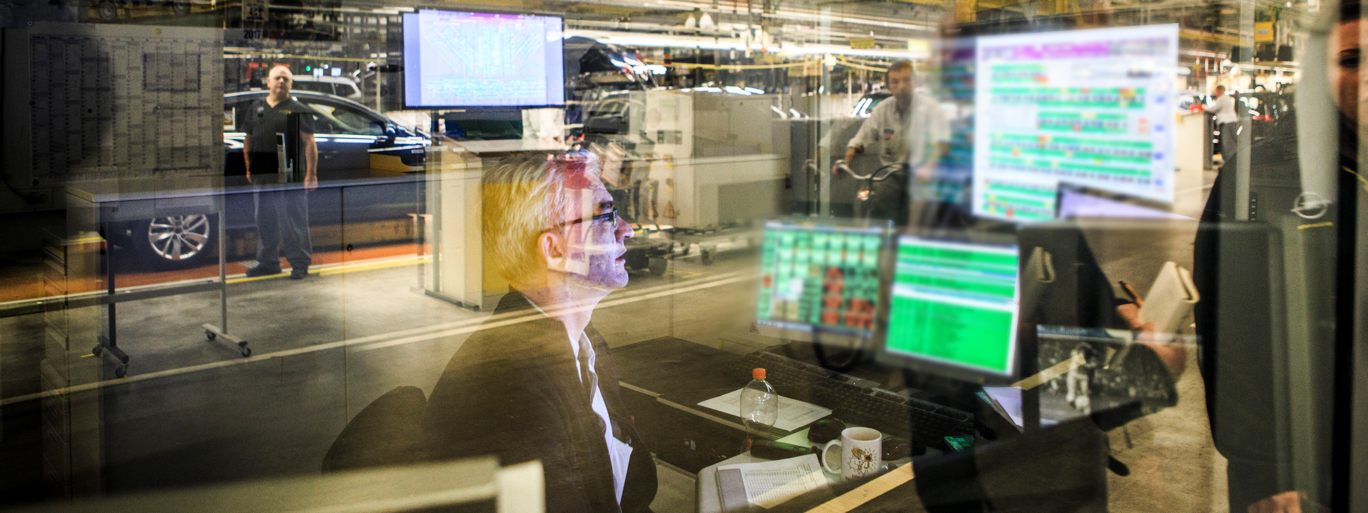
Hinter Glas: Bei den Kollegen im sogenannten Nerv Center laufen in Echtzeit die Informationen zur Produktion zusammen.
Know-how aus Lautern
50 dieser Einbaukomponenten wie beispielsweise der Träger des Armaturenbretts – ein hochkomplexes Bauteil, für das allein 40 Einzelteile gefertigt und miteinander verschweißt werden – kommen von den Kollegen aus Kaiserslautern. Ebenso „Made in Kaiserslautern“: die besonders leichte Aluminium-Motorhaube.
Der Insignia ist nicht nur bei den Kunden erfolgreich, auch in den Medien. Das Opel-Flaggschiff hat im ersten Jahr renommierte Preise von namhaften Publikationen erhalten, darunter das „Goldene Lenkrad 2017“ in Polen (Auto Świat, Foto rechts) und Slowenien (Auto Bild) sowie die Auszeichnung als „Best Car 2017” (Fleet Cars & Vans, Fleet Auto Premium) in Polen und „Fleet News of the Year“ (FLEET Magazine) in Tschechien. Dass die neue Insignia-Generation nicht nur für Privatkunden, sondern auch für den Flotteneinsatz attraktiv ist, beweist die jüngste Auszeichnung: Das Flaggschiff wurde in Großbritannien mit dem „Company Car Today CCT100“-Award (Company Car Today) ausgezeichnet. Auch bei diversen Vergleichen europäischer Automobilzeitschriften setzte sich der Insignia gegen starke Konkurrenz durch.
So entsteht ein Flaggschiff
1 Der Form halber
Bis zu 30 Tonnen schwer sind die angelieferten Stahlrollen, sogenannte Coils. Die acht Pressenstraßen formen aus dem Blech die rund 600 Einzelteile der Karosserie, darunter die Türen inklusive charakteristischer Sicke. Ein einzelnes formgebendes Presswerkzeug wiegt bis zu 25 Tonnen.
- Dieser Coil, der gerade angeliefert wird, wiegt gute 20 Tonnen.
- Die acht Pressenstraßen formen aus dem Blech die Einzelteile der Karosserie.
- Schon jetzt bestens zu erkennen: die charakteristische Sicke der Türen.
2 Das schweißt zusammen
Nach einer festen Choreographie setzen im Rohbau über 1.200 Roboter über 6.000 Schweißpunkte. Hinzu kommen gut hundert Meter Klebenaht, um aus den Einzelteilen die Insignia-Karosserie aufzubauen.
- Neben verschiedenen Schweißtechniken kommt vermehrt Strukturkleber zum Einsatz.
- Über hundert Meter Klebenaht, viermal mehr als beim Vorgänger machen die Karosserie zum hochfesten Leichtgewicht.
- Die Aluminium-Motorhaube wird im Komponentenwerk Kaiserslautern gefertigt.
3 Schicht für Schicht
47 Stationen durchläuft die Karosserie bis insgesamt 6,5 Kilogramm Grund-, Basis- sowie Klarlack aufgetragen sind – und die Hülle in einer der 15 erhältlichen Farben glänzt. Komplexester Arbeitsschritt ist die Fahrt durch das 20 Meter lange Tauchbecken, um den perfekten Korrosionsschutz zu gewährleisten. Kuriose Station des elfstündigen Prozesses: Emu-Federn entfernen selbst kleinste Staubpartikel von der Hülle.
- Elf Stunden dauert es, bis die Karosserie in einer der 15 erhältlichen Farben glänzt.
- Bevor das Fahrzeug seinen Decklack erhält, werden in der Lackiererei vollautomatisch alle Nähte der Karosserie versiegelt.
4 Gut gebaut
Fünf Stunden lang vervollständigen in jeder Schicht 400 Kollegen in der Fertig- und Endmontage das Fahrzeug – unterteilt in 300 akribisch einstudierte Arbeitsschritte. Die Logistik sorgt dafür, dass jedes der potenziellen 7.500 Bauteile zur richtigen Zeit an der richtigen Station bereitliegt. Kniffliger Part: den mehrere Kilometer langen Hauptkabelsatz zu montieren. Am Ende fährt ein exakt nach Kundenwunsch gebautes Flaggschiff vom Band.
- Der Insignia heiratet seinen Motor, das Getriebe und die Achsen.
- In der Endmontage werden die Fahrzeuge mit allen Flüssigkeiten befüllt.
- Auch jedes Cockpit wird nach den Ausstattungswünschen der Kunden individuell zusammengebaut.
Stand Januar 2018